Technology and Applications of edm wire machining
EDM wire machining, also known as wire EDM (Electrical Discharge Machining), is a specialized manufacturing process used to cut intricate shapes in electrically conductive materials. It utilizes a thin, electrically charged wire to erode material in a controlled manner. Here’s an overview of its technology and applications:
Technology:
Wire EDM operates by creating electrical discharges (sparks) between the wire electrode and the workpiece submerged in dielectric fluid. These discharges generate intense heat, melting and vaporizing small particles from the workpiece, which are then flushed away by the dielectric fluid. The wire, typically made of brass or tungsten, is continuously fed from a spool to maintain a precise cutting path determined by computer numerical control (CNC). This process allows for extremely tight tolerances and intricate shapes without inducing mechanical stresses on the material.
Applications:
1. Tool and Die Making: Wire EDM is extensively used in tool and die manufacturing for producing complex shapes that are difficult or impossible to achieve with conventional machining techniques. It is particularly suited for hardened materials such as tool steels.
2. Prototyping and Small Batch Production: Due to its ability to create complex shapes quickly and accurately, wire EDM is ideal for prototyping new components and small batch production runs. It enables manufacturers to iterate designs rapidly and efficiently.
3. Aerospace and Automotive Industries: These industries utilize wire EDM for manufacturing precision components like turbine blades, gears, and injection molds. The process ensures high accuracy and repeatability, critical for safety and performance in aerospace and automotive applications.
4. Medical Devices: Wire EDM is employed in manufacturing surgical instruments, implants, and other medical devices requiring intricate geometries and biocompatible materials.
5. Electronics: In the electronics industry, wire EDM is used for making fine metal parts, micro-components, and molds for plastic injection molding of electronic housings and connectors.
In conclusion, EDM wire machining is a versatile and precise manufacturing technology with applications across various industries where complex shapes and high precision are required. Its ability to work with hard materials and produce intricate parts makes it indispensable in modern manufacturing processes.
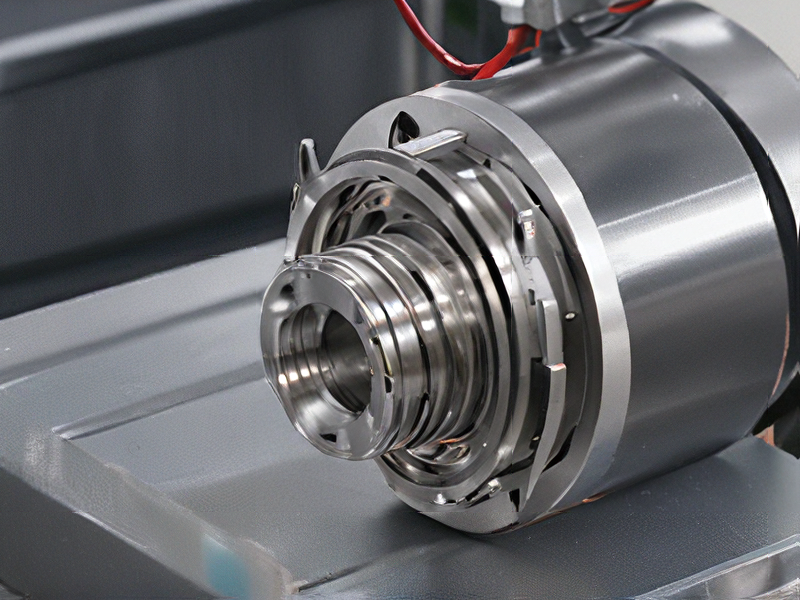
Quality Testing Methods for edm wire machining and how to control quality
Quality testing methods for EDM (Electrical Discharge Machining) wire machining are essential to ensure precision, accuracy, and surface integrity of the machined parts. Here are some common methods and quality control measures:
Quality Testing Methods
1. Dimensional Inspection:
– CMM (Coordinate Measuring Machine): Measures the dimensions of the machined part against the CAD model.
– Optical Comparators: Provides magnified images for precise measurement.
2. Surface Roughness Testing:
– Surface Profilometers: Measures surface roughness parameters like Ra, Rz.
– Optical Surface Scanners: Provides non-contact surface roughness measurement.
3. Microstructure Analysis:
– Microscopy: Examines the microstructure of the material to identify any changes or defects due to machining.
4. Electrical Testing:
– Conductivity Testing: Ensures that the EDM process hasn’t altered the electrical properties of conductive materials.
5. Tensile and Hardness Testing:
– Hardness Testers: Checks for any changes in hardness post-machining.
– Tensile Testing Machines: Assesses the material’s mechanical properties.
Quality Control Measures
1. Process Parameter Optimization:
– Regularly monitor and adjust parameters like pulse duration, current, and voltage to maintain optimal cutting conditions.
2. Wire Condition Monitoring:
– Ensure the EDM wire is in good condition, checking for wear or defects that could affect machining accuracy.
3. Coolant and Filtration System Maintenance:
– Regularly check and maintain the dielectric fluid’s cleanliness and proper functioning of filtration systems to prevent contamination.
4. Machine Calibration:
– Routine calibration of EDM machines ensures that they operate within specified tolerances.
5. Statistical Process Control (SPC):
– Use SPC tools to monitor the EDM process, identifying and controlling variations to maintain consistent quality.
6. Regular Training:
– Continuous training for operators on best practices and latest technologies in EDM to ensure they can identify and mitigate potential quality issues.
Implementing these testing methods and quality control measures ensures that EDM wire machining processes produce high-quality parts consistently, meeting stringent industry standards.
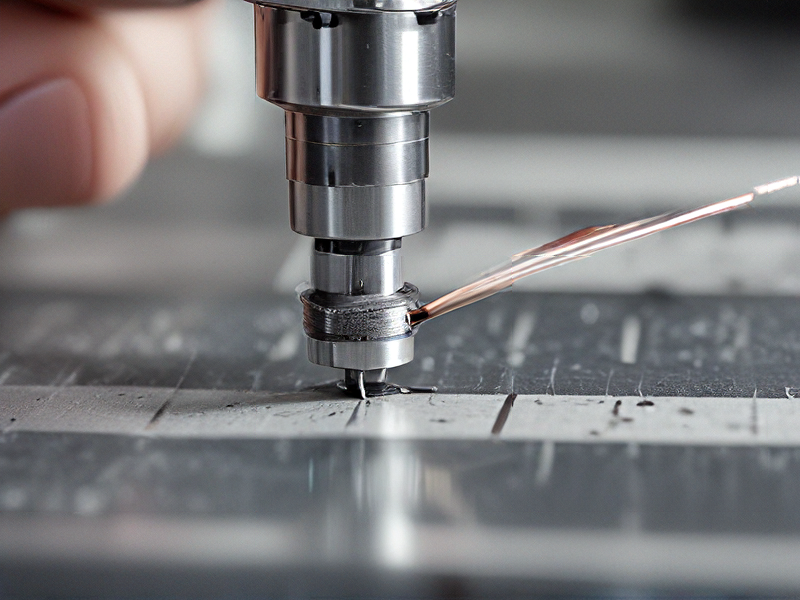
Tips for Procurement and Considerations when Purchasing from edm wire machining
When procuring EDM (Electrical Discharge Machining) wire, several key considerations can help ensure you make an informed and effective purchase:
1. Quality Assurance: Ensure the supplier adheres to stringent quality standards. Look for certifications like ISO 9001, which indicate quality management practices. Request samples to assess the wire’s performance before committing to a bulk order.
2. Wire Specifications: Understand the technical specifications required for your application. This includes wire diameter, tensile strength, electrical conductivity, and surface finish. Selecting the right wire grade is crucial for achieving accurate machining results.
3. Supplier Reputation: Research potential suppliers for their reputation in the industry. Look for customer reviews, testimonials, and case studies. Strong relationships with established suppliers can also provide better support and reliability.
4. Cost vs. Value: While price is always a factor, consider the overall value. Cheaper wires may have lower quality or performance, leading to increased downtime or inferior machining results. Calculate the total cost of ownership, factoring in potential waste and rework.
5. Lead Times and Availability: Confirm the supplier’s lead times and ensure that they can meet your production schedule. Consistent availability of the product is essential to avoid disruptions in your machining processes.
6. Technical Support: Choose suppliers that offer excellent technical support. Having access to experts who can provide guidance on using the wire effectively can enhance your machining operations and minimize issues.
7. Sustainability: Consider suppliers who prioritize sustainable practices. Eco-friendly wire options and responsible sourcing can align with your company’s sustainability goals.
By prioritizing these considerations, you can enhance your procurement process for EDM wire, leading to improved machining efficiency and overall productivity.
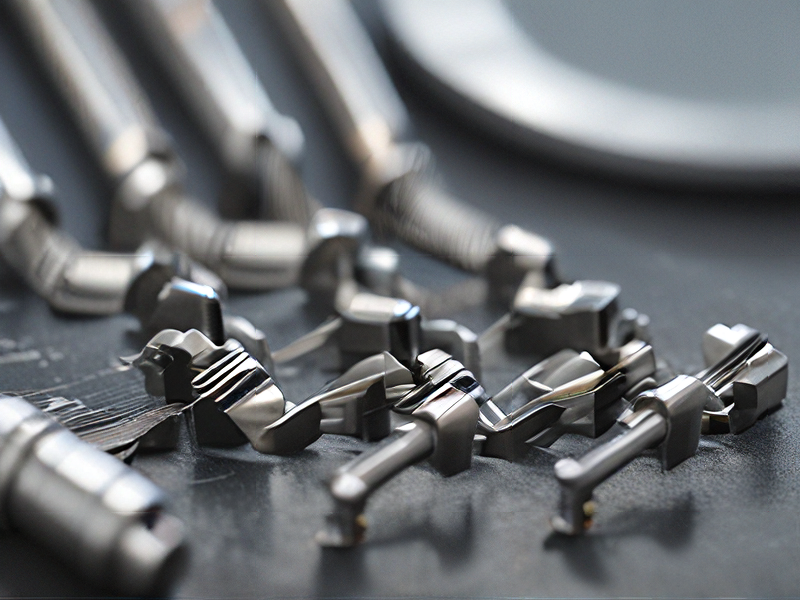
FAQs on Sourcing and Manufacturing from edm wire machining in China
Certainly! Here are some frequently asked questions (FAQs) regarding sourcing and manufacturing from EDM wire machining in China:
1. Why should I consider EDM wire machining in China?
EDM wire machining in China often offers competitive pricing without compromising on quality. Chinese manufacturers are known for their proficiency in precision engineering and can handle large-scale production efficiently.
2. How can I ensure quality when sourcing from China?
It’s crucial to conduct thorough supplier evaluations, including factory visits if possible, and to request samples for testing. Implementing strict quality control measures and using reputable third-party inspection services can also help maintain quality standards.
3. What are the typical lead times for EDM wire machining in China?
Lead times can vary depending on factors such as order complexity, quantity, and supplier capacity. Generally, lead times range from a few weeks to a couple of months. Clear communication with suppliers about deadlines is essential.
4. What about intellectual property (IP) protection?
Protecting intellectual property is a valid concern. Engaging legal expertise to draft robust contracts and nondisclosure agreements (NDAs) can help safeguard your designs and proprietary information.
5. Are there language barriers or cultural differences to consider?
Language barriers can be overcome by working with suppliers who have proficient English speakers or utilizing translators. Understanding cultural norms and business practices through research or local partners can facilitate smoother communication and negotiations.
6. What are the payment terms typically used?
Payment terms often involve a combination of initial deposits, progress payments, and final balances upon completion and inspection. Negotiating favorable terms while ensuring financial security is advisable.
7. How can I manage logistics and shipping effectively?
Utilizing experienced freight forwarders or logistics providers familiar with international shipping regulations can streamline the process. Clear agreements on incoterms and responsibilities regarding customs clearance are essential.
Navigating sourcing and manufacturing processes in China requires diligence in supplier selection, clear communication, and proactive management of logistics and quality control to ensure successful outcomes.
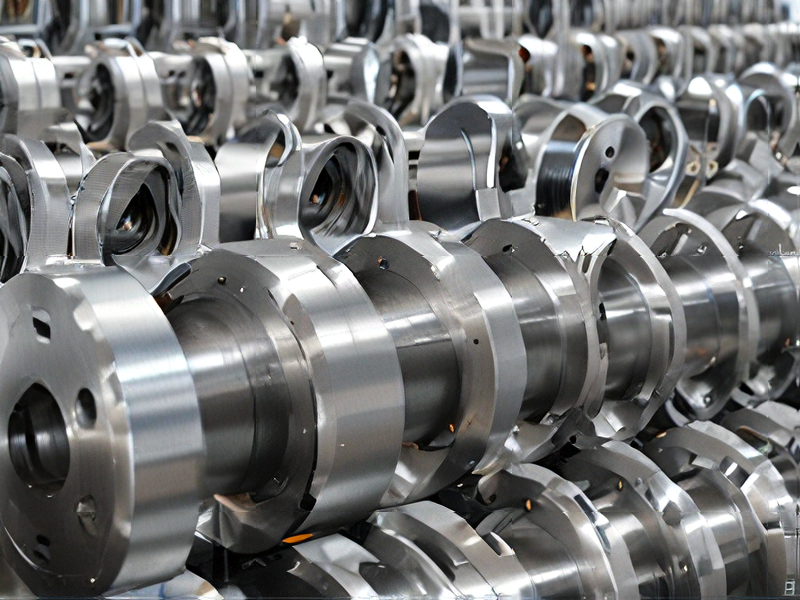