Technology and Applications of fabrication sheet metal
Sheet metal fabrication is a vital process in various industries, involving the shaping of metal sheets into desired forms and structures. Key technologies in this field include:
1. Cutting: Techniques like laser cutting, plasma cutting, and waterjet cutting are used for precision. Laser cutting offers high accuracy for complex shapes, while plasma is efficient for thicker materials. Waterjet cutting is versatile, handling various materials without thermal distortion.
2. Forming: This includes bending, rolling, and stamping. Press brakes bend the metal sheets into desired angles, while rollers shape them into cylindrical forms. Stamping uses dies to form metal parts, ideal for mass production.
3. Joining: Welding (TIG, MIG, spot welding), riveting, and adhesive bonding are common methods. Welding creates strong joints, with TIG being precise for thinner materials and MIG suitable for thicker sections. Riveting provides mechanical strength, while adhesives offer a clean finish without thermal effects.
4. Finishing: Processes like painting, powder coating, and galvanizing enhance appearance and corrosion resistance. Powder coating provides a durable finish, and galvanizing offers excellent protection against rust.
Applications span various industries:
– Automotive: Fabricated sheet metal is crucial in vehicle bodies, chassis, and other components.
– Aerospace: High-strength, lightweight metal sheets are used in aircraft structures and components.
– Construction: Roofing, HVAC ducts, and structural elements rely on sheet metal.
– Consumer Goods: Appliances, electronics enclosures, and furniture often incorporate fabricated metal parts.
Advancements in CNC (Computer Numerical Control) technology and automation have significantly improved precision, efficiency, and repeatability in sheet metal fabrication, making it a cornerstone of modern manufacturing.
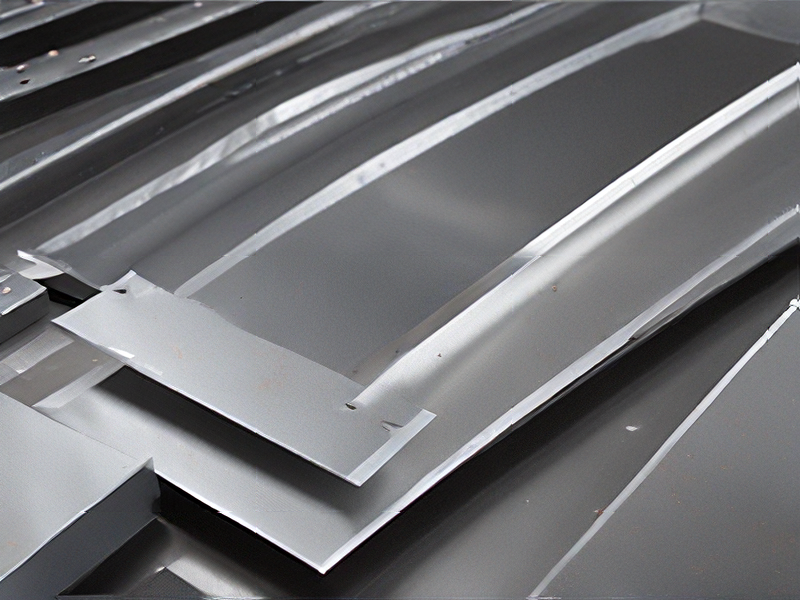
Quality Testing Methods for fabrication sheet metal and how to control quality
Quality testing methods for fabrication sheet metal are essential to ensure products meet the required standards and specifications. Here are some common methods and quality control practices:
Testing Methods
1. Visual Inspection:
– Purpose: Detect surface defects such as scratches, dents, and corrosion.
– Tools: Visual aids like magnifying glasses and proper lighting.
2. Dimensional Inspection:
– Purpose: Ensure dimensions and tolerances are within specified limits.
– Tools: Vernier calipers, micrometers, and coordinate measuring machines (CMM).
3. Non-Destructive Testing (NDT):
– Ultrasonic Testing (UT): Detects internal defects using high-frequency sound waves.
– Radiographic Testing (RT): Uses X-rays or gamma rays to identify internal flaws.
– Magnetic Particle Testing (MPT): Detects surface and slightly subsurface defects in ferromagnetic materials.
– Dye Penetrant Testing (DPT): Reveals surface-breaking defects through capillary action of a dye.
4. Destructive Testing:
– Tensile Testing: Measures material strength and elongation by pulling the sample until it breaks.
– Bend Testing: Assesses ductility and soundness by bending the material.
– Hardness Testing: Determines material hardness using methods like Rockwell, Brinell, or Vickers.
Quality Control Practices
1. Standard Operating Procedures (SOPs):
– Document and adhere to standardized procedures for every stage of fabrication.
2. Material Traceability:
– Maintain records of material sources and batches to trace back any quality issues.
3. Statistical Process Control (SPC):
– Use statistical methods to monitor and control the manufacturing process.
4. Regular Audits and Inspections:
– Conduct routine inspections and audits to ensure compliance with quality standards.
5. Training and Certification:
– Ensure staff are adequately trained and certified to perform specific quality tests.
6. Corrective and Preventive Actions (CAPA):
– Implement CAPA systems to address any identified quality issues and prevent recurrence.
Conclusion
Effective quality testing and control in sheet metal fabrication involve a combination of visual, dimensional, non-destructive, and destructive testing methods, along with stringent quality control practices. These measures ensure the final product meets all required standards and specifications, enhancing reliability and customer satisfaction.
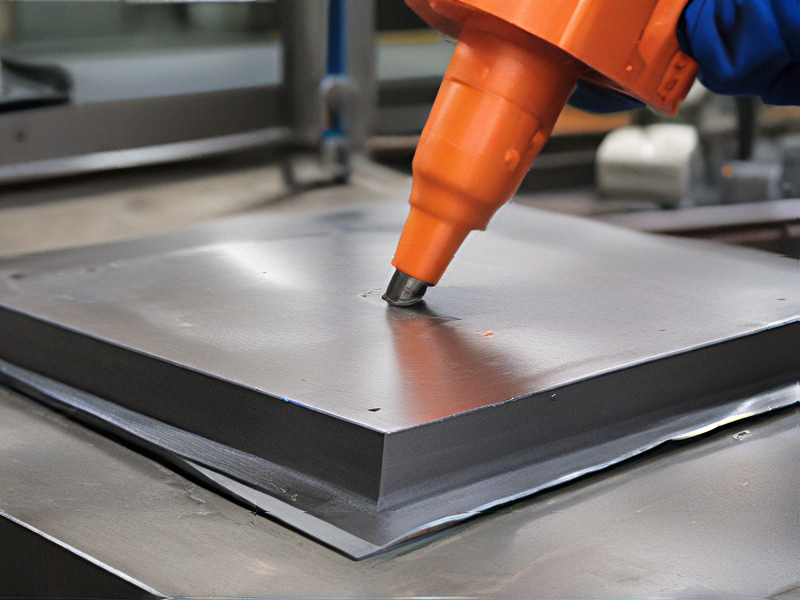
Tips for Procurement and Considerations when Purchasing from fabrication sheet metal
Tips for Procurement and Considerations When Purchasing Sheet Metal Fabrication
1. Define Requirements Clearly:
– Specify material type, thickness, and finish.
– Detail the design specifications, including dimensions, tolerances, and any special features.
2. Supplier Selection:
– Choose suppliers with a proven track record in sheet metal fabrication.
– Verify their certifications (e.g., ISO 9001) and quality control processes.
3. Quality Assurance:
– Request samples or prototypes before placing a bulk order.
– Ensure the supplier has robust inspection and testing procedures.
4. Cost Management:
– Obtain multiple quotes to compare pricing.
– Consider the total cost of ownership, including shipping, handling, and potential import duties.
5. Lead Time and Capacity:
– Confirm the supplier’s production capacity and lead times.
– Plan for any potential delays, especially for complex or large-volume orders.
6. Customization and Flexibility:
– Check the supplier’s ability to handle custom designs and modifications.
– Ensure they can accommodate future changes or additional orders.
7. Technological Capabilities:
– Evaluate the supplier’s equipment and technology, such as CNC machines, laser cutting, and welding capabilities.
– Prefer suppliers who use advanced software for design and manufacturing processes.
8. Sustainability:
– Inquire about the supplier’s environmental policies and practices.
– Consider the use of recycled materials and energy-efficient processes.
9. Communication:
– Maintain clear and frequent communication with the supplier.
– Use project management tools to track progress and address issues promptly.
10. After-Sales Support:
– Ensure the supplier offers adequate after-sales support, including warranties and repair services.
– Verify their responsiveness to post-delivery issues and queries.
By focusing on these aspects, you can ensure a smooth procurement process and obtain high-quality sheet metal fabrication that meets your project needs.
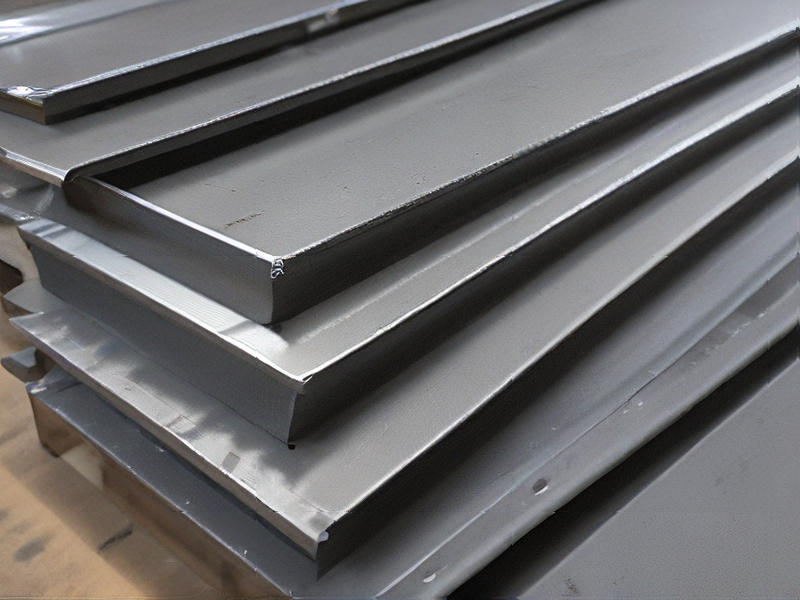
FAQs on Sourcing and Manufacturing from fabrication sheet metal in China
FAQs on Sourcing and Manufacturing Fabricated Sheet Metal in China
1. Why source fabricated sheet metal from China?
China offers competitive pricing, advanced manufacturing capabilities, and a wide range of suppliers experienced in producing high-quality sheet metal components. The country’s extensive supply chain and skilled labor force make it an attractive option for cost-effective and efficient production.
2. What are the key considerations when choosing a supplier?
– Experience and Expertise: Look for suppliers with a proven track record in fabricating sheet metal.
– Certifications: Ensure the supplier has relevant certifications such as ISO 9001.
– Quality Control: Check their quality control processes and inspection capabilities.
– Communication: Strong communication skills and responsiveness are crucial.
3. How can I verify the quality of the products?
– Sample Testing: Request samples before placing a bulk order.
– Factory Audits: Conduct on-site audits to assess the manufacturing processes.
– Third-Party Inspections: Hire independent inspection agencies to verify product quality.
4. What are the common fabrication processes used?
– Laser Cutting: Precise and efficient for various thicknesses.
– Bending and Forming: Shapes metal sheets into desired forms.
– Welding: Joins metal parts securely.
– Punching: Creates holes and shapes in metal sheets.
5. How do I handle logistics and shipping?
– Incoterms: Understand international commercial terms (e.g., FOB, CIF).
– Freight Forwarders: Use reliable freight forwarders for smooth shipping.
– Customs Clearance: Ensure all documentation is accurate to avoid delays.
6. What are the potential risks and how to mitigate them?
– Quality Issues: Regular inspections and clear specifications.
– Communication Barriers: Use bilingual staff or translators.
– Intellectual Property: Use Non-Disclosure Agreements (NDAs) and choose reputable suppliers.
7. How can I ensure sustainable and ethical sourcing?
– Supplier Audits: Regularly audit suppliers for compliance with environmental and labor standards.
– Certifications: Look for suppliers with certifications in sustainable practices.
By addressing these FAQs, you can navigate the complexities of sourcing and manufacturing fabricated sheet metal in China more effectively.
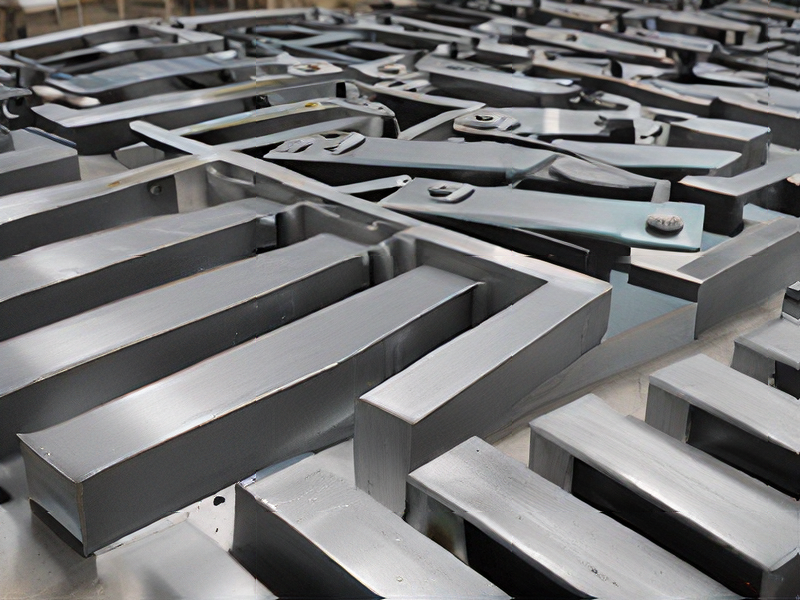