Technology and Applications of galvanization of steel
Galvanization is a process that involves coating steel or iron with a layer of zinc to enhance its corrosion resistance. This technique is vital in various industries due to its ability to prolong the lifespan of steel components in harsh environments.
The most common method of galvanization is hot-dip galvanization, where steel is submerged in molten zinc, allowing a metallurgical bond to form between the two metals. Other methods include electrogalvanization, where an electric current deposits a layer of zinc onto the steel surface, and zinc spray coating, involving the thermal spraying of zinc particles.
Applications of galvanized steel are widespread:
1. Construction: Galvanized steel is used for structural components, roofing, and siding due to its durability and weather resistance.
2. Automotive Industry: Car manufacturers incorporate galvanized components to improve vehicle longevity and performance, especially in areas exposed to moisture.
3. Infrastructure: Galvanized steel is essential for building bridges, railings, and fences, where it helps withstand environmental elements and reduce maintenance costs.
4. Agricultural Equipment: Farm machinery and storage structures benefit from galvanization, as the coating protects against rust and increases equipment lifespan.
5. Electrical Applications: Galvanized steel is often used in electrical towers and poles, providing a safe and long-lasting solution for power distribution.
In summary, galvanization significantly enhances the durability and functionality of steel products, making it a crucial process across multiple sectors, including construction, automotive, infrastructure, agriculture, and electrical applications. Its ability to resist corrosion ensures reduced maintenance costs and improved product lifespan.
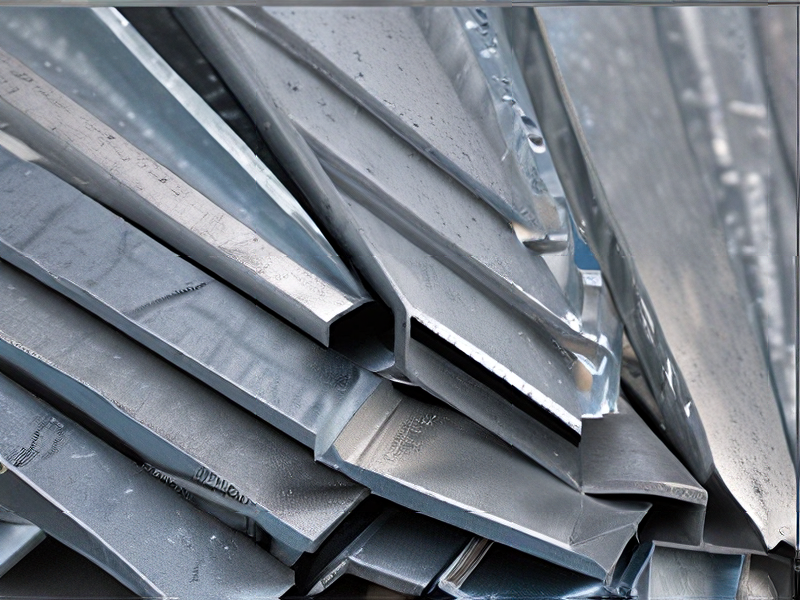
Quality Testing Methods for galvanization of steel and how to control quality
Quality testing of galvanized steel is crucial to ensure durability and corrosion resistance. Here are some effective methods and quality control measures:
Testing Methods:
1. Thickness Measurement: Using a micrometer or an electromagnetic gauge, the thickness of the zinc coating is measured. A standard range is generally between 45-85 microns depending on the application.
2. Adhesion Tests: The adhesion of the zinc coating can be evaluated through the cross-cut test, where a grid pattern is cut into the coating, and adhesive tape is applied to check for any peeling or flaking.
3. Visual Inspection: A visual examination can identify surface defects such as uneven coating or bare spots. Glossiness is also assessed, as a uniform sheen indicates better quality.
4. Salt Spray Test: This accelerated corrosion test exposes galvanized samples to a saline environment, simulating long-term exposure to corrosive conditions. It helps predict longevity.
5. Bending Test: This assesses the ductility of the galvanized coating. The steel is bent at a specified radius, and any cracking in the coating indicates poor quality.
Quality Control Measures:
– Raw Material Inspection: Ensure high-quality steel is used, as impurities can affect the galvanizing process.
– Process Monitoring: Regular monitoring of the galvanizing bath temperature and zinc concentration helps maintain optimal conditions.
– Standards Compliance: Adhere to ASTM A123/A123M or ISO 1461 standards for hot-dip galvanizing.
– Training: Regular training for personnel involved in the galvanization process to ensure best practices.
– Documentation: Maintain records of inspections and tests to trace quality issues back to their source.
By implementing these testing methods and control measures, the quality of galvanized steel can be consistently assured.
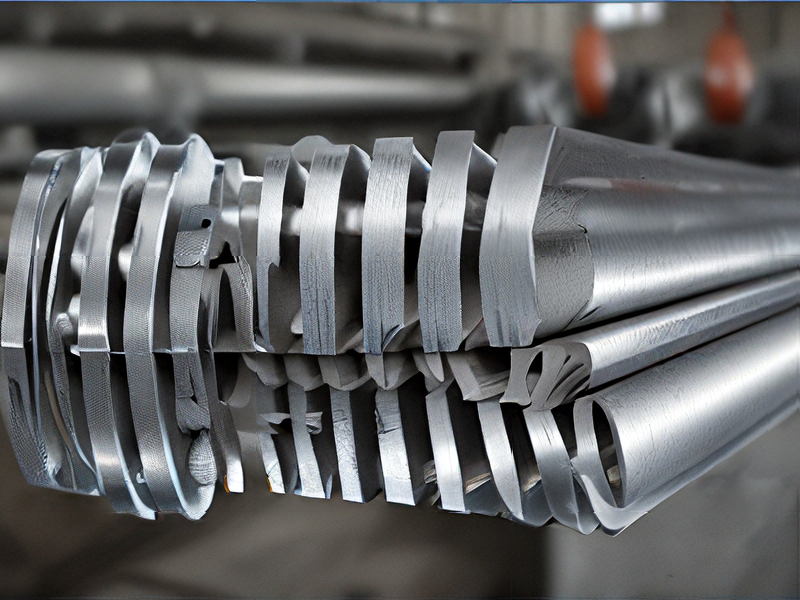
Tips for Procurement and Considerations when Purchasing from galvanization of steel
When procuring galvanized steel, it’s essential to consider several factors to ensure quality and cost-effectiveness. Here are some tips and considerations:
1. Material Specifications: Understand the specific requirements for galvanized steel, including grades, thickness, and coating types. Refer to standards such as ASTM (American Society for Testing and Materials) to ensure compliance.
2. Supplier Evaluation: Research and select reputable suppliers. Assess their track record, production capabilities, and certifications. Request samples to evaluate quality and consistency.
3. Coating Quality: Examine the galvanization process used by suppliers. Hot-dip galvanization typically provides a thicker, more durable coating than electro-galvanization. Ensure that the coating thickness meets the specified standards.
4. Corrosion Resistance: Consider the environment where the steel will be used. Different environments (e.g., coastal, industrial) may require varying levels of corrosion resistance and protection.
5. Cost Analysis: Compare prices among suppliers, but don’t compromise on quality for cost savings. Ultimately, a higher upfront cost for superior quality can lead to lower maintenance and replacement expenses.
6. Lead Times: Assess the supplier’s ability to meet your delivery timelines. Ensure they can accommodate your project schedules without delays.
7. Post-Purchase Support: Inquire about warranties and support services for the galvanized steel. Good suppliers should offer assistance with installation or any issues that arise post-purchase.
8. Sustainability: Look into the environmental practices of the manufacturer. Sourcing from suppliers that adhere to sustainable practices can enhance your corporate responsibility and brand image.
By keeping these considerations in mind, procurement professionals can make informed decisions that align with project requirements and organizational goals.
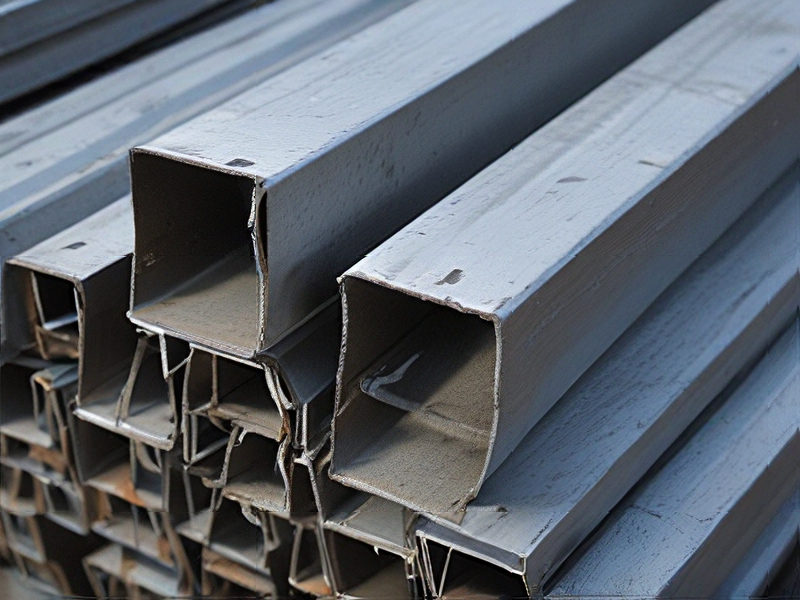
FAQs on Sourcing and Manufacturing from galvanization of steel in China
FAQs on Sourcing and Manufacturing Galvanized Steel in China
1. What is galvanized steel?
Galvanized steel is steel that has been coated with a layer of zinc to prevent rusting and corrosion. This process enhances durability, making it suitable for outdoor applications and harsh environments.
2. Why source galvanized steel from China?
China is one of the largest producers of galvanized steel, offering competitive pricing, a wide range of products, and advanced manufacturing technologies. Many suppliers also provide custom solutions to meet specific project requirements.
3. What are the quality standards for galvanized steel in China?
Galvanized steel in China typically adheres to international standards such as ASTM (American Society for Testing and Materials) or ISO (International Organization for Standardization). Always request certificates and conduct inspections to ensure compliance.
4. What should I consider when selecting a supplier?
Look for suppliers with a proven track record, positive reviews, and certifications. Consider their production capacity, quality control measures, and ability to provide timely deliveries. Request sample products to assess quality.
5. How is the shipping process managed?
Most manufacturers offer assistance with logistics, including shipping and customs clearance. Understand the Incoterms (e.g., FOB, CIF) and confirm that shipping costs and delivery times are clearly outlined in the contract.
6. What are the common applications of galvanized steel?
Galvanized steel is widely used in construction, automotive, agricultural equipment, and manufacturing of appliances due to its resistance to corrosion and longevity.
7. Are there any import duties or regulations to be aware of?
Yes, be aware of any tariffs, import duties, and regulations specific to your country. It’s advisable to consult with a customs broker to navigate these complexities effectively.
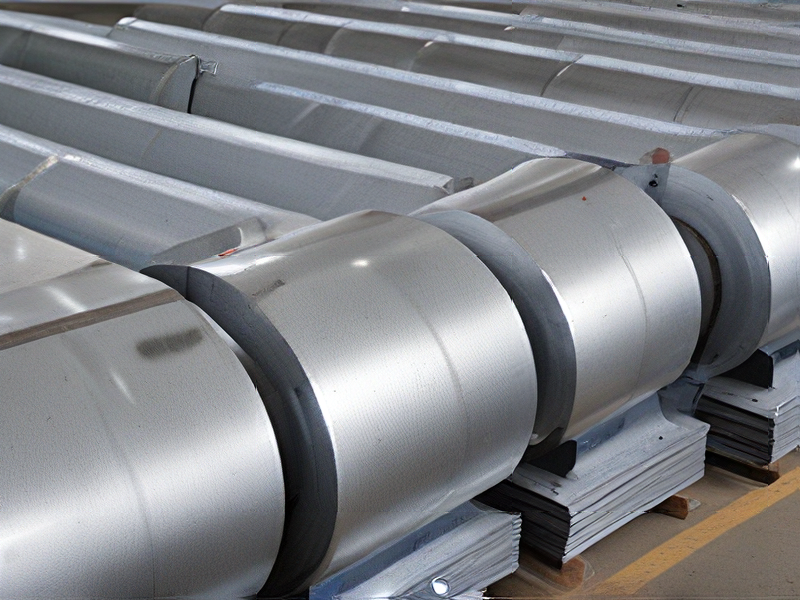