Technology and Applications of galvanized steel metal
Galvanized steel is steel that has been coated with a layer of zinc to prevent corrosion, enhancing its durability and longevity. The galvanization process, typically achieved through hot-dip galvanizing or electro-galvanizing, provides a protective barrier against environmental elements, making it ideal for various applications.
In construction, galvanized steel is widely used in structural components, roofing, and fencing due to its resistance to rust and degradation. It is commonly found in outdoor environments where exposure to moisture and air can lead to corrosion. The material is also essential in the manufacturing of metal frames, scaffolding, and handrails.
In the automotive industry, galvanized steel is utilized for body panels and chassis components, offering resistance to rust and improving the vehicle’s lifespan. Its lightweight properties contribute to fuel efficiency, making it a preferred choice for manufacturers.
Additionally, galvanized steel is prevalent in agriculture, where it is used for storage tanks, silos, and animal enclosures, benefiting from its ruggedness and low maintenance. The electrical sector also employs galvanized steel for utility poles and telecommunications towers, leveraging its strength and weather resistance.
Galvanized steel’s versatility extends to consumer goods, including appliances and furniture, where its aesthetic appeal and robust characteristics are appreciated. The low-cost manufacturing process and the availability of recycled materials further enhance its sustainability profile.
In summary, galvanized steel is a key material across multiple industries, combining strength, flexibility, and corrosion resistance, thereby facilitating innovations and applications in modern technology and infrastructure.
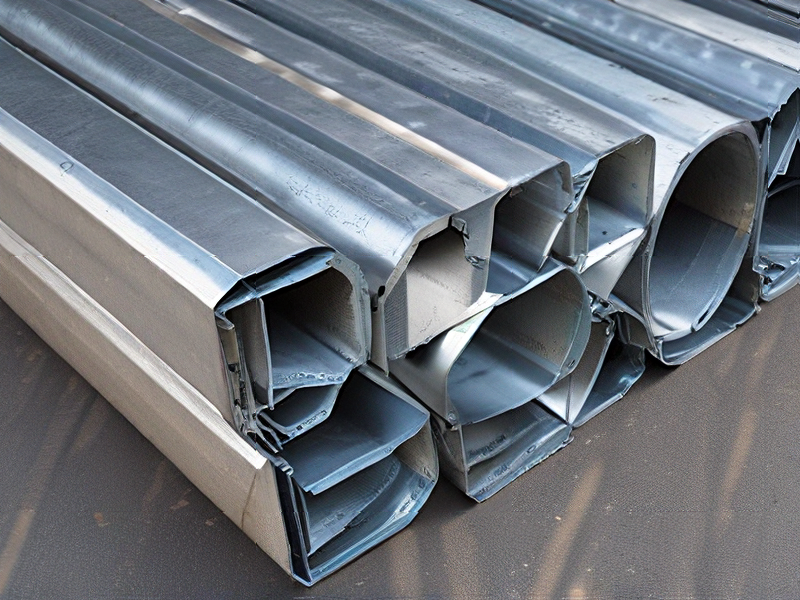
Quality Testing Methods for galvanized steel metal and how to control quality
Quality testing of galvanized steel is crucial to ensure durability, corrosion resistance, and adherence to industry standards. Here are some effective methods and control measures:
Testing Methods:
1. Thickness Measurement: Use non-destructive methods like magnetic gauges or eddy current testing to assess the zinc coating thickness, which should typically meet ASTM A123 or other relevant standards.
2. Adhesion Testing: Conduct a peel test to evaluate the bond between the zinc coating and the steel substrate. A satisfactory bond minimizes the risk of delamination.
3. Corrosion Resistance Testing: Subject samples to accelerated corrosion tests (e.g., salt spray test as per ASTM B117) to evaluate the coating’s protective qualities over time.
4. Visual Inspection: Regularly inspect for defects such as blisters, bare spots, and uneven coating. This can help identify potential issues early in production.
5. Microstructure Analysis: Use microscopy to inspect the zinc layer’s microstructure, ensuring the proper formation of zinc-iron alloys, which enhances corrosion resistance.
Quality Control Measures:
1. Standard Operating Procedures (SOPs): Implement clear SOPs for the galvanizing process, including proper surface preparation, bath temperature, and immersion time.
2. Training: Regular training for personnel involved in the galvanizing process to ensure they adhere to best practices and understand quality requirements.
3. Routine Audits: Conduct internal audits and inspections to verify compliance with industry standards and internal quality benchmarks.
4. Supplier Quality Management: Ensure that raw materials meet specified standards and that suppliers are regularly evaluated for quality compliance.
5. Documentation and Traceability: Maintain detailed records of testing results and production processes to facilitate accountability and trace any quality issues that may arise.
By employing these testing methods and quality control measures, manufacturers can ensure high-quality galvanized steel products that meet customer and industry specifications.

Tips for Procurement and Considerations when Purchasing from galvanized steel metal
When procuring galvanized steel, several key considerations can ensure you make informed purchasing decisions:
1. Material Specification: Ensure the galvanized steel meets relevant standards (e.g., ASTM A123 for hot-dip galvanizing). Review specifications for thickness, grade, and coating type to match your project requirements.
2. Supplier Reputation: Choose a reputable supplier with a track record in providing quality galvanized steel. Read reviews, ask for references, and assess their quality control processes.
3. Zinc Coating: The thickness of the galvanized coating directly impacts corrosion resistance. Verify the coating’s weight (in grams per square meter); heavier coatings offer better protection, especially for harsh environments.
4. Application Needs: Consider the steel’s intended use—structural, aesthetic, or both. Different applications may require specific properties, such as tensile strength or corrosion resistance.
5. Cost Considerations: Compare prices among suppliers but prioritize quality and service. Lowest cost may not equate to the best value, especially if it compromises quality.
6. Lead Time: Assess supplier lead times to align with your project schedule. Delays in procurement can affect overall timelines.
7. Sustainability: If sustainable practices are important for your project, choose suppliers committed to environmentally responsible methods, such as recycling steel.
8. After-Sales Support: Understand the supplier’s after-sale service, including warranties, technical support, and availability of replacement parts, which can be crucial for ongoing projects.
By carefully evaluating these factors, you can make strategic procurement decisions that ensure the quality and longevity of your galvanized steel applications.

FAQs on Sourcing and Manufacturing from galvanized steel metal in China
FAQs on Sourcing and Manufacturing Galvanized Steel from China
1. What is galvanized steel?
Galvanized steel is steel that has been coated with a layer of zinc to prevent rusting. This makes it suitable for various applications, especially outdoors or in moist environments.
2. Why source galvanized steel from China?
China is one of the largest producers of galvanized steel, providing competitive pricing, extensive manufacturing capabilities, and a wide range of product options.
3. What are the typical applications of galvanized steel?
Common applications include construction materials, automotive parts, roofing, fencing, HVAC systems, and various industrial components.
4. How do I choose a reliable supplier?
Research potential suppliers by checking their certifications (ISO, CE), reviewing client testimonials, and assessing their production capacities through site visits or virtual tours.
5. What quality standards should I look for?
Ensure that the product meets international standards such as ASTM, EN, or JIS, which specify the quality and performance characteristics of galvanized steel.
6. What is the minimum order quantity (MOQ)?
MOQ varies by supplier and product type. Typically, it ranges from a few tons to several hundred tons, depending on the manufacturer.
7. What are the shipping options?
Common shipping methods include ocean freight, air freight, or rail. Ocean freight is the most economical for large orders, while air freight is faster for smaller quantities.
8. Are there customs duties when importing?
Yes, there may be customs duties and taxes depending on your country’s regulations. Always check local import laws before placing orders.
9. How long does manufacturing and shipping take?
Manufacturing time can range from a few weeks to several months, depending on order size and complexity. Shipping can take additional weeks based on the method chosen.
