Technology and Applications of horizontal machining centers
Horizontal machining centers (HMCs) are advanced machine tools widely used in the manufacturing industry for their precision, efficiency, and versatility. Unlike vertical machining centers (VMCs), HMCs have a horizontally oriented spindle, which allows for better chip evacuation, improved tool life, and enhanced machining capabilities.
Technology
Spindle Orientation: The horizontal spindle orientation is the defining feature, which facilitates better chip removal by gravity, reducing heat build-up and improving surface finish.
Rotary Table: HMCs typically feature a rotary table, enabling multi-face machining in a single setup. This reduces the need for part repositioning, improving accuracy and reducing cycle times.
Pallet Changer: Many HMCs are equipped with a pallet changer system, allowing operators to load and unload parts while the machine is in operation. This feature significantly boosts productivity and reduces downtime.
Tool Magazine: HMCs come with large tool magazines that can hold numerous tools, allowing for complex machining operations without the need for manual tool changes.
Applications
Automotive Industry: HMCs are widely used in the automotive sector for machining engine blocks, transmission cases, and other critical components. Their ability to handle large, heavy parts and perform multiple operations in a single setup makes them invaluable.
Aerospace Industry: In aerospace, HMCs are essential for producing complex, high-precision parts like turbine blades, aircraft structures, and landing gear components. The high rigidity and accuracy of HMCs ensure the production of components that meet stringent industry standards.
General Manufacturing: HMCs are used across various manufacturing industries for producing parts with complex geometries. Their versatility allows for a wide range of applications, from heavy-duty cutting to high-speed finishing.
Die and Mold: The ability to machine intricate details and maintain high precision makes HMCs ideal for die and mold manufacturing, where accuracy is paramount.
Conclusion
Horizontal machining centers represent a significant advancement in machining technology, offering improved efficiency, accuracy, and versatility. Their application across various industries highlights their critical role in modern manufacturing processes.
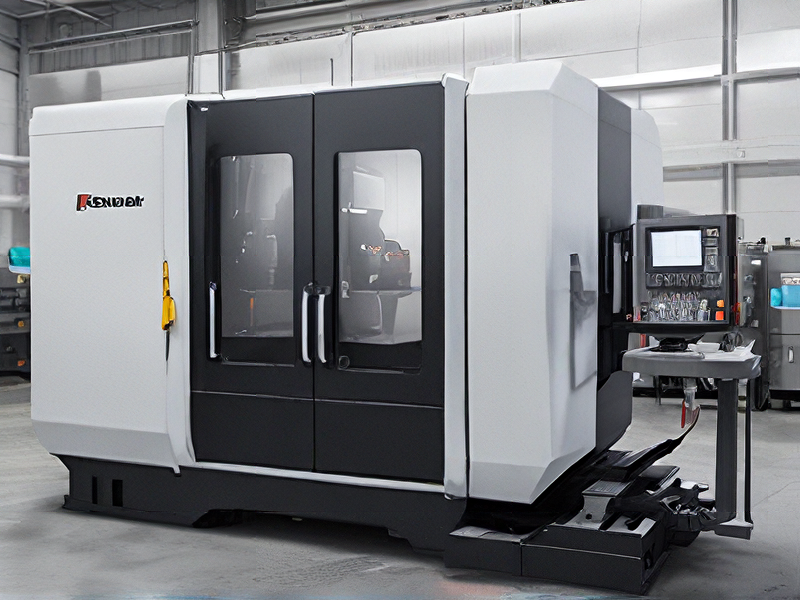
Quality Testing Methods for horizontal machining centers and how to control quality
Quality testing for horizontal machining centers (HMCs) involves several methods to ensure precision, performance, and reliability. These include:
1. Geometric Accuracy Tests: Checking the alignment and accuracy of machine components using laser interferometers, ballbars, and dial indicators to measure straightness, flatness, and angular deviations.
2. Dimensional Accuracy Tests: Using coordinate measuring machines (CMMs) and precision gauges to verify that machined parts meet specified tolerances.
3. Surface Finish Tests: Employing profilometers and surface roughness testers to ensure the quality of the machined surface.
4. Thermal Stability Tests: Monitoring the machine’s response to thermal variations through thermal imaging and temperature sensors to ensure consistent performance.
5. Vibration Analysis: Using accelerometers and vibration analyzers to detect and mitigate excessive vibrations that can affect machining accuracy.
6. Load Tests: Evaluating the machine’s performance under various load conditions to ensure it can handle the specified workpiece sizes and weights without compromising accuracy.
7. Cycle Time Analysis: Comparing actual machining cycle times against expected values to identify inefficiencies or issues in the machining process.
Quality Control Methods:
1. Statistical Process Control (SPC): Implementing SPC charts to monitor and control the machining process, ensuring consistency and identifying trends or deviations.
2. Preventive Maintenance: Regularly scheduled maintenance tasks to keep the HMC in optimal working condition, reducing downtime and preventing unexpected failures.
3. Calibration: Periodic calibration of the machine and its measuring instruments to maintain accuracy.
4. Operator Training: Ensuring that operators are well-trained in using the HMC and understanding quality control measures to reduce human error.
5. Process Documentation: Maintaining detailed records of machining processes, quality checks, and maintenance activities to trace and address any quality issues.
6. Automation and Sensors: Utilizing automated systems and sensors for real-time monitoring and adjustments to maintain machining precision and quality.
By integrating these methods, manufacturers can ensure the high-quality performance of horizontal machining centers, leading to superior product quality and operational efficiency.
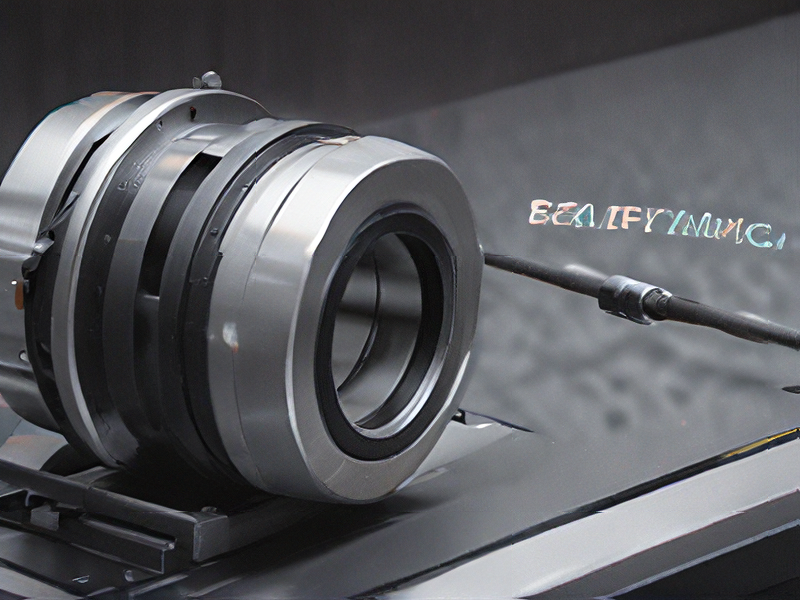
Tips for Procurement and Considerations when Purchasing from horizontal machining centers
When procuring horizontal machining centers (HMCs), consider the following tips to ensure you make an informed decision:
1. Define Requirements:
– Workload Capacity: Assess the volume and complexity of the machining tasks. Ensure the HMC can handle the required workload and part sizes.
– Precision and Speed: Evaluate the precision and speed requirements of your projects to match the HMC’s capabilities.
2. Evaluate Technical Specifications:
– Spindle Speed and Power: Higher spindle speeds and power are essential for efficient cutting of various materials.
– Tool Capacity: A larger tool magazine allows for greater flexibility and reduces downtime for tool changes.
– Axis Travel and Work Envelope: Ensure the machine’s axis travel and work envelope accommodate your largest parts.
3. Quality and Reliability:
– Brand and Model Reputation: Research the reliability and performance of different brands and models. User reviews and expert opinions can be valuable.
– Build Quality: Check for robust construction and durable materials to ensure long-term performance.
4. Advanced Features:
– Automation and Integration: Consider HMCs with automation capabilities, such as pallet changers and robotic integration, to enhance productivity.
– Software Compatibility: Ensure the machine is compatible with your existing CAD/CAM software for seamless integration.
5. Cost Considerations:
– Initial Investment: Compare prices across different suppliers while considering the machine’s features and capabilities.
– Operating Costs: Factor in the cost of maintenance, tooling, and energy consumption. Opt for energy-efficient models if possible.
6. Support and Service:
– Supplier Support: Choose suppliers with a strong support network, including training, technical support, and readily available spare parts.
– Warranty and Maintenance: Ensure comprehensive warranty coverage and consider service contracts for regular maintenance.
7. Future-Proofing:
– Scalability: Select machines that can be upgraded or expanded to accommodate future growth and technological advancements.
Thoroughly evaluate these aspects to ensure the HMC you choose aligns with your production needs and long-term goals.
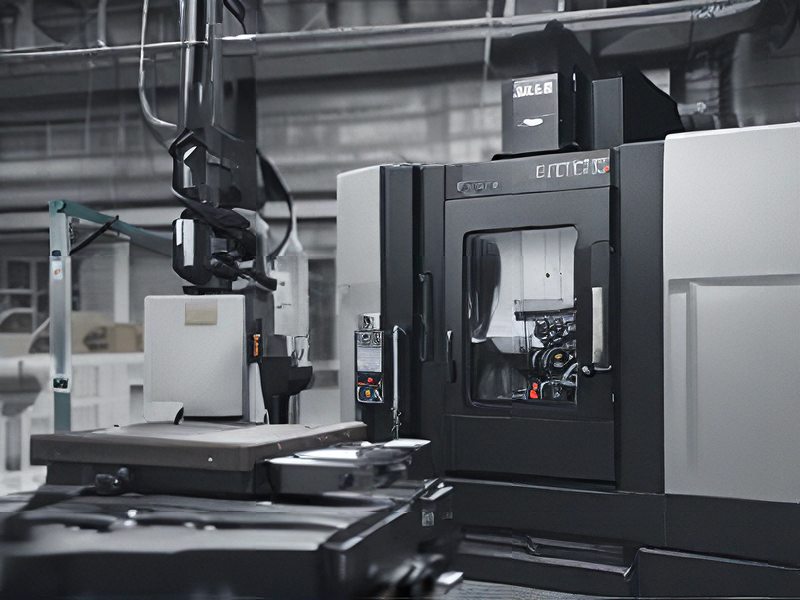
FAQs on Sourcing and Manufacturing from horizontal machining centers in China
FAQs on Sourcing and Manufacturing from Horizontal Machining Centers in China
1. What are Horizontal Machining Centers (HMCs)?
HMCs are advanced CNC (Computer Numerical Control) machines that perform various milling operations. They are characterized by their horizontal spindle orientation, which allows for efficient chip evacuation and multiple side machining in one setup.
2. Why source from China?
China offers competitive pricing, advanced technology, and a vast network of suppliers. The country has become a global hub for manufacturing, providing high-quality machinery and components.
3. What industries benefit from HMCs?
HMCs are widely used in automotive, aerospace, medical device manufacturing, and general engineering industries due to their precision and efficiency.
4. How to select a supplier in China?
Consider the supplier’s experience, certifications (ISO 9001), customer reviews, and the quality of their machines. Visiting the factory or requesting samples can also provide insight into their capabilities.
5. What are the key factors in evaluating HMCs?
Look for precision, reliability, spindle speed, tool capacity, and the machine’s ability to handle complex geometries. After-sales service and technical support are also crucial.
6. Are there risks involved?
Yes, risks include potential communication barriers, quality control issues, and longer lead times. Mitigate these by establishing clear contracts, conducting thorough due diligence, and using third-party inspection services.
7. How to ensure quality control?
Implement stringent quality checks, use third-party inspection services, and establish clear specifications and standards in contracts. Regularly monitor production processes and provide feedback.
8. What are the cost considerations?
Costs include the price of the machine, shipping, customs duties, and any modifications required. Additionally, consider ongoing maintenance and potential downtime costs.
9. How to manage logistics?
Work with experienced logistics providers familiar with importing machinery. Ensure proper documentation, including invoices, packing lists, and certificates of origin, to avoid delays.
10. What about intellectual property (IP) protection?
Use non-disclosure agreements (NDAs) and choose reputable suppliers with a track record of IP respect. Registering patents or trademarks in China can provide additional protection.
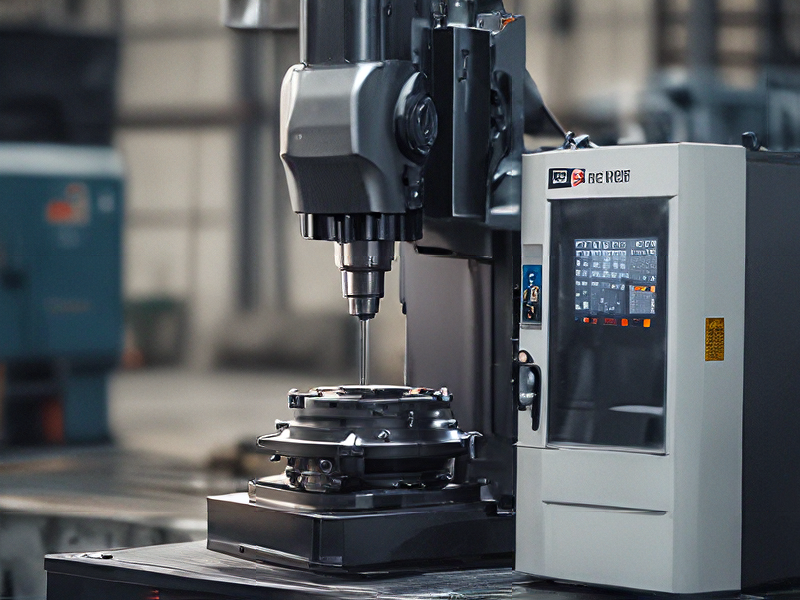