Technology and Applications of industrial metal supply
Industrial metal supply plays a crucial role in various sectors, including construction, manufacturing, and aerospace. The technology and applications in this field are continually evolving to meet demands for efficiency, sustainability, and innovation.
Technology: Advanced technologies such as automation, the Internet of Things (IoT), and artificial intelligence (AI) are transforming metal supply chains. Automated processes improve accuracy in inventory management and reduce human error. IoT devices enable real-time tracking of metal stocks, ensuring timely replenishment and optimal resource utilization. AI algorithms analyze market trends and demand forecasts, helping suppliers optimize production schedules and maintain competitive pricing.
Applications: Industrial metals, including steel, aluminum, copper, and titanium, are integral to a wide array of applications. In construction, steel is a fundamental material for structural frameworks, while aluminum is prized for its lightweight and corrosion-resistant properties in both structural and decorative applications. In the automotive sector, metals are essential for manufacturing vehicles with better fuel efficiency and safety features. Aerospace industries rely on specialized alloys like titanium for their strength-to-weight ratio and heat resistance, enhancing aircraft performance and longevity.
Sustainability is another key focus, with industries increasingly adopting recycled metals to reduce environmental impact. Innovations such as additive manufacturing (3D printing) are also gaining traction, allowing for the creation of complex metal parts with minimal waste.
In summary, the intersection of technology and applications in industrial metal supply is driving forward efficiency, sustainability, and innovation, reshaping how industries source and utilize essential materials.

Quality Testing Methods for industrial metal supply and how to control quality
Quality testing in industrial metal supply is crucial to ensure materials meet specifications and perform reliably in applications. Here are key methods and control measures:
1. Visual Inspection: The first line of defense, involving the assessment of surface condition for defects such as cracks, corrosion, or improper finishes.
2. Mechanical Testing:
– Tensile Testing: Measures the strength and ductility of materials by pulling samples until they break.
– Hardness Testing: Assesses resistance to deformation using methods like Brinell, Rockwell, or Vickers tests.
– Impact Testing: Evaluates toughness by measuring the energy absorbed during fracture of a standard specimen under impact load (e.g., Charpy test).
3. Chemical Analysis: Ensures the composition of metal meets specified standards, using techniques like spectroscopy or mass spectrometry to detect alloying elements.
4. Non-Destructive Testing (NDT): Techniques such as ultrasonic testing, magnetic particle testing, and radiographic inspection identify internal and surface defects without damaging the material.
5. Metallographic Examination: Involves microscopic analysis of metal structure, aiding in the assessment of grain size, phase distribution, and overall integrity.
Quality Control Measures:
– Standard Operating Procedures (SOPs): Establish clear protocols for testing, handling, and reporting of results.
– Supplier Quality Assurance: Implement rigorous evaluation and approval processes for suppliers, ensuring compliance with industry standards (e.g., ISO 9001).
– Regular Training: Equip personnel with the necessary skills and knowledge to perform tests effectively and interpret results accurately.
– Documentation and Traceability: Maintain records of all tests and inspections to trace back materials to their source, supporting accountability and compliance.
By combining these methodologies and controls, companies can ensure consistent quality in their metal supply, reducing risks in manufacturing and end-use applications.
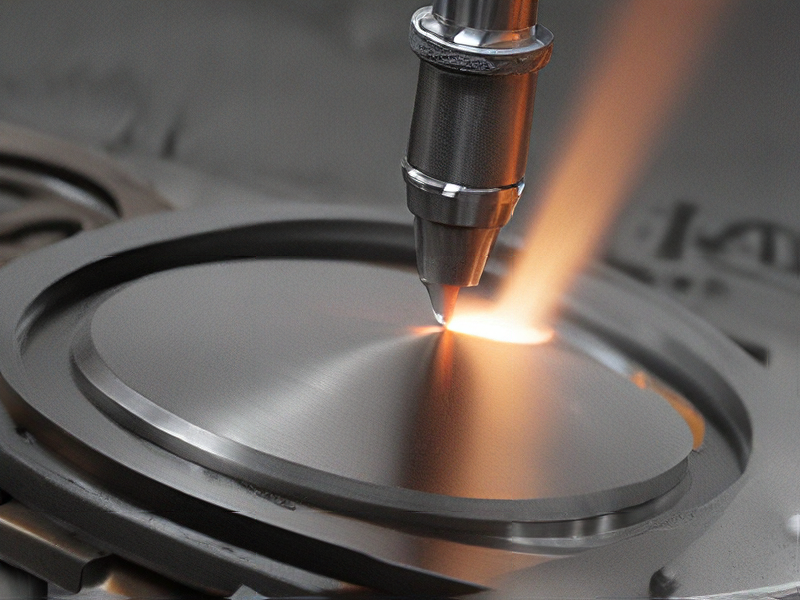
Tips for Procurement and Considerations when Purchasing from industrial metal supply
When procuring from industrial metal suppliers, several key considerations can optimize your purchasing experience. Here are essential tips to consider:
1. Identify Requirements: Clearly define the specifications of the metal you need, including type, grade, thickness, and dimensions. Understanding your requirements minimizes errors and ensures you order the correct material.
2. Quality Assurance: Verify the supplier’s quality certifications, such as ISO or ASTM compliance. This ensures that the metal meets industry standards and will perform adequately for your application.
3. Supplier Reputation: Research the supplier’s reputation in the industry. Read reviews, seek references, and evaluate their history in delivering quality products and services. A reliable supplier can be a key partner in your supply chain.
4. Cost Analysis: While price is important, assess the total cost of ownership, which includes shipping, handling, and potential waste or defects. Sometimes, a higher upfront cost results in better quality and lower long-term expenses.
5. Lead Times: Confirm the supplier’s lead times and ability to meet your deadlines. Delays in delivery can disrupt your production schedule, so having a clear timeline is crucial.
6. Customization Options: If your project requires specific modifications, check if the supplier offers customization services, such as cutting or machining, to better suit your needs.
7. Sustainability Practices: Consider suppliers that engage in sustainable practices. Environmentally responsible sourcing is increasingly important and can enhance your company’s corporate responsibility profile.
8. After-Sales Support: Evaluate the supplier’s customer service and support capabilities. Good after-sales support can address potential issues quickly and enhance your overall experience.
By following these guidelines, you can make informed procurement decisions that align with your project’s requirements and enhance operational efficiency.

FAQs on Sourcing and Manufacturing from industrial metal supply in China
FAQs on Sourcing and Manufacturing Industrial Metal Supply in China
1. What are the benefits of sourcing from China?
China offers competitive pricing, a wide range of materials, established supply chains, and experienced manufacturers, making it a desirable location for industrial metal sourcing.
2. How do I find a reliable supplier?
Conduct thorough research through online platforms like Alibaba, Global Sources, and Made-in-China. Check supplier credentials, customer reviews, and request references. Engaging a sourcing agent can also help.
3. What should I consider when negotiating prices?
Discuss minimum order quantities, payment terms, and delivery timelines. Consider including quality assurance and inspection clauses in the agreement to ensure product standards.
4. How can I ensure quality control?
Establish clear specifications for materials and manufacturing processes. Consider hiring third-party inspection services to conduct quality checks during production and before shipment.
5. What are typical payment terms?
Standard terms include a deposit (usually 30%) upfront, with the balance paid before shipment. Be cautious and use secure payment methods to protect your investment.
6. What shipping options are available?
Common shipping methods include air freight for smaller, urgent orders, and sea freight for larger shipments. Assess costs and delivery times based on your needs.
7. Are there any regulatory issues to consider?
Be aware of international trade regulations, import duties, and tariffs that may impact your shipment. Consult with legal experts to ensure compliance with your country’s import laws.
8. What about lead times?
Lead times can vary based on order size and complexity but typically range from 4 to 12 weeks. Always confirm with your supplier for a more accurate estimate.
9. Can I customize metal products?
Yes, many manufacturers in China offer customization, including specific dimensions, materials, and finishes, but discuss this during the initial negotiation.
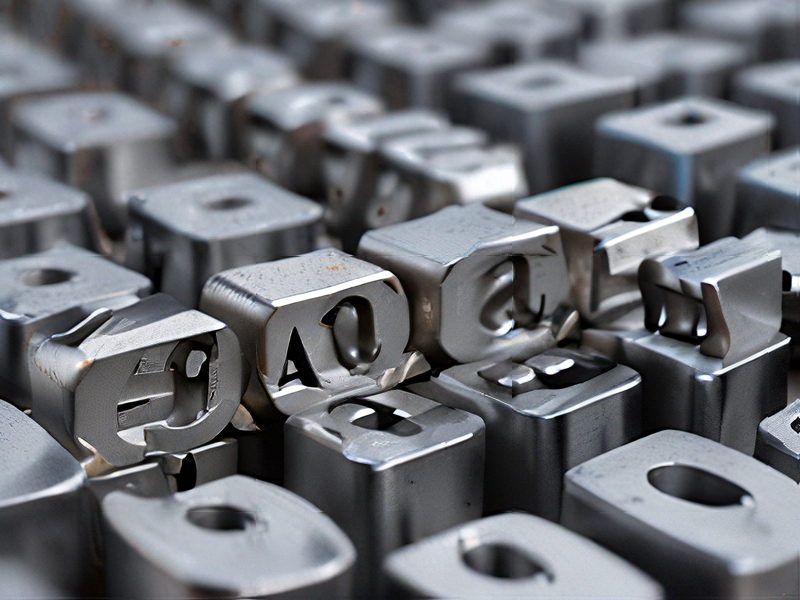