Technology and Applications of laser and cutting machine
Laser cutting technology has revolutionized various industries, significantly enhancing precision and efficiency in material processing. Utilizing focused laser beams, this method melts, burns, or vaporizes materials, offering high-speed cutting with intricate designs and minimal waste.
Applications:
1. Manufacturing: In metal fabrication, laser cutting is employed for creating complex shapes in steel, aluminum, and other materials. Its precision reduces the need for secondary operations, improving overall productivity.
2. Aerospace: The aerospace sector relies on laser cutting for lightweight and durable components, providing precision in fabricating intricate parts that meet rigorous safety standards.
3. Automotive: Automobile manufacturers use laser cutting for cutting body panels and intricate components, allowing for lightweight designs that enhance fuel efficiency and performance.
4. Textiles: In the textile industry, lasers enable precise cutting of fabrics, which prevents fraying and improves the quality of finished garments.
5. Medical Devices: The ability to cut small and precise components makes laser cutting invaluable in producing medical devices and instruments, which often require strict tolerances.
6. Signage and Decor: Lasers allow for the precise cutting of materials such as acrylic and wood, making them highly effective for creating detailed signage and decorative elements.
Advantages:
– Precision: Laser cutting achieves high accuracy, enabling detailed work that is difficult to achieve with traditional methods.
– Versatility: It can cut a wide variety of materials, including metals, plastics, wood, and textiles.
– Efficiency: High speed and reduced material wastage lead to cost savings for manufacturers.
In summary, laser cutting technology is a powerful tool across multiple industries, providing enhanced precision, efficiency, and versatility in material processing.
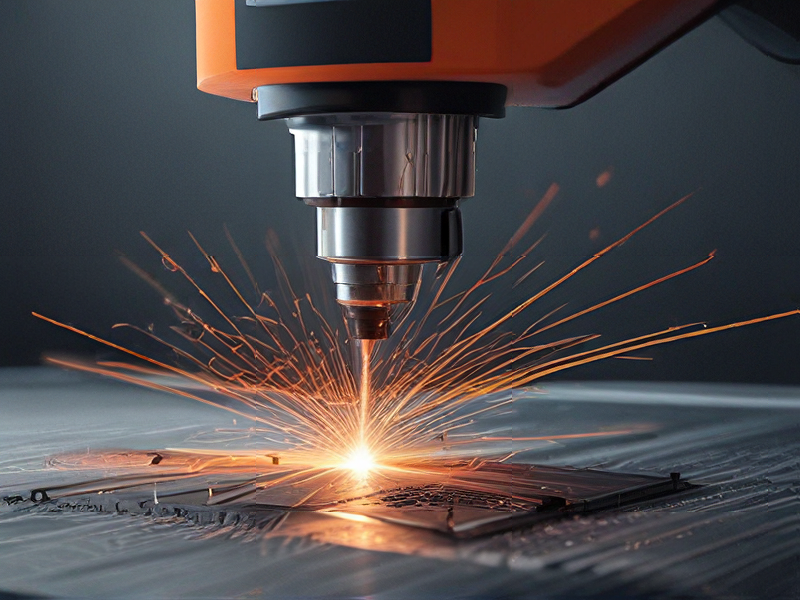
Quality Testing Methods for laser and cutting machine and how to control quality
Quality testing for laser and cutting machines is essential to ensure precision, reliability, and performance. Here are key methods and controls:
1. Calibration: Regular calibration of the machine is crucial. Use standardized test materials and compare results with the specified standards to ensure precision in cutting dimensions.
2. Visual Inspection: Conduct a thorough visual inspection of cuts for uniformity, surface finish, and edge quality. Look for signs of melting, burrs, or warping, which indicate issues with power settings or material handling.
3. Dimensional Verification: Measure cut parts with calipers or laser measurement tools. Precision requires that cuts meet defined tolerances as per engineering drawings.
4. Performance Testing: Evaluate the machine’s cutting speed and efficiency. Monitor the time it takes to perform cuts and how that aligns with production goals.
5. Material Testing: Use different materials during tests to assess how the machine handles various thicknesses and types, ensuring adaptability and consistency in outputs.
6. Software Calibration: Check the software settings regularly. Any discrepancies in settings can affect the quality of cuts.
7. Usage Data Monitoring: Implement monitoring systems to track machine performance, error rates, and downtime. Analyze this data to identify trends and areas needing improvement.
8. Operator Training: Ensure operators are well-trained on machine settings and maintenance procedures. Knowledgeable operators can mitigate many quality issues.
By employing these testing methods and controls, businesses can maintain high-quality standards in laser cutting operations, ultimately leading to increased efficiency and customer satisfaction.
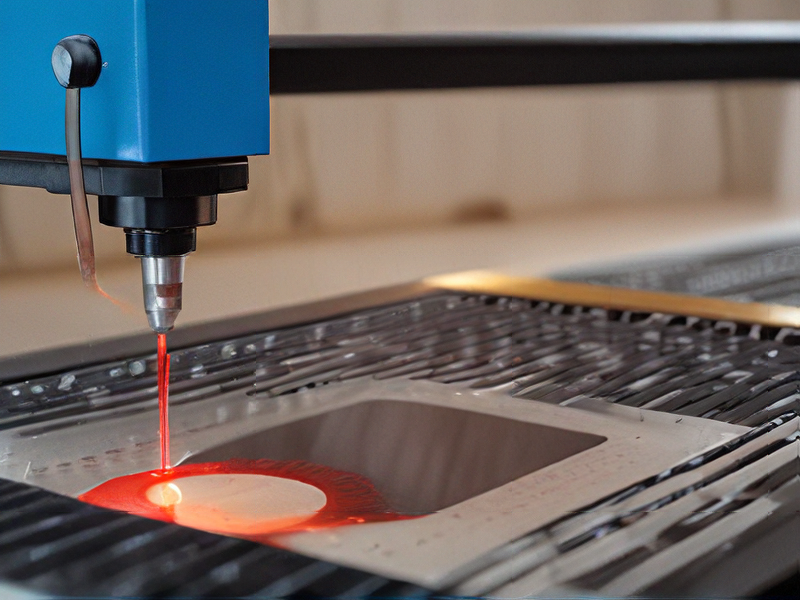
Tips for Procurement and Considerations when Purchasing from laser and cutting machine
When procuring a laser and cutting machine, consider the following tips to ensure a smart investment:
1. Define Your Requirements: Clearly outline what materials you will be cutting (e.g., metal, wood, fabric) and the thicknesses you anticipate. Identify the types of projects you plan to undertake, which will help you choose the appropriate type of laser (CO2, fiber, etc.).
2. Budget: Establish a budget that includes not just the purchase price but also installation, training, maintenance, and consumables (like lenses and filters).
3. Supplier Reputation: Research potential suppliers. Look for reviews, testimonials, and case studies to gauge their reliability and customer service.
4. Machine Specifications: Compare technical specifications such as cutting speed, precision, power, and bed size. Make sure the machine’s capabilities align with your operational needs.
5. Support and Warranty: Ensure the machine comes with a comprehensive warranty and that the supplier provides solid customer support. Quick access to parts and technical assistance can minimize downtime.
6. Future Scalability: Consider whether the machine can adapt to your future needs. If your business grows, you may require a machine with greater capabilities.
7. Software Compatibility: Check whether the machine is compatible with the design software you currently use or plan to use.
8. Training and Safety: Ensure that the supplier offers adequate training for your team and emphasizes safety protocols, as laser cutting can pose hazards.
By carefully evaluating these factors, you can minimize risks and optimize your purchasing decision, ultimately enhancing your production efficiency and quality.
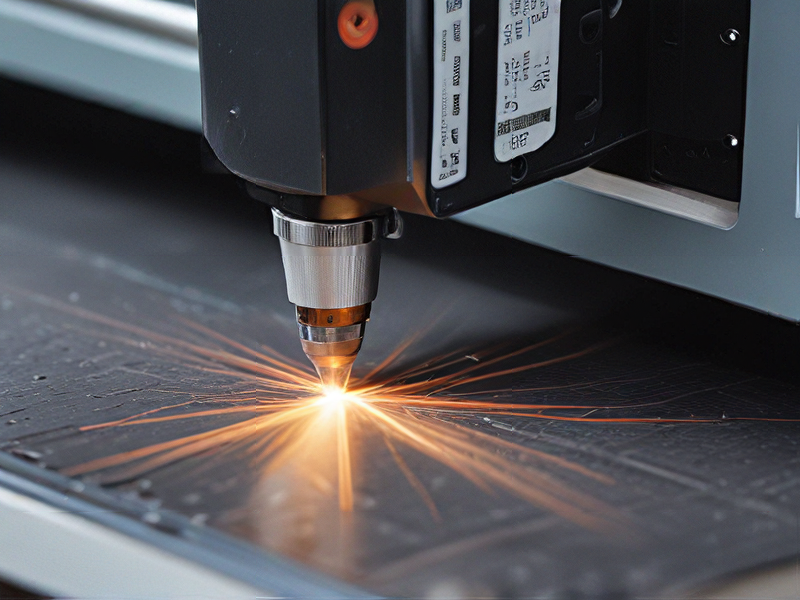
FAQs on Sourcing and Manufacturing from laser and cutting machine in China
FAQs on Sourcing and Manufacturing Laser and Cutting Machines in China
1. Why choose China for laser and cutting machines?
China is a leading manufacturer with advanced technology, competitive pricing, and a vast supply chain. Its factories are equipped with modern machinery and skilled labor, making it ideal for sourcing.
2. How do I find reliable suppliers?
Utilize platforms like Alibaba, Made-in-China, and Global Sources. Verify suppliers through trade shows, reviews, and certifications (ISO, CE).
3. What should I consider when evaluating a supplier?
Assess their production capacity, quality control measures, lead times, and after-sales support. Request product samples to evaluate quality before placing larger orders.
4. What are the common payment methods?
Common methods include T/T (telegraphic transfer), PayPal, and L/C (letter of credit). Each has its pros and cons regarding security and speed.
5. How can I ensure product quality?
Implement strict quality control measures. Consider hiring a third-party inspection service at various production stages or before shipment.
6. What about shipping and customs?
Work with a reliable freight forwarder to handle shipping logistics. Understand customs regulations and duties that might apply upon importation.
7. What are the delivery lead times?
Lead times vary based on order size and seasonality but typically range from 30 to 90 days. Confirm timelines with your supplier.
8. Can I customize the machines?
Yes, many manufacturers offer customization options. Provide specific requirements, such as size, features, or branding.
9. What support is available post-purchase?
Check if the supplier offers warranties, spare parts, and technical support. Ensure they can provide service remotely or on-site if needed.
10. What are the advantages of local sourcing?
Local sourcing reduces shipping times and costs and enhances communication and problem resolution.
By conducting thorough research and due diligence, businesses can successfully source high-quality laser and cutting machines from China.
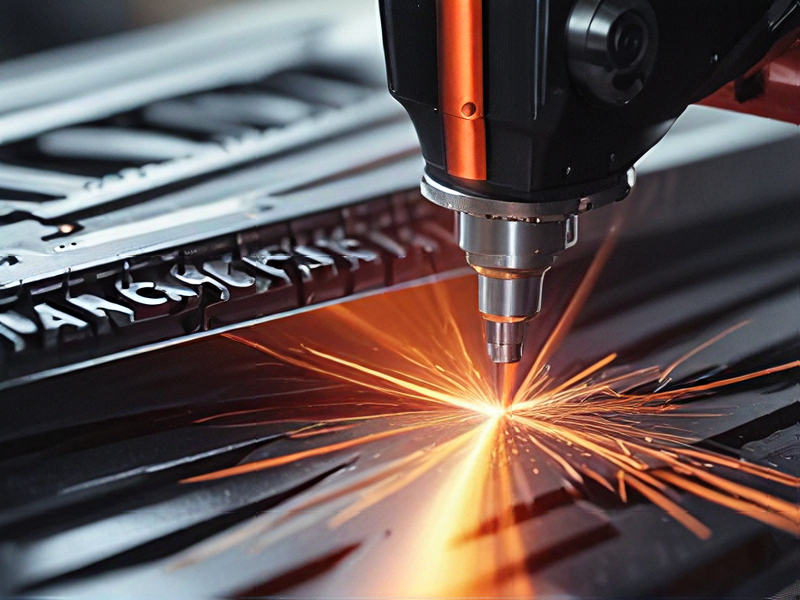