Technology and Applications of laser carving machine
Laser carving machines utilize focused laser beams to engrave or cut materials with high precision, making them valuable tools in various industries. The technology relies on a laser source—commonly CO2, fiber, or diode lasers—that emits concentrated light, which is directed through optics to focus on a material’s surface.
Applications of laser carving machines span multiple sectors:
1. Manufacturing: They are widely used for engraving logos, serial numbers, and intricate designs on products like metal parts and electronic components.
2. Arts and Crafts: Artists and crafters use laser engraving for creating detailed artwork on wood, glass, acrylic, and leather, enabling complex designs that are difficult to achieve with traditional methods.
3. Signage: Laser carving machines are popular in the creation of signs and plaques, allowing for precise text and graphics on various materials, enhancing branding and visibility.
4. Jewelry Making: Jewelers utilize lasers for engraving intricate patterns or texts on metal or gemstones, providing personalization options for consumers.
5. Architecture and Interior Design: Designers employ laser carving for decorative panels and custom furnishings, adding unique elements to interiors.
6. Education: Schools and maker spaces use laser engraving machines for educational projects, helping students learn about design, technology, and manufacturing processes.
The benefits of laser carving include high accuracy, versatility, minimal material wastage, and the ability to automate processes, making them efficient tools for both small-scale and large-scale production. As technology advances, the applications of laser carving will likely expand, enhancing creative possibilities across industries.
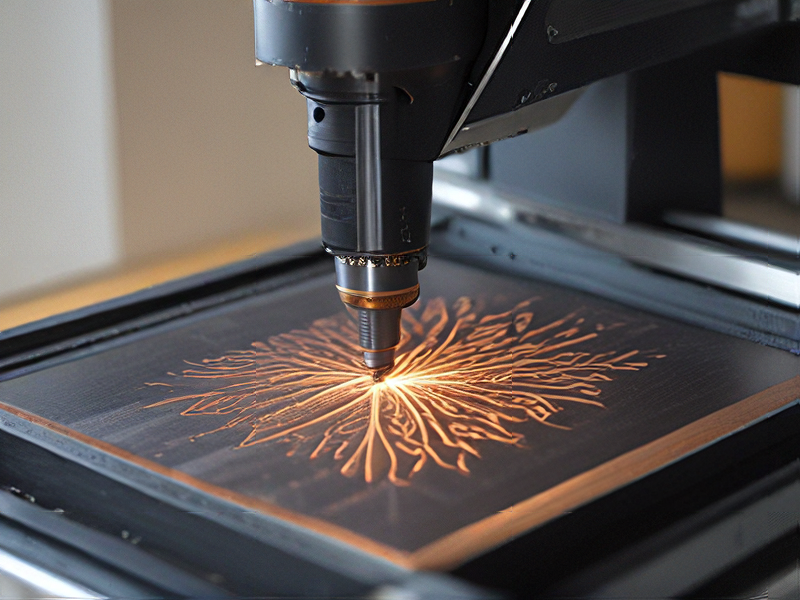
Quality Testing Methods for laser carving machine and how to control quality
Quality testing for laser carving machines is essential to ensure precision, reliability, and performance. Here are key methods and control measures:
1. Calibration: Regular calibration of the laser beam is crucial. Use certified measurement tools to check the focus, power output, and alignment of the beam. This ensures consistency in carving depth and accuracy.
2. Material Testing: Different materials respond differently to laser carving. Conduct tests on various substrates (wood, acrylic, et al.) to establish optimal settings (speed, power, frequency). Record results for future reference.
3. Dimensional Accuracy: Employ digital calipers or laser measuring tools to verify the dimensions of carved components. Compare the results with the design specifications to ensure compliance.
4. Visual Inspection: Conduct visual inspections post-carving for imperfections, such as incomplete cuts or burn marks. This can help identify issues with machine settings or material quality.
5. Functionality Testing: If the carved product is intended for specific applications, conduct functionality tests to ensure it meets required operational standards.
6. User Feedback: Implement a feedback mechanism from users for continuous improvement. Collect data on product performance and any defects reported.
7. Statistical Process Control (SPC): Utilize SPC techniques to monitor production processes. Regular data analysis helps identify trends and areas needing adjustment, ensuring long-term quality control.
8. Maintenance Routine: Establish a scheduled maintenance program for the laser machine. Regular cleaning of lenses, checking optics, and mechanical components prevent deterioration in quality.
By implementing these methods, manufacturers can maintain high-quality standards, reduce error rates, and enhance customer satisfaction in laser carving outputs.
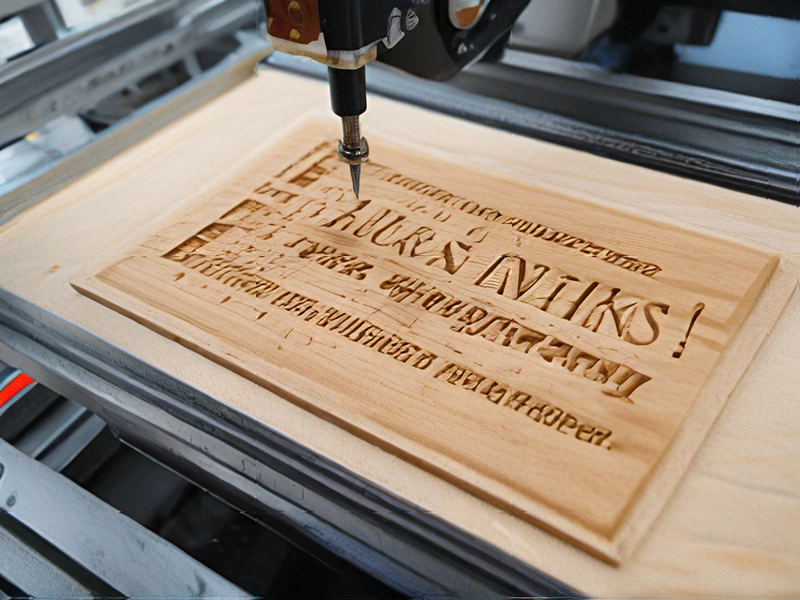
Tips for Procurement and Considerations when Purchasing from laser carving machine
When purchasing a laser carving machine, it’s crucial to evaluate several key factors to ensure an optimal purchase. Here are some tips and considerations:
1. Purpose and Material Compatibility: Identify what materials you plan to carve (wood, acrylic, leather, metal, etc.) and ensure the machine can handle them. Different machines have varied power ratings and capabilities.
2. Power and Speed: Higher wattage machines generally offer faster engraving and cutting. Consider your production volume and the required detail level when evaluating power ratings.
3. Size and Work Area: Assess the size of the work area based on the projects you intend to undertake. A larger machine allows for bigger projects, but will require more workspace.
4. Software Compatibility: Ensure the machine comes with or supports user-friendly software for designing and operating the machine. Check for compatibility with popular design software like Adobe Illustrator or CorelDRAW.
5. Ease of Use: Look for features that facilitate ease of operation, such as intuitive controls, setup processes, and maintenance requirements. User-friendly machines save time and enhance productivity.
6. Customer Support and Warranty: Check the manufacturer’s reputation for customer service. A solid warranty and responsive support are crucial for troubleshooting or repairs.
7. Budget: Balance features with budget constraints. Consider long-term investment and potential returns, keeping in mind that cheaper options may lack necessary capabilities or durability.
8. Reviews and Recommendations: Research reviews and seek recommendations from other users or experts in the field. Their experiences can provide invaluable insights.
By carefully considering these aspects, you can make a more informed decision that aligns with your needs and enhances your crafting projects.
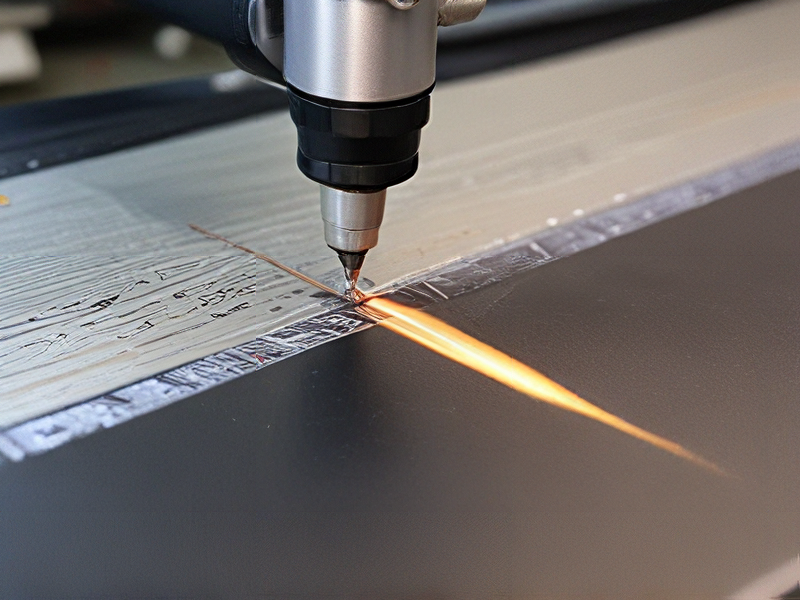
FAQs on Sourcing and Manufacturing from laser carving machine in China
FAQs on Sourcing and Manufacturing Laser Carving Machines in China
1. Why choose China for laser carving machines?
China is a global leader in manufacturing, offering competitive prices, advanced technology, and a huge selection of suppliers. The extensive experience in production ensures high-quality machinery tailored to various needs.
2. How to find a reliable supplier?
Start by attending trade shows, such as the Canton Fair, or use online platforms like Alibaba and Made-in-China. Check supplier credentials, reviews, and production capabilities. Request samples to evaluate quality.
3. What certifications should I look for?
Ensure the machines have relevant certifications such as CE, ISO 9001, and FDA. These certifications signify compliance with international quality and safety standards.
4. What is the typical lead time for manufacturing?
Lead times vary, but generally, it ranges from 4 to 12 weeks, depending on the complexity of the machine and the supplier’s workload. Always confirm estimated delivery dates before placing an order.
5. What should I know about customs and shipping?
Import duties and regulations differ by country. Familiarize yourself with your country’s import policies and collaborate with a forwarder for efficient shipping. Consider air freight for quicker delivery or sea freight for cost-effectiveness.
6. What about after-sales support?
Discuss warranty terms and after-sales service with your supplier upfront. It’s essential to understand technical support, part availability, and maintenance service options.
7. Can I customize machines for specific needs?
Yes, many Chinese manufacturers offer customization options to accommodate specific requirements, such as size, power, and additional features.
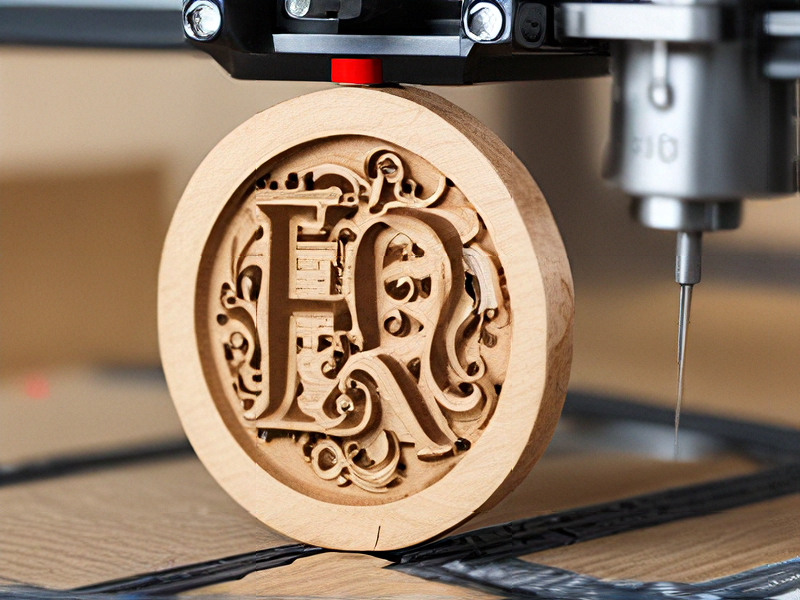