Technology and Applications of laser cleaning machine
Laser cleaning machines use laser beams to remove contaminants, rust, coatings, and other impurities from surfaces. This technology leverages high-energy laser pulses to ablate the unwanted material without damaging the underlying substrate.
Technology
1. Laser Source: Fiber and solid-state lasers are commonly used. They emit high-frequency pulses that precisely target contaminants.
2. Optics and Scanning System: Advanced optics focus the laser beam, and scanning systems direct it across the surface.
3. Control System: Integrated software controls the laser parameters, ensuring efficient and safe operation.
Applications
1. Industrial Cleaning: Removal of rust, paint, and oxides from metals, especially in automotive, aerospace, and manufacturing sectors.
2. Cultural Heritage: Restoration of artworks and historical artifacts by delicately removing layers of dirt and corrosion.
3. Electronics: Cleaning of printed circuit boards (PCBs) and semiconductor wafers without using chemicals.
4. Precision Cleaning: Cleaning delicate components in the medical device industry and precision instruments.
Advantages
1. Non-contact Process: Prevents wear and tear on the material.
2. Eco-friendly: Eliminates the need for chemicals and solvents.
3. Precision: Allows for selective cleaning without damaging the substrate.
4. Efficiency: Fast processing with minimal waste generation.
Challenges
1. Initial Cost: High investment cost compared to traditional methods.
2. Energy Consumption: Requires significant power for high-intensity applications.
3. Material Compatibility: Not suitable for all materials and surfaces.
Laser cleaning machines offer a cutting-edge solution for various industries, combining efficiency, precision, and environmental benefits. Their application continues to expand as the technology advances.
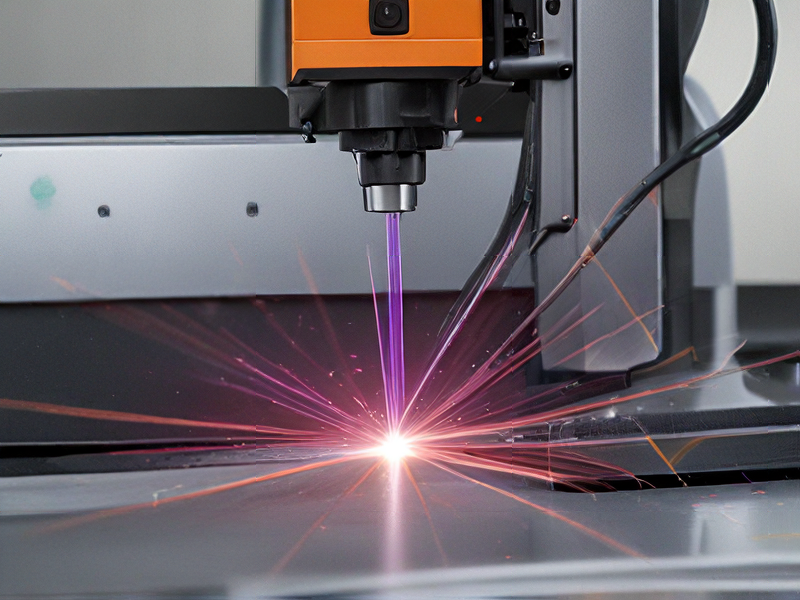
Quality Testing Methods for laser cleaning machine and how to control quality
Quality testing for laser cleaning machines involves several methods to ensure performance, safety, and reliability. Here are the key methods and quality control measures:
Testing Methods
1. Visual Inspection:
– Surface Cleanliness: Inspect surfaces cleaned by the laser for residues or contaminants.
– Laser Path and Components: Check for wear, alignment, and cleanliness.
2. Performance Testing:
– Power Measurement: Verify laser output power using a power meter.
– Beam Quality: Assess the beam profile and spot size with beam profilers.
– Speed and Precision: Test the accuracy and speed of the cleaning process.
3. Material Compatibility:
– Substrate Testing: Conduct trials on different materials to ensure the laser does not damage the substrate.
– Adhesion Tests: Check for changes in adhesion properties post-cleaning.
4. Safety Testing:
– Interlock Systems: Ensure safety interlocks are functioning to prevent accidental exposure.
– Emission Testing: Measure emissions to ensure they are within safe limits.
5. Environmental Testing:
– Temperature and Humidity: Test the machine under various environmental conditions to ensure consistent performance.
Quality Control Measures
1. Standard Operating Procedures (SOPs):
– Develop detailed SOPs for operation, maintenance, and calibration.
2. Regular Calibration:
– Schedule routine calibration of laser power and alignment using certified equipment.
3. Training and Certification:
– Ensure operators are well-trained and certified to handle the machine and perform quality checks.
4. Documentation and Reporting:
– Maintain detailed logs of all tests, inspections, and maintenance activities.
5. Feedback Loop:
– Implement a system for collecting and analyzing user feedback to continuously improve the machine and processes.
By incorporating these testing methods and quality control measures, manufacturers can ensure that laser cleaning machines perform reliably and safely, providing effective cleaning without damaging the underlying materials.
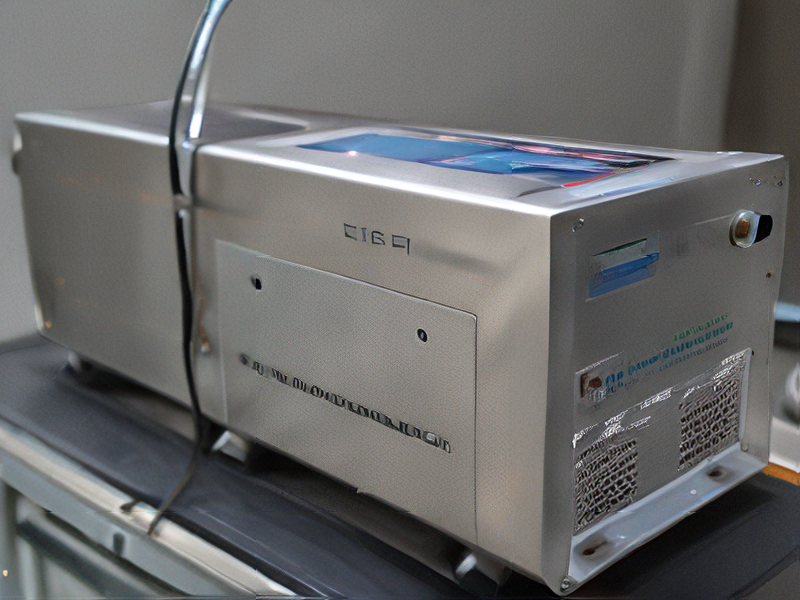
Tips for Procurement and Considerations when Purchasing from laser cleaning machine
When procuring a laser cleaning machine, careful consideration of various factors ensures optimal performance and value for investment. Here are key tips and considerations:
1. Assess Cleaning Needs:
– Identify the types of materials and contaminants to be cleaned. Different laser cleaning machines are optimized for various surfaces and substances.
2. Power and Frequency:
– Evaluate the laser power and frequency. Higher power lasers clean more efficiently but may damage delicate surfaces. Frequency impacts the precision and speed of cleaning.
3. Portability and Size:
– Determine if a portable machine is necessary. Portable machines are ideal for on-site jobs, while stationary units are better for fixed locations.
4. Control and Automation:
– Look for machines with advanced control systems and automation capabilities. This improves precision, repeatability, and ease of use.
5. Safety Features:
– Ensure the machine has robust safety features, including proper shielding, emergency stops, and interlocks to protect operators from laser exposure.
6. Maintenance and Support:
– Consider the maintenance requirements and availability of technical support. Opt for machines with low maintenance needs and reliable support from the manufacturer.
7. Training and Usability:
– Check if the manufacturer provides training for operators. User-friendly interfaces and comprehensive training reduce the risk of errors and enhance efficiency.
8. Cost and ROI:
– Analyze the cost relative to the benefits. A higher initial investment may be justified by lower operating costs, increased efficiency, and better cleaning results.
9. Regulatory Compliance:
– Ensure the machine complies with local regulations and industry standards for laser safety and emissions.
10. Vendor Reputation:
– Research the vendor’s reputation, read reviews, and consider their experience and reliability in the market.
By thoroughly evaluating these aspects, you can make an informed decision, ensuring the selected laser cleaning machine meets your operational needs and provides long-term value.
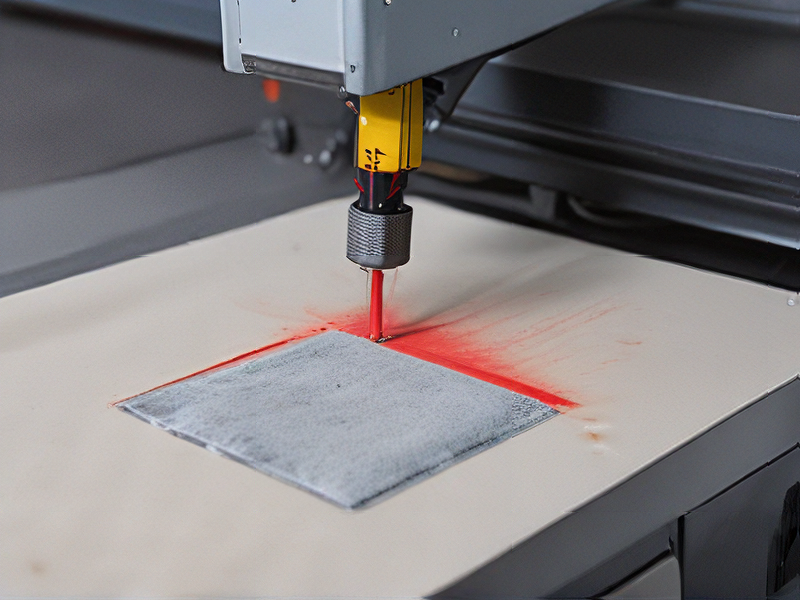
FAQs on Sourcing and Manufacturing from laser cleaning machine in China
FAQs on Sourcing and Manufacturing Laser Cleaning Machines in China
1. Why source laser cleaning machines from China?
China offers competitive pricing, advanced technology, and a wide range of manufacturers, making it a cost-effective and efficient option for sourcing laser cleaning machines.
2. How do I find reliable manufacturers?
Use platforms like Alibaba, Global Sources, and Made-in-China. Verify suppliers through customer reviews, ratings, and third-party verification services. Visiting trade shows and factory audits also help.
3. What should I consider when choosing a supplier?
Evaluate their production capacity, quality control processes, certifications (ISO, CE), and after-sales service. Request samples to assess product quality.
4. Are there any regulatory requirements?
Ensure the machines meet international safety and performance standards such as ISO, CE, and RoHS. Check your country’s import regulations and compliance requirements.
5. What is the typical lead time for production?
Lead times vary but generally range from 20 to 60 days, depending on the order size and manufacturer’s capacity. Confirm with the supplier.
6. How do I handle quality control?
Implement strict quality control measures including pre-shipment inspections, third-party audits, and testing samples. Use services from companies like SGS or Bureau Veritas.
7. What are the payment terms?
Common payment terms include T/T (bank transfer), L/C (Letter of Credit), and PayPal. Initial orders often require a deposit (30%-50%) with the balance paid before shipment.
8. How is shipping handled?
Manufacturers typically handle shipping through freight forwarders. Options include sea freight (cheaper, slower) and air freight (more expensive, faster). Ensure your logistics partner handles customs clearance.
9. Can I get customized machines?
Yes, many manufacturers offer customization based on your specifications. Discuss your requirements in detail and ensure clear communication throughout the process.
10. What after-sales support is available?
After-sales support varies; check for warranty terms, availability of spare parts, and technical support. Reliable suppliers offer comprehensive after-sales services to ensure smooth operation.
Sourcing from China can be highly beneficial with thorough research and careful selection of suppliers.
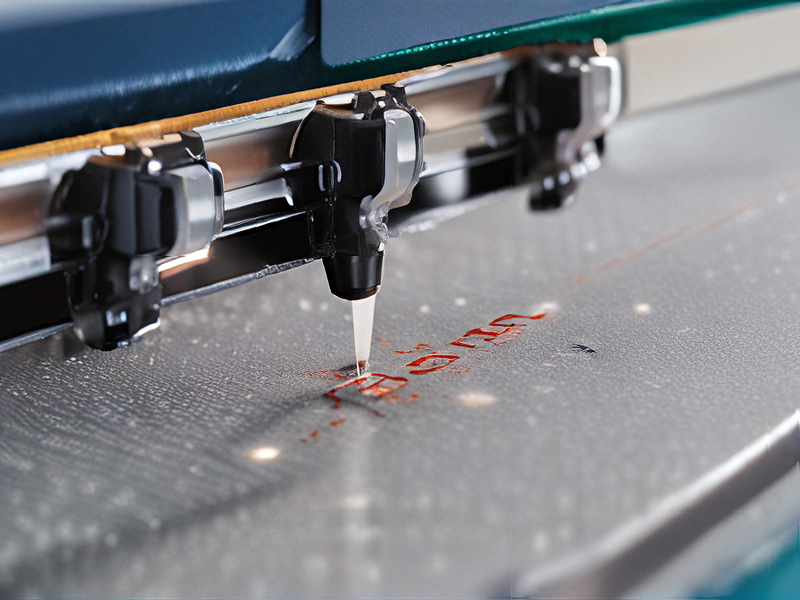