Technology and Applications of laser cutting machine
Laser cutting machines are advanced tools that utilize focused laser beams to cut or engrave materials with high precision and minimal waste. These machines operate by directing a high-powered laser beam onto a material’s surface, which melts, burns, or vaporizes the material, resulting in a clean cut.
Technology:
The core technology behind laser cutting involves various types of lasers such as CO2, fiber, and Nd:YAG lasers. CO2 lasers are commonly used for cutting non-metallic materials like wood, plastics, and fabrics, while fiber lasers are more efficient for metals, including stainless steel and aluminum. The laser’s intensity, speed, and focus can be adjusted for different materials and thicknesses, allowing for versatility in applications.
Applications:
Laser cutting is widely used across multiple industries:
1. Manufacturing: For precision cutting of complex shapes in metal parts, improving efficiency and reducing waste.
2. Automotive: Producing intricate components with tight tolerances, essential for vehicle safety and performance.
3. Electronics: Creating precise cuts in circuit boards and enclosures, facilitating miniaturization and improved design.
4. Aerospace: Allowing for lightweight and strong components to be fabricated from advanced materials.
5. Fashion and Textiles: Used for creating custom designs in fabrics, leather, and other materials, providing unique patterns and textures.
6. Signage and Architecture: Enabling detailed engraving and cutting of signage and decorative features.
The combination of speed, accuracy, and versatility makes laser cutting an invaluable technology in modern manufacturing and design processes, driving innovation across various fields.
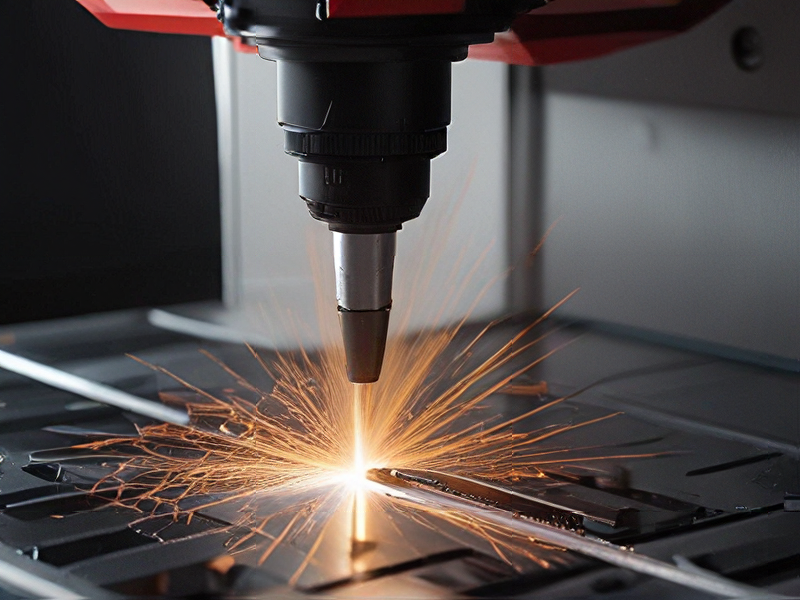
Quality Testing Methods for laser cutting machine and how to control quality
Quality testing for laser cutting machines is crucial to ensure precision, efficiency, and durability. Here are key methods and strategies for quality control:
1. Visual Inspection: Conduct thorough visual checks of cut edges for signs of burn marks, discoloration, or roughness. Consistent surface finish and clean cuts indicate proper operation.
2. Dimensional Accuracy Testing: Utilize calipers and gauges to measure the dimensions of cut parts against specifications. This helps identify any deviations in size or shape caused by machine calibration issues.
3. Material Thickness Tolerance: Test the machine’s ability to cut different material thicknesses. Regularly measure the kerf width (the width of the material removed by the cut) to ensure it aligns with recommended tolerances.
4. Dross Assessment: Check for dross (excess material left on the cut edges). Excessive dross can indicate improper settings like speed or power levels.
5. Cut Quality Tests: Perform cut quality tests by evaluating the mechanical properties of the cut edges. This may include checking for burrs or ensuring no material warps during cutting.
6. Calibration and Maintenance: Regularly calibrate the laser cutter according to the manufacturer’s specifications. Implement a preventive maintenance schedule to minimize downtime and ensure optimal performance.
7. Feedback Loop: Establish a feedback mechanism from operators and quality inspectors to continuously improve the cutting process based on observed deficiencies.
8. Documentation and Standards Compliance: Maintain detailed records of all quality tests and ensure compliance with industry standards, facilitating traceability and accountability.
By implementing these quality testing methods, manufacturers can control and enhance the performance of laser cutting machines, leading to improved product quality and operational efficiency.
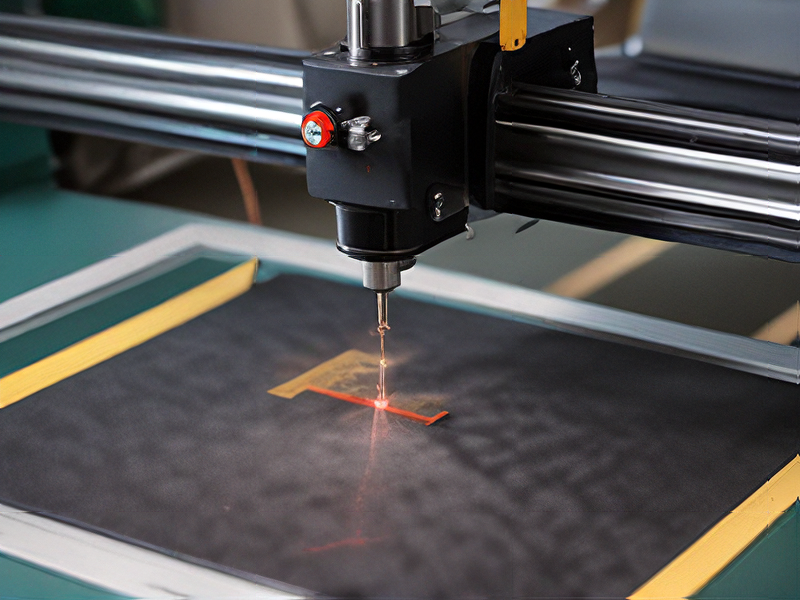
Tips for Procurement and Considerations when Purchasing from laser cutting machine
When purchasing a laser cutting machine, consider the following tips to ensure you make a well-informed decision:
1. Define Requirements: Clearly outline your cutting needs, including materials, thickness, and production volume. This will help narrow down the machine types and specifications.
2. Types of Lasers: Understand the different types of lasers (CO2, fiber, and YAG) and choose one based on the materials you plan to cut. CO2 lasers are best for non-metal materials, while fiber lasers excel with metals.
3. Power and Speed: Higher wattage increases cutting speed and material thickness capabilities. Assess your production needs to determine the appropriate power level.
4. Software Compatibility: Ensure the machine is compatible with your existing CAD/CAM software for seamless integration into your workflow.
5. Space Requirements: Evaluate your available workspace, as some machines can be large and may require additional ventilation or safety measures.
6. Training and Support: Consider the manufacturer’s training offerings and technical support. A strong support system can significantly ease the learning curve.
7. Maintenance and Parts Availability: Investigate maintenance requirements and the availability of replacement parts to avoid long downtimes.
8. Budget: Set a realistic budget, considering not only the machine cost but also operating expenses (like power consumption, maintenance, and consumables).
9. Warranty and Service Agreement: Review warranty options and service agreements to ensure protection against defects and future issues.
10. Reputation and Reviews: Research manufacturer reputation and read customer reviews. Engaging with user forums can provide insights into long-term performance and reliability.
By carefully evaluating these considerations, you can confidently select a laser cutting machine that meets your production needs and budget.
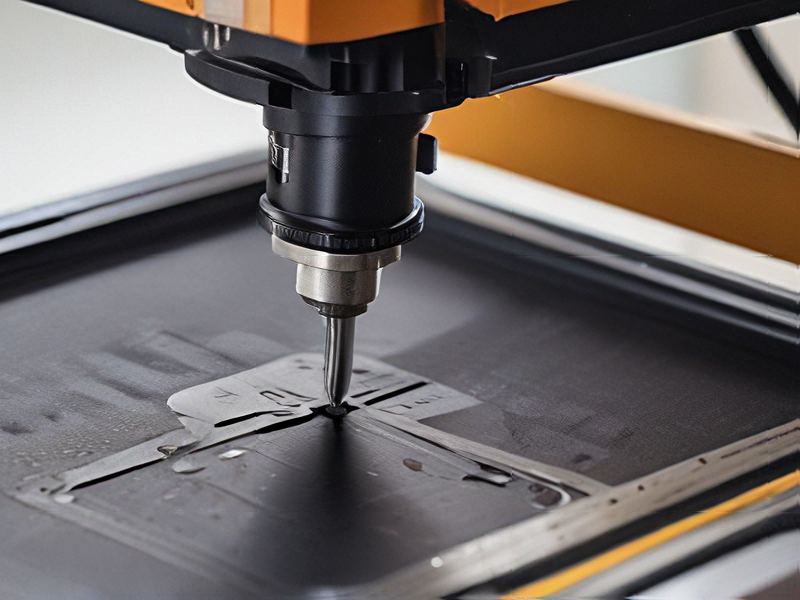
FAQs on Sourcing and Manufacturing from laser cutting machine in China
FAQs on Sourcing and Manufacturing Laser Cutting Machines in China
1. Why source laser cutting machines from China?
China is a leading hub for manufacturing thanks to its advanced technology, competitive prices, and vast production capacity. Many Chinese manufacturers offer high-quality laser cutting machines tailored to various industries.
2. What should I consider when selecting a manufacturer?
Evaluate the manufacturer’s experience, certifications (such as ISO), customer reviews, and production capabilities. It’s also beneficial to request samples or visit their facility if possible.
3. How do I ensure quality control?
Implement quality control measures such as pre-production samples, regular inspections during production, and final quality checks before shipment. Establish clear quality criteria and maintain communication with the manufacturer.
4. What are the typical lead times?
Lead times can vary widely based on the complexity of the machine and the manufacturer. On average, production can take from a few weeks to several months, depending on the order size and customization requirements.
5. Are there additional costs involved?
Yes, consider shipping, customs duties, taxes, and potential import tariffs. Additionally, factor in costs for quality inspections and logistics.
6. What are the payment terms?
Payment terms typically include a deposit (often 30-50%) upfront, with the balance due before shipment. Discuss terms clearly to avoid misunderstandings later.
7. How do I handle post-purchase support?
Check if the manufacturer offers warranties, technical support, and after-sales services. It’s crucial to understand their policies on parts replacement and machine maintenance.
For a successful sourcing experience, conduct thorough research, maintain clear communication, and build a relationship with your manufacturer.
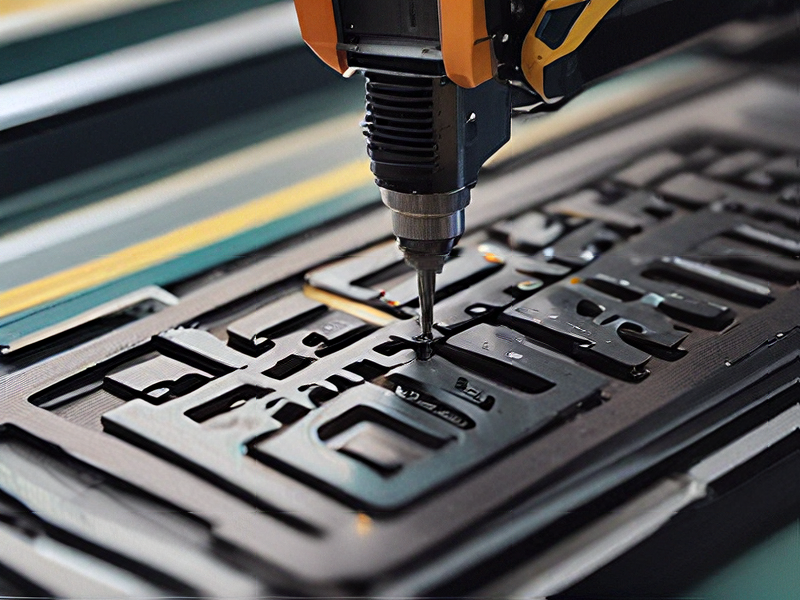