Technology and Applications of laser cutting machine for tubes
Laser cutting machines for tubes employ high-powered lasers to precisely cut and shape metal tubes. This technology utilizes a focused laser beam to melt, burn, or vaporize material, leaving a clean, precise edge. The main components include the laser source, cutting head, motion system, and control system.
Technology:
1. Fiber Lasers: They are commonly used due to their high efficiency and ability to cut various materials including steel, aluminum, and copper. Fiber lasers offer excellent beam quality and cutting speed.
2. CO2 Lasers: These are suitable for cutting non-metal materials and thicker metals. They provide high cutting power and quality.
3. Hybrid Lasers: Combining fiber and CO2 lasers, hybrid systems leverage the strengths of both technologies for versatile applications.
Applications:
1. Automotive Industry: Laser tube cutting is used for producing exhaust systems, structural components, and intricate parts with high precision and repeatability.
2. Furniture Manufacturing: Manufacturers use laser cutting to create complex designs and joints in metal frames, enhancing aesthetics and structural integrity.
3. Aerospace: The technology is crucial for manufacturing lightweight, durable components, such as seat frames and structural supports, where precision is paramount.
4. Construction and Architecture: Laser cutting is employed for creating metal frameworks, decorative elements, and structural components with intricate designs.
5. Medical Devices: Precision and cleanliness are critical for producing surgical instruments and medical implants, making laser cutting an ideal method.
Advantages:
– Precision: High accuracy in cutting complex shapes and designs.
– Speed: Faster than traditional cutting methods.
– Versatility: Suitable for a wide range of materials and thicknesses.
– Quality: Produces clean cuts with minimal material wastage.
– Automation: Integration with CNC systems allows for automated and efficient production.
In summary, laser cutting machines for tubes are a vital technology in modern manufacturing, offering unparalleled precision, speed, and versatility across various industries.
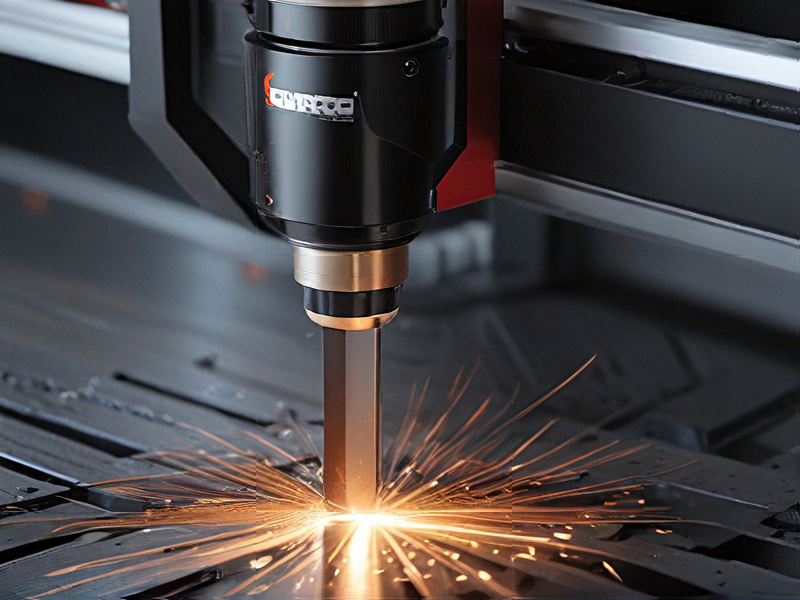
Quality Testing Methods for laser cutting machine for tubes and how to control quality
Quality testing for laser cutting machines for tubes involves several methods to ensure precision, efficiency, and consistency. Here are key methods and control measures:
1. Dimensional Accuracy Testing:
– Method: Use calipers and micrometers to measure the cut dimensions and compare them to design specifications.
– Control: Regular calibration of measurement tools and the laser machine ensures accuracy.
2. Cut Surface Quality:
– Method: Inspect the cut edges for burrs, roughness, and heat-affected zones using visual and tactile assessments.
– Control: Adjust laser power, speed, and focus settings to minimize imperfections.
3. Material Integrity:
– Method: Perform non-destructive testing (NDT) like ultrasonic or dye penetrant testing to check for cracks or weaknesses.
– Control: Maintain optimal machine parameters and cooling systems to reduce thermal stress.
4. Consistency and Repeatability:
– Method: Conduct repeated cuts on sample tubes and measure variance in dimensions and quality.
– Control: Implement statistical process control (SPC) to monitor and control process variations.
5. Laser Beam Quality:
– Method: Use beam profilers to check the laser beam’s focus, intensity distribution, and alignment.
– Control: Regular maintenance and alignment of the laser optics.
6. Heat Affected Zone (HAZ) Analysis:
– Method: Examine the microstructure of the cut edges using metallographic analysis to assess the HAZ.
– Control: Optimize laser parameters to minimize HAZ, preserving material properties.
7. Burr and Dross Analysis:
– Method: Evaluate the presence and size of burrs or dross on the cut edges.
– Control: Adjust cutting speed and gas pressure to reduce burr formation.
By integrating these testing methods and control measures, manufacturers can ensure high-quality laser cutting of tubes, leading to improved product performance and customer satisfaction.
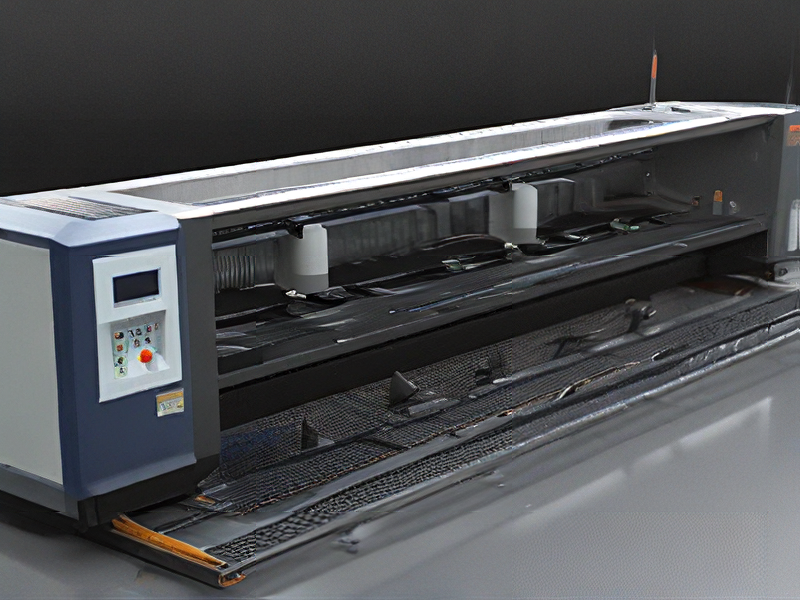
Tips for Procurement and Considerations when Purchasing from laser cutting machine for tubes
When procuring a laser cutting machine for tubes, consider the following tips and factors:
Technical Specifications
1. Material Compatibility: Ensure the machine can handle the materials you work with, such as steel, aluminum, or copper.
2. Cutting Speed and Thickness: Check the maximum thickness and speed it can cut, aligning with your production needs.
3. Precision and Accuracy: Look for machines with high precision to ensure quality cuts, especially for intricate designs.
Machine Features
4. Automation Capabilities: Opt for machines with automated loading and unloading systems to improve efficiency and reduce labor costs.
5. Software Integration: Ensure the machine’s software is compatible with your existing design software for seamless operations.
6. Tube Handling: Consider machines with advanced tube handling features, such as automatic centering and clamping, for better accuracy.
Cost Considerations
7. Initial Investment vs. Long-term Benefits: Evaluate the initial cost against the long-term benefits, such as increased production speed and reduced waste.
8. Maintenance Costs: Factor in the cost and frequency of maintenance. Machines with low maintenance requirements can save money over time.
9. Energy Efficiency: Energy-efficient machines can reduce operational costs.
Vendor and Support
10. Reputation and Reliability: Choose reputable vendors known for reliable machines and good after-sales support.
11. Warranty and Service: Check the warranty period and availability of technical support and spare parts.
Operational Impact
12. Training Requirements: Consider the training needed for your staff to operate the new machine efficiently.
13. Space and Infrastructure: Ensure you have adequate space and infrastructure, such as power supply and ventilation, for the machine.
Compliance and Safety
14. Safety Features: Look for machines with robust safety features to protect operators and comply with safety regulations.
15. Regulatory Compliance: Ensure the machine complies with local and international standards and regulations.
By carefully evaluating these aspects, you can make an informed decision and select a laser cutting machine that best suits your production needs and budget.
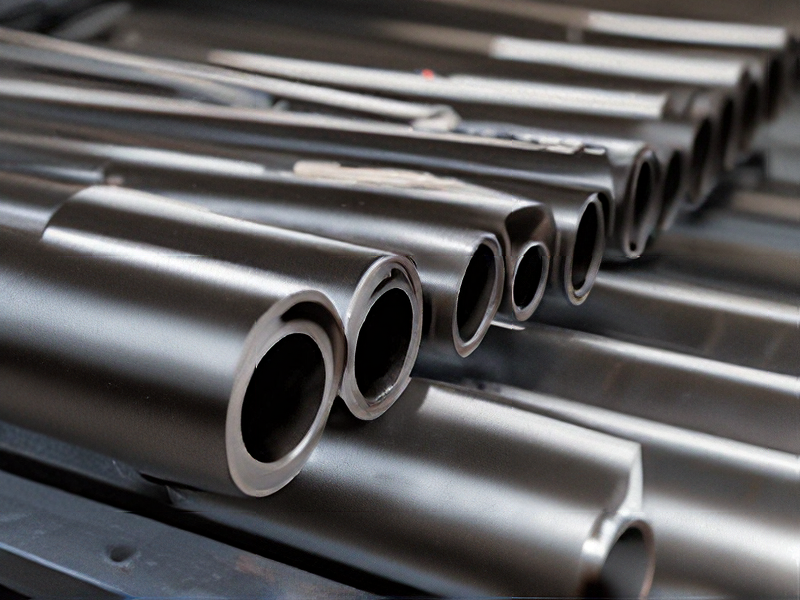
FAQs on Sourcing and Manufacturing from laser cutting machine for tubes in China
FAQs on Sourcing and Manufacturing Laser Cutting Machines for Tubes in China
#### 1. Why source laser cutting machines from China?
China is a leading manufacturer of laser cutting machines, offering competitive prices, advanced technology, and a wide range of options. Chinese manufacturers often provide customization and robust after-sales support.
#### 2. How to find reliable suppliers?
Use platforms like Alibaba, Made-in-China, and Global Sources. Check supplier certifications, read customer reviews, and consider visiting the factory. Look for ISO 9001 certification and CE marking to ensure quality standards.
#### 3. What are the key features to look for?
Consider the machine’s power (measured in watts), cutting speed, precision, tube diameter range, software compatibility, and ease of use. Also, evaluate the machine’s maintenance requirements and the availability of spare parts.
#### 4. How to verify the quality of the machine?
Request product samples and performance videos. Check for certifications like ISO, CE, and FDA. Conduct a factory audit if possible, or hire a third-party inspection service to ensure the machine meets your standards.
#### 5. What are the payment terms?
Common terms include a 30% deposit upfront and the balance before shipment. Use secure payment methods like letters of credit or escrow services to mitigate risk.
#### 6. What about shipping and logistics?
Chinese manufacturers typically handle FOB (Free On Board) shipping, meaning they cover costs up to the port of shipment. You will need to arrange for a freight forwarder to handle transportation to your destination.
#### 7. How to handle after-sales service and support?
Ensure the supplier offers a warranty, typically one year for the machine and six months for consumables. Check if they provide remote technical support, on-site training, and spare parts availability.
#### 8. What are the common challenges?
Language barriers, time zone differences, and quality control are common challenges. Mitigate these by maintaining clear communication, using a bilingual liaison, and setting clear quality expectations from the outset.
By following these guidelines, you can effectively source and manufacture laser cutting machines for tubes from China, ensuring quality and reliability.
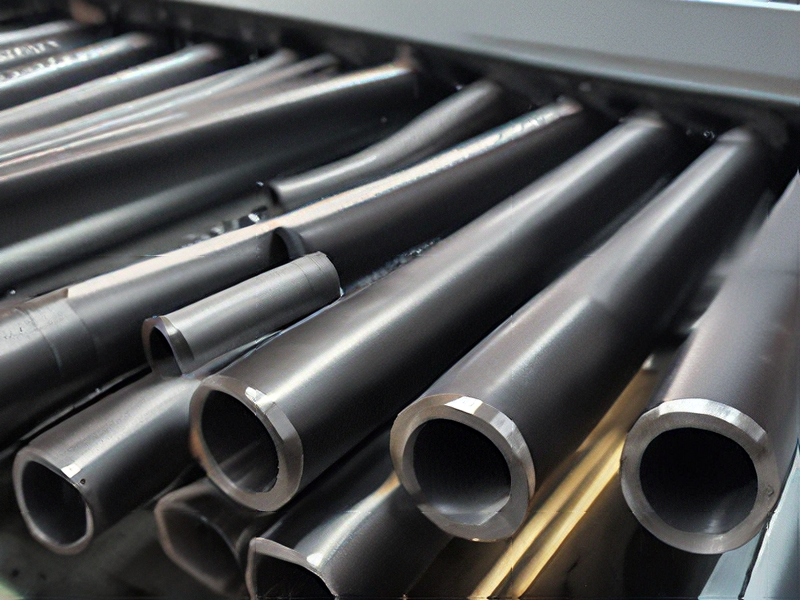