Technology and Applications of laser cutting machine wood
Laser cutting machines are revolutionizing woodworking with their precision and versatility. These machines use a high-powered laser beam to cut through wood, offering several advantages over traditional cutting methods.
Precision and Intricacy: Laser cutting machines can achieve incredibly fine cuts and intricate designs that are difficult to replicate with other tools. This precision is ideal for creating detailed patterns, engravings, or custom shapes in wood.
Versatility: They can cut through a variety of wood types and thicknesses, from thin veneers to thick hardwoods, with consistent accuracy. This versatility makes them suitable for a wide range of woodworking applications, including furniture manufacturing, cabinetry, signage, and crafts.
Efficiency and Speed: Laser cutting is faster than many traditional woodworking methods, as it can cut through material swiftly and often in a single pass. This efficiency reduces production times and increases output capacity.
Minimal Waste: Laser cutting minimizes material waste compared to traditional sawing or routing techniques. The precision of the laser beam allows for nesting parts closely together, optimizing the use of wood and reducing scrap.
Customization and Personalization: These machines enable high levels of customization, allowing woodworkers to create unique, personalized pieces easily. They can etch logos, names, or intricate designs directly onto wood surfaces, adding value and uniqueness to finished products.
Complex Joinery and Assembly: Laser cutting machines can also create precise joints and interlocking parts, facilitating complex assembly processes without the need for additional fasteners or adhesives.
Overall, laser cutting machines have transformed woodworking by offering unmatched precision, versatility, and efficiency. They empower woodworkers to explore new design possibilities and streamline production processes, making them invaluable tools in modern woodworking workshops.
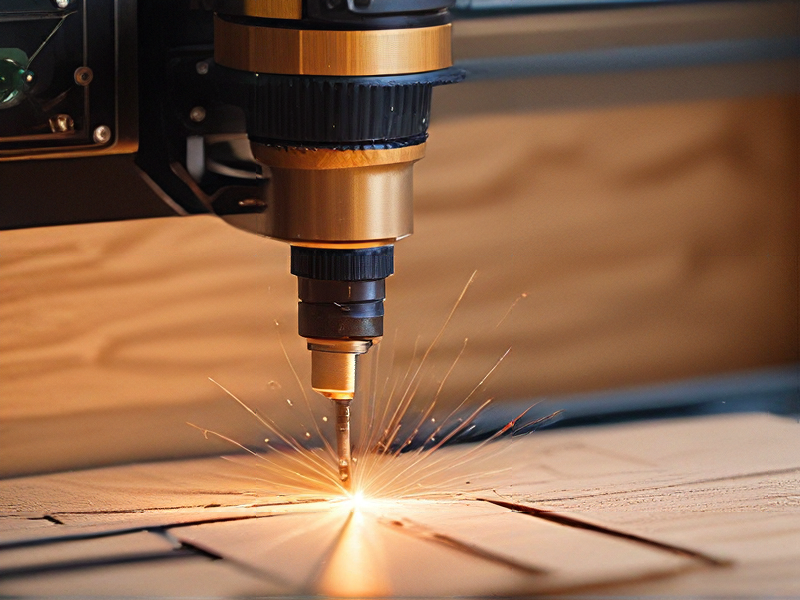
Quality Testing Methods for laser cutting machine wood and how to control quality
Quality testing methods for laser cutting machines used on wood typically include:
1. Dimensional Accuracy: Measure cut pieces against design specifications using calipers or coordinate measuring machines (CMM).
2. Edge Quality: Inspect for smooth edges without charring or burns, using visual inspection or magnification.
3. Material Integrity: Check for signs of burning or scorching on the wood surface.
4. Accuracy of Cuts: Verify the precision of cuts against CAD drawings or templates, ensuring no deviations.
5. Testing at Various Speeds and Powers: Validate optimal settings by testing different parameters for consistency and quality.
To control quality:
1. Regular Maintenance: Ensure the laser cutting machine is well-maintained to prevent issues like misalignment or power fluctuations.
2. Calibration Checks: Regularly calibrate the machine to maintain accuracy and performance.
3. Operator Training: Train operators on proper machine operation, maintenance, and troubleshooting.
4. Quality Control Procedures: Implement robust QC checks at each stage of production to detect and rectify issues promptly.
5. Feedback Loop: Establish a feedback mechanism where operators can report any quality concerns for immediate action.
By following these methods and controls, manufacturers can ensure consistent quality in laser-cut wood products.
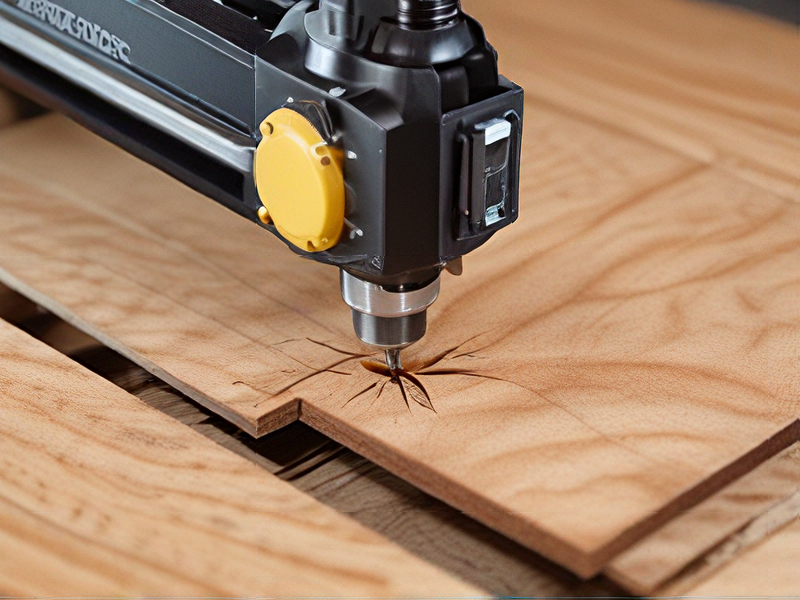
Tips for Procurement and Considerations when Purchasing from laser cutting machine wood
When procuring a laser cutting machine for wood, several key considerations can ensure a successful purchase. Here are some essential tips:
1. Define Your Requirements: Identify the types of wood and the thickness you will be cutting. Determine the precision and speed needed for your projects.
2. Machine Power: Choose a laser with appropriate wattage. Higher wattage machines cut thicker materials faster but can be more expensive. Common options range from 40W to 150W for woodworking.
3. Cutting Area: Ensure the machine’s cutting bed size matches the dimensions of your typical projects. Larger cutting areas allow for more flexibility but also require more space.
4. Software Compatibility: Ensure the machine is compatible with design software you use, such as AutoCAD, CorelDRAW, or Adobe Illustrator. User-friendly software can significantly streamline your workflow.
5. Ventilation and Safety: Laser cutting wood produces fumes and smoke. Look for machines with efficient exhaust systems and filters. Safety features like emergency stop buttons and protective covers are also crucial.
6. Precision and Quality: Assess the machine’s precision and the quality of its output. Look for features like high-resolution engraving and smooth cutting edges.
7. Support and Training: Choose a supplier that offers comprehensive support and training. Proper setup and maintenance training can enhance the longevity and performance of your machine.
8. Budget: Balance your budget with the features and capabilities you need. While it’s tempting to opt for cheaper models, investing in a reliable, higher-quality machine can be more cost-effective in the long run.
9. Warranties and Service: Check the warranty and service agreements. A good warranty and responsive customer service can save time and costs if issues arise.
10. Reviews and References: Read reviews and ask for references from other businesses. First-hand experiences can provide valuable insights into the machine’s performance and reliability.
By considering these factors, you can select a laser cutting machine that best suits your woodworking needs, ensuring quality results and operational efficiency.
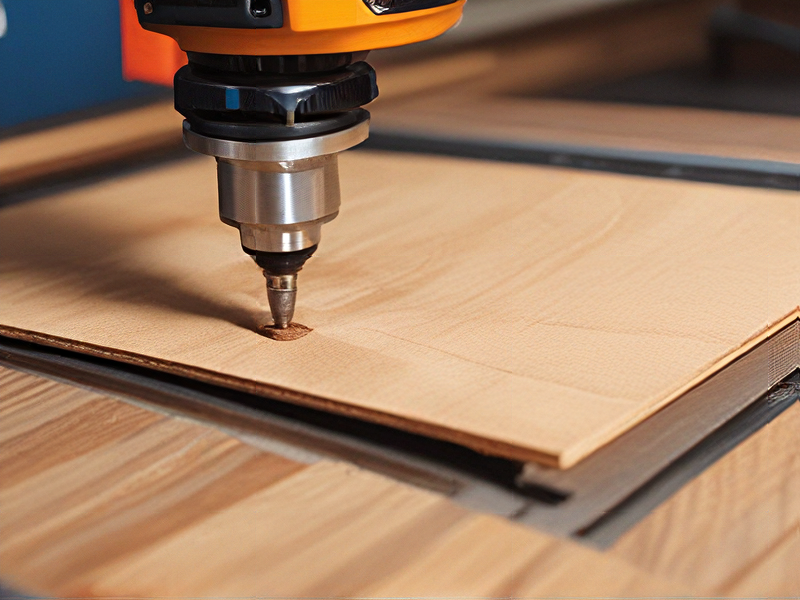
FAQs on Sourcing and Manufacturing from laser cutting machine wood in China
When sourcing and manufacturing laser-cut wood products from China, several frequently asked questions (FAQs) commonly arise:
1. What types of wood are suitable for laser cutting?
Different woods react differently to laser cutting. Popular choices include plywood, MDF (medium-density fiberboard), and various hardwoods like birch or oak.
2. What file formats are compatible with Chinese laser cutting machines?
Typically, DXF (Drawing Exchange Format) and AI (Adobe Illustrator) files are widely accepted. These formats maintain vector information crucial for precise cuts.
3. How can I ensure the quality of laser-cut wood products from Chinese suppliers?
Conduct thorough supplier vetting by requesting samples, checking certifications (like ISO 9001), and verifying client testimonials or reviews.
4. What are the typical lead times for laser-cut wood products from China?
Lead times vary based on complexity and order size but generally range from a few days to several weeks. Factors like shipping and customs clearance also affect total delivery times.
5. What are the cost considerations for laser cutting wood in China?
Costs depend on material type, design complexity, and batch size. Request detailed quotations including material costs, machine setup fees, and any additional handling charges.
6. How can I manage intellectual property concerns when outsourcing to China?
Ensure clear contracts with non-disclosure agreements (NDAs) and intellectual property (IP) protections. Working with reputable suppliers who respect IP rights is crucial.
By addressing these FAQs, businesses can navigate the sourcing and manufacturing process of laser-cut wood products in China more effectively, ensuring quality, efficiency, and compliance with their specific needs.
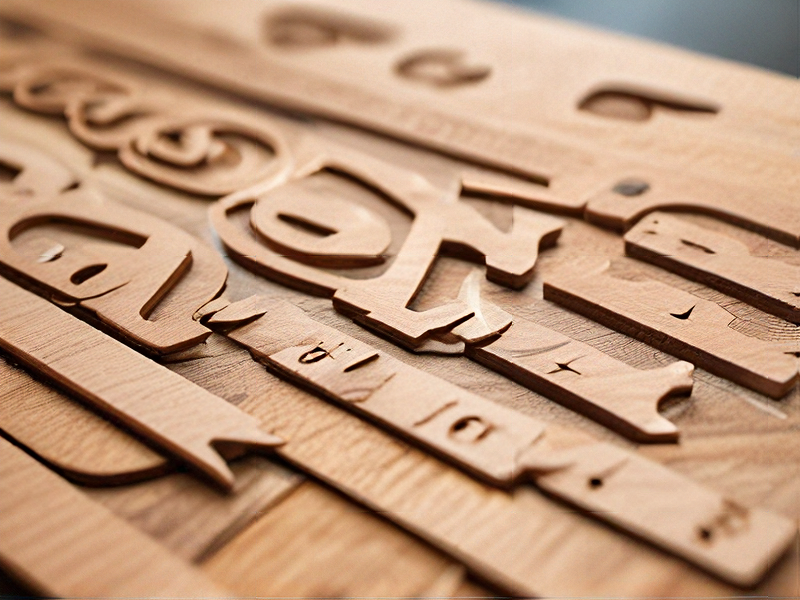