Technology and Applications of laser etched metal
Laser etching is a precise and versatile technology used to mark and modify metal surfaces.
Applications:
* Identification & Branding: Permanent marking of products, components, and assets for traceability and branding.
* Customization & Decoration: Creating intricate designs, logos, and personalized engravings on metal items like jewelry, trophies, and signage.
* Functional Modifications: Etching can alter the surface properties of metal, enhancing functionalities like conductivity, reflectivity, or wear resistance.
* Micro-Machining: Precise etching enables the creation of tiny features and structures in metal for applications in microelectronics, sensors, and biomedical devices.
How it Works:
A high-powered laser beam is focused onto the metal surface. The intense heat vaporizes the metal at the point of impact, creating a precisely defined design or pattern. Different laser wavelengths and pulse durations can be used to achieve varying etch depths and finishes.
Advantages:
* High precision and detail
* Fast and efficient process
* Durable and permanent markings
* Versatility in materials and applications
Laser etching offers a wide range of possibilities for marking, modifying, and enhancing metal surfaces across various industries.
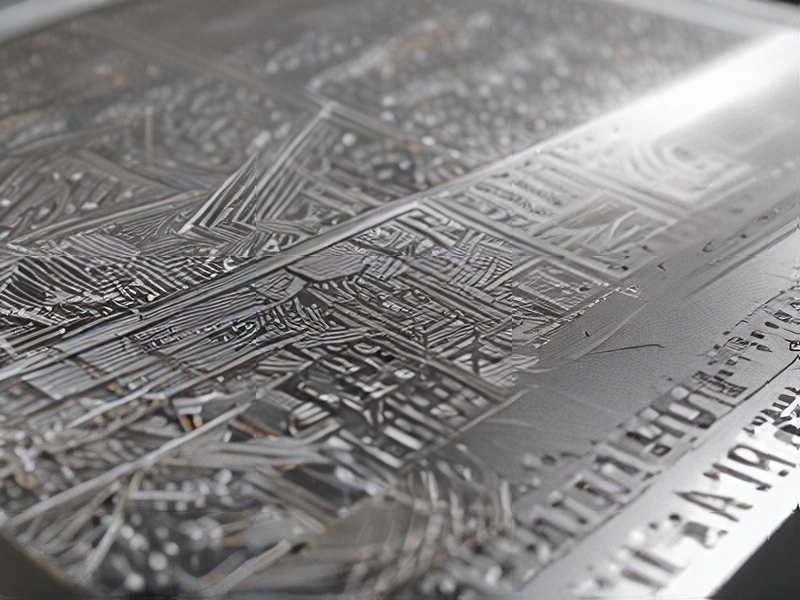
Quality Testing Methods for laser etched metal and how to control quality
Quality testing methods for laser etched metal focus on verifying the accuracy, consistency, and durability of the etched features.
Visual Inspection: This straightforward method involves examining the etched surface for defects like incomplete cuts, uneven depths, over-burning, or distortion. Magnifiers and microscopes can enhance visibility.
Dimensional Measurement: Using calipers, micrometers, or coordinate measuring machines (CMMs), the dimensions of etched features are compared to design specifications. This ensures accuracy and repeatability.
Material Analysis: Techniques like X-ray fluorescence (XRF) can analyze the chemical composition of the etched area to confirm the desired metal properties haven’t been compromised.
Surface Roughness Measurement: Instruments like profilometers assess the surface texture of the etched area, ensuring it meets required standards for functionality and aesthetics.
Durability Testing: This involves subjecting the etched metal to simulated environmental conditions (temperature, humidity, corrosive agents) to assess the longevity and resistance of the etch.
Control Measures:
* Laser System Calibration: Regular calibration ensures the laser operates at the precise power and focus required for consistent etching.
* Material Selection: Choosing appropriate metal types and thicknesses based on the etching requirements.
* Process Parameters Optimization: Fine-tuning laser power, scan speed, and other parameters for each specific application.
* Operator Training: Skilled operators are crucial for consistent quality and safe operation of the laser system.
By implementing these quality testing methods and control measures, manufacturers can guarantee the precision, longevity, and reliability of laser etched metal components.
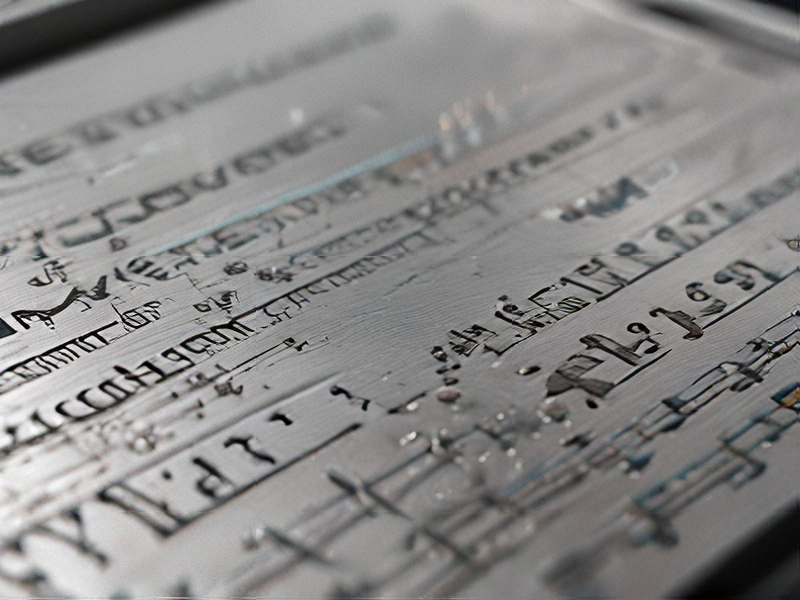
Tips for Procurement and Considerations when Purchasing from laser etched metal
Purchasing laser-etched metal involves careful consideration to ensure quality and meet your specific needs. Here are some tips:
Material Selection: Choose the metal type based on your application’s requirements. Stainless steel is durable and corrosion-resistant, aluminum is lightweight and affordable, while brass offers a distinct aesthetic.
Design and Specifications: Provide clear and detailed design specifications, including desired size, shape, font type, and etching depth.
Finishing Options: Consider various finishing options like polishing, anodizing, or coating to enhance the appearance and durability of the etched metal.
Quantity and Lead Time: Discuss your order quantity and required lead time with the supplier to ensure timely delivery.
Supplier Evaluation: Research and select reputable suppliers with experience in laser etching. Request samples and compare quotes to assess quality and pricing.
Quality Control: Insist on quality control measures such as dimensional accuracy, etching clarity, and surface finish inspection.
Communication: Maintain open communication with the supplier throughout the process to ensure project success.
Remember, a well-informed procurement process will result in high-quality laser-etched metal products that meet your exact specifications.
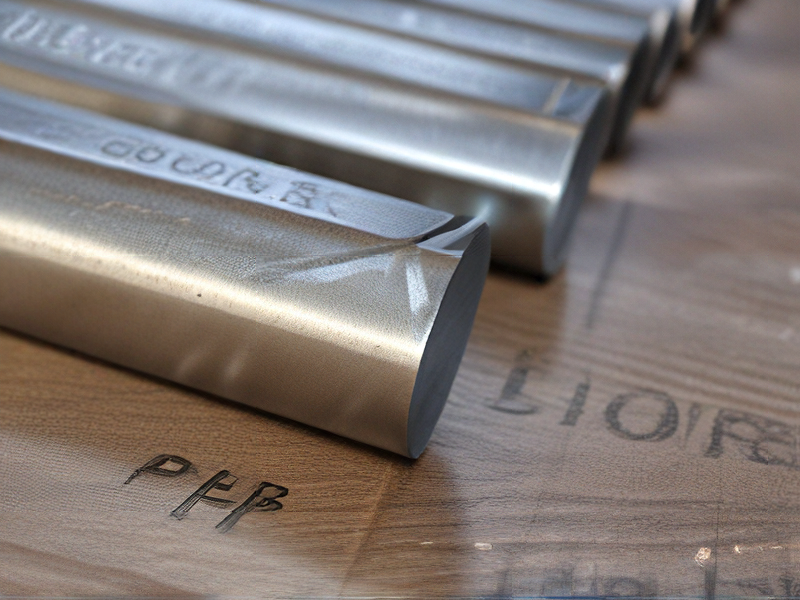
FAQs on Sourcing and Manufacturing from laser etched metal in China
Laser etched metal sourcing and manufacturing in China can be a cost-effective solution for various applications.
Sourcing:
* Online Platforms: Alibaba, Global Sources, and Made-in-China are popular platforms to find manufacturers.
* Industry Events: Attending trade shows focused on metalworking and laser technology can connect you with potential suppliers.
* Local Agencies: Consider partnering with a sourcing agent familiar with Chinese manufacturers specializing in laser etching.
Manufacturing:
* Capabilities: Ensure the manufacturer has the necessary laser etching technology and experience with your desired metals and designs.
* Quality Control: Inquire about their quality control processes to ensure precision and consistency in the etching.
* Lead Times: Discuss production lead times and confirm they align with your project timeline.
Key Considerations:
* Minimum Order Quantities (MOQs): Many manufacturers have MOQs, so factor this into your budget and production needs.
* Communication: Clear communication about your requirements, design specifications, and quality expectations is crucial.
* Payment Terms: Negotiate secure payment terms and ensure clear understanding of payment schedules.
Remember to thoroughly vet potential manufacturers, request samples, and establish a strong working relationship for successful laser etched metal sourcing and manufacturing in China.
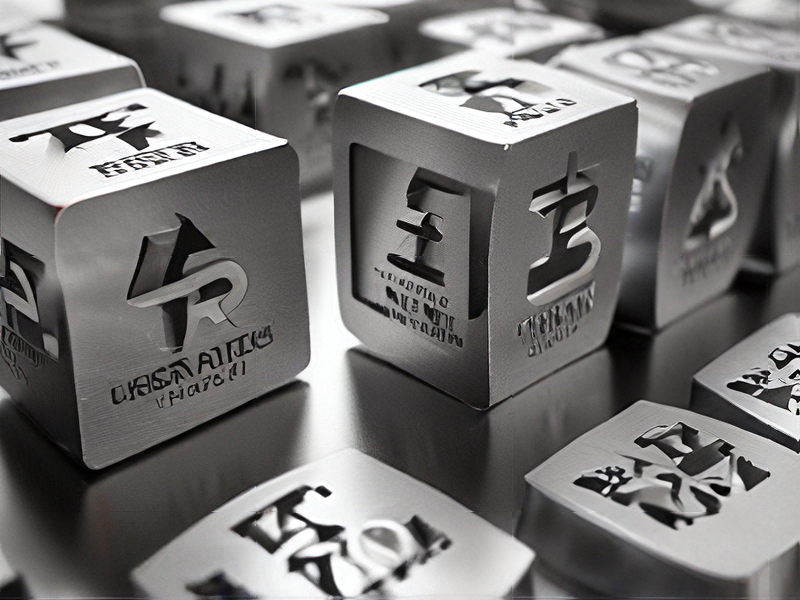