Technology and Applications of laser etching machine
Laser etching machines utilize highly focused beams of light to engrave or mark materials with precision and efficiency. Their applications span various industries, including manufacturing, automotive, aerospace, electronic, and artistic fields.
Technology: Laser etching relies on different types of lasers, such as CO2, fiber, and diode lasers, each suited for specific materials. CO2 lasers are ideal for organic materials like wood and leather, while fiber lasers excel in marking metals and plastics. The process involves controlled pulsing of laser light that removes layers of material to create designs or text. Advanced computer software often drives these machines, allowing intricate designs to be programmed and repeated with minimal human intervention.
Applications:
1. Manufacturing: In production lines, laser etching machines are employed for part identification, serial numbers, and barcodes, enhancing traceability and quality control.
2. Jewelry Design: Jewelers use laser etching to create detailed engravings on metals such as gold and silver, enabling custom designs and personalization.
3. Electronics: In the electronics sector, laser etching marks components with vital information like logos and specifications without adding weight or bulk.
4. Artwork and Crafting: Artists leverage laser etching to produce intricate designs on various materials, from paper to glass.
5. Medical Devices: In the medical field, lasers mark surgical instruments and implants, ensuring easy identification and traceability while maintaining sterility.
Overall, the versatility and precision of laser etching machines make them indispensable in modern manufacturing and creative industries.
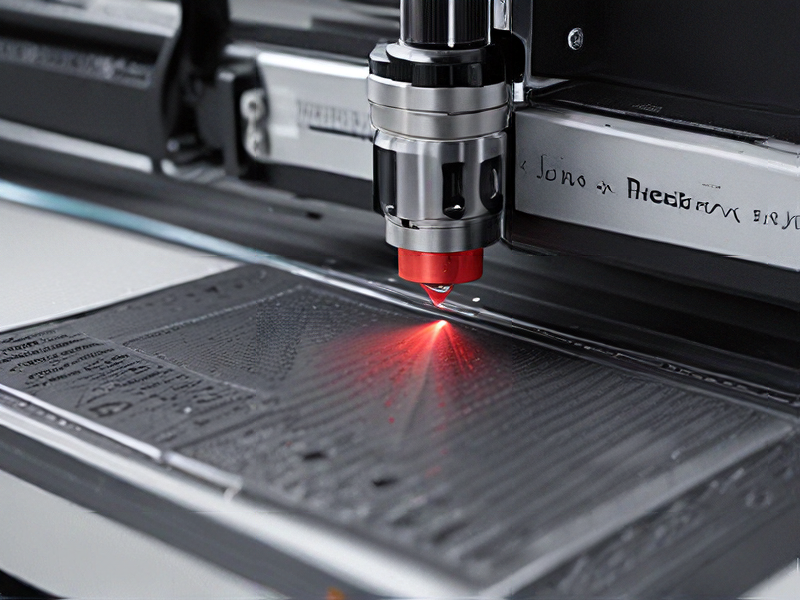
Quality Testing Methods for laser etching machine and how to control quality
Quality testing for laser etching machines is crucial to ensure precision, consistency, and reliability in the etching process. Here are several effective methods to assess and control quality:
1. Visual Inspection: Start with a thorough visual inspection of the etched samples. Check for uniformity in depth, clarity of engraving, and absence of defects such as burns or inconsistencies in color.
2. Dimensional Measurement: Use calipers or laser measurement tools to verify the dimensions of the etched patterns. Accurate measurements ensure that the laser settings are correctly calibrated.
3. Depth Measurement: Employ optical or contact-based depth gauges to assess the etching depth. Consistent depth is critical for functional applications and aesthetic quality.
4. Material Testing: Test the adhesion and durability of the etched designs, especially for industrial applications. Techniques such as tape tests can determine how well the etching withstands wear and tear.
5. Machine Calibration: Regularly calibrate the laser settings, focusing on power, speed, and frequency. Use standardized test patterns to verify the machine’s performance consistently.
6. Environmental Control: Maintain stable environmental conditions, controlling factors like temperature and humidity that may affect the material and the laser operation.
7. Documentation and Feedback Loop: Establish a robust documentation process for each batch of etched items. Maintain records of machine settings and results for continuous improvement. Use customer feedback to refine processes.
Ultimately, a combination of these methods, along with proper training for operators, will enhance the quality of laser etching machine outputs and ensure customer satisfaction. Regular maintenance and adherence to standardized procedures are vital for consistent quality control.
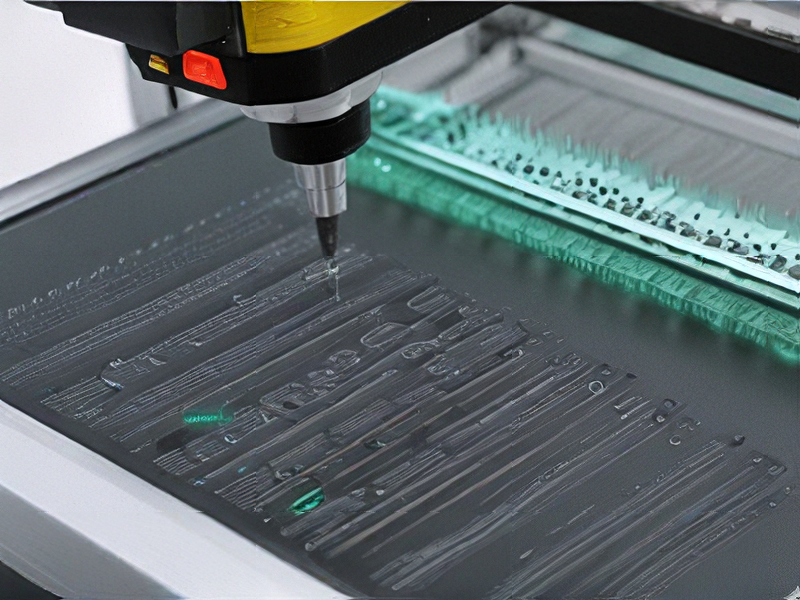
Tips for Procurement and Considerations when Purchasing from laser etching machine
When considering the procurement of a laser etching machine, several key factors should be taken into account to ensure a wise investment.
1. Purpose and Material Compatibility: Define what materials you plan to etch (e.g., wood, metal, acrylic). Ensure the machine you choose is compatible with these materials and meets your specific application needs.
2. Machine Type: Evaluate the type of laser technology (CO2, fiber, or diode). CO2 lasers are great for organic materials, while fiber lasers excel in metal etching. Choose based on your primary use cases.
3. Power and Speed: Higher wattage generally provides faster processing times and a better ability to cut or engrave deeper. Balance power requirements with your production volume to optimize performance.
4. Software and Usability: Check the software compatibility for design uploads. User-friendly software can significantly reduce the learning curve and improve productivity.
5. Size and Footprint: Consider the machine dimensions to ensure it fits your workspace. Factor in the need for ventilation and safety measures as well.
6. Budget and Total Cost of Ownership: Look beyond the initial purchase price to consider maintenance costs, consumables (like lenses and mirrors), and potential downtime.
7. Manufacturer Reputation and Support: Research manufacturers for reliability and after-sales support. Warranty options and available customer service are crucial for long-term satisfaction.
8. Training and Resources: Investigate what training is offered to help you maximize the machine’s capabilities. Good support can enhance your operational efficiency.
By carefully evaluating these considerations, you can make a more informed decision when purchasing a laser etching machine that meets your needs and budget.
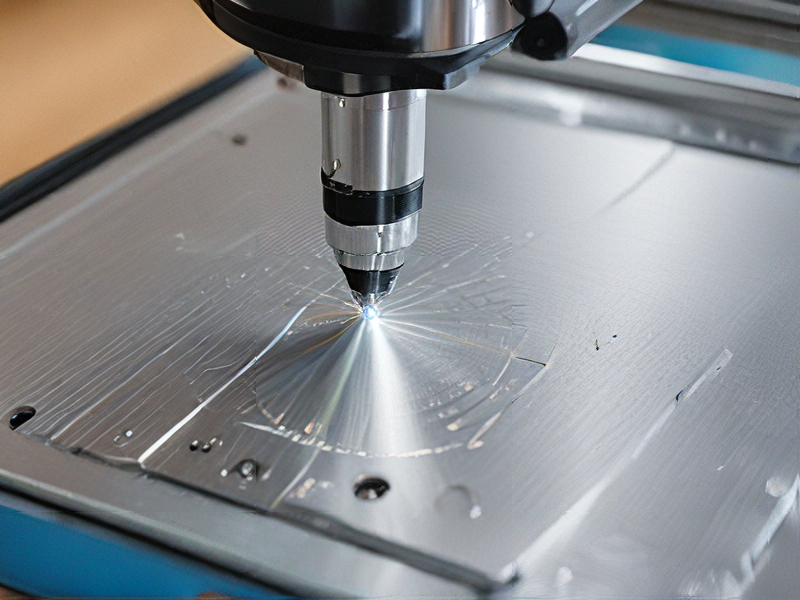
FAQs on Sourcing and Manufacturing from laser etching machine in China
FAQs on Sourcing and Manufacturing Laser Etching Machines from China
1. What is a laser etching machine?
A laser etching machine uses focused laser beams to engrave, cut, or mark materials like metal, wood, glass, and plastic with high precision.
2. Why source laser etching machines from China?
China is a global leader in manufacturing, known for competitive pricing, advanced technology, and a wide range of options. Many factories offer customization and scalability.
3. How do I find reliable manufacturers?
Start by researching established suppliers on platforms such as Alibaba, Made-in-China, and Global Sources. Check reviews, request references, and verify certifications.
4. What should I consider when evaluating suppliers?
Evaluate the manufacturer’s experience, production capacity, quality control processes, and customer service. Inquire about their compliance with international standards.
5. What is the typical MOQ (Minimum Order Quantity) for laser etching machines?
MOQs vary by manufacturer but typically range from 1 to 10 units. Clarify this upfront to align with your budget and needs.
6. How is shipping handled?
Most manufacturers offer assistance with logistics. Choose between air freight for speed or sea freight for cost-effectiveness. Ensure customs clearance is managed.
7. What about warranties and after-sales support?
Ask about warranty periods, support services, and availability of spare parts. A good manufacturer should provide comprehensive after-sales service.
8. How do I handle payment?
Secure payment methods include bank transfers or payment platforms like PayPal. Be cautious with upfront payments; a 30% deposit is common.
9. What documentation is needed for import?
You’ll generally require a commercial invoice, packing list, bill of lading, and any necessary certificates for compliance.
For a successful sourcing experience, thorough research and clear communication are key.
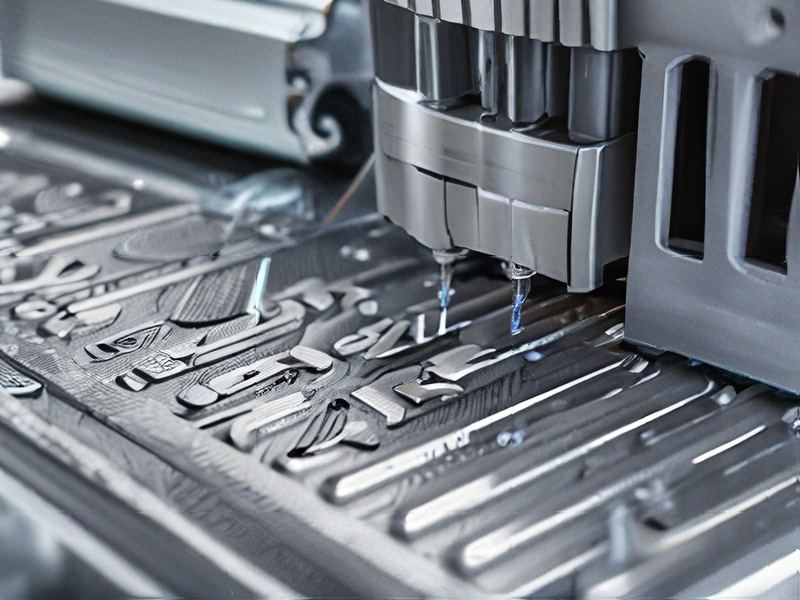