Technology and Applications of laser machine for cutting wood
Laser machines for cutting wood utilize high-powered lasers to precisely cut through various types of wood and wood-based materials. These machines are equipped with CO2 or fiber laser sources, each offering distinct advantages based on the specific requirements of the application.
CO2 lasers are commonly used for wood cutting due to their ability to efficiently absorb into organic materials like wood. They generate a wavelength of around 10.6 micrometers, ideal for cleanly cutting through wood without excessive burning or charring. These lasers are versatile, capable of cutting intricate designs with high precision and minimal material wastage.
Fiber lasers, on the other hand, are gaining popularity for wood cutting due to their high energy efficiency and maintenance advantages. They operate at wavelengths around 1.06 micrometers and are particularly effective for cutting thinner wood materials swiftly and with precision. Fiber lasers are known for their speed and ability to handle reflective materials, making them suitable for a variety of wood types and thicknesses.
Key applications of laser wood cutting include furniture manufacturing, cabinetry, model making, and architectural models. The precision of laser cutting allows for intricate patterns, detailed engraving, and complex shapes that traditional woodworking methods may struggle to achieve. Additionally, lasers can cut wood with minimal kerf width (the amount of material removed by the cutting process), reducing material waste and optimizing production efficiency.
Overall, laser cutting machines for wood combine advanced technology with high precision, making them indispensable tools in modern woodworking and manufacturing processes. Their ability to handle a wide range of materials and produce intricate cuts positions them as essential equipment in industries requiring precision and efficiency in wood processing.
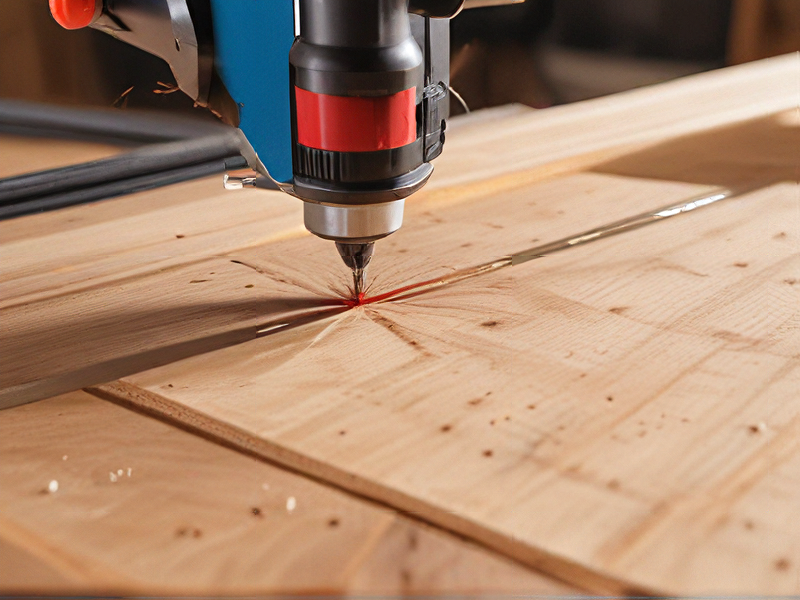
Quality Testing Methods for laser machine for cutting wood and how to control quality
Quality testing methods for a laser machine used for cutting wood typically involve several key approaches to ensure consistent and precise results:
1. Dimensional Accuracy Checks: Utilize precision measuring tools such as calipers or laser measurement devices to verify that cut pieces adhere to specified dimensions within allowable tolerances.
2. Edge Quality Assessment: Inspect cut edges for smoothness, consistency, and absence of burn marks or charring. Visual inspection and tactile evaluation can be supplemented by microscopic examination for fine detail.
3. Material Integrity Testing: Conduct stress tests on cut pieces to ensure they withstand intended use conditions without cracking or warping. This may involve subjecting samples to bending, compression, or environmental conditions.
4. Accuracy of Cuts: Use optical comparators or digital imaging systems to compare cut profiles against design specifications. Software analysis can detect deviations and assess alignment issues within acceptable parameters.
5. Operational Parameters Monitoring: Regularly calibrate laser power settings, focal lengths, and beam alignments to maintain optimal cutting performance and consistency.
Quality Control Measures:
1. Routine Maintenance: Implement a preventive maintenance schedule to keep the laser machine in optimal condition, reducing the risk of performance degradation or sudden failures.
2. Operator Training: Ensure operators are well-trained in machine operation, maintenance procedures, and quality inspection protocols to identify and rectify issues promptly.
3. Statistical Process Control (SPC): Monitor key performance indicators (KPIs) such as cut accuracy and material wastage using statistical methods to detect trends or deviations from established norms.
4. Feedback Loop: Establish a feedback mechanism where operators can report issues encountered during operation. Use this feedback to continuously improve processes and address recurring problems.
By implementing these quality testing methods and control measures, manufacturers can enhance product quality, minimize waste, and optimize the performance of laser machines used for cutting wood.
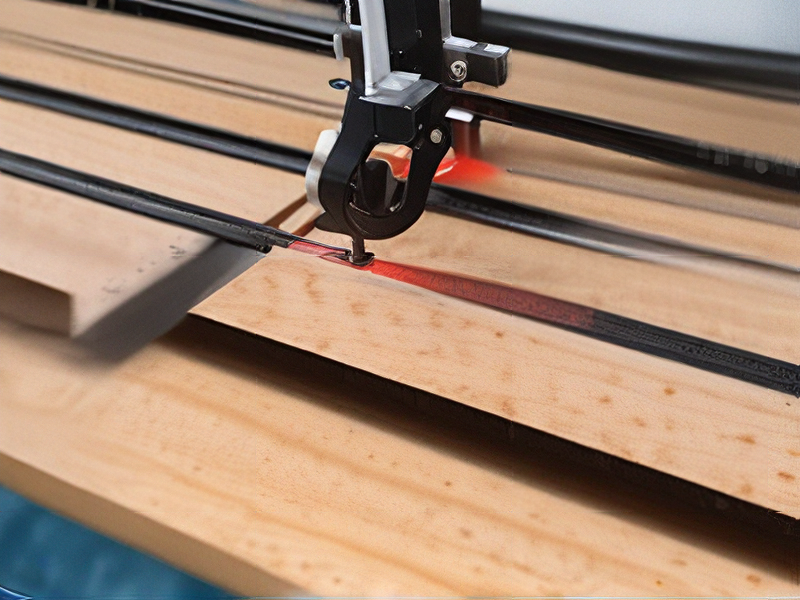
Tips for Procurement and Considerations when Purchasing from laser machine for cutting wood
When procuring a laser machine for cutting wood, it’s essential to consider both technical specifications and practical needs to ensure an optimal purchase. Here are some tips and considerations:
Key Considerations:
1. Laser Power: Choose a laser with sufficient power for the types and thicknesses of wood you plan to cut. Higher wattage allows for faster cutting and the ability to cut thicker materials.
2. Bed Size: Ensure the machine’s bed size can accommodate the largest pieces of wood you intend to work with. A larger bed provides more versatility and reduces the need for frequent repositioning.
3. Precision and Accuracy: Check the machine’s precision and cutting accuracy, crucial for detailed work and minimizing material wastage. Look for specifications on cutting tolerance and resolution.
4. Cooling System: A reliable cooling system is vital to maintain performance and prevent overheating. Consider whether the machine uses water or air cooling and the capacity of the cooling system.
5. Software Compatibility: Ensure the laser cutter is compatible with design software you are comfortable using. Good software integration enhances productivity and ease of use.
6. Maintenance and Support: Investigate the availability of customer support and ease of maintenance. Machines with readily available spare parts and strong manufacturer support are preferable.
7. Safety Features: Look for machines with robust safety features such as emergency stop buttons, protective casings, and proper ventilation systems to handle fumes and dust.
Tips:
– Supplier Reputation: Choose a reputable supplier known for quality products and reliable after-sales service. Read reviews and seek recommendations.
– Cost vs. Value: Don’t solely focus on price. Consider the long-term value, including the machine’s durability, efficiency, and potential return on investment.
– Training and Usage: Ensure proper training for operating the machine to maximize its capabilities and maintain safety standards.
– Trial and Demonstration: Whenever possible, request a demonstration or trial run to observe the machine’s performance and ensure it meets your specific needs.
– Future-proofing: Consider potential future needs and scalability. Investing in a slightly more advanced machine may save costs in the long run as your business grows.
By keeping these considerations in mind, you can make a well-informed decision when purchasing a laser machine for cutting wood, ensuring it meets your current and future needs effectively.
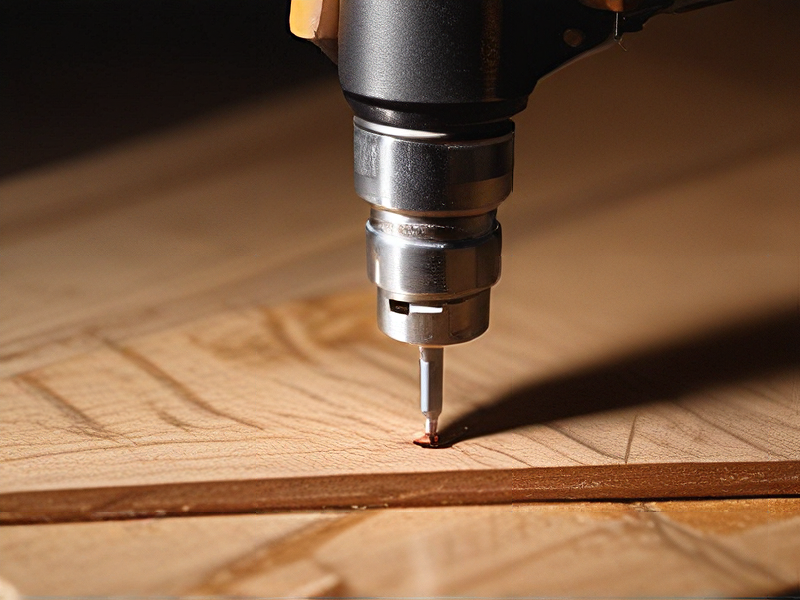
FAQs on Sourcing and Manufacturing from laser machine for cutting wood in China
FAQs on Sourcing and Manufacturing Laser Machines for Cutting Wood in China
1. Why source laser machines from China?
China is known for its competitive pricing, advanced technology, and a wide variety of manufacturers. This combination offers cost-effective solutions without compromising on quality.
2. How do I find reliable manufacturers?
Utilize online platforms like Alibaba, Made-in-China, and Global Sources. Look for manufacturers with positive reviews, verified profiles, and trade assurances. Attending trade shows such as the Canton Fair can also provide direct insights.
3. What should I look for in a supplier?
Consider the supplier’s experience, certifications (like ISO9001, CE), customer feedback, and after-sales support. It’s beneficial if the supplier offers customization and has a robust quality control process.
4. What are the common types of laser machines available?
Common types include CO2 lasers, fiber lasers, and diode lasers. CO2 lasers are widely used for cutting wood due to their precision and efficiency.
5. How do I ensure the quality of the machines?
Request product samples, inspect the manufacturing facility (either personally or via third-party inspection services), and verify the technical specifications. Ensuring compliance with international standards is crucial.
6. What are the typical payment terms?
Common payment terms include 30% deposit before production and 70% balance before shipment. Using payment methods like Letter of Credit (L/C) or Trade Assurance on Alibaba can provide additional security.
7. How long does the manufacturing and shipping process take?
Manufacturing usually takes 20-30 days, depending on customization. Shipping can take an additional 2-6 weeks, based on the shipping method and destination.
8. What should I know about customs and import duties?
Familiarize yourself with your country’s import regulations and duties for laser machines. Hiring a customs broker can streamline the process.
9. Are there after-sales services and warranties?
Reputable suppliers offer warranties (typically 1-2 years) and after-sales services, including technical support, parts replacement, and maintenance guidelines.
10. How do I handle potential language barriers?
Communicate clearly using simple English. Employing a translator or sourcing agent can mitigate misunderstandings and ensure smooth negotiations.
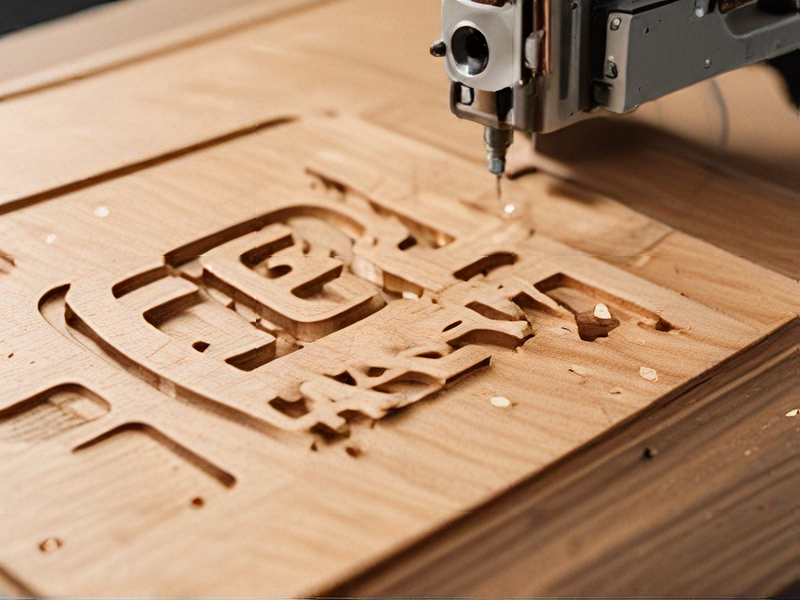