Technology and Applications of laser machine welder
Laser machine welding utilizes focused laser beams to join materials, primarily metals and thermoplastics. This advanced technology offers numerous advantages, making it popular in various industrial applications.
One of the key technologies behind laser welding is the high-energy density of lasers, which allows for precise and rapid heating of the materials being joined. The process can be accomplished using different types of lasers, such as fiber, CO2, and solid-state lasers. These lasers enable deep penetration and minimal heat-affected zones, leading to stronger and cleaner welds with reduced risk of distortion.
Applications of laser welding span multiple sectors. In the automotive industry, it is used for welding components like chassis and exhaust systems, promoting lightweight designs that enhance fuel efficiency. In electronics, laser welding connects delicate components in devices such as smartphones and laptops with precision. The aerospace industry benefits from laser welding’s ability to create strong, lightweight structures, vital for performance and safety.
Additionally, laser welding can automate processes, integrating seamlessly with robotics for increased efficiency and reduced labor costs. Its versatility allows it to handle a variety of materials, including stainless steel, aluminum, and even plastics, making it invaluable in manufacturing.
Overall, laser machine welding stands out for its speed, accuracy, and adaptability across various industries, driving innovation and improving production efficiency.
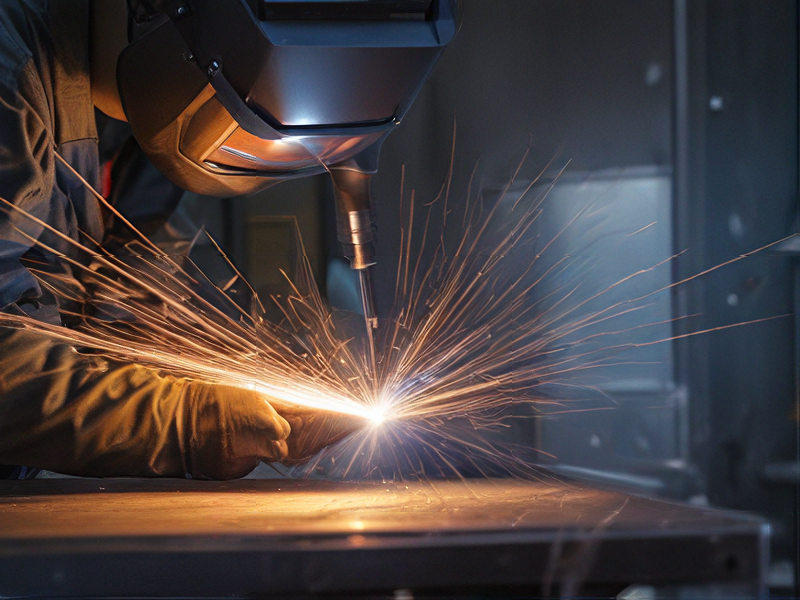
Quality Testing Methods for laser machine welder and how to control quality
Quality testing for laser machine welders is crucial to ensure precision and reliability in welding applications. Key methods include:
1. Laser Beam Quality Assessment:
– Use a beam profiler to evaluate the beam’s intensity distribution and focus. This ensures the laser operates within specified parameters, impacting weld quality.
2. Weld Inspection Techniques:
– Visual Inspection: Check for irregularities such as inconsistencies or discolorations on the weld bead.
– Ultrasonic Testing (UT): Detects internal defects through high-frequency sound waves.
– X-ray or CT Scanning: Identifies internal cracks or voids not visible externally.
3. Mechanical Testing:
– Perform tensile testing to determine the strength and ductility of the welded joints.
– Use bend tests to evaluate ductility and assess the quality of the weld under stress.
4. Microstructural Analysis:
– Employ metallographic examination to analyze grain structure and identify potential issues like porosity or unwanted phase formations.
5. Dimensional Accuracy Checks:
– Use calipers and gauges to ensure welded parts meet specified tolerances.
Quality Control Procedures:
– Implement a Quality Management System (QMS) that adheres to industry standards like ISO 9001 to systematically manage and improve quality processes.
– Regularly calibrate and maintain equipment to ensure consistent performance.
– Conduct training sessions for operators to enhance their skills and understanding of laser welding principles.
– Establish a feedback loop using data from inspections and tests to continuously refine processes and materials.
By encompassing these testing methods and control techniques, manufacturers can enhance the reliability and precision of laser- welded components.

Tips for Procurement and Considerations when Purchasing from laser machine welder
When considering the procurement of a laser machine welder, several key factors should be evaluated to ensure a successful purchase:
1. Specifications and Capabilities: Assess the specific welding applications required, such as material types, thicknesses, and joint configurations. Ensure the machine’s specifications align with your operational needs.
2. Types of Laser Technology: Understand the differences between fiber, CO2, and Nd:YAG lasers. Each has unique advantages depending on the materials being welded and the desired precision.
3. Machine Efficiency and Speed: Evaluate the speed of the welding process and overall machine efficiency. Faster welding can lead to higher productivity and lower operational costs.
4. Cost Considerations: Analyze the total cost of ownership, including initial purchase price, maintenance, and operating costs. Often, lower upfront costs can lead to higher long-term expenses.
5. Supplier Reputation and Support: Research suppliers for their reputation, customer service, and support offerings. Consider their experience in your industry and the availability of after-sale support, including training and maintenance services.
6. Safety Features: Ensure the laser welder has appropriate safety mechanisms, such as emergency stop buttons, protective enclosures, and proper ventilation systems to minimize workplace hazards.
7. Integration and Compatibility: Assess how the new machine will integrate with existing production processes and equipment. Compatibility can streamline workflows and reduce downtime.
8. Warranty and Service Agreements: Look for favorable warranty terms and service agreements that provide peace of mind regarding future repairs and maintenance.
9. User Training: Ensure that the supplier offers adequate training for operators to maximize the machine’s capabilities and minimize operational risks.
By carefully considering these factors, you can make a more informed decision and enhance your welding operations.

FAQs on Sourcing and Manufacturing from laser machine welder in China
FAQs on Sourcing and Manufacturing Laser Machine Welders in China
Q1: Why source laser machine welders from China?
A1: China is a leading manufacturer of laser technology due to its advanced manufacturing capabilities, cost-effectiveness, and an extensive range of suppliers. You can access high-quality products at competitive prices.
Q2: How to find reliable manufacturers?
A2: Use platforms like Alibaba, Made-in-China, or Global Sources. Check reviews, certifications (like ISO), and request samples to verify quality. Additionally, consider visiting trade shows to meet suppliers face-to-face.
Q3: What should I consider about quality control?
A3: Establish clear quality standards and conduct regular inspections. Consider hiring a local quality control agent or working with third-party inspection services to ensure compliance during production.
Q4: How do I handle communication barriers?
A4: Use clear and concise language, and avoid jargon. Employ a reliable interpreter if necessary. Written agreements and specifications help minimize misunderstandings.
Q5: What are the typical lead times for manufacturing?
A5: Lead times can vary but generally range from 4 to 12 weeks, depending on order volume, customization, and supplier workload. Always confirm timelines before placing an order.
Q6: Are there any legal considerations when importing?
A6: Familiarize yourself with import regulations, tariffs, and customs duties in your country. Ensure compliance with local safety and environmental standards for laser equipment.
Q7: What about after-sales service and support?
A7: Inquire about warranty terms and support services. Good manufacturers often provide training, maintenance, and access to spare parts.
By addressing these key points, you can streamline the sourcing and manufacturing process for laser machine welders from China.
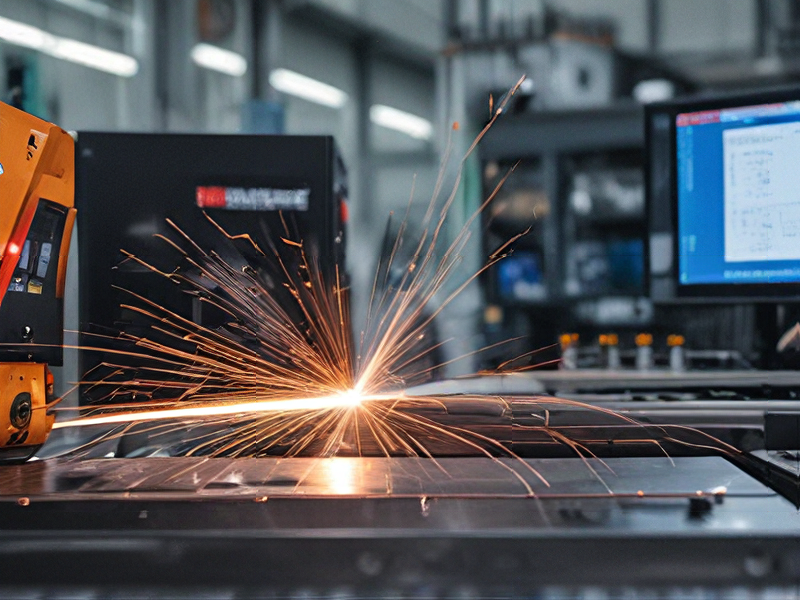