Technology and Applications of laser machine wood cutting
Laser machines revolutionize wood cutting by offering precision, efficiency, and versatility. These machines utilize high-powered lasers to cut through wood with exceptional accuracy, making them ideal for intricate designs and complex shapes. The technology works by focusing a laser beam onto the wood surface, which vaporizes or burns away material along the designated cutting path.
Key advantages include minimal material wastage due to narrow kerf widths, precise control over cutting depths and patterns, and the ability to cut various wood types and thicknesses. Laser cutting also seals wood edges during the process, reducing the need for additional finishing.
Applications span multiple industries:
1. Craftsmanship and Design: Artisans and designers use laser cutting to create custom furniture, decorative items, and artistic pieces that demand intricate detailing.
2. Manufacturing: Mass production benefits from laser cutting’s ability to consistently replicate designs with high precision, making it valuable for furniture manufacturing, cabinetry, and flooring industries.
3. Prototyping and Model Making: Architects and engineers use laser cutting to create scaled models and prototypes quickly and accurately.
4. Personalization: Custom engraving and etching onto wood products like signs, gifts, and promotional items are made easier with laser technology.
Despite its advantages, laser cutting requires considerations such as material type and thickness, as well as proper ventilation and safety measures due to the potential for emissions and fire hazards. Advances in laser technology continue to refine these machines, expanding their capabilities and applications across industries.
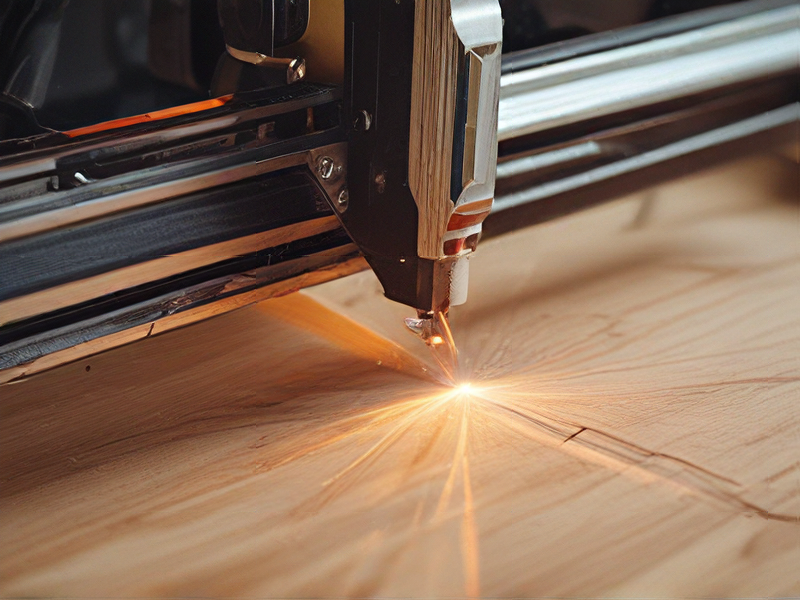
Quality Testing Methods for laser machine wood cutting and how to control quality
Quality testing methods for laser machine wood cutting typically include:
1. Dimensional Accuracy: Use calipers or laser measurement tools to verify that cut dimensions match specifications.
2. Edge Quality: Inspect cut edges visually and with magnification for smoothness, burns, or charring.
3. Material Integrity: Check for any signs of burning, discoloration, or warping that might affect the wood’s structural integrity.
4. Precision of Cuts: Measure the precision of cuts against design specifications using computer-aided tools or templates.
5. Repeatable Performance: Conduct multiple tests to ensure consistency in cutting across different batches or runs.
To control quality:
– Routine Maintenance: Regularly calibrate and maintain the laser machine to ensure consistent performance.
– Operator Training: Provide comprehensive training to operators on machine settings, material handling, and quality standards.
– Quality Checks: Implement a systematic quality control process at different stages of production, from pre-cut checks to post-cut inspections.
– Feedback Loop: Establish a feedback mechanism where operators can report issues encountered during cutting for continuous improvement.
By integrating these methods and controls, manufacturers can maintain high-quality standards in laser machine wood cutting processes.
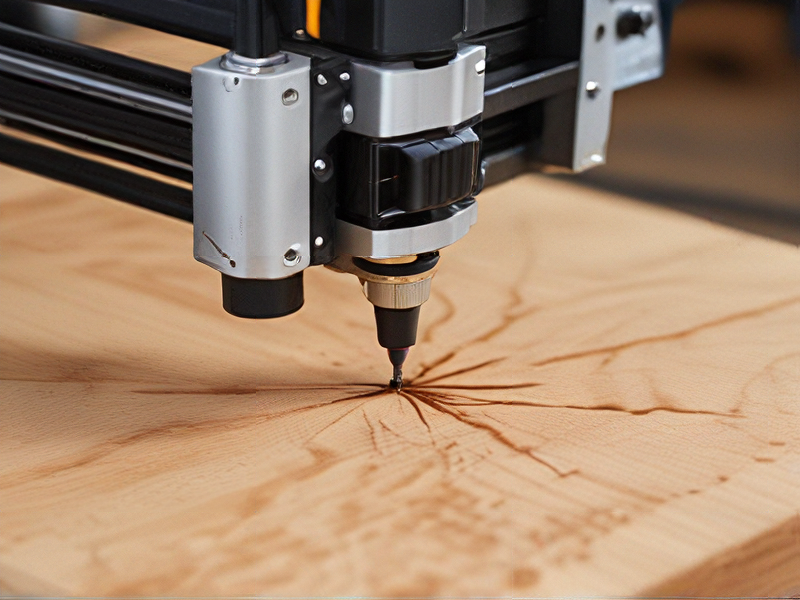
Tips for Procurement and Considerations when Purchasing from laser machine wood cutting
When procuring a laser machine for wood cutting, consider several key factors to ensure you get the right equipment for your needs:
1. Laser Type and Power: Decide between CO2 and fiber lasers based on your material thickness and cutting speed requirements. Higher wattage lasers are suitable for thicker woods and faster cutting speeds.
2. Bed Size and Material Handling: Choose a machine with a bed size that accommodates your typical sheet sizes of wood. Consider automated material handling options if handling large volumes.
3. Precision and Accuracy: Look for machines with high-resolution optics and precision mechanics to ensure accurate cutting, especially for intricate designs or fine detailing.
4. Ease of Use and Software Compatibility: Opt for user-friendly interfaces and software that supports your design workflow. Compatibility with CAD/CAM software can streamline production.
5. Maintenance and Support: Consider the availability of technical support and maintenance services from the supplier or manufacturer to minimize downtime and ensure longevity of the machine.
6. Safety Features: Ensure the machine complies with safety standards and includes features like emergency stops, enclosed cutting areas, and fume extraction systems to protect operators and workspace.
7. Cost and ROI: Evaluate initial investment costs against potential returns on investment based on increased production efficiency and reduced material waste.
8. Supplier Reputation and Reviews: Choose a reputable supplier with positive customer reviews and a track record of delivering reliable equipment and support.
9. Training and Skill Requirements: Assess the training and skill levels required for operating the machine effectively. Some suppliers offer training programs as part of the purchase.
10. Future Expansion: Consider future expansion needs and whether the machine can be upgraded or scaled to meet growing production demands.
By carefully considering these factors, you can make an informed decision when purchasing a laser machine for wood cutting that aligns with your operational requirements and budget.
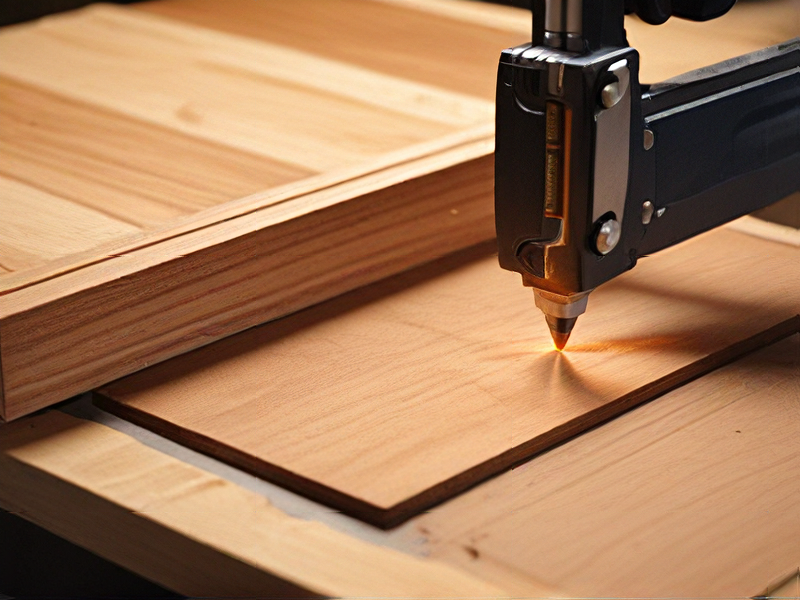
FAQs on Sourcing and Manufacturing from laser machine wood cutting in China
Certainly! When sourcing and manufacturing laser machine wood cutting equipment from China, here are some frequently asked questions (FAQs) to consider:
1. What are the advantages of sourcing laser machines from China?
– China offers competitive pricing due to lower labor and manufacturing costs. They also have a well-established infrastructure for producing advanced machinery.
2. How do I ensure the quality of laser cutting machines from Chinese suppliers?
– Research suppliers thoroughly, checking their reputation, certifications (like ISO), and customer reviews. Request samples or visit their facilities if possible to inspect quality standards.
3. What types of laser cutting machines are available from Chinese manufacturers?
– Chinese manufacturers offer a wide range, including CO2 laser machines for wood, fiber laser cutters for metal, and hybrid machines for versatile cutting applications.
4. What are the typical lead times and shipping options?
– Lead times vary but are generally influenced by customization and order volume. Shipping options include sea freight, which is cost-effective but slower, and air freight for faster delivery.
5. Are there language barriers or cultural differences to consider?
– While English proficiency is improving, communication can sometimes be challenging. Using clear specifications and possibly working with agents or translators can mitigate these issues.
6. What about after-sales support and warranty?
– Ensure suppliers provide comprehensive after-sales support, including training, troubleshooting, and spare parts availability. Clarify warranty terms to avoid misunderstandings.
7. What are the payment terms and import/export considerations?
– Negotiate payment terms that balance risk between both parties. Understand import/export regulations, tariffs, and taxes to avoid unexpected costs.
Navigating these questions can help streamline the process of sourcing laser machine wood cutting equipment from China, ensuring a successful partnership with reliable suppliers.
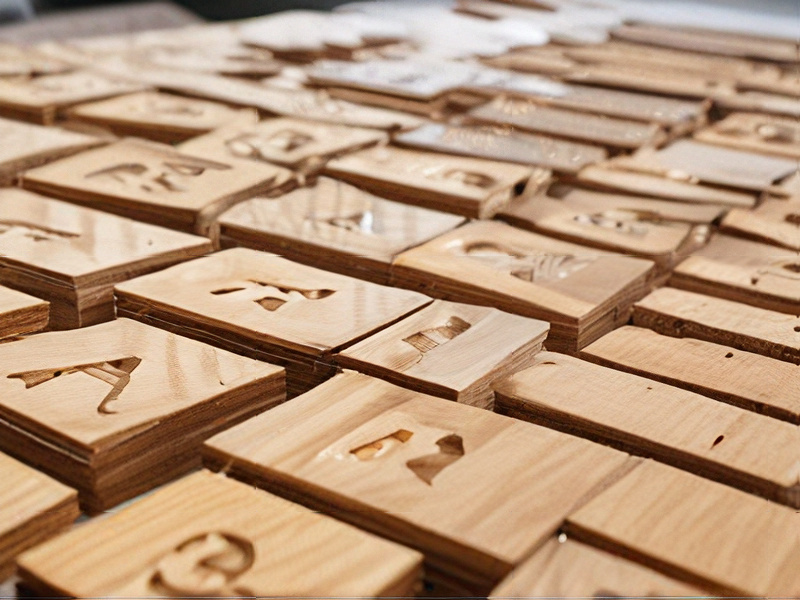