Technology and Applications of laser marking machine on metal
Laser marking machines are widely utilized for marking metals due to their precision, permanence, and versatility. Using a focused laser beam, these machines can etch alphanumeric characters, logos, barcodes, and other designs onto metal surfaces without physical contact. The process involves localized heating, which causes oxidation or material removal, leaving a high-contrast mark.
Key technologies include fiber lasers, which offer high beam quality and efficiency, making them ideal for metals. CO2 lasers are also used for certain applications, providing flexibility in marking plastics and organic materials alongside metals.
Applications span various industries such as automotive, aerospace, electronics, and medical devices. In automotive manufacturing, laser marking ensures traceability and part identification. In aerospace, it facilitates part serialization and compliance with stringent quality standards. In electronics, micro-marking on circuit boards aids in component identification and tracking.
Advantages include non-contact processing, minimal material deformation, and high processing speeds, enhancing productivity. The non-toxic nature of laser marking compared to traditional ink or chemical methods aligns with environmental regulations.
Challenges include initial equipment costs and process optimization for different metal types and thicknesses. However, ongoing advancements in laser technology continue to improve marking quality and efficiency, driving broader adoption across industries seeking reliable, high-precision marking solutions.
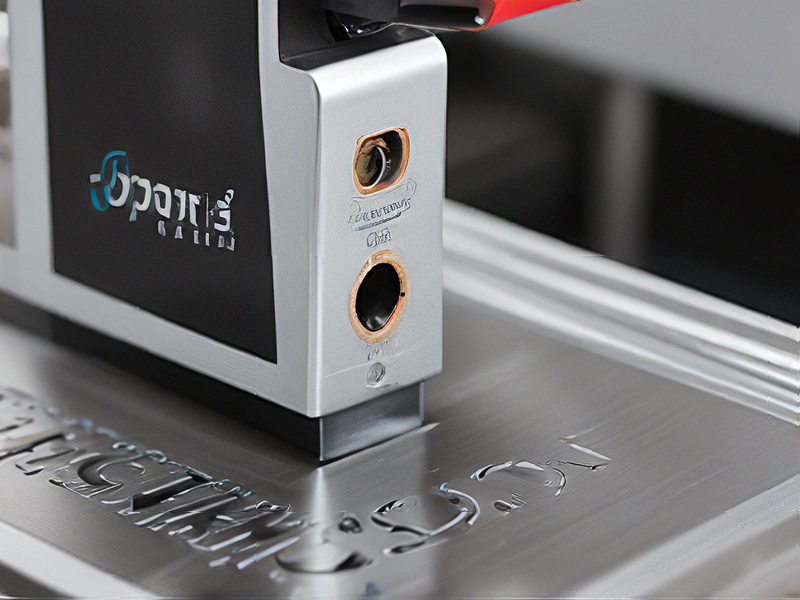
Quality Testing Methods for laser marking machine on metal and how to control quality
Quality testing for laser marking on metal involves several methods to ensure the precision, durability, and legibility of the marks. Here are key methods and controls:
1. Visual Inspection
Method: Examine the marked area under various lighting conditions and magnifications.
Control: Use high-resolution cameras and microscopes to detect imperfections such as inconsistent marking depth, incomplete marks, or surface damage.
2. Surface Roughness Testing
Method: Employ profilometers to measure surface roughness.
Control: Ensure the laser settings (power, speed, frequency) are optimized to produce consistent roughness that aligns with the required specifications.
3. Depth Measurement
Method: Utilize depth gauges or 3D laser scanners to measure the depth of the marking.
Control: Adjust laser parameters to achieve uniform depth according to the design requirements.
4. Adhesion and Durability Testing
Method: Conduct scratch tests, rub tests, and environmental tests (temperature, humidity, chemicals) to assess the mark’s durability.
Control: Use standardized test methods like ASTM or ISO to evaluate adhesion and resistance to wear.
5. Contrast and Legibility Assessment
Method: Analyze the contrast between the mark and the base material using image analysis software.
Control: Optimize laser parameters to enhance contrast and ensure marks are legible under different lighting conditions.
6. Consistency and Repeatability Testing
Method: Perform repeated marking on identical samples and compare results.
Control: Implement statistical process control (SPC) to monitor and maintain consistency over time.
7. Microscopic Analysis
Method: Examine the marks under a microscope to detect micro-cracks or other minute defects.
Control: Regularly calibrate and maintain laser equipment to prevent deviations.
Controlling Quality
– Calibration: Regularly calibrate laser marking machines.
– Maintenance: Perform routine maintenance and replace worn-out parts.
– Training: Ensure operators are well-trained in handling and troubleshooting the equipment.
– Software: Utilize advanced software for precise control of laser parameters.
– Documentation: Maintain detailed records of tests and machine settings for traceability.
By combining these testing methods and controls, the quality of laser markings on metal can be effectively managed, ensuring reliable and high-quality outcomes.
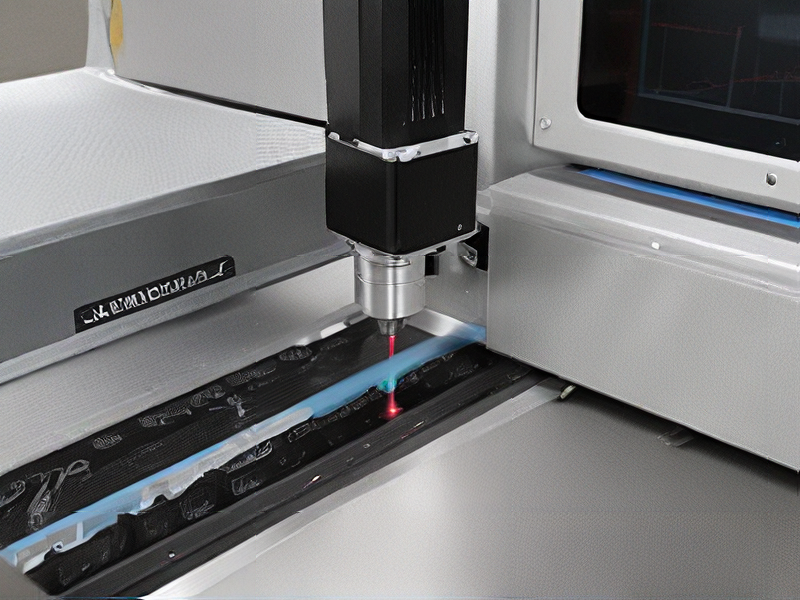
Tips for Procurement and Considerations when Purchasing from laser marking machine on metal
When procuring a laser marking machine for metal, several key considerations can streamline the decision-making process:
1. Type of Laser Technology: Choose between fiber, CO2, or UV lasers based on your specific marking requirements (depth, speed, material compatibility).
2. Marking Quality and Precision: Evaluate the machine’s capability to achieve high-resolution markings without compromising on clarity or durability.
3. Speed and Throughput: Assess the machine’s marking speed, especially if you have high-volume production needs.
4. Software and Compatibility: Ensure the software is user-friendly and supports various file formats (CAD, vector graphics) for seamless integration into your workflow.
5. Maintenance Requirements: Consider the ease of maintenance and availability of service and support from the manufacturer or supplier.
6. Safety Features: Verify that the machine meets safety standards and includes features like interlocks and enclosure systems to protect operators.
7. Cost and Return on Investment (ROI): Compare initial purchase costs with long-term operational savings and productivity gains to determine the ROI.
8. Supplier Reputation and Support: Choose a reputable supplier with a track record of quality products and reliable customer support.
9. Training and Technical Expertise: Ensure the supplier provides adequate training for your operators and technical support for any troubleshooting needs.
10. Future Scalability: Anticipate future needs and ensure the machine can accommodate potential expansions or changes in production requirements.
By carefully considering these factors and aligning them with your specific operational needs, you can make a well-informed decision when purchasing a laser marking machine for metal.
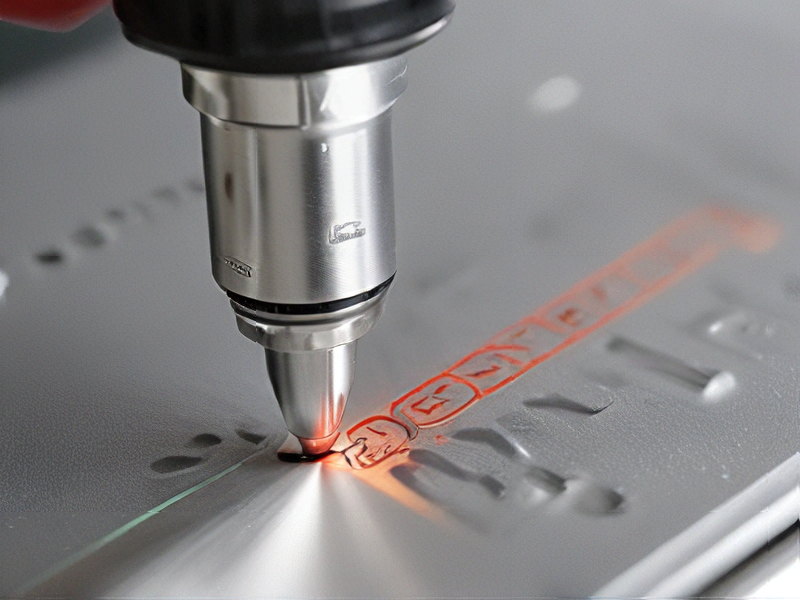
FAQs on Sourcing and Manufacturing from laser marking machine on metal in China
FAQs on Sourcing and Manufacturing Laser Marking Machines on Metal in China
1. Why source laser marking machines from China?
China offers competitive pricing, advanced technology, and a wide range of options for laser marking machines. Manufacturers benefit from high-quality production and cost-effective solutions.
2. What are the key features to look for in a laser marking machine?
Consider power output, marking speed, precision, software compatibility, and the type of laser (fiber, CO2, or UV). These features determine the machine’s efficiency and suitability for different metals.
3. How do I find reliable manufacturers in China?
Utilize online platforms like Alibaba, Made-in-China, and Global Sources. Verify suppliers through reviews, certifications, and factory audits. Engaging with a sourcing agent can also ensure quality and reliability.
4. What certifications should Chinese manufacturers have?
Look for ISO 9001 for quality management, CE for European standards, and FDA for US compliance. These certifications ensure the machine meets international safety and quality standards.
5. What are the common types of laser marking technologies available?
The main types are fiber lasers, ideal for metals; CO2 lasers, suitable for non-metals; and UV lasers, used for precision marking on sensitive materials. Fiber lasers are most commonly used for metal marking.
6. How does the shipping process work?
Manufacturers typically handle the export process, including customs documentation. Shipping can be via sea or air freight. Ensure you understand Incoterms (FOB, CIF) to clarify responsibilities and costs.
7. What about after-sales support and warranties?
Reputable manufacturers offer warranties ranging from 1 to 3 years, including technical support and spare parts. Confirm the terms of service, including remote assistance and local repair options.
8. Are there risks in sourcing from China?
Risks include quality discrepancies, communication barriers, and logistics challenges. Mitigate these by conducting thorough research, clear contracts, and regular communication.
9. Can I customize the machines?
Yes, many manufacturers offer customization to meet specific requirements, including software, power settings, and physical design.
10. What payment terms are common?
Typical terms include a 30% deposit with the balance paid before shipment. Payment methods often accepted are T/T (bank transfer), L/C (letter of credit), and sometimes PayPal for smaller amounts.
These FAQs provide a foundational understanding for sourcing and manufacturing laser marking machines on metal from China, ensuring informed decision-making and successful procurement.
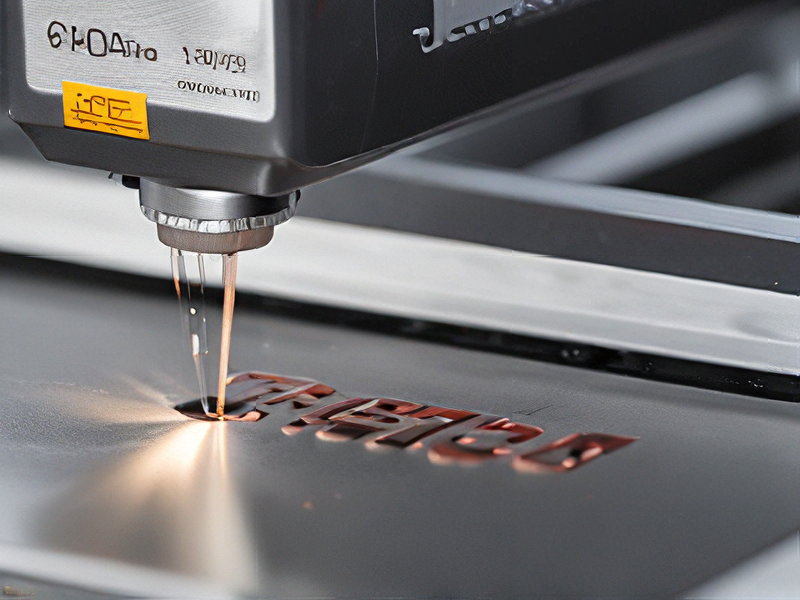