Technology and Applications of laser marking metal
Laser marking on metal is a precise and efficient method used to inscribe text, logos, barcodes, and other information onto metal surfaces. This technology employs focused laser beams to create high-contrast marks that are permanent and resistant to wear and corrosion.
Technology
Laser marking technology utilizes various laser types, including fiber lasers, CO2 lasers, and UV lasers, each suited for different applications. Fiber lasers are the most common for metal marking due to their high power and efficiency. The process involves directing the laser beam onto the metal surface, where it alters the material through engraving, annealing, or etching:
– Engraving: The laser removes a portion of the metal, creating a groove or depression.
– Annealing: The laser heats the metal without removing material, causing oxidation that changes the surface color.
– Etching: The laser removes a thin layer of metal, leaving a contrasting mark.
Applications
Laser marking is used across various industries due to its precision, speed, and durability. Key applications include:
– Automotive: Marking parts and components for traceability and compliance with regulations.
– Aerospace: Identifying parts with serial numbers, barcodes, and logos to ensure traceability and authenticity.
– Medical Devices: Ensuring compliance with strict regulatory requirements by marking instruments and implants with unique identifiers.
– Electronics: Labeling components and circuit boards with serial numbers, logos, and barcodes.
– Jewelry: Personalizing pieces with intricate designs, names, and dates.
Advantages
Laser marking offers several benefits:
– Non-contact process: Prevents damage to the metal.
– High precision: Allows for intricate and detailed markings.
– Durability: Marks are resistant to wear, heat, and chemicals.
– Speed: Rapid marking process suitable for high-volume production.
In summary, laser marking on metal is a versatile and robust technology crucial for ensuring product identification, traceability, and compliance across various industries.
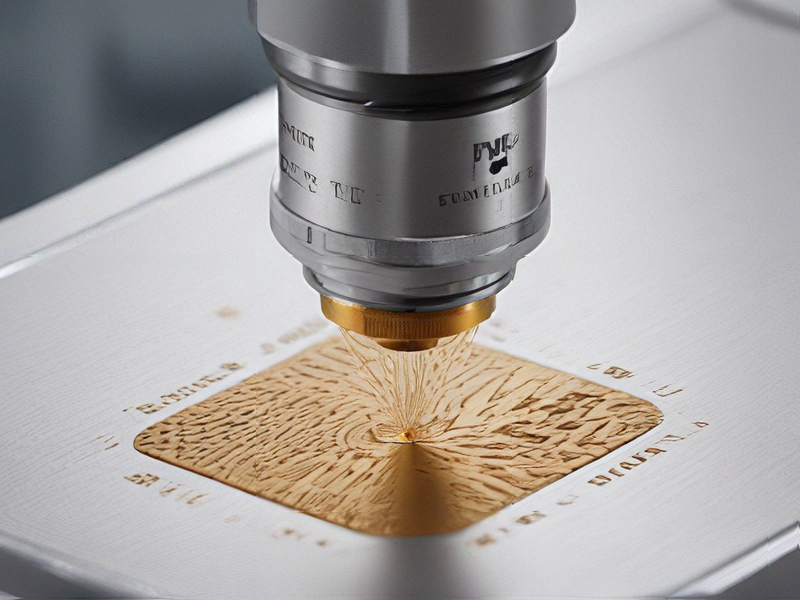
Quality Testing Methods for laser marking metal and how to control quality
Quality testing for laser marking on metal involves several methods to ensure precision, durability, and clarity. Key testing methods and quality control techniques include:
1. Visual Inspection: This basic method checks for the overall appearance, readability, and completeness of the laser marks. Any defects, such as incomplete marks or excessive burn, are identified.
2. Microscopic Examination: Using microscopes to examine the marks closely ensures fine details are accurately reproduced and checks for micro-cracks or inconsistencies.
3. Surface Profilometry: This technique measures the depth and topography of the laser mark, ensuring it meets the specified depth and surface characteristics.
4. Adhesion and Abrasion Tests: These tests assess the durability of the laser mark by simulating wear and tear. Methods include tape tests (to check adhesion) and abrasion tests (to simulate rubbing or scratching).
5. Corrosion Testing: Exposing the marked metal to corrosive environments checks the resistance of the laser mark to corrosion, ensuring longevity and readability over time.
6. Laser Power and Speed Calibration: Regularly calibrating the laser’s power and speed settings ensures consistent marking quality. Incorrect settings can lead to variations in mark depth and clarity.
7. Material Compatibility Tests: Different metals react differently to laser marking. Testing different materials ensures the process is optimized for each type of metal, maintaining quality across various substrates.
8. Software Verification: Ensuring the software controlling the laser is up-to-date and correctly configured prevents errors and maintains precision in marking.
9. Environmental Controls: Maintaining a controlled environment (temperature, humidity, dust) in the laser marking area prevents external factors from affecting the mark quality.
To control quality, implement a robust quality management system (QMS) that includes regular equipment maintenance, operator training, and detailed documentation of processes and results. Regular audits and continuous improvement practices help in maintaining high standards of quality in laser marking on metal.
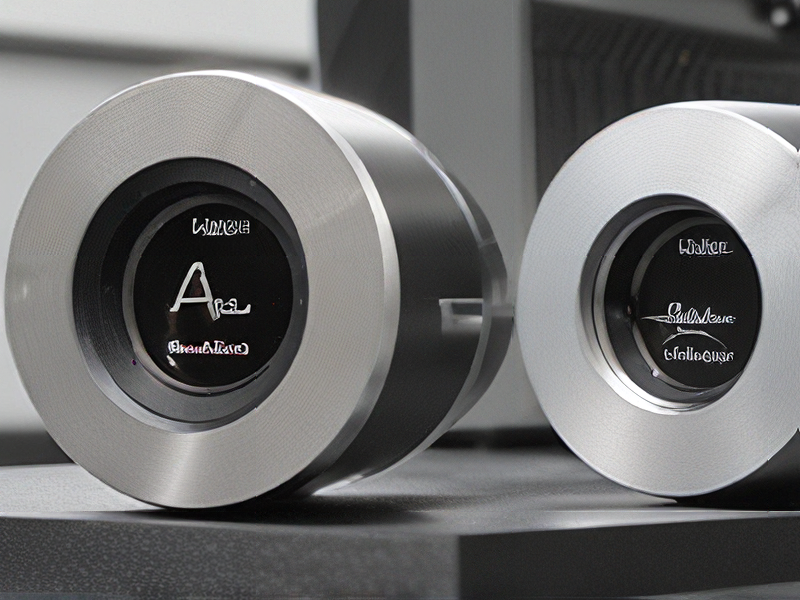
Tips for Procurement and Considerations when Purchasing from laser marking metal
When procuring laser marking systems for metal, consider the following tips and factors:
Key Considerations
1. Material Compatibility: Ensure the laser marking system is suitable for the specific type of metal you are working with, such as stainless steel, aluminum, or titanium.
2. Laser Type: Fiber lasers are often preferred for metal marking due to their efficiency and precision. Evaluate if this type suits your requirements.
3. Power and Speed: Higher power lasers can mark more quickly and deeply, but may be more expensive. Assess the balance between speed, depth of marking, and budget.
4. Precision and Quality: Look for systems that offer high resolution and consistent quality, crucial for detailed or high-precision applications.
5. Software Compatibility: Ensure the marking software is user-friendly and compatible with your existing systems. Advanced features like CAD import can be beneficial.
6. Safety Features: Verify that the system includes safety features such as enclosures and safety interlocks to protect operators.
7. Maintenance and Support: Consider the availability of maintenance services and technical support. A reliable supplier should offer robust post-purchase support.
Tips for Procurement
1. Supplier Evaluation: Choose reputable suppliers with a track record of quality and reliability. Customer reviews and case studies can provide insight into their performance.
2. Cost vs. Value: While cost is important, consider the total cost of ownership, including maintenance and operational costs. Sometimes a higher upfront cost can result in lower long-term expenses.
3. Customization: Look for suppliers who can tailor the system to your specific needs, whether it’s for specific marking depths or customized software features.
4. Training and Installation: Ensure the supplier offers comprehensive training and installation services to maximize the efficiency and safety of the system.
5. Warranty and Service Contracts: Secure a solid warranty and consider extended service contracts to safeguard against potential future issues.
6. Sample Testing: Request sample markings on your material to evaluate the system’s performance before making a final decision.
By carefully considering these factors and tips, you can ensure that your procurement process for a laser marking system is thorough, resulting in a solution that meets your needs effectively and efficiently.
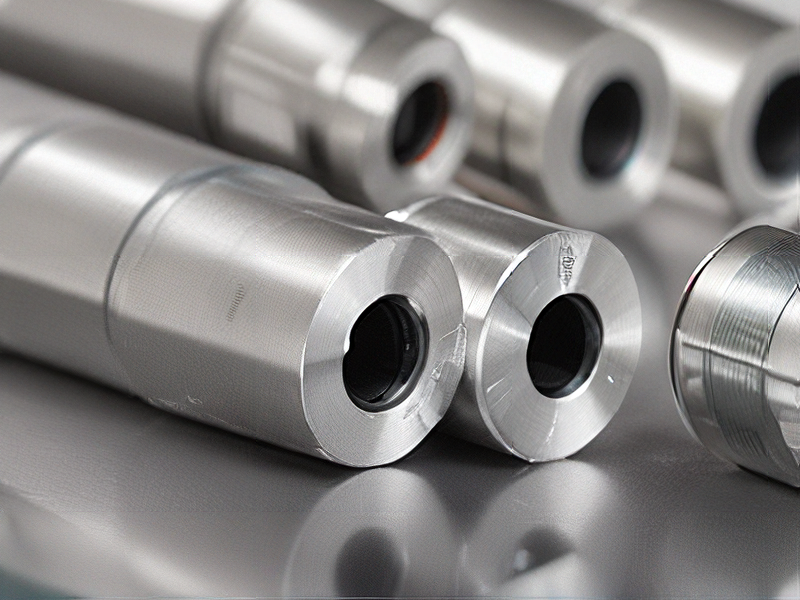
FAQs on Sourcing and Manufacturing from laser marking metal in China
FAQs on Sourcing and Manufacturing Laser Marked Metal in China
#### 1. Why source laser marked metal from China?
China offers competitive pricing, advanced technology, and a wide selection of manufacturers experienced in laser marking. This makes it a cost-effective option without compromising on quality.
#### 2. How do I find reliable manufacturers in China?
Use platforms like Alibaba, Global Sources, and Made-in-China. Look for manufacturers with high ratings, extensive experience, and positive reviews. Request samples to evaluate quality before placing bulk orders.
#### 3. What are the common laser marking techniques used?
Fiber laser marking is the most common, providing high precision and durability. CO2 and YAG lasers are also used, depending on the material and required marking depth.
#### 4. How can I ensure the quality of laser marked metals?
Request detailed specifications and quality assurance certificates from the manufacturer. Consider third-party inspections and audits. Always request samples before large-scale production.
#### 5. What factors affect the cost of laser marking in China?
Costs depend on material type, design complexity, batch size, and additional services like coating or finishing. Bulk orders typically reduce per-unit costs.
#### 6. Are there any standards or certifications to look for?
Look for ISO certification and compliance with RoHS and REACH standards. These ensure that the products meet international quality and safety standards.
#### 7. What is the typical lead time for manufacturing?
Lead times vary but typically range from 2 to 6 weeks, depending on order complexity and size. Ensure to factor in shipping times when planning.
#### 8. How do I handle shipping and logistics?
Most manufacturers offer shipping services. You can also use freight forwarders for better control. Ensure you understand import regulations and duties in your country.
#### 9. What are the payment terms commonly used?
Common terms include a 30% deposit before production and the remaining 70% upon shipment. Use secure payment methods like Letters of Credit or Alibaba’s Trade Assurance for added security.
#### 10. Can I customize my laser marked metal products?
Yes, most manufacturers offer customization services. Provide detailed specifications and designs to ensure your requirements are met.
Sourcing laser marked metal from China can be a seamless process with the right preparation and due diligence.
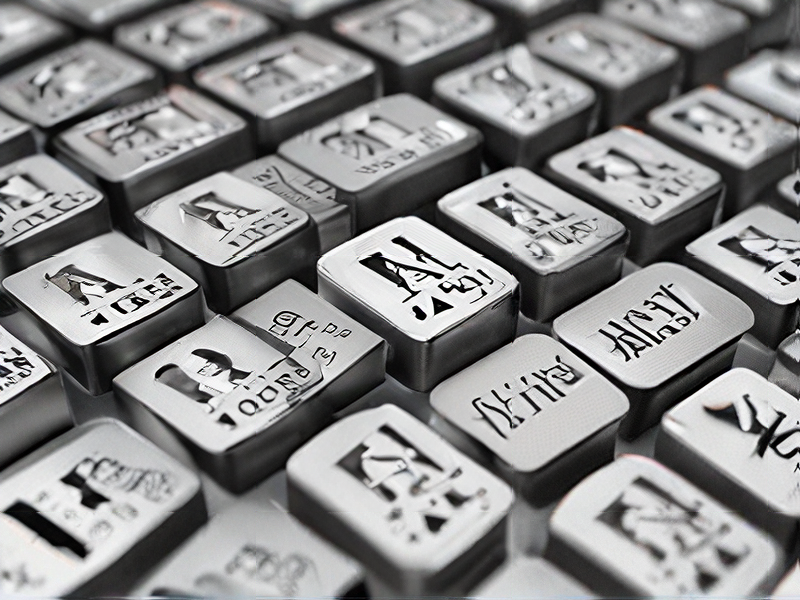