Technology and Applications of laser marking on metal
Laser marking on metal involves using a focused beam of light to create permanent marks on metal surfaces. The technology relies on different methods, including annealing, engraving, etching, and foaming, each suitable for various applications depending on the desired mark and metal type.
Technologies:
1. Fiber Lasers: Widely used for metal marking due to their high beam quality and efficiency. Ideal for applications requiring fine detail and high-speed marking.
2. CO2 Lasers: Less common for metals but used in certain applications where deeper engraving is not required.
3. Nd:YAG Lasers: Versatile and can be used for both deep engraving and surface marking.
Applications:
1. Industrial Manufacturing: Used for part identification, traceability, and quality control by marking serial numbers, barcodes, and QR codes on automotive, aerospace, and electronic components.
2. Medical Devices: Ensures compliance with regulatory requirements by marking instruments and implants with identification codes and logos.
3. Jewelry and Personalization: Engraving custom designs, logos, and text on jewelry and luxury items.
4. Tool and Die Making: Marking tools and dies with identification numbers, measurements, and calibration data.
Advantages:
– Durability: Laser marks are resistant to wear, heat, and chemicals, making them ideal for harsh environments.
– Precision: Allows for high-resolution marking, essential for detailed logos, text, and barcodes.
– Speed: Rapid marking capabilities increase production efficiency.
– Non-contact Process: Reduces mechanical wear on the marking device and prevents damage to the metal surface.
Laser marking on metal is a crucial technology across various industries due to its precision, durability, and versatility.
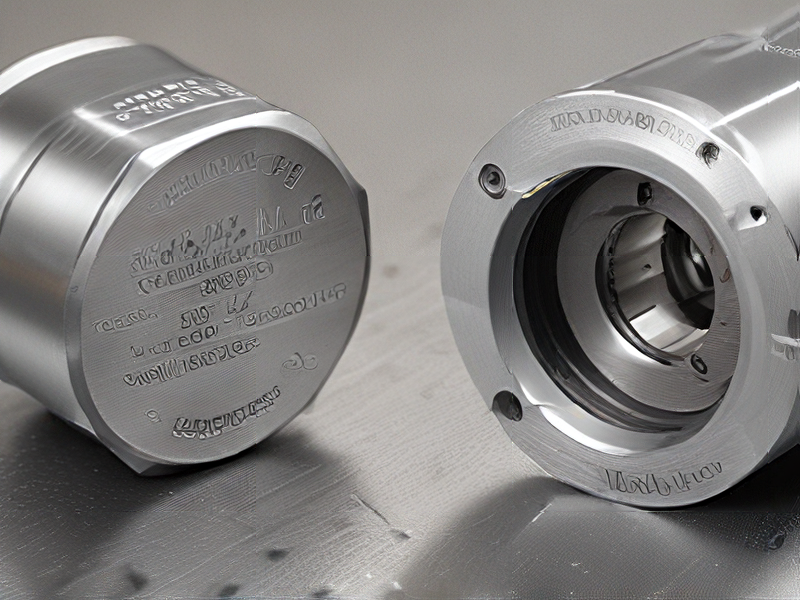
Quality Testing Methods for laser marking on metal and how to control quality
Quality testing for laser marking on metal involves several methods to ensure the markings are precise, durable, and meet required standards. Key testing methods include:
1. Visual Inspection: Using magnification tools to check for clarity, sharpness, and consistency of the markings.
2. Microscopy: Employing optical or electron microscopes to analyze the fine details of the laser mark, ensuring it meets micro-level specifications.
3. Depth Measurement: Utilizing profilometers or other depth-measuring tools to confirm that the laser has penetrated the metal to the desired depth.
4. Adhesion Tests: Applying tape or other adhesives to the marked area and then removing it to check if any part of the marking is lifted, ensuring the mark’s adhesion to the metal.
5. Abrasion Resistance: Scratching or rubbing the marked surface with specified materials to test the durability of the mark under physical stress.
6. Chemical Resistance: Exposing the marked metal to chemicals or solvents to ensure the marking remains intact and legible.
7. Thermal Cycling: Subjecting the marked metal to varying temperatures to test the mark’s stability under thermal stress.
8. Contrast Measurement: Using optical measurement tools to quantify the contrast between the marked and unmarked areas, ensuring readability.
Quality Control Methods
1. Standard Operating Procedures (SOPs): Implementing detailed SOPs for laser marking processes, including machine settings, material handling, and environmental controls.
2. Calibration and Maintenance: Regular calibration and maintenance of laser marking equipment to ensure consistent performance and accuracy.
3. Training and Certification: Ensuring that operators are well-trained and certified to handle laser marking equipment, reducing the risk of errors.
4. Process Monitoring: Utilizing real-time monitoring systems to track laser performance and marking quality during production.
5. Sample Testing: Conducting regular sample testing from production batches to ensure ongoing quality and compliance with specifications.
6. Data Recording and Analysis: Keeping detailed records of marking parameters and inspection results to identify trends, address issues, and improve processes.
These methods collectively help maintain high-quality standards in laser marking on metals, ensuring durability, readability, and compliance with industry requirements.
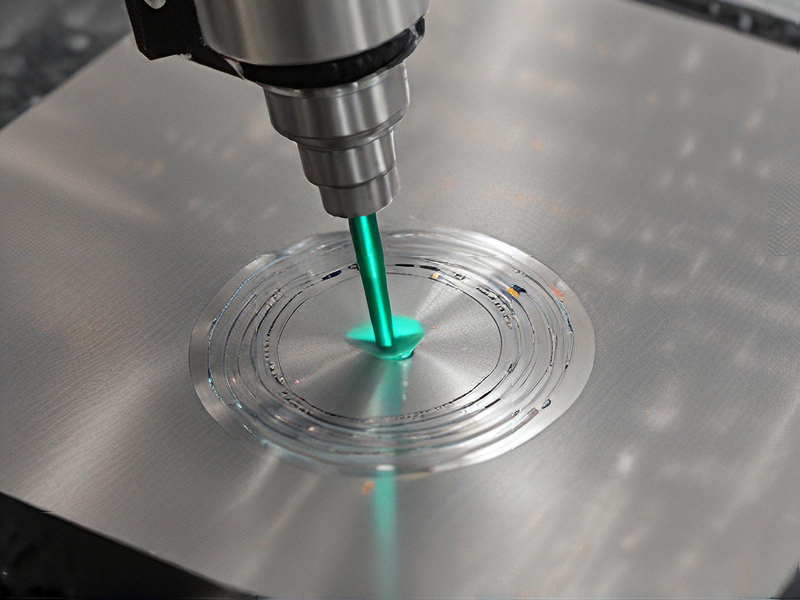
Tips for Procurement and Considerations when Purchasing from laser marking on metal
When procuring laser marking services for metal, consider the following tips and factors:
1. Material Compatibility: Ensure the laser marking technology is compatible with the metal type you’re using (e.g., stainless steel, aluminum, titanium). Different metals may require different laser settings.
2. Laser Type: Choose the appropriate laser type (fiber, CO2, or Nd:YAG) based on the metal and desired marking quality. Fiber lasers are generally preferred for metals due to their precision and efficiency.
3. Marking Quality: Evaluate the resolution, contrast, and permanence of the markings. High-quality laser markings should be clear, durable, and resistant to wear and environmental factors.
4. Speed and Efficiency: Consider the marking speed, especially for high-volume production. Faster marking speeds can increase productivity but ensure it doesn’t compromise quality.
5. Customization and Flexibility: Ensure the laser marking system can handle various designs, including logos, serial numbers, and barcodes. The ability to quickly switch between different markings is crucial for flexibility.
6. Software and Automation: Look for user-friendly software that offers easy design creation and integration with existing automation systems. This can streamline the marking process and reduce the likelihood of errors.
7. Cost: Assess the total cost of ownership, including initial investment, maintenance, and operating costs. Fiber lasers, while more expensive upfront, often offer lower long-term costs due to their durability and low maintenance needs.
8. Vendor Reliability: Choose a reputable vendor with a proven track record in laser marking technology. Consider their customer support, warranty, and service options.
9. Safety: Ensure the laser marking system complies with safety standards and includes necessary safety features to protect operators from laser exposure.
10. Environmental Impact: Consider the environmental footprint of the laser marking process, including energy consumption and any waste produced.
By addressing these factors, you can ensure efficient, high-quality, and cost-effective laser marking on metal for your procurement needs.
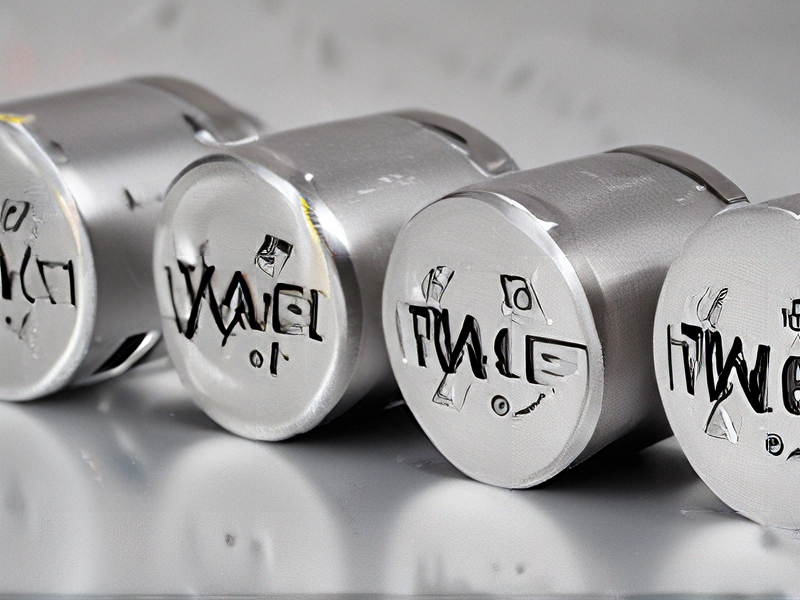
FAQs on Sourcing and Manufacturing from laser marking on metal in China
FAQs on Sourcing and Manufacturing Laser Marking on Metal in China
#### 1. Why source laser marking on metal from China?
China offers competitive pricing, advanced technology, and a vast pool of experienced manufacturers. The country’s robust supply chain ensures high-quality materials and efficient production processes.
#### 2. What types of metals can be laser marked?
Common metals include stainless steel, aluminum, brass, copper, titanium, and various alloys. Laser marking is versatile and can be used on both coated and uncoated surfaces.
#### 3. What should I consider when choosing a manufacturer?
Look for manufacturers with certifications like ISO 9001, experience in laser marking, a strong portfolio, and positive customer reviews. Visiting the factory or requesting samples can also help assess quality.
#### 4. How does laser marking work on metal?
Laser marking involves using a focused laser beam to alter the surface of the metal. It can create precise, permanent marks such as logos, serial numbers, and barcodes without damaging the material.
#### 5. What are the benefits of laser marking on metal?
Laser marking is precise, permanent, and resistant to wear and corrosion. It is also flexible for different designs and types of information and does not require direct contact with the metal.
#### 6. How do I ensure the quality of the laser marking?
Specify your requirements clearly, including the type of metal, design, and marking depth. Request prototypes or samples before full production. Regularly monitor the production process and conduct quality checks on finished products.
#### 7. What are the typical lead times and costs?
Lead times vary but generally range from a few days to a few weeks, depending on order complexity and volume. Costs depend on factors like material type, design intricacy, and quantity, but sourcing from China is usually cost-effective.
#### 8. Are there any risks associated with sourcing from China?
Risks include potential communication barriers, intellectual property concerns, and quality control issues. Mitigate these by working with reputable suppliers, using contracts, and considering third-party inspections.
#### 9. How can I handle logistics and shipping?
Work with experienced freight forwarders and clarify shipping terms (e.g., FOB, CIF). Ensure proper packaging to prevent damage during transit and plan for potential customs delays.
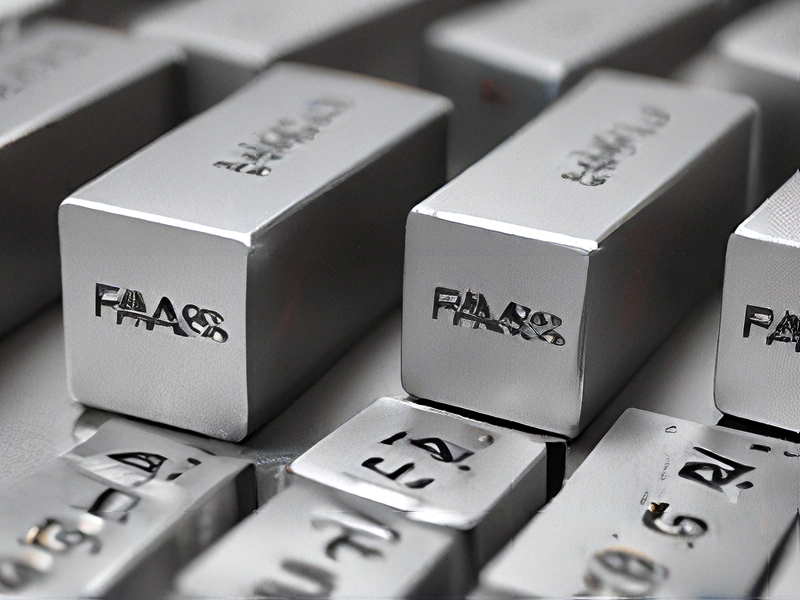