Technology and Applications of laser welder machine
Laser welding technology utilizes focused laser beams to join materials, primarily metals and thermoplastics, with high precision and minimal thermal distortion. This method offers several advantages over traditional welding techniques, including deeper penetration, faster processing speeds, and a narrower heat-affected zone, which reduces the risk of warping or damaging surrounding materials.
The core technology involves generating a concentrated laser beam, which is directed through optics to a specific point on the workpiece. The intense heat from the laser melts the materials at the joint, allowing them to fuse as they cool. Common types of lasers used in welding include CO2 lasers, fiber lasers, and solid-state lasers, each with distinct characteristics suitable for different applications.
Laser welding applications span various industries, including automotive, aerospace, electronics, and medical device manufacturing. For instance, in automotive production, it’s employed for joining components like chassis and body parts, enhancing structural integrity while maintaining lightweight designs. In electronics, laser welding is used for assembling delicate components such as circuit boards and sensors, ensuring high precision without damaging sensitive parts.
Additionally, advancements in laser technology have enabled increased automation, integrating with robotic systems for high-volume production and improved consistency. The adaptability of laser welders allows for various joint designs and materials, making them ideal for both prototype development and large-scale manufacturing.
Overall, laser welding is revolutionizing fabrication processes, offering superior quality, efficiency, and versatility, positioning itself as a leading choice in modern industrial applications.
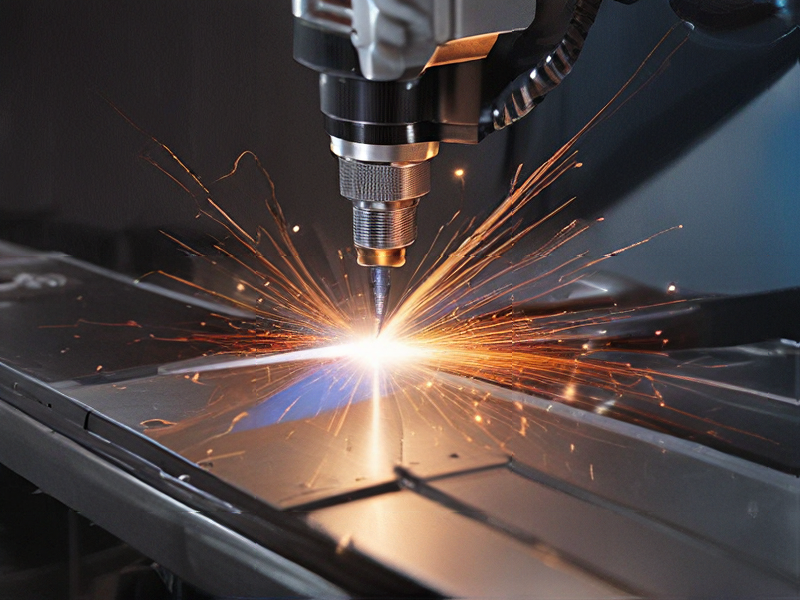
Quality Testing Methods for laser welder machine and how to control quality
Quality testing for laser welding machines is critical to ensure reliable performance and optimal weld quality. Here are some key methods and control techniques:
1. Visual Inspection: Regularly inspect weld seams for surface defects such as cracks, porosity, or incomplete fusion. Visual standards like ISO 5817 can help determine acceptable quality levels.
2. Dimension Verification: Use calipers and gauges to measure weld size and alignments. Ensure that the weld dimensions meet specified tolerances.
3. Non-Destructive Testing (NDT): Employ methods like ultrasonic testing, X-ray, or dye penetrant to detect internal defects without damaging the workpiece. This helps in identifying issues that are not visible on the surface.
4. Pull Testing: Conduct tensile tests to evaluate the strength of the weld. This determines if the weld can withstand operational loads without failure.
5. Hardness Testing: Measure the hardness of the weld zone using Rockwell or Vickers hardness tests. A consistent hardness profile ensures that the material properties are retained post-welding.
6. Welding Parameters Control: Implement software or hardware to monitor laser parameters like power, speed, and focus throughout the process. Maintain records of these parameters to identify trends and anomalies.
7. Process Validation: Periodically validate the welding process by running control samples and comparing them against established criteria or specifications.
8. Regular Maintenance: Perform routine maintenance checks on the laser welder to ensure optimal performance and reduce variability in production.
By incorporating these quality testing methods and controls, manufacturers can maintain high standards of laser welding integrity, ensuring safe and effective operation in various applications.
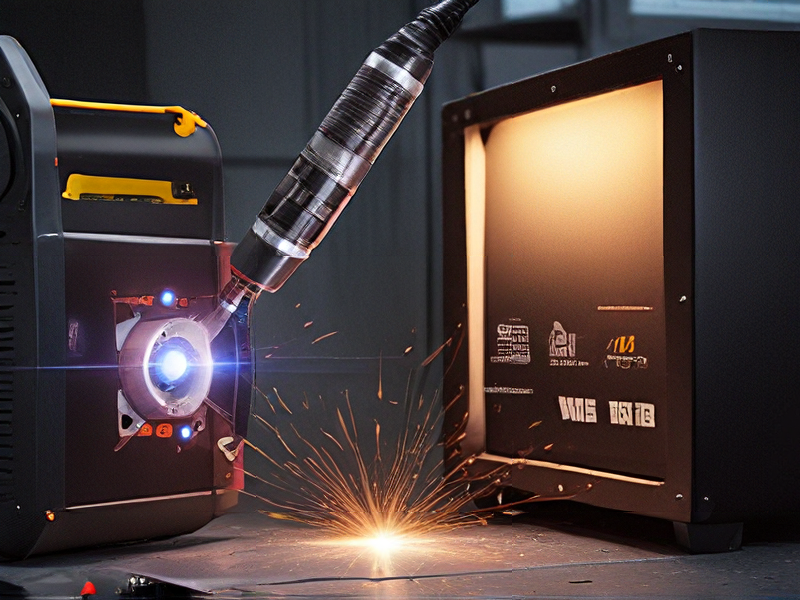
Tips for Procurement and Considerations when Purchasing from laser welder machine
When considering the procurement of a laser welder machine, several critical tips and considerations can guide your purchasing decision:
1. Identify Your Needs: Understand the specific welding requirements for your applications, such as material types, thicknesses, and production volumes. This will help determine the appropriate laser type (e.g., fiber or CO2) and power output.
2. Research Manufacturers: Choose reputable manufacturers known for quality, reliability, and after-sales support. Look for companies with positive customer reviews and strong industry endorsements.
3. Evaluate Technical Specifications: Examine the machine’s hardware, including laser power, beam quality, and pulse duration. Ensure it meets your production needs while offering precision and efficiency.
4. Consider Automation Options: Explore integrated automation systems that can enhance productivity. Automation can reduce labor costs and improve consistency in weld quality.
5. Total Cost of Ownership: Assess not only the initial purchase price but also long-term costs, including maintenance, consumables (e.g., lenses, nozzles), and energy consumption.
6. Training and Support: Inquire about training programs for operators and technical support availability. A knowledgeable support team can reduce downtime and improve machine utilization.
7. Warranty and Service Agreements: Look for comprehensive warranty options and service agreements that offer timely support and maintenance to prevent costly disruptions.
8. Compliance and Safety: Ensure the machine complies with industry standards and safety regulations. Safety features should protect operators and meet regulatory requirements.
By thoroughly evaluating these aspects, you can make a well-informed decision that aligns with your operational goals and budget.
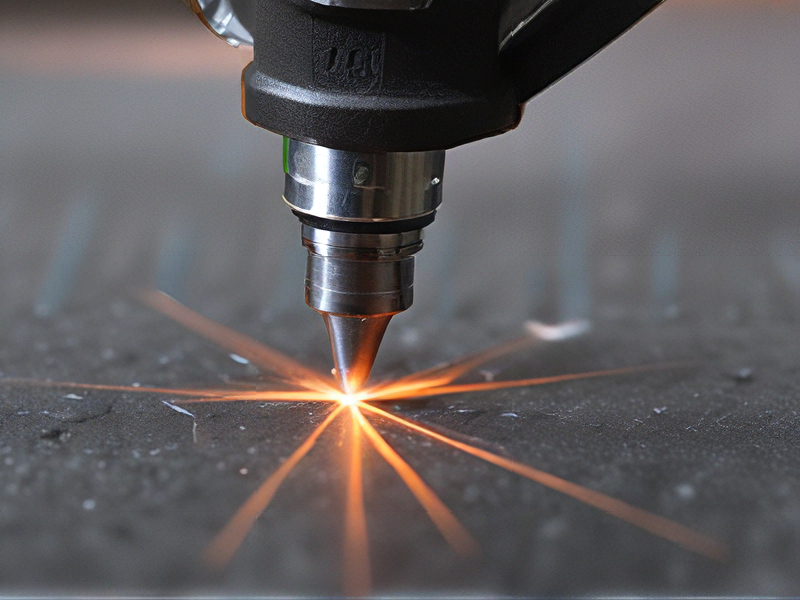
FAQs on Sourcing and Manufacturing from laser welder machine in China
FAQs on Sourcing and Manufacturing Laser Welder Machines from China
1. What should I look for in a laser welder manufacturer in China?
– Prioritize manufacturers with industry certifications (ISO, CE) and a strong reputation. Check their experience, technological capabilities, and customer reviews to ensure reliability and quality.
2. How do I verify a manufacturer’s credibility?
– Request references, visit their facilities if possible, and check third-party reviews or ratings. Consider engaging an inspection service before committing.
3. What is the typical lead time for production?
– Lead times can vary based on order size and complexity but typically range from 4 to 12 weeks. Always confirm timelines in advance.
4. What are the costs involved in sourcing laser welders?
– Costs include manufacturing, shipping, customs duties, and potential tariffs. Get a detailed quote that outlines all expenses to avoid surprises.
5. Can I customize laser welding machines?
– Most manufacturers offer customization options. Define your requirements clearly, such as power and functionality, during initial discussions.
6. What are my shipping options?
– Common shipping methods include sea freight, air freight, and express courier services. The choice depends on budget, urgency, and volume.
7. How do I handle after-sales support?
– Confirm that the manufacturer provides after-sales services, including training, spare parts availability, and remote support.
8. What payment methods are accepted?
– Payment terms may vary. Common methods include T/T (bank transfer), L/C (letter of credit), and PayPal. Ensure clarity on payment structure before proceeding.
9. Are there language barriers to consider?
– English is commonly spoken in Chinese manufacturing sectors, but ensure you have a reliable point of contact who understands your requirements clearly.
By addressing these FAQs, you can navigate the sourcing process more effectively and establish a successful partnership in China.
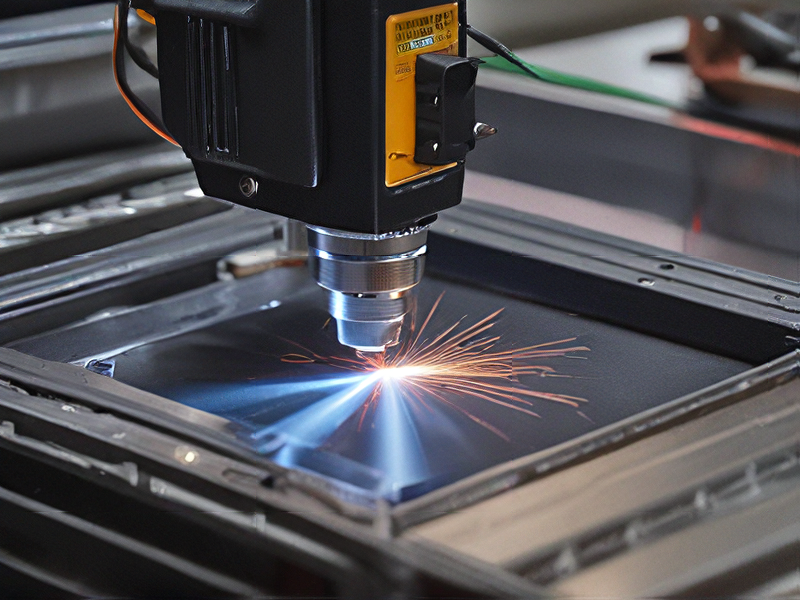