Technology and Applications of lathe machining
Lathe machining is a fundamental manufacturing process that involves rotating a workpiece against a cutting tool to shape it into desired forms. This method is widely used for creating cylindrical, conical, or flat surfaces and is essential in various industries like automotive, aerospace, and manufacturing.
Technology: Modern lathes are equipped with Computer Numerical Control (CNC) technology, enabling precise automation and complex shaping without manual intervention. CNC lathes offer superior accuracy, repeatability, and speed, allowing for intricate designs and tighter tolerances. Additionally, advancements in materials, such as carbide and ceramic cutting tools, have improved the durability and efficiency of lathe operations. Programmable software facilitates quick changes in design, reducing production time and minimizing waste.
Applications: Lathe machining serves diverse applications including:
1. Parts Manufacturing: Producing shafts, rods, and bushings with specific dimensions for machinery.
2. Automotive Components: Machining engine parts, gears, and axle shafts for vehicles.
3. Aerospace Industry: Creating complex components for aircraft and spacecraft, where precision and material integrity are critical.
4. Medical Devices: Manufacturing surgical instruments and implants that require high precision.
5. Woodturning: Crafting furniture and artistic items, where ornamental shapes are required.
In summary, lathe machining remains a vital technology with extensive applications across various sectors, driven by advancements in CNC technology and materials that enhance its capabilities and precision. Its combination of versatility and efficiency ensures its continued relevance in modern manufacturing.
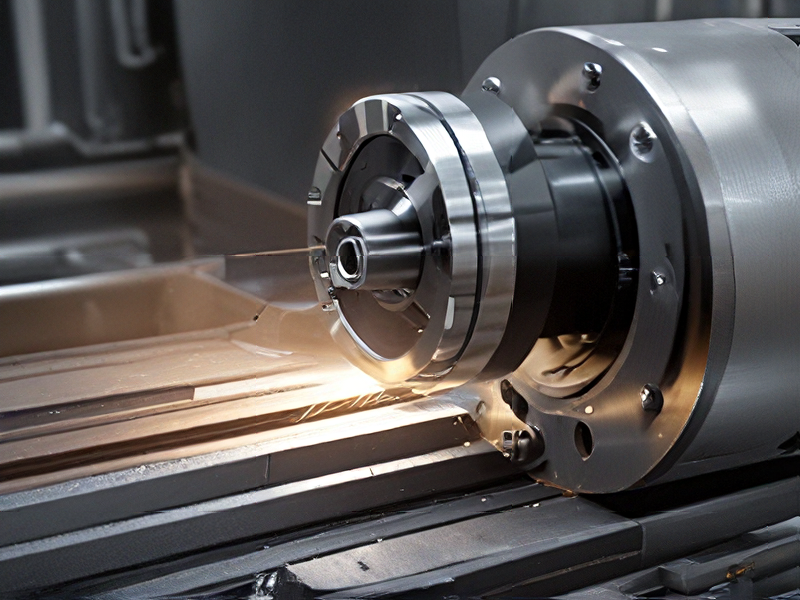
Quality Testing Methods for lathe machining and how to control quality
Quality testing in lathe machining is crucial to ensure precision and reliability. Here are some effective methods and controls:
1. Dimension Inspection: Utilize calipers and micrometers to measure critical dimensions against specified tolerances. Regular calibration of these tools is essential to maintain accuracy.
2. Surface Finish Evaluation: Apply techniques like visual inspection, roughness measurement tools (e.g., profilometers), or comparator charts to assess the surface quality. A consistent surface finish reduces friction and wear in applications.
3. Runout Measurement: Use dial indicators to check the runout on machined components. This ensures that the rotational accuracy of the lathe is maintained, which is critical for parts that must fit seamlessly in assemblies.
4. Material Testing: Perform material verification tests such as hardness tests (e.g., Rockwell or Brinell) and chemical composition analysis to confirm that the right materials are used.
5. Functional Testing: After machining, test the part’s functionality in its intended application. This might involve assembling with other components to verify fit and function.
Quality Control Techniques:
– Statistical Process Control (SPC): Implement SPC to monitor production processes through control charts, helping to identify trends or deviations in machining performance in real-time.
– Lean Manufacturing Principles: Adopt lean methodologies to eliminate waste and improve process efficiency. Regular training for operators on quality awareness and procedures can enhance results.
– Documented Procedures: Establish and maintain standard operating procedures (SOPs) for lathe operations, ensuring consistency in machining processes.
Incorporating these quality testing methods and controls within the lathe machining process will significantly improve overall product quality and reliability.
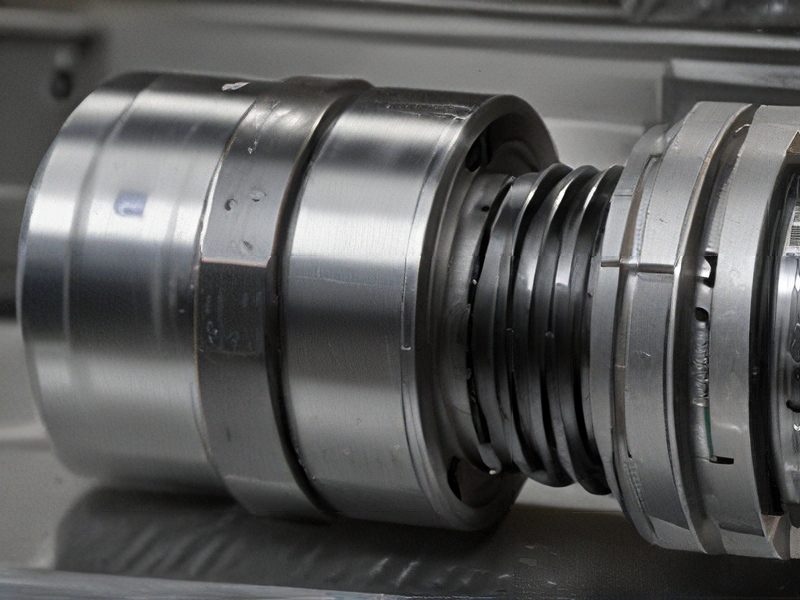
Tips for Procurement and Considerations when Purchasing from lathe machining
When considering procurement for lathe machining services, several key tips and factors should guide your purchasing decision:
1. Define Specifications: Clearly outline your project requirements, including dimensions, tolerances, materials, and intended use. This ensures that suppliers understand your needs.
2. Supplier Selection: Research potential suppliers thoroughly. Look for companies with experience in your industry, positive customer reviews, and proven quality management systems.
3. Certifications and Standards: Ensure the supplier adheres to relevant industry standards (e.g., ISO 9001). Certifications indicate a commitment to quality and reliability.
4. Capabilities Assessment: Evaluate the supplier’s machinery and technology capabilities. Ensure they have modern, well-maintained equipment suitable for your project’s specifications.
5. Lead Times and Capacity: Inquire about production lead times and the supplier’s capacity to handle your orders, especially during peak times. Reliable timelines are crucial for project planning.
6. Pricing Structure: Understand the pricing model—ask for detailed quotations, including any setup, labor, and material costs. Be wary of significantly low prices, which may compromise quality.
7. Quality Control Processes: Investigate the quality assurance measures in place, such as inspection methods and testing protocols. A robust quality control process is essential to avoid defects.
8. Communication Excellence: Establish clear communication channels with the supplier. Good communication can prevent misunderstandings and delays.
9. Post-Purchase Support: Consider the supplier’s willingness to provide support post-purchase, including handling defects or providing maintenance information.
10. Long-term Relationships: Consider building long-term partnerships with trusted suppliers to ensure continuity and a deeper understanding of your evolving needs.
By focusing on these aspects, you can make informed decisions that enhance your procurement process in lathe machining projects.
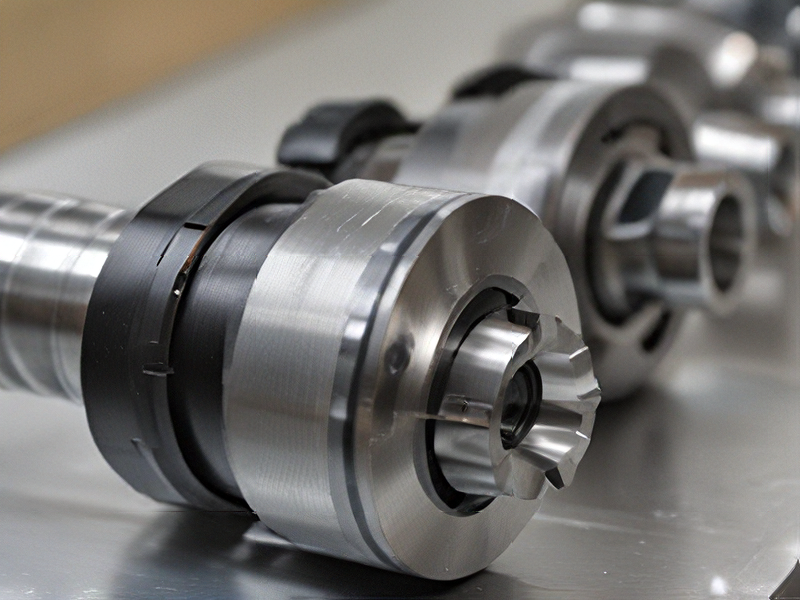
FAQs on Sourcing and Manufacturing from lathe machining in China
FAQs on Sourcing and Manufacturing Lathe Machining in China
1. What is lathe machining?
Lathe machining is a manufacturing process that involves removing material from a workpiece using a rotating cut tool. This process is commonly used for creating cylindrical parts with precision.
2. Why source lathe machining from China?
China offers competitive pricing, advanced manufacturing technologies, and a vast network of skilled labor. Many Chinese manufacturers have experience in producing high-quality machined parts.
3. How do I find a reliable manufacturer in China?
Research potential suppliers using platforms like Alibaba or Global Sources. Check their credentials, certifications, and customer reviews. Conduct factory audits if possible.
4. What are common materials used in lathe machining?
Common materials include aluminum, stainless steel, brass, and plastics. The choice of material depends on the end-use and specific requirements of your project.
5. What are the typical lead times?
Lead times can vary based on order complexity and volume. Generally, expect 2-6 weeks for production, plus additional time for shipping.
6. What quality control measures should I consider?
Request sample parts before full production. Ensure manufacturers follow quality standards like ISO 9001. Regular inspections during manufacturing can help maintain quality.
7. How do I handle shipping and logistics?
Coordinate with your supplier to understand the shipping options. Consider using freight forwarders to manage customs and delivery efficiently.
8. What should I be aware of regarding intellectual property (IP)?
Ensure that you have non-disclosure agreements (NDAs) in place and consider trademark registration for your products to protect your IP.
9. Can I get custom designs?
Yes, most manufacturers can work with your designs. Provide detailed specifications and CAD drawings for accurate production.
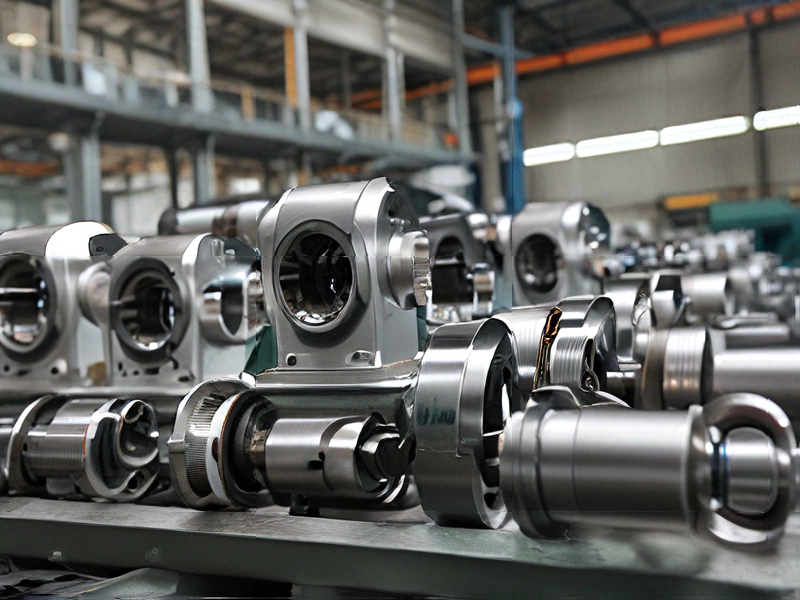