Technology and Applications of m-codes in cnc
In CNC (Computer Numerical Control) machining, M-codes are machine control codes that initiate specific actions or functions on the machine tool. These codes are crucial for automating operations, ensuring precision, and enhancing efficiency in manufacturing processes.
M-codes serve various purposes, including:
1. Tool Changes: M-codes manage tool changes, allowing the machine to automatically swap tools during machining processes. This reduces downtime and improves workflow continuity.
2. Coolant Control: They activate or deactivate coolant systems based on operational requirements, ensuring proper temperature management and lubrication during cutting.
3. Spindle Control: M-codes govern spindle operations such as start, stop, speed, and direction changes. This functionality is essential for adjusting cutting speeds and optimizing machining parameters.
4. Program Stops and Starts: They enable pausing (stop) and resuming (start) of CNC programs, facilitating manual interventions, inspections, or adjustments during machining.
5. Auxiliary Functions: M-codes can trigger auxiliary equipment such as part probes, pallet changers, or conveyor systems, streamlining automated manufacturing processes.
Applications of M-codes extend across various CNC machining operations, including milling, turning, drilling, and grinding. Each machine tool and CNC system may have specific M-codes tailored to its capabilities and manufacturer specifications.
In summary, M-codes play a pivotal role in CNC technology by providing precise control over machine functions, enhancing operational efficiency, and supporting advanced manufacturing capabilities. Understanding and utilizing M-codes effectively are essential for optimizing CNC processes and achieving high-quality production outputs.
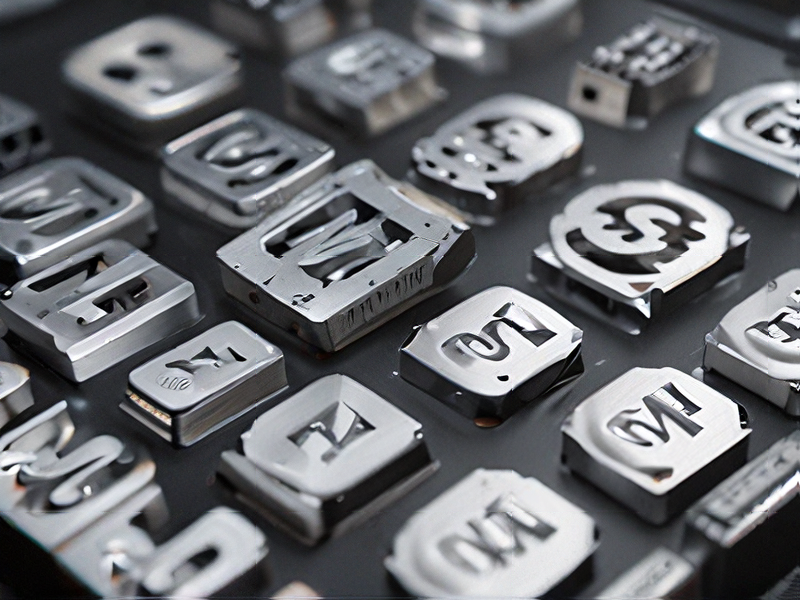
Quality Testing Methods for m-codes in cnc and how to control quality
Quality testing methods for M-codes in CNC (Computer Numerical Control) machines involve rigorous procedures to ensure accurate operation and reliability:
1. Simulation Testing: Use CNC simulation software to validate M-code sequences virtually before executing them on actual machines. This helps in detecting errors and optimizing performance.
2. Dry Run Testing: Conduct a dry run of the program without cutting material to verify tool paths, speeds, feeds, and M-code functionality. This minimizes the risk of machine damage.
3. Code Review: Thoroughly review M-code sequences for syntax errors, logical inconsistencies, and adherence to machine-specific requirements. Automated code analyzers can assist in this process.
4. Tool Calibration: Regularly calibrate tools and measuring instruments to ensure accurate machining dimensions as specified by the M-codes.
5. Error Handling: Implement error handling routines within the CNC program to manage unexpected conditions gracefully, such as tool breakage or material shortage.
To control quality effectively:
– Training and Certification: Ensure operators are trained in CNC programming and M-code usage. Certification programs validate competency.
– Documentation: Maintain comprehensive documentation of CNC programs, revisions, and test results to track changes and ensure traceability.
– Process Audits: Conduct regular audits to verify adherence to quality standards and identify areas for improvement.
– Feedback Loop: Establish a feedback loop where operators provide insights on program performance and suggest optimizations.
By employing these methods and controls, manufacturers can enhance the reliability and efficiency of CNC operations while minimizing risks associated with M-code errors.
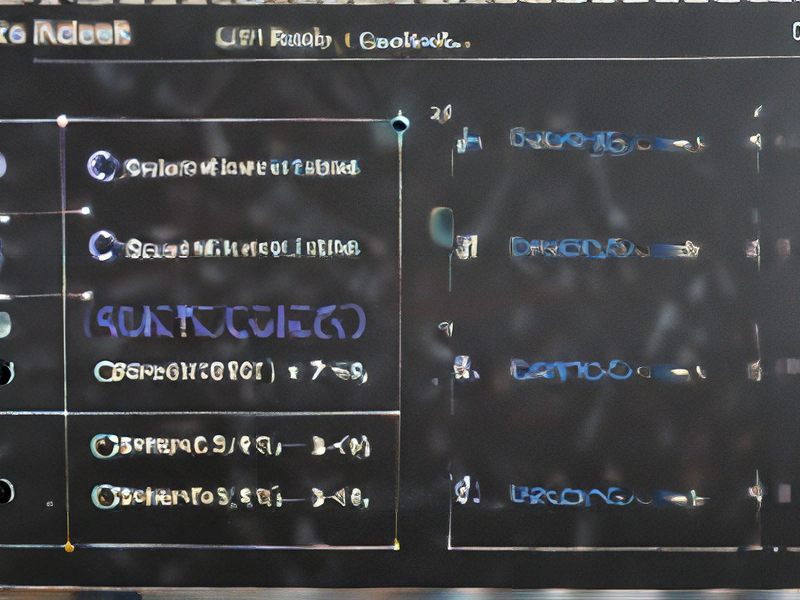
Tips for Procurement and Considerations when Purchasing from m-codes in cnc
Tips for Procurement and Considerations when Purchasing M-Codes in CNC
1. Understand M-Codes: M-codes are machine codes used in CNC programming to control various machine functions. Familiarize yourself with the specific M-codes required for your operations to ensure you procure the correct codes.
2. Identify Requirements: Determine the specific requirements of your CNC machines and operations. Different machines and tasks may require different M-codes. Make a comprehensive list of all necessary codes.
3. Quality and Compatibility: Ensure that the M-codes you purchase are of high quality and compatible with your CNC machines. Check for compatibility with your machine’s make and model to avoid operational issues.
4. Vendor Selection: Choose reputable vendors with a track record of supplying reliable M-codes. Research potential vendors, read reviews, and check references to ensure they can meet your needs.
5. Cost Considerations: Compare prices from different vendors, but avoid compromising on quality for lower costs. Consider the total cost of ownership, including potential downtime due to incompatible or faulty codes.
6. Technical Support: Opt for vendors that offer robust technical support. In case of issues or questions, having access to knowledgeable support staff can save time and prevent production delays.
7. Training and Documentation: Ensure that the M-codes come with adequate documentation and training materials. Proper understanding and usage of M-codes are crucial for efficient CNC operations.
8. Compliance and Standards: Check that the M-codes comply with industry standards and regulations. Using standard-compliant codes ensures safety and interoperability.
9. Testing and Validation: Before full-scale implementation, test the M-codes in a controlled environment. Validate their performance and ensure they work seamlessly with your CNC machines.
10. Maintenance and Updates: Establish a plan for regular maintenance and updates of M-codes. Stay informed about new versions or patches that may enhance functionality or security.
By following these tips and considerations, you can ensure a smooth procurement process and optimal performance of your CNC operations.
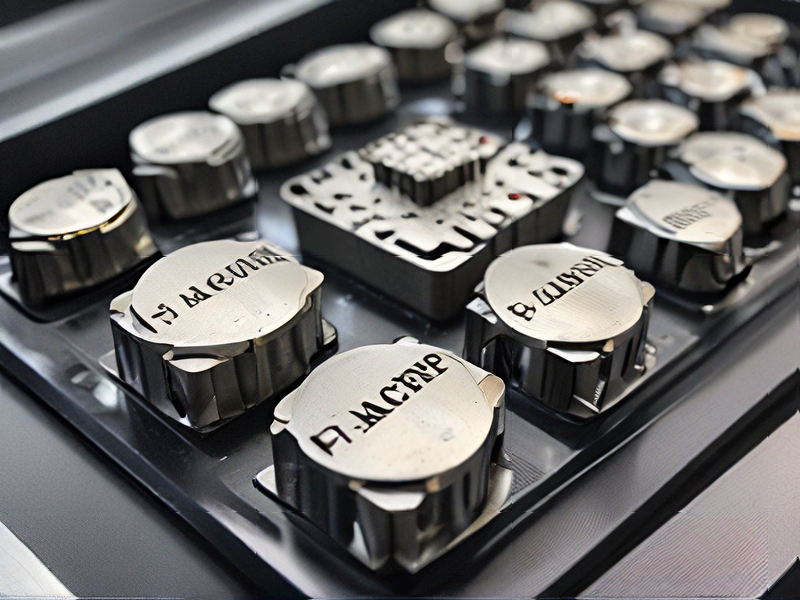
FAQs on Sourcing and Manufacturing from m-codes in cnc in China
FAQs on Sourcing and Manufacturing from M-Codes in CNC in China
1. What are M-Codes in CNC machining?
M-Codes are machine codes that control various functions in CNC (Computer Numerical Control) machining. These codes manage machine operations like coolant control, tool changes, and program stops, distinct from G-Codes, which dictate movement and cutting paths.
2. Why should I source CNC machining from China?
China offers competitive pricing, high-quality manufacturing, and a vast network of suppliers. The country has advanced technology, skilled labor, and extensive experience in CNC machining, making it a cost-effective and reliable option.
3. How do I ensure quality when sourcing from China?
To ensure quality, work with reputable suppliers and consider third-party inspections. Establish clear specifications, request samples, and conduct factory audits. Using platforms like Alibaba and Made-in-China can help identify reliable suppliers.
4. What is the typical lead time for CNC parts from China?
Lead times vary depending on the complexity and quantity of the parts. Generally, production can take 2-4 weeks, with additional time for shipping. Custom orders might require more time for design verification and prototyping.
5. How are intellectual property rights protected when manufacturing in China?
Protect your intellectual property by working with trusted suppliers and using contracts that include non-disclosure agreements (NDAs) and non-compete clauses. Registering patents and trademarks in China provides additional legal protection.
6. What are the common payment terms for CNC machining orders in China?
Common payment terms include 30% upfront and 70% upon completion or before shipping. Letters of credit (L/C) and Trade Assurance (on platforms like Alibaba) are also used to secure transactions.
7. How can I handle logistics and shipping from China?
Logistics can be managed through freight forwarders who handle shipping, customs clearance, and delivery. Options include sea freight for bulk orders and air freight for smaller, urgent shipments.
8. Are there any language barriers when dealing with Chinese suppliers?
Language barriers can exist, but many suppliers have English-speaking staff. Clear, concise communication and visual aids (like drawings and specifications) can mitigate misunderstandings.
By addressing these common concerns, businesses can effectively source and manufacture CNC parts in China, leveraging the country’s strengths in the global supply chain.
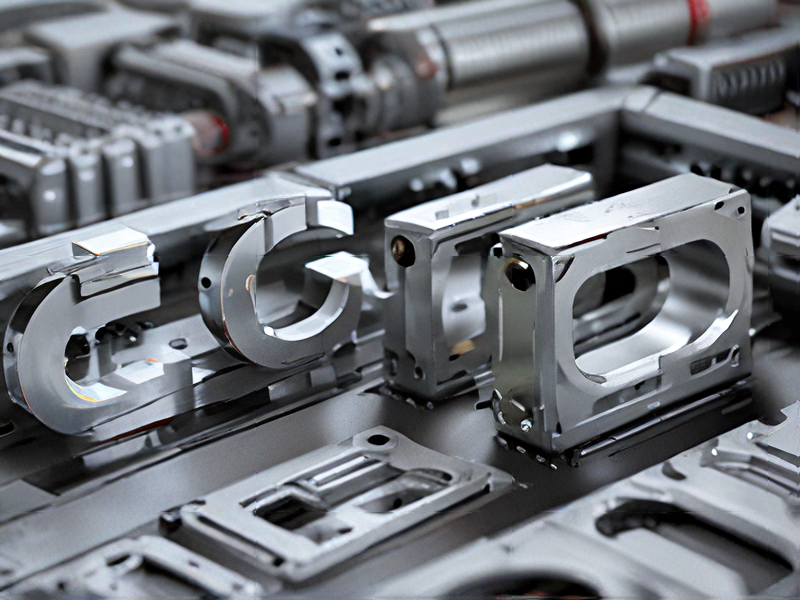