Technology and Applications of machine cnc
Computer Numerical Control (CNC) technology revolutionizes manufacturing by automating machine tools through computer programming. CNC machines can operate lathes, mills, routers, and grinders with high precision, enabling complex parts to be produced consistently and efficiently.
The CNC process begins with a Computer-Aided Design (CAD) model, which is converted into a format readable by the CNC machine via Computer-Aided Manufacturing (CAM) software. This programming guides the machine’s movements along multiple axes, typically ranging from three to five, allowing for intricate designs and tight tolerances.
CNC technology finds applications across various industries. In aerospace, it is used to manufacture components with stringent weight and precision requirements. The automotive industry employs CNC machines for producing engine parts and body components, ensuring performance and safety standards. Additionally, the medical sector utilizes CNC technology for intricate surgical tools and implants, where exact specifications are crucial.
The advantages of CNC technology include increased productivity, enhanced precision, reduced human error, and the ability to produce repetitive tasks without fatigue. Furthermore, modern CNC machines can be programmed for rapid prototyping, allowing for faster iterations in product development.
In summary, CNC technology represents a significant advancement in manufacturing, leveraging computer programming to enhance precision, efficiency, and versatility across various industries. Its applications continue to expand, paving the way for innovations in design and production processes.
Quality Testing Methods for machine cnc and how to control quality
Quality testing methods for CNC (Computer Numerical Control) machining are essential to ensure precision and reliability in manufacturing. Here are some effective methods and practices to control quality:
1. Visual Inspection: Regular visual checks can identify surface defects, dimensional inconsistencies, or signs of wear in tools. Operators should be trained to recognize common issues promptly.
2. Measurement Tools: Utilize calibrated tools such as calipers, micrometers, and gauges to measure critical dimensions. Automated measurement systems, like CMM (Coordinate Measuring Machines), can provide higher accuracy and efficiency.
3. First Article Inspection (FAI): Conduct a thorough inspection of the first completed part against design specifications. This ensures that the CNC program produces parts within tolerance limits before regular production begins.
4. Statistical Process Control (SPC): Collect data throughout the production process to monitor performance. Control charts can help identify variations and trends, enabling proactive adjustments.
5. Tool Condition Monitoring: Implement systems to monitor tool wear and performance in real-time. Predictive maintenance can be scheduled to reduce downtime and enhance quality.
6. Material Verification: Ensure the use of certified materials that meet the specified standards. Regular testing, such as hardness tests or chemical composition analysis, can help maintain material integrity.
7. Process Audits: Regularly audit the CNC processes and operators to ensure adherence to quality protocols. Training and certification of operators play a crucial role in maintaining quality standards.
8. Feedback Loop: Create a feedback mechanism for continuous improvement. Documenting and analyzing defects allows for corrective actions and process enhancements.
By integrating these methods, manufacturers can effectively control quality, reduce waste, and ensure that CNC machined parts meet the required specifications.
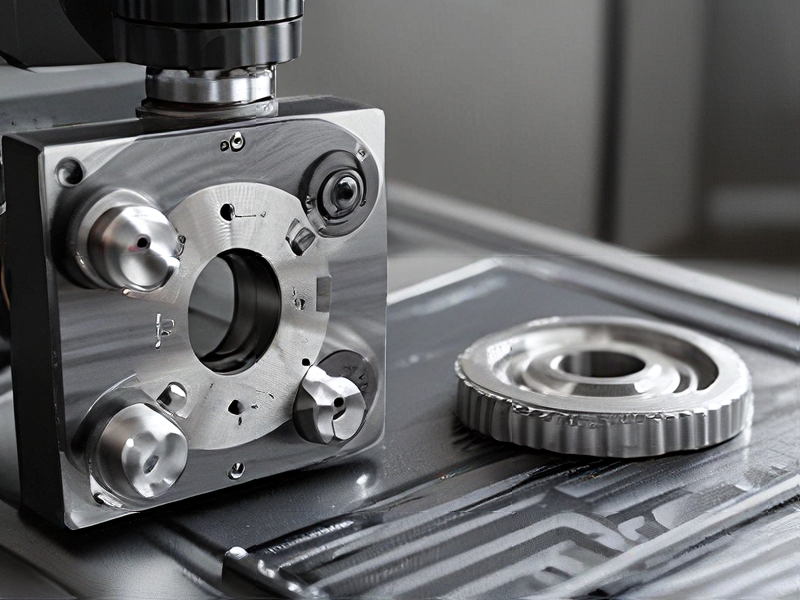
Tips for Procurement and Considerations when Purchasing from machine cnc
When procuring CNC machines, several key considerations ensure you make a sound investment.
1. Define Requirements: Identify your specific machining needs, including materials, dimensions, precision, and complexity of the projects. Different CNC machines are tailored for various tasks, so clarity in your requirements is essential.
2. Budget: Establish a clear budget that includes not just the machine cost but also installation, training, maintenance, and potential upgrades. Factor in operational costs and ROI expectations.
3. Supplier Research: Investigate potential suppliers carefully. Look for established manufacturers with good reputations, positive customer reviews, and dedicated customer service. Verify their support and warranty policies.
4. Technology and Features: Evaluate the technology of the CNC machine. Look for advanced features such as automation, software compatibility, and user-friendly interfaces that can improve efficiency and reduce downtime.
5. Maintenance and Support: Consider the availability of maintenance services, spare parts, and technical support. Machines with reliable support can minimize operational disruptions.
6. Training: Check if the supplier offers training programs for your staff. Proper training ensures optimal use of the machine and extends its lifespan.
7. Consider Resale Value: Some CNC machines maintain their value better than others. Understanding the depreciation trends can help in future planning.
8. Flexibility and Scalability: Choose a CNC machine that can adapt to evolving manufacturing needs or different materials, offering long-term value.
9. Inspect Before Purchase: Whenever possible, visit the supplier’s facility to see the machine in action and assess its build quality and functionality.
By considering these factors, you can make a more informed decision, ensuring that your CNC machine purchase meets both current and future operational needs.
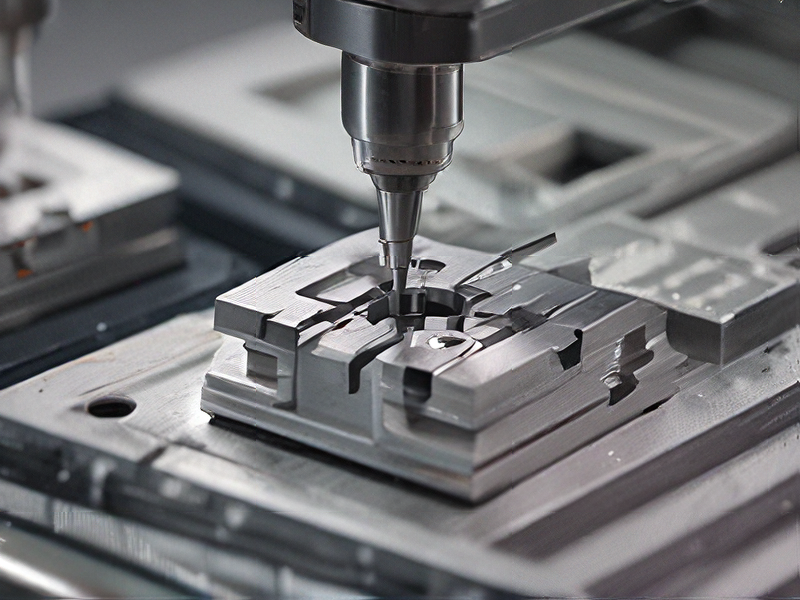
FAQs on Sourcing and Manufacturing from machine cnc in China
FAQs on Sourcing and Manufacturing CNC Machines in China
1. What types of CNC machines can I source in China?
China offers a wide range of CNC machines, including CNC mills, lathes, routers, plasma cutters, and laser cutters, suitable for various applications.
2. How do I find a reliable CNC manufacturer in China?
To find a reliable manufacturer, consider platforms like Alibaba or Made-in-China. Check their reviews, certifications, and past work. Visiting factories or sourcing agents can also help.
3. What are the typical lead times for CNC machining?
Lead times can vary but generally range from 4 to 12 weeks, depending on the complexity of the design, order quantity, and manufacturer capabilities.
4. What should I know about Quality Control?
Quality control is crucial. Specify quality standards in your contract and consider hiring third-party inspection services to ensure products meet your requirements.
5. What payment methods are commonly used?
Common payment methods include wire transfers, PayPal, or Alibaba Trade Assurance. It’s advisable to use secure payment methods to protect your investment.
6. Are there language barriers?
Language barriers can exist, but many manufacturers employ English-speaking staff. Clear communication through written specifications can help mitigate misunderstandings.
7. What are the shipping options?
Shipping options include air freight for faster delivery or sea freight for cost-effective bulk shipments. Ensure you discuss logistics with your supplier.
8. What are the import duties and regulations?
Import duties vary by country and product type. Research local regulations to ensure compliance, and consult with customs brokers if necessary.
9. Can I get custom designs?
Yes, many manufacturers offer custom CNC machining based on your designs. Provide detailed CAD drawings and specifications for accurate results.
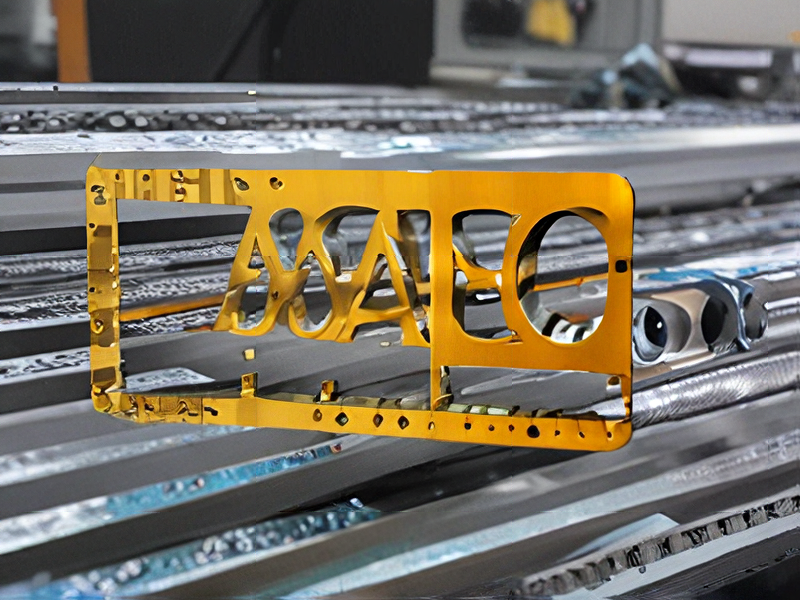