Technology and Applications of machine for grinding
Machine grinding encompasses a variety of technologies used to shape and refine surfaces by removing material. This process is crucial in various industries for achieving precise dimensions, smooth finishes, and improved material properties.
Common machine grinding applications include:
* Precision Manufacturing: Grinding is essential for creating highly accurate components in industries like aerospace, automotive, and electronics.
* Toolmaking: Cutting tools, dies, and molds require precise grinding to maintain sharpness and dimensional accuracy.
* Surface Finishing: Grinding removes imperfections and achieves desired surface textures, enhancing the aesthetics and functionality of products.
Machine grinding technologies utilize different types of grinding wheels and methods, such as:
* Centerless Grinding: Grinds cylindrical parts without the need for centers, suitable for high-volume production.
* Surface Grinding: Creates flat and parallel surfaces on workpieces.
* Internal Grinding: Grinds bores and holes to precise dimensions.
Advances in machine grinding include incorporating automation, sensors, and computer numerical control (CNC) for increased precision, efficiency, and repeatability.
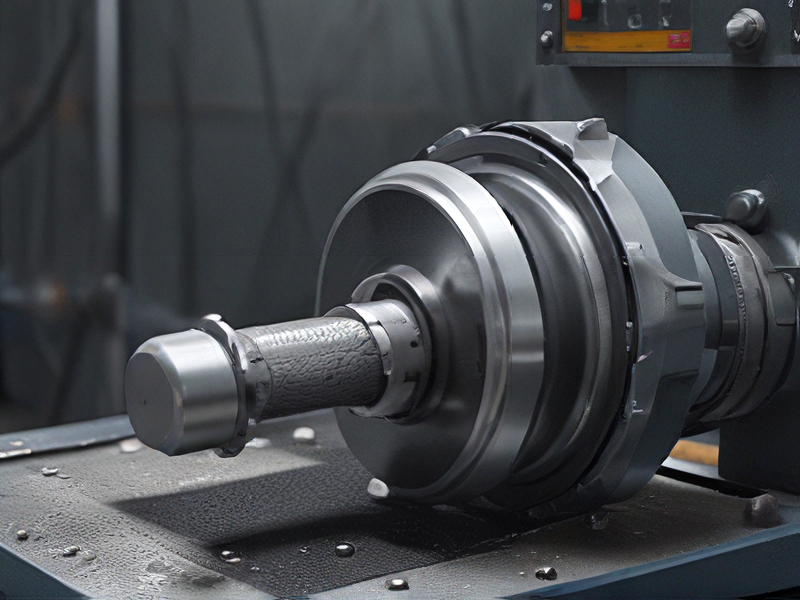
Quality Testing Methods for machine for grinding and how to control quality
Quality testing methods for grinding machines focus on ensuring precision, surface finish, and dimensional accuracy.
Here’s a breakdown:
1. Dimensional Inspection:
– Calipers: Measure workpiece dimensions like diameter, length, and thickness.
– Micrometers: Precisely measure small distances and features.
– Coordinate Measuring Machines (CMMs): Automated systems for comprehensive 3D dimensional analysis.
2. Surface Finish Evaluation:
– Surface Roughness Meter (Profilometer): Measures surface texture irregularities (Ra, Rz values).
– Optical Comparators: Visualize surface defects and deviations from ideal profiles.
– Laser Scanning: Creates detailed 3D maps of surface topography.
3. Functional Testing:
– Run-out Tests: Evaluate the concentricity of rotating components.
– Grinding Wheel Life Tests: Assess wheel wear and performance under specific conditions.
– Process Simulation: Use software to predict grinding performance and identify potential issues.
Quality Control Measures:
– Regular calibration of measurement equipment.
– Strict adherence to grinding parameters (feed rate, speed, depth of cut).
– Monitoring wheel wear and replacing it when necessary.
– Utilizing feedback control systems to adjust grinding parameters in real-time.
– Statistical Process Control (SPC): Tracking and analyzing process data to identify variations and trends.
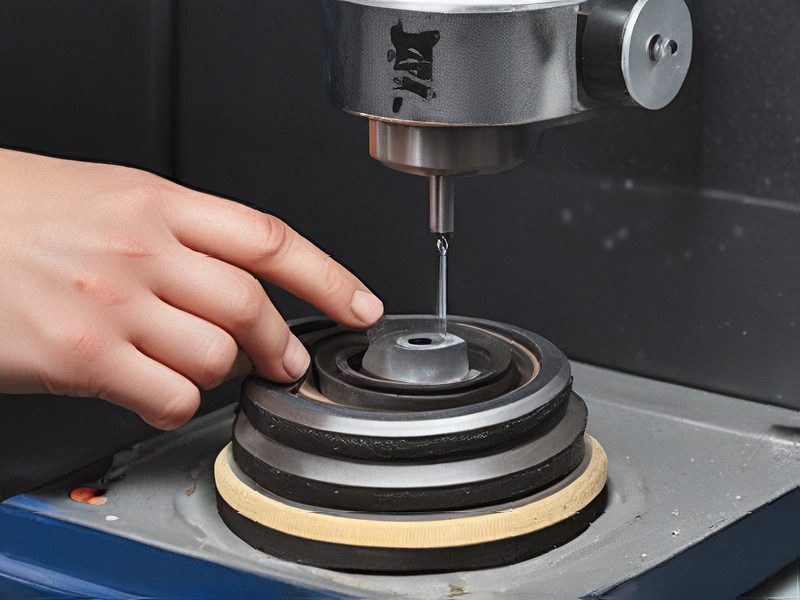
Tips for Procurement and Considerations when Purchasing from machine for grinding
Here are some tips for procuring and considering machine grinding purchase:
Application:
* Define your needs: What materials will you grind? What size and shape of pieces? Required accuracy and surface finish? This determines the type of grinder (surface, cylindrical, centerless, etc.).
Machine Specs:
* Grinding wheel: Diameter, width, grit size, material type – crucial for material removal rate, surface finish, and wheel life.
* Spindle Speed: Affects material removal and surface quality.
* Feed Rate: Influences material removal and surface finish.
* Worktable Size: Must accommodate your workpiece size.
* Power: Depends on material hardness and required removal rate.
* Automation: Consider semi-automated or fully automated options for efficiency.
Vendor:
* Reputation: Research the vendor’s experience, reliability, and customer support.
* Service: Ensure prompt after-sales support, maintenance, and spare parts availability.
* Training: Look for comprehensive operator training programs.
Budget:
* Initial Cost: Factor in machine price, accessories, and installation.
* Operating Cost: Consider wheel costs, power consumption, and maintenance expenses.
Other:
* Safety Features: Prioritize machines with robust safety mechanisms.
* Ergonomics: Ensure operator comfort and minimize strain.
* Environmental Impact: Choose energy-efficient models and consider noise levels.
Remember, investing in a quality grinder that meets your specific needs will ensure efficient and reliable operation for years to come.
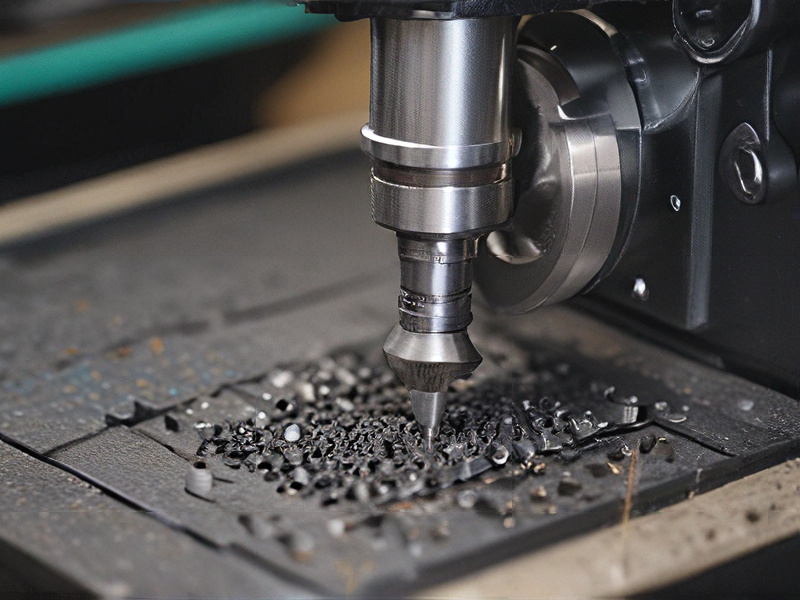
FAQs on Sourcing and Manufacturing from machine for grinding in China
Sourcing and manufacturing grinding machines in China can be a cost-effective solution for businesses. Here’s a breakdown of key aspects:
Sourcing:
* Online Platforms: Alibaba, Global Sources, and Made-in-China are excellent starting points to find Chinese grinding machine manufacturers and suppliers.
* Trade Shows: Attending industry-specific trade shows in China offers opportunities to meet manufacturers face-to-face and explore their offerings.
* Industry Associations: Connecting with relevant industry associations can provide valuable leads and insights.
Manufacturing:
* OEM (Original Equipment Manufacturing): Many Chinese manufacturers offer OEM services, customizing grinding machines to meet specific requirements.
* Quality Control: Establish stringent quality control measures throughout the manufacturing process. Consider on-site inspections or third-party quality audits.
* Logistics: Plan for efficient logistics and shipping arrangements to ensure timely delivery.
Key Considerations:
* Machine Type: Identify the specific type of grinding machine required (e.g., surface grinder, internal grinder, cylindrical grinder).
* Technical Specifications: Define precise technical specifications based on desired precision, capacity, and other requirements.
* Communication: Ensure clear and effective communication with manufacturers throughout the process.
By carefully considering these factors, businesses can successfully source and manufacture grinding machines in China.
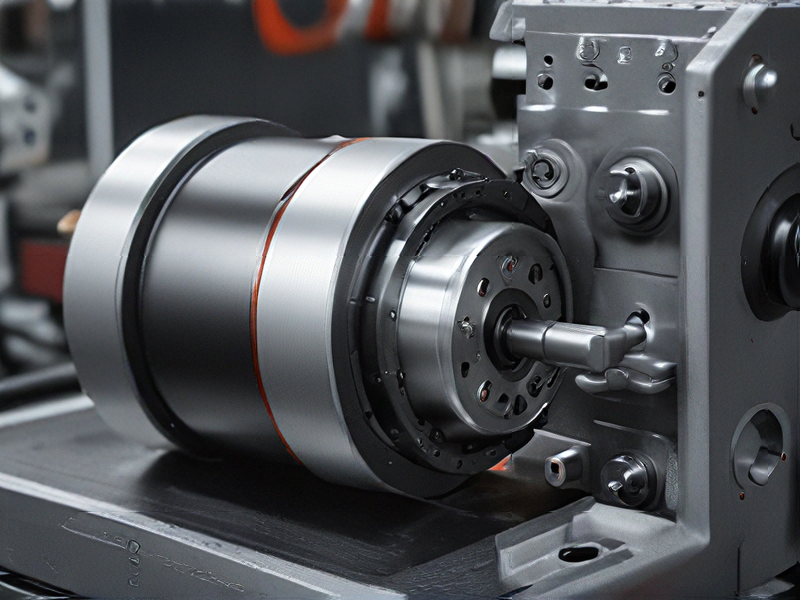