Technology and Applications of machine milling
Machine milling is a manufacturing process that involves the removal of material from a workpiece using rotary cutters. This subtractive machining technique is widely used in various industries due to its precision and versatility.
Technology
1. Types of Milling Machines:
– Vertical Milling Machines: The spindle axis is vertical, ideal for small-scale production.
– Horizontal Milling Machines: The spindle is horizontal, suitable for larger workpieces and heavy-duty tasks.
– CNC Milling Machines: Computer Numerical Control (CNC) milling allows for automated, precise cuts and complex geometries, enhancing production efficiency.
2. Cutting Tools: Various tools, such as end mills, face mills, and slab mills, cater to different milling operations. Tool selection depends on the material and desired finish.
3. Materials: Milling can work with metals (steel, aluminum), plastics, wood, and composite materials, making it applicable across diverse sectors.
Applications
1. Manufacturing Components: Used for creating complex components in automotive, aerospace, and electronics.
2. Prototyping: Rapid prototyping applications allow engineers to test designs before full-scale production.
3. Custom Fabrication: One-off or small batch productions benefit from milling’s adaptability to create tailored parts.
4. Surface Finishing: Milling techniques improve surface finish and dimensional accuracy, vital for high-tolerance applications.
5. Tool and Die Making: Reserved for crafting molds and dies used in mass production processes.
Machine milling remains a cornerstone of modern manufacturing, delivering high precision, versatility, and efficiency in producing a wide range of components and products. As technology advances, including the integration of AI and IoT, the capabilities and applications of milling will continue to expand.
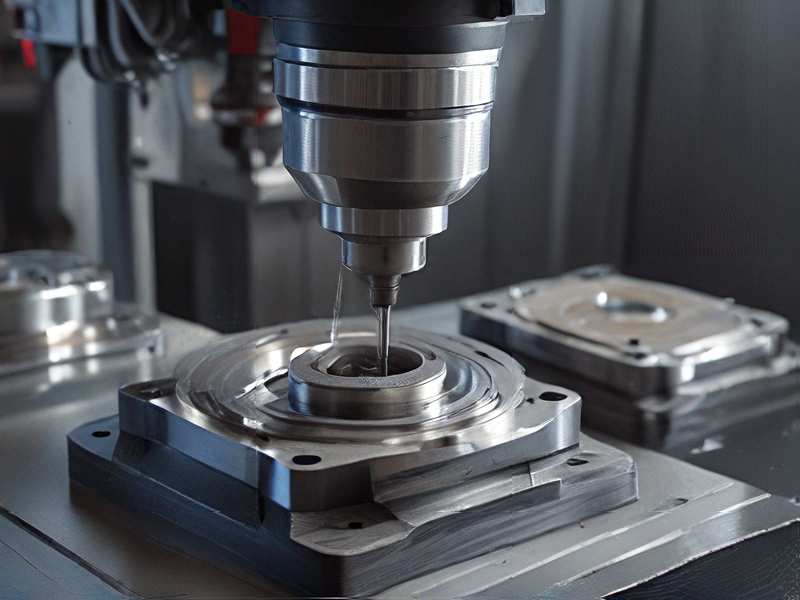
Quality Testing Methods for machine milling and how to control quality
Quality testing methods for machining milling are critical to ensure precision, consistency, and reliability in the final product. Here are several effective methods and controls:
1. Dimensional Inspection: Use calipers, micrometers, and coordinate measuring machines (CMM) to check critical dimensions against specifications. Regularly calibrate measuring tools to maintain accuracy.
2. Surface Finish Measurement: Evaluate surface quality using surface roughness testers. Specify acceptable roughness profiles to ensure surfaces meet functional requirements.
3. Visual Inspection: Conduct thorough visual inspections for defects such as burrs, cracks, or tool marks. Employ magnifying tools for enhanced inspection, especially in complex geometries.
4. Material Verification: Confirm that the correct material is being used by utilizing material testing methods, such as spectroscopy or hardness testing, to ensure compliance with specifications.
5. Tool Condition Monitoring: Regularly inspect milling tools for wear and damage. Implement sensors to monitor tool performance and replace tools before they reach unacceptable wear levels.
6. Process Control: Utilize Statistical Process Control (SPC) to monitor key parameters during machining. Collect data on cutting speeds, feeds, and temperatures to identify trends that may affect quality.
7. First Article Inspection (FAI): Perform a comprehensive inspection of the first produced item from a new batch or setup. Validate that it meets all specifications before mass production.
8. Documentation and Traceability: Maintain clear records of inspections, tool changes, and material batches to track quality issues and institute corrective actions when needed.
Implementing these methods ensures that the milling process maintains high standards of quality, minimizing waste and rework while enhancing customer satisfaction.
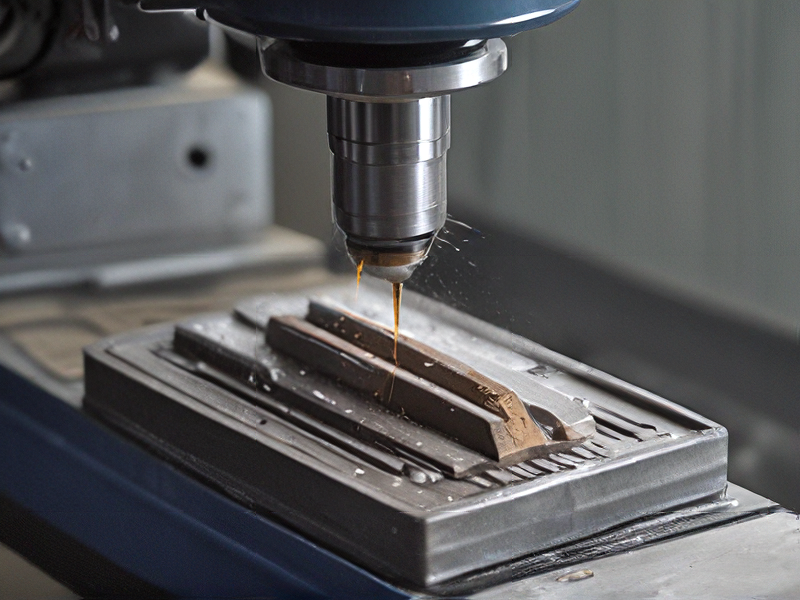
Tips for Procurement and Considerations when Purchasing from machine milling
When procuring machine milling services or equipment, there are several key considerations to ensure a successful purchase:
1. Define Requirements: Clearly outline your project specifications, such as material types, tolerances, dimensions, and quantities. This will help you communicate effectively with suppliers.
2. Supplier Evaluation: Assess potential suppliers based on their experience, reputation, and capabilities. Review customer testimonials and case studies to gauge their reliability and quality.
3. Technology Compatibility: Ensure the milling machines or services you are considering are compatible with your current technologies and workflows. Look for features like CNC capability, automation, and software compatibility.
4. Cost vs. Value: While price is important, evaluate the overall value. Cheaper options may not always meet quality standards or provide adequate support. Consider total cost of ownership, including maintenance, operation, and potential downtime.
5. Lead Times: Discuss delivery timelines with suppliers. Ensure they can meet your deadlines and consider their production capacity to handle sudden increases in volume.
6. Quality Assurance: Inquire about their quality control processes. Suppliers should have robust measures in place to ensure precision and adherence to specifications.
7. Communication: Maintain open lines of communication throughout the procurement process. This helps address any potential issues early and fosters a collaborative relationship.
8. Post-Purchase Support: Consider the level of technical support and training offered after the purchase. Good after-sales service can minimize operational disruptions and increase your team’s efficiency.
By keeping these considerations in mind, you can make informed decisions when purchasing machine milling services or equipment.
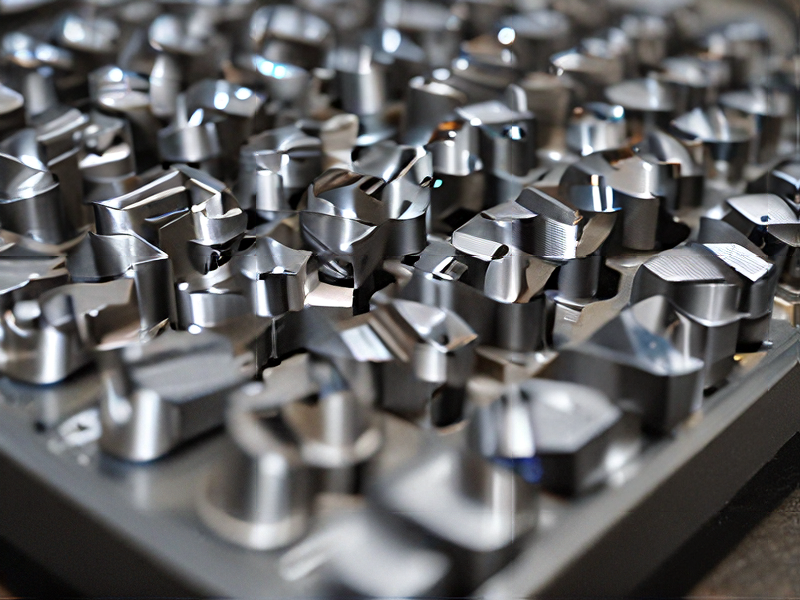
FAQs on Sourcing and Manufacturing from machine milling in China
FAQs on Sourcing and Manufacturing Machine Milling in China
1. What is machine milling?
Machine milling is a manufacturing process that involves removing material from a workpiece using rotary cutters. It’s widely used for producing precise dimensions in metal and other materials.
2. Why source milling services from China?
China offers competitive pricing, advanced technology, and a vast selection of manufacturers, making it an attractive option for outsourcing machining needs.
3. How do I find reliable manufacturers?
Research potential suppliers through platforms like Alibaba or Made-in-China, check their certifications, and read reviews. Additionally, consider visiting factories or working with sourcing agents.
4. What certifications should I look for?
Look for ISO 9001 (quality management), ISO 14001 (environmental management), and industry-specific certifications that demonstrate compliance with international standards.
5. What is the typical lead time for milling services?
Lead times can vary based on order complexity and volume but generally range from a few weeks to a couple of months. Always confirm timelines with your manufacturer.
6. What are the payment terms?
Common terms include a deposit upfront (usually 30-50%) and the balance before shipment. Ensure to agree on payment methods that protect both parties, such as through escrow services.
7. How do I handle quality control?
Establish clear specifications, inspect samples before bulk production, and consider third-party inspections to ensure quality standards are met.
8. What are the shipping options?
Freight options include sea, air, and expedited courier services. Choose based on your budget, lead time, and shipment weight.
9. Are there language barriers?
While many manufacturers speak English, it’s advisable to use clear, simple language and visual aids to minimize misunderstandings. Employing a local representative can also help.
By addressing these FAQs, you can effectively navigate the complexities of sourcing and manufacturing machine milling projects in China.
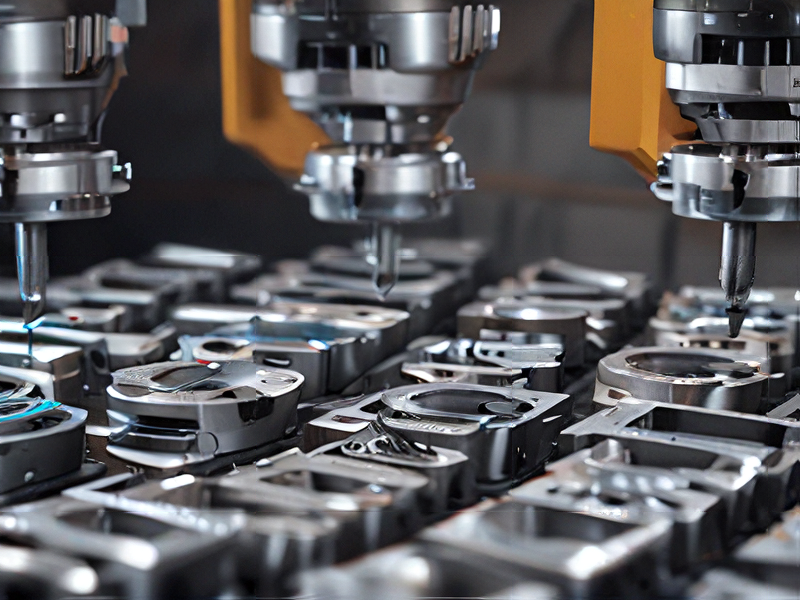