Technology and Applications of machines cnc
CNC (Computer Numerical Control) technology has revolutionized the field of manufacturing by offering precision, efficiency, and versatility. CNC machines utilize computer software to control their movements, allowing for intricate designs and repetitive tasks with minimal human intervention. This technology encompasses various types of machines, including CNC mills, lathes, routers, plasma cutters, and 3D printers.
The primary advantage of CNC machines is their ability to produce complex components with high accuracy, reducing material waste and minimizing human error. They can work with a variety of materials, including metals, plastics, and wood, making them ideal for diverse applications across industries, such as automotive, aerospace, and manufacturing.
In automotive production, CNC machines are pivotal in creating engine components and body parts with tight tolerances. In the aerospace sector, they are employed to fabricate lightweight structures and intricate components essential for flight safety. Additionally, CNC technology plays a critical role in the creation of prototypes, allowing for faster product development cycles.
Customization is another significant application of CNC technology. Manufacturers can quickly modify designs within the software to meet specific client needs, enhancing the flexibility of production processes. Furthermore, advancements in CNC technology, such as the integration of artificial intelligence and IoT, are paving the way for smart factories, where machines autonomously optimize performance and predict maintenance needs.
In summary, CNC technology is an integral part of modern manufacturing, offering precision, flexibility, and efficiency across numerous industries, thereby driving innovation and productivity in production processes.
Quality Testing Methods for machines cnc and how to control quality
Quality testing in CNC (Computer Numerical Control) machining is crucial for ensuring precision and reliability in manufactured parts. Here are some effective methods and controls for maintaining quality in CNC operations:
1. Dimensional Inspection: Utilize calipers, micrometers, and coordinate measuring machines (CMM) to verify that the dimensions of the machined parts meet the specified tolerances. This step should be conducted throughout the production process.
2. Tool Wear Monitoring: Implement a tool management system that tracks tool wear and replacement schedules. Regularly inspect tools for wear and replace them as needed to maintain precision and surface finish quality.
3. In-Process Monitoring: Employ sensors and feedback loops within the CNC machine to continuously monitor parameters such as spindle speed, feed rates, and temperature. This real-time data helps identify deviations from the set standards immediately.
4. Surface Finish Testing: Use surface roughness testers to evaluate the finish of machined parts. This is particularly important for components that require tight surface quality specifications.
5. First Article Inspection (FAI): Conduct an inspection of the first produced part against the design specifications before mass production. This ensures that any issues are caught early in the process.
6. Statistical Process Control (SPC): Analyze production data to identify trends and variations. Control charts can help in understanding the stability of the process and reducing variability.
7. Documentation and Traceability: Maintain thorough records of inspections, processes, and materials used for each job. This ensures traceability and accountability, which is vital for quality control.
By implementing these methods, manufacturers can ensure that CNC machined products meet quality standards and customer specifications, leading to reduced waste and increased customer satisfaction.
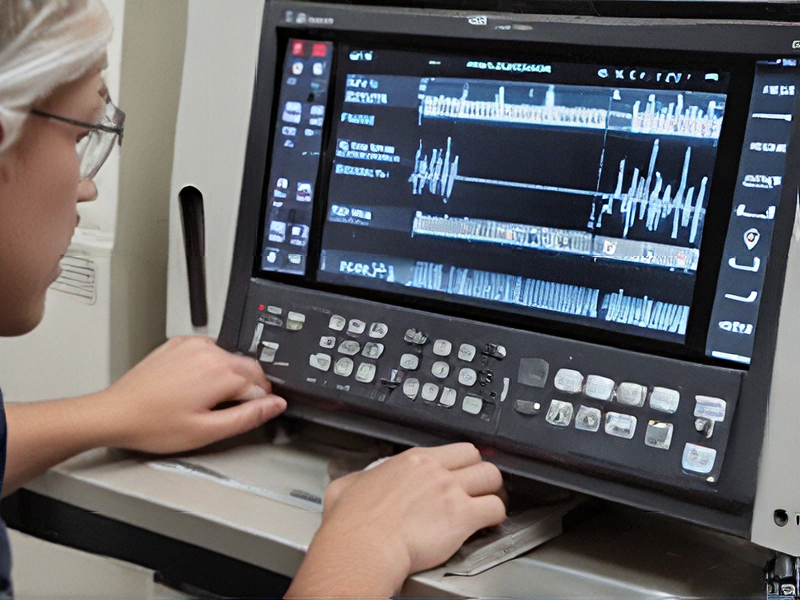
Tips for Procurement and Considerations when Purchasing from machines cnc
When purchasing CNC (Computer Numerical Control) machines, consider the following tips and aspects to ensure a successful procurement process:
1. Define Requirements: Clearly outline your production needs, including materials, part size, complexity, volume, and tolerances. This ensures that you select a machine equipped to meet your specific demands.
2. Budget Appropriately: Establish a budget that encompasses not just the initial purchase price but also installation, training, maintenance, tooling, and potential upgrades. CNC machines can be a significant investment.
3. Research Suppliers: Investigate reputable manufacturers and suppliers. Look into customer reviews, case studies, and support services to assess reliability and customer satisfaction.
4. Evaluate Technology: Examine the technological features of the CNC machine, such as its control software, precision, speed, and flexibility. Ensure it aligns with the latest industry standards.
5. Consider Training and Support: Evaluate the level of training and ongoing support offered by the supplier. Effective training is crucial for maximizing machine utilization and minimizing downtime.
6. Assess Maintenance Needs: Understand the machine’s maintenance requirements and the availability of spare parts. A machine with lower maintenance needs can save costs in the long run.
7. Check for Compatibility: Ensure that the CNC machine is compatible with your existing tools and software. This can help streamline operations and reduce additional investment in new equipment.
8. Test Before Purchase: If possible, request a demonstration or visit a facility using the machine. This provides insights into its performance and capabilities.
By considering these factors, you can make a more informed decision, ultimately enhancing productivity and efficiency in your operations.
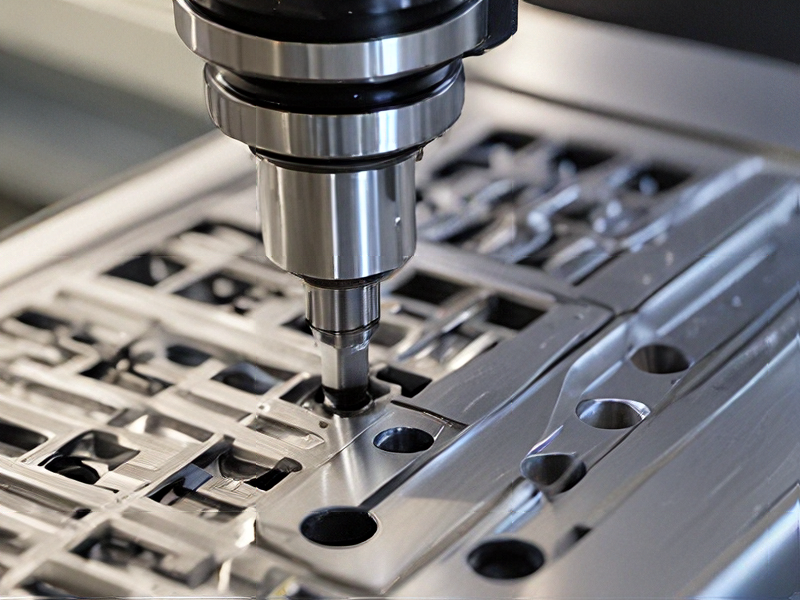
FAQs on Sourcing and Manufacturing from machines cnc in China
FAQs on Sourcing CNC Machines and Manufacturing in China
1. Why choose China for CNC machining?
China offers a combination of advanced technology, skilled labor, and competitive pricing. Many manufacturers have state-of-the-art CNC machines capable of producing high-quality parts efficiently.
2. How do I find reliable CNC suppliers in China?
Start by researching online platforms like Alibaba, Made-in-China, or directories like Global Sources. Look for suppliers with good reviews, years of experience, and relevant certifications (e.g., ISO 9001).
3. What is the typical lead time for CNC machining in China?
Lead times can vary based on complexity and order size, typically ranging from 2 to 6 weeks. Always confirm specific timelines before placing an order.
4. What are the common payment terms?
Standard payment methods include T/T (Telegraphic Transfer), PayPal, and L/C (Letter of Credit). Many suppliers require a deposit (usually 30%) before production starts.
5. How do I ensure quality control?
Request samples before full-scale production. Also, consider visiting the facility or hiring a third-party inspection service to ensure standards are met.
6. What should I be aware of regarding shipping?
Understand incoterms (e.g., FOB, CIF) that define responsibilities in shipping. Work with experienced logistics partners to navigate customs and import regulations.
7. Are there language barriers?
While many suppliers speak English, it’s advisable to communicate clearly and possibly use translation tools. Hiring a local sourcing agent can help bridge any gaps.
8. What if issues arise during manufacturing?
Establish clear communication channels and a return policy beforehand. Most suppliers are willing to address problems if they’re identified promptly.
By understanding these aspects, you can effectively source CNC machining partners in China and ensure a smooth manufacturing process.
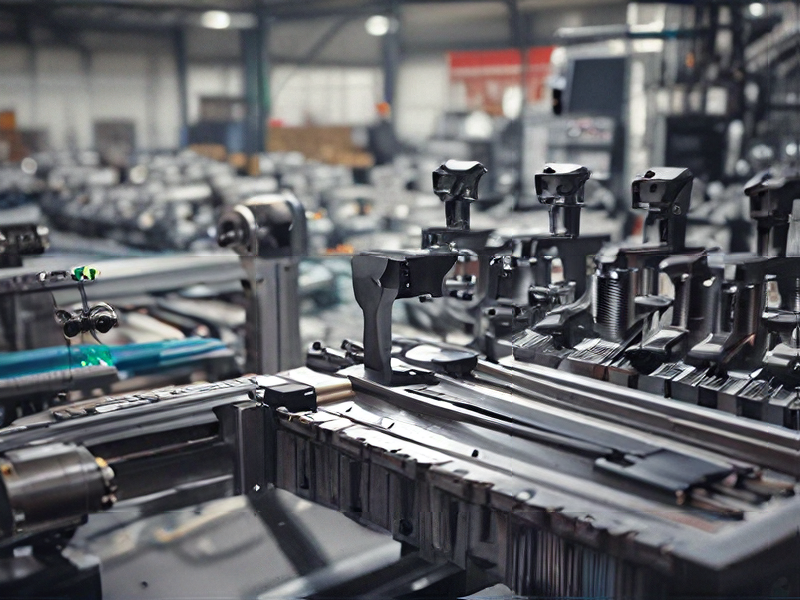