Technology and Applications of machining cnc
CNC (Computer Numerical Control) machining is a revolutionary technology that automates the control of machining tools via computer programming. It allows for precise and efficient manufacturing processes in various applications, including automotive, aerospace, medical devices, and consumer goods.
CNC machines operate by interpreting a program that specifies the machining operations needed to create a part. This program, often written in G-code, directs the machine’s movements and tool paths, allowing for complex shapes and designs that traditional machining methods struggle to achieve.
Key technologies in CNC machining include milling, turning, and electrical discharge machining (EDM). Milling involves rotating a cutting tool to remove material from a stationary workpiece, while turning uses a rotating workpiece against a fixed cutting tool. EDM, on the other hand, uses electrical discharges to shape materials, making it ideal for hard metals that are difficult to machine using conventional methods.
The applications of CNC machining are extensive. In the automotive industry, it is used to manufacture components such as engine blocks and transmission housings. The aerospace sector benefits from CNC technology to produce lightweight and intricate parts like turbine blades. Additionally, the medical field relies on CNC machining for custom prosthetics and surgical instruments, highlighting its versatility and precision.
CNC machining also enhances production efficiency by reducing lead times, minimizing waste, and allowing for continuous operation. With advancements such as multi-axis machining and automation, CNC technology continues to evolve, driving innovation and enhancing productivity across various industries. Overall, CNC machining stands as a cornerstone of modern manufacturing, enabling the production of high-quality parts with unparalleled accuracy.
Quality Testing Methods for machining cnc and how to control quality
Quality testing in CNC machining is crucial to ensure that parts meet required specifications and tolerances. Here are some commonly used methods:
1. Dimensional Inspection: Utilize calipers, micrometers, and CMM (Coordinate Measuring Machine) to verify dimensions against CAD models. This ensures that critical dimensions are within specified tolerances.
2. Visual Inspection: Conduct a thorough visual examination for surface finish, potential defects like burrs, cracks, or scratches, and adherence to design specifications. This is often the first line of defense in quality control.
3. Functional Testing: For parts that must fit or work together, assemble the components to test their functionality. This confirms that machined parts meet operational requirements.
4. Hardness and Material Testing: Perform hardness tests (e.g., Rockwell or Brinell) and material analysis to ensure that the material properties meet specifications for strength and durability.
5. Non-Destructive Testing (NDT): Techniques like ultrasonic testing or dye penetrant inspection can be employed to detect subsurface defects without damaging the part.
Quality Control Methods:
1. Statistical Process Control (SPC): Implement SPC to monitor and control the machining process through data collection and analysis. This helps in identifying trends and variations in production.
2. First Article Inspection (FAI): Conduct a comprehensive inspection of the first part produced to ensure it meets all specifications before full-scale production begins.
3. Work Instructions and Standard Operating Procedures (SOPs): Develop and adhere to detailed work instructions and SOPs to minimize variations in the manufacturing process.
4. Training and Skill Assessment: Regularly train operators on best practices and utilize skill assessments to ensure competency in machining operations.
By integrating these testing methods and control measures, manufacturers can enhance the quality and reliability of CNC machined parts.
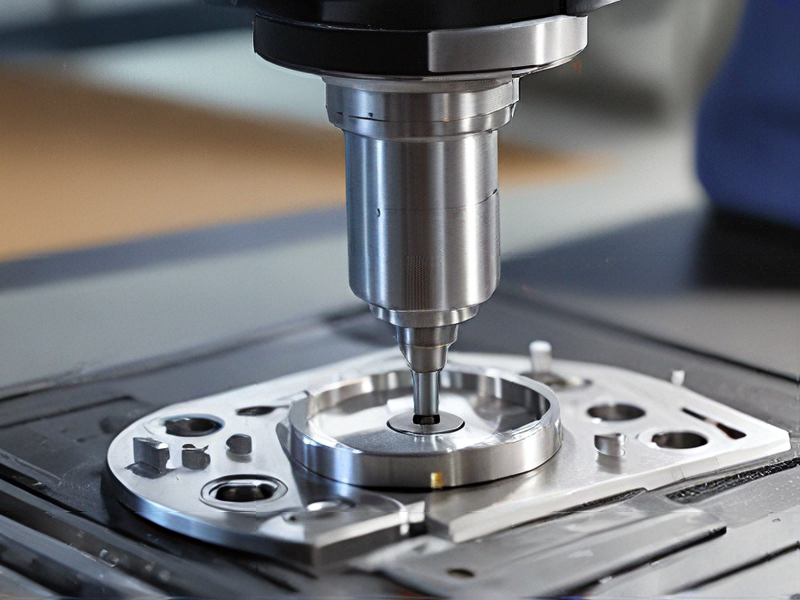
Tips for Procurement and Considerations when Purchasing from machining cnc
When procuring CNC machining services, several key considerations can help ensure a successful partnership and quality outcomes.
1. Supplier Research: Investigate potential suppliers’ reputations, capabilities, and experience in your specific industry. Look for reviews, testimonials, and case studies that demonstrate their expertise.
2. Certifications and Standards: Ensure the supplier complies with relevant industry standards (e.g., ISO 9001). Certifications reflect a commitment to quality and can assure consistent results.
3. Capabilities and Technology: Assess the supplier’s machinery and technology. Modern, high-speed CNC machines can produce parts more accurately and quickly. Ensure they have the capacity to handle your required quantities and complexities.
4. Material Options: Confirm that the supplier can work with the materials you need. Different CNC machining methods work better with specific materials (e.g., metals, plastics). Discuss material sourcing to understand lead times and costs.
5. Prototyping and Iteration: For complex parts, consider suppliers that offer prototyping services. Rapid prototyping allows for design validation before mass production, reducing the risk of costly errors.
6. Cost Transparency: Request detailed quotes that break down costs, including setup, machining, and finishing. Look out for hidden fees and ensure you understand the pricing structure.
7. Lead Times and Flexibility: Discuss lead times upfront. A reliable supplier should provide realistic timelines and show flexibility to accommodate changes or urgent orders.
8. Quality Control Processes: Inquire about their quality assurance practices. A strong focus on quality will help prevent defects and ensure your specifications are met.
9. Communication and Support: Evaluate their communication channels. Responsive and clear communication is vital for addressing issues and ensuring project alignment.
By thoroughly considering these aspects, you can make informed decisions and establish a fruitful relationship with your CNC machining supplier.
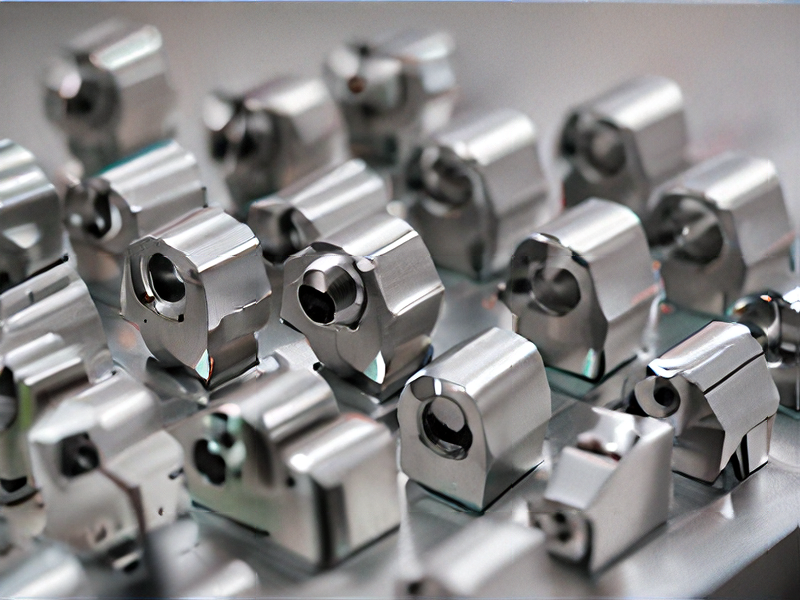
FAQs on Sourcing and Manufacturing from machining cnc in China
FAQs on Sourcing and Manufacturing CNC Machining in China
1. What is CNC machining?
CNC (Computer Numerical Control) machining is a manufacturing process that uses computer-controlled tools to create parts and components from metal, plastic, or other materials with high precision.
2. Why source CNC machining from China?
China offers competitive pricing, a wide range of suppliers, advanced technology, and production capacity, making it an attractive option for many businesses seeking cost-effective manufacturing solutions.
3. What should I consider when choosing a supplier?
Evaluate the supplier’s experience, certifications (like ISO), production capabilities, quality control processes, and past customer reviews. Communication and responsiveness are also crucial.
4. How can I ensure quality control?
Implement quality assurance protocols such as regular inspections, request samples before full production, and consider third-party quality audits. Establish clear specifications and expectations upfront.
5. What are the common challenges in sourcing from China?
Common challenges include language barriers, time zone differences, varying quality standards, and potential shipping delays. It’s important to address these by maintaining clear communication and setting realistic timelines.
6. What are lead times for CNC machining?
Lead times can vary widely based on complexity, quantity, and supplier capabilities. Generally, it ranges from a few weeks to several months. Always confirm estimated lead times upfront.
7. How do I handle shipping and customs?
Choose a reliable logistics provider and familiarize yourself with customs regulations. Calculate import duties and tariffs to avoid unexpected costs.
8. Are there minimum order quantities (MOQs)?
Many suppliers have MOQs, which may vary based on the product and production costs. It’s essential to discuss this during the initial negotiation phase.
9. Can I get a prototype before mass production?
Yes, most CNC machining suppliers can create prototypes. This step helps verify design and functionality before committing to larger orders.
For specific inquiries, always consult with professionals familiar with international sourcing.
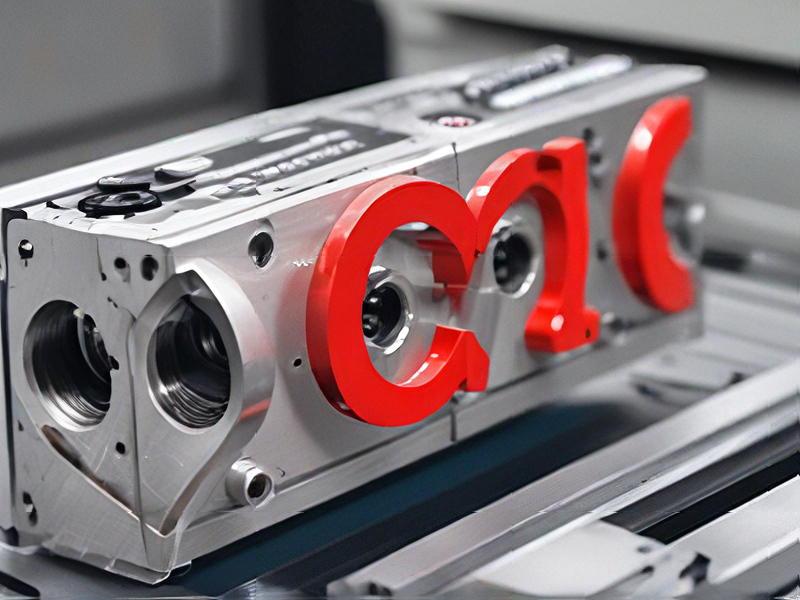