Technology and Applications of machining shops
Machining shops are essential facilities in the manufacturing sector, specializing in shaping materials into precise components using various machining processes. These shops employ advanced technologies to enhance efficiency, precision, and product quality. Key technologies include Computer Numerical Control (CNC) machines, which automate the cutting processes to produce complex geometries with high accuracy and repeatability.
Additionally, machining shops utilize different operations such as turning, milling, drilling, and grinding. Each operation serves a specific purpose—turning is used for cylindrical parts, milling for flat surfaces and intricate shapes, drilling for creating holes, and grinding for finishing surfaces and achieving tight tolerances.
The integration of additive manufacturing, such as 3D printing, is also emerging in machining shops, allowing the production of complex shapes that can be refined through traditional machining processes. This hybrid approach improves material efficiency and reduces lead times.
Software applications play a crucial role in modern machining shops, with CAD (Computer-Aided Design) and CAM (Computer-Aided Manufacturing) systems facilitating design and production planning. These tools help in simulating machining processes, optimizing tool paths, and reducing waste.
In terms of applications, machining shops serve diverse industries, including aerospace, automotive, electronics, and medical devices. They produce critical components like engines, structural parts, and precision instruments. With the rise of Industry 4.0, machining shops are increasingly adopting IoT (Internet of Things) technology, enabling real-time monitoring of equipment and predictive maintenance, which enhances productivity and minimizes downtime.
Overall, the combination of advanced machining technologies and innovative applications ensures that machining shops remain vital to modern manufacturing.
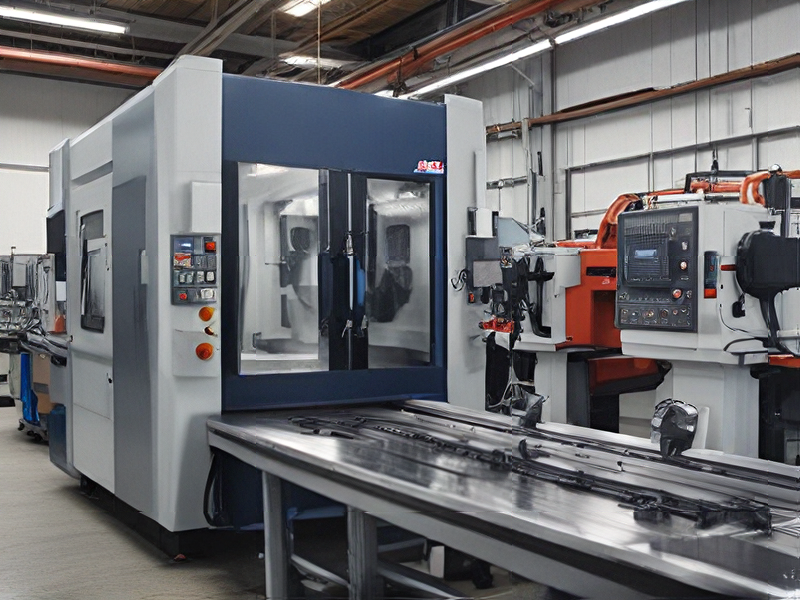
Quality Testing Methods for machining shops and how to control quality
Quality testing in machining shops is crucial to ensure that the final products meet specifications and standards. Here are several methods and strategies for controlling quality:
1. Incoming Material Inspection: Verify that raw materials meet required specifications before processing. Utilize techniques such as spectrometry for metals or dimensional checks for precision components.
2. In-Process Inspection: Implement regular checks during the machining process. This includes monitoring dimensions, surface finish, and tool wear. Using gauges, calipers, and micrometers helps maintain tolerances in real-time.
3. Final Inspection: Once machining is completed, perform a comprehensive inspection of the finished product. This may involve coordinate measuring machines (CMMs) or optical comparators to assess critical dimensions and surface integrity.
4. Statistical Process Control (SPC): Use statistical methods to monitor and control the machining process. By collecting data on production variance, trends can be identified early, minimizing defects.
5. Quality Management System (QMS): Implement a QMS like ISO 9001 to establish standard operating procedures (SOPs), promote consistency, and encourage continuous improvement. Regular audits ensure compliance and identify areas for enhancement.
6. Operator Training: Invest in regular training for machinists on best practices, machine operation, and inspection techniques. A knowledgeable workforce is essential for maintaining quality.
7. Feedback Loop: Establish a feedback mechanism where quality control data informs the machining processes. Analyzing rejection reasons helps make informed adjustments to prevent future occurrences.
By integrating these quality testing methods and controls, machining shops can significantly enhance their product reliability and customer satisfaction.
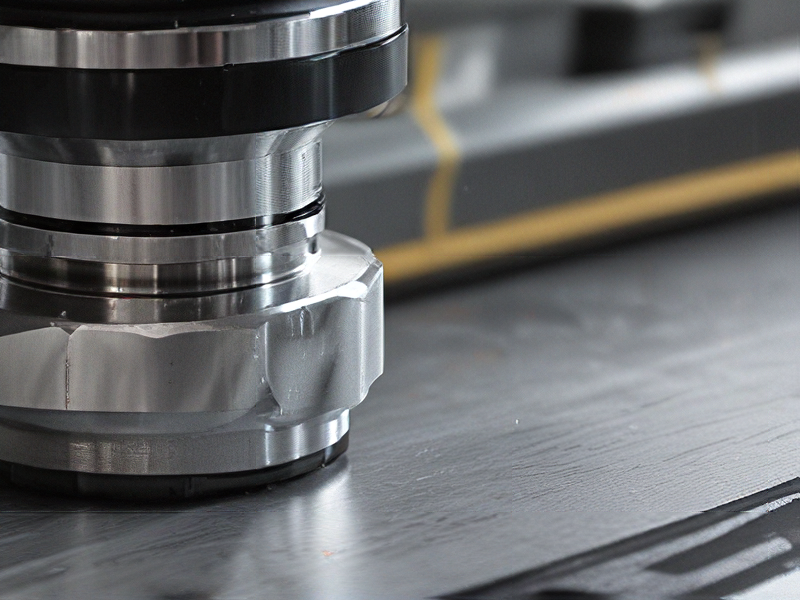
Tips for Procurement and Considerations when Purchasing from machining shops
When procuring from machining shops, several key considerations can enhance your purchasing experience and ensure optimal outcomes.
1. Quality Assurance: Verify the shop’s certifications (e.g., ISO 9001) and quality control processes. Request samples or references to assess their manufacturing precision and adherence to specifications.
2. Capabilities and Equipment: Understand the shop’s capabilities, including the types of materials they work with, machining processes (CNC, manual), and equipment used. Match these capabilities to your specific project requirements.
3. Lead Times: Inquire about production timelines. Reliable shops should provide clear estimates and can accommodate your schedule to avoid delays in project completion.
4. Cost Transparency: Request detailed quotes that break down costs for labor, materials, and any additional fees (like setup costs). Compare quotes from multiple suppliers but beware of prices that seem too low, as they may compromise quality.
5. Communication: Establish clear channels of communication. A partnership with a responsive shop enhances collaboration and can streamline problem resolution during the production process.
6. Flexibility and Support: Assess the shop’s willingness to adapt to changes in design or materials. Their ability to support adjustments can be crucial, especially in dynamic project environments.
7. Location and Shipping: Consider the shop’s location, as proximity can influence lead times and shipping costs. Factor in logistics during the procurement process.
8. Long-term Relationships: Building a long-term relationship with a machining shop can lead to better pricing, priority service, and improved collaboration, so consider potential future projects.
By focusing on these areas, you can make informed decisions that enhance procurement efficiency and product quality.
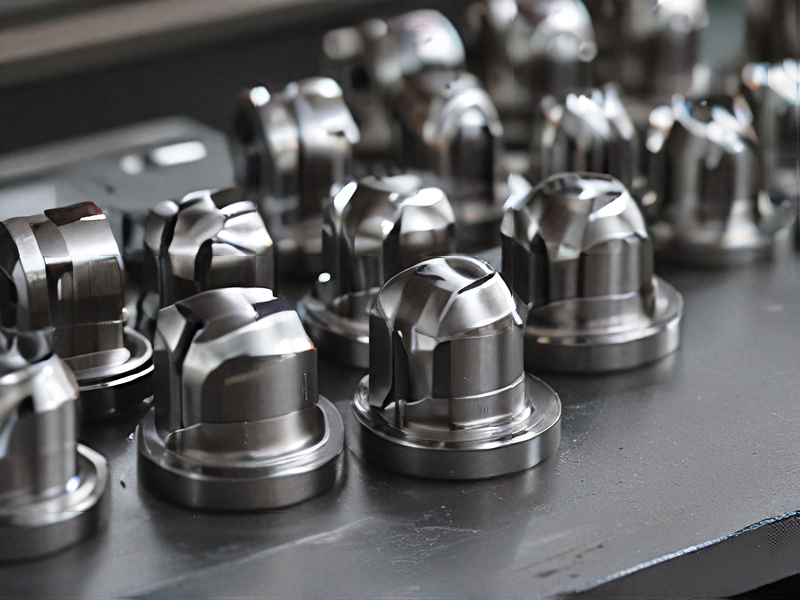
FAQs on Sourcing and Manufacturing from machining shops in China
FAQs on Sourcing and Manufacturing from Machining Shops in China
1. Why source from machining shops in China?
China offers cost-effective manufacturing, a wide range of skilled labor, advanced technology, and scalability. This can lead to significant savings and faster production times.
2. What are the risks of sourcing from China?
Potential risks include quality control issues, communication barriers, intellectual property concerns, and longer lead times. Conducting due diligence on suppliers can mitigate these risks.
3. How do I find reliable machining shops?
Start with platforms like Alibaba, Global Sources, or Made-in-China. Attending trade shows and utilizing sourcing agents can also help identify reputable manufacturers.
4. What certifications should I look for?
Look for ISO 9001 (Quality Management) and ISO 13485 (Medical Devices) certifications, depending on your industry. These certifications indicate a commitment to quality.
5. How to ensure product quality?
Implement a robust quality control plan, request samples, conduct factory audits, and consider third-party inspections to ensure products meet your specifications.
6. What is the typical lead time for production?
Lead times vary based on complexity and order size but generally range from 3 to 12 weeks. Discuss timelines upfront with your supplier.
7. How can I protect my intellectual property?
Use non-disclosure agreements (NDAs), choose trustworthy suppliers, and consider legal advice for patent protections if necessary.
8. What are the shipping options?
Common shipping methods include air freight for urgent orders and sea freight for larger, non-urgent shipments. Evaluate costs and timelines based on your needs.
9. What are the payment terms?
Payment terms can vary, but common methods include a deposit upfront and balance before shipment. Always clarify terms in the contract.
By carefully navigating these factors, you can successfully source and manufacture high-quality products from machining shops in China.
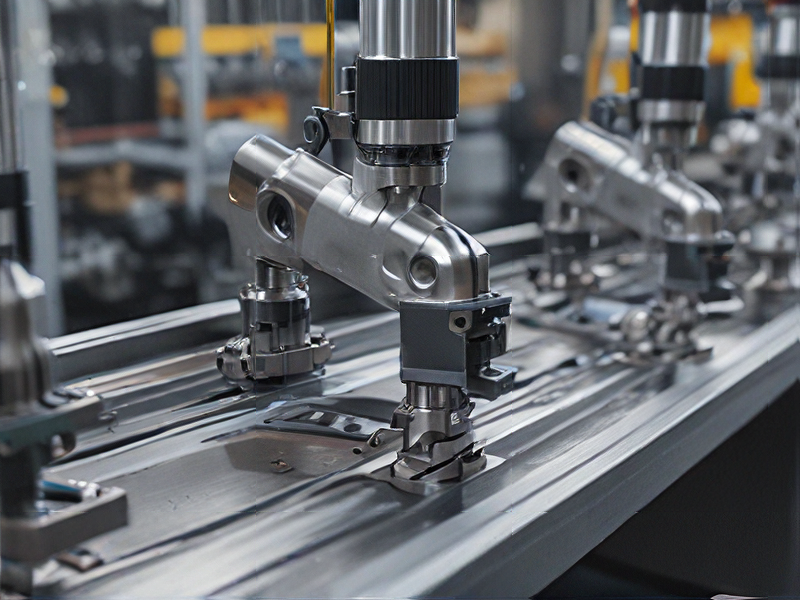