Technology and Applications of machinist symbols
Machinist symbols are crucial in manufacturing and engineering, providing a standardized way to communicate specifications for machined parts. These symbols are typically used on technical drawings, blueprints, and CAD models to convey critical information to machinists and other personnel involved in manufacturing processes.
Common machinist symbols include:
1. Dimensioning and Tolerancing: Symbols like concentricity, perpendicularity, and parallelism indicate specific geometric tolerances that parts must meet. These ensure parts fit and function correctly when assembled.
2. Surface Texture: Symbols such as roughness average (Ra), surface finish, and waviness help define the texture and quality of machined surfaces, crucial for functionality and aesthetics.
3. Hole and Thread Specifications: Symbols for holes (depth, diameter) and threads (pitch, type) ensure precise alignment and compatibility during assembly.
4. Material Specifications: Symbols denote the type of material, heat treatment requirements, and other material-specific details critical for manufacturing processes and part performance.
Applications of machinist symbols span various industries including automotive, aerospace, and electronics manufacturing. Engineers and designers rely on these symbols to communicate design intent accurately to machinists and ensure parts are manufactured to exact specifications. Machinists interpret these symbols to set up machines, select tools, and perform inspections, ensuring parts meet quality standards and functional requirements.
Overall, machinist symbols streamline communication, improve accuracy, and facilitate efficient manufacturing processes, contributing to the quality and reliability of machined parts across industries.

Quality Testing Methods for machinist symbols and how to control quality
Quality testing methods for machinist symbols primarily involve verification against engineering drawings and specifications. Here are key approaches:
1. Dimensional Inspection: Use of precision measurement tools such as calipers, micrometers, and coordinate measuring machines (CMMs) to verify dimensions specified by the symbols.
2. Visual Inspection: Examination of surface finishes, welds, and overall appearance to ensure adherence to specified standards.
3. Functional Testing: Testing the functionality of components to ensure they perform as intended, which may involve assembly tests or mechanical operation checks.
4. Material Testing: Verification of material properties such as hardness, tensile strength, and chemical composition through tests like hardness testing or spectroscopy.
5. Statistical Process Control (SPC): Monitoring and controlling manufacturing processes using statistical methods to ensure consistency and quality over time.
Controlling quality involves implementing these methods consistently throughout production, documenting results, and taking corrective actions when deviations occur. Training personnel on interpreting machinist symbols and using testing equipment is crucial for maintaining high standards. Regular audits and reviews of processes help refine quality control measures and ensure continuous improvement.
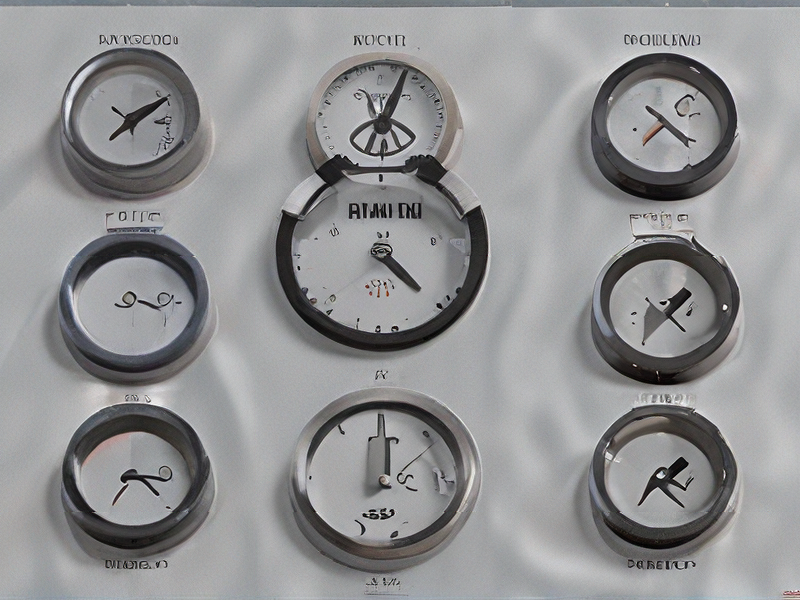
Tips for Procurement and Considerations when Purchasing from machinist symbols
When procuring parts or services from machinist symbols, it’s crucial to consider several key factors to ensure successful outcomes:
1. Blueprint Interpretation: Understand and interpret the machinist symbols correctly from the blueprint or technical drawing provided. Symbols convey critical information about dimensions, tolerances, surface finishes, and other specifications essential for manufacturing precision parts.
2. Material Specifications: Verify the material requirements specified in the blueprint. Different materials have varying mechanical properties (strength, hardness, corrosion resistance), which can significantly impact the part’s performance and longevity.
3. Tolerance Requirements: Pay close attention to tolerance specifications indicated by symbols such as geometric dimensioning and tolerancing (GD&T). These define permissible variations in dimensions and ensure parts fit together correctly and function as intended.
4. Surface Finish: Machinist symbols also indicate required surface finishes. Consider the application requirements (e.g., smoothness for sealing surfaces or roughness for grip) to select the appropriate machining processes and finishing techniques.
5. Quality Assurance: Ensure the machinist or supplier has robust quality control measures in place. This includes inspection protocols, certifications (ISO, AS9100, etc.), and a track record of delivering parts that meet specified requirements.
6. Cost and Lead Time: Balance cost considerations with quality and lead time requirements. Machining complexity, material choice, tolerances, and finishing impact pricing. Discuss lead times upfront to align with project schedules.
7. Communication: Maintain clear and open communication with the machinist or supplier throughout the procurement process. Clarify any ambiguities in the blueprint, confirm specifications, and address any concerns promptly to avoid misunderstandings.
8. Supplier Capability: Evaluate the machinist or supplier’s expertise, equipment capabilities, and experience with similar projects. A supplier familiar with your industry or specific requirements may offer insights and efficiencies.
By considering these factors, you can enhance the procurement process for machined parts, ensuring they meet your project’s specifications, quality standards, and timeline expectations.
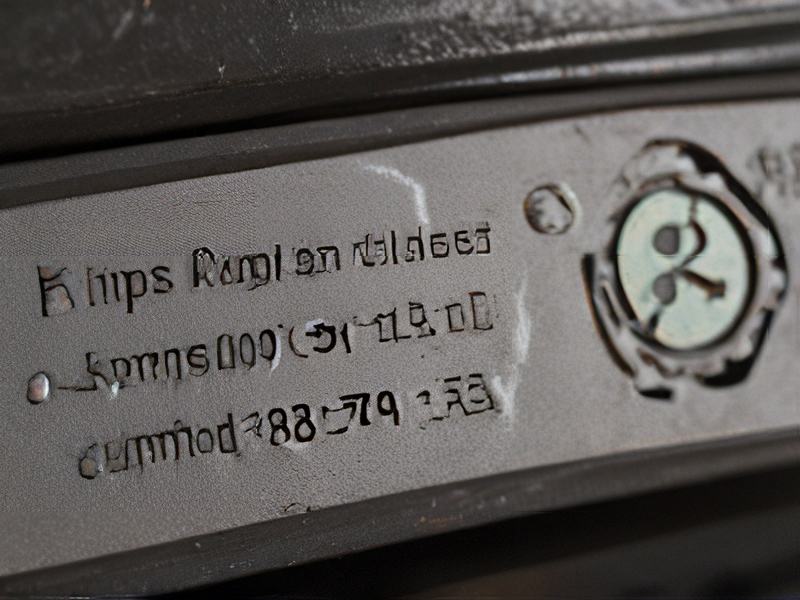
FAQs on Sourcing and Manufacturing from machinist symbols in China
When sourcing and manufacturing from China, understanding machinist symbols is crucial for clear communication and accurate production. Here are some FAQs to guide you:
1. What are machinist symbols?
Machinist symbols are graphical representations used in engineering drawings to specify requirements for machining operations, such as dimensions, tolerances, surface finishes, and more.
2. Why are machinist symbols important when sourcing from China?
Clear and standardized communication through machinist symbols helps ensure that manufacturers in China understand your requirements precisely, reducing the risk of errors and misunderstandings in production.
3. Which machinist symbols are commonly used in China?
Common symbols include those for dimensions (such as diameter and length), geometric tolerances (like concentricity and perpendicularity), surface finishes (such as roughness average), and symbols indicating special processes or treatments.
4. How can I ensure machinist symbols are understood by Chinese manufacturers?
Provide detailed engineering drawings with internationally recognized symbols, ensure translations are accurate, and clarify any specifications that may be ambiguous.
5. What should I consider regarding cultural and language differences?
Be aware of potential language barriers and cultural differences in interpreting specifications. Clarify expectations upfront and maintain open communication channels throughout the manufacturing process.
6. How do machinist symbols impact quality control?
Properly specified machinist symbols facilitate consistent quality control by providing clear benchmarks against which manufactured parts can be measured and verified.
Understanding and correctly applying machinist symbols when sourcing from China enhances efficiency, reduces manufacturing costs, and helps maintain product quality to meet international standards.
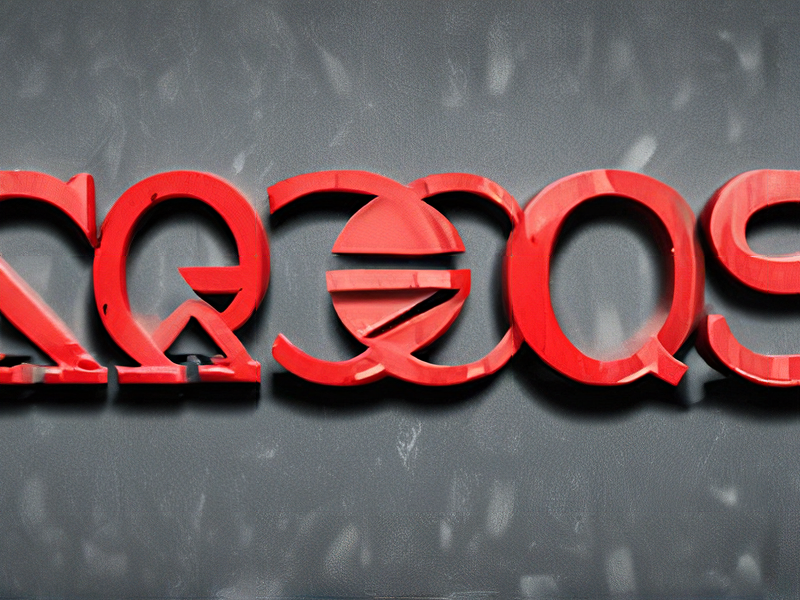