Technology and Applications of material stainless steel
Stainless steel is a versatile and durable alloy primarily composed of iron, chromium, and, in some cases, nickel and molybdenum. Its remarkable resistance to corrosion, staining, and oxidation makes it a preferred choice across various industries.
Applications:
1. Construction: Stainless steel is widely used in building structures, facades, and roofing materials, as it combines strength with aesthetic appeal. Its longevity reduces maintenance costs.
2. Food and Beverage Industry: Due to its hygienic properties, stainless steel is essential in manufacturing kitchen appliances, food processing equipment, and storage containers. Its resistance to rust and ease of cleaning meet stringent health standards.
3. Medical Equipment: In healthcare, stainless steel is utilized for surgical instruments, implants, and medical devices due to its biocompatibility, strength, and resistance to sterilization processes.
4. Automotive Sector: Stainless steel components are used in exhaust systems and trim pieces for their durability and resistance to high temperatures and corrosion, improving vehicle longevity.
5. Consumer Goods: Products like cutlery, cookware, and fixtures are often made from stainless steel for their aesthetic appeal, durability, and easy maintenance.
Technological Advancements:
Recent innovations in stainless steel technology include:
– Advanced Manufacturing Techniques: Methods such as 3D printing and laser cutting are enabling complex designs and customized solutions.
– Corrosion-Resistant Alloys: Developments in alloy compositions have led to materials with enhanced resistance to aggressive environments, expanding their applicability in harsh conditions.
– Eco-Friendly Production: Sustainable manufacturing processes are being adopted, which reduce energy consumption and emissions associated with stainless steel production.
In summary, stainless steel’s unique properties and ongoing technological advancements ensure its continued relevance across multiple sectors, contributing to efficiency and sustainability.
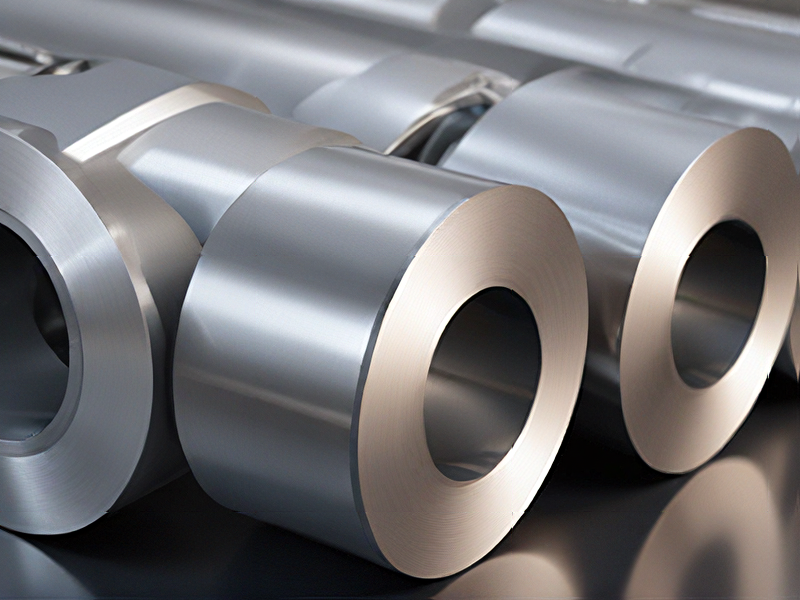
Quality Testing Methods for material stainless steel and how to control quality
Quality testing methods for stainless steel are crucial to ensure that the material meets specific performance and safety standards. Key testing methods include:
1. Chemical Composition Analysis: Utilizing techniques like Optical Emission Spectroscopy (OES) or X-ray Fluorescence (XRF), the composition of stainless steel is analyzed to confirm it meets specified alloy standards.
2. Mechanical Testing: Tests such as tensile strength, yield strength, and elongation assess the material’s mechanical properties. These are performed according to ASTM or ISO standards to ensure reliability.
3. Hardness Testing: Methods like Rockwell, Brinell, or Vickers hardness tests determine the hardness of the material, indicating its resistance to deformation and wear.
4. Corrosion Testing: Salt spray tests or electrochemical tests evaluate the corrosion resistance, a critical property of stainless steel. This assesses performance in various environments.
5. Non-Destructive Testing (NDT): Techniques such as ultrasonic testing, magnetic particle testing, and dye penetrant testing detect internal and surface flaws without damaging the material.
To control quality effectively:
– Supplier Selection: Choose reputable suppliers with quality certifications, such as ISO 9001.
– Incoming Inspection: Conduct routine inspections and tests on materials upon receipt to ensure they meet specifications.
– Standard Operating Procedures (SOPs): Establish and follow SOPs for processing, testing, and handling stainless steel.
– Documentation and Traceability: Maintain thorough records of all tests and inspections, ensuring traceability of materials to their source.
– Training: Equip personnel with training on quality standards and testing methods to enhance overall quality control.
Implementing these methods ensures that stainless steel components meet the required quality and performance standards, ultimately leading to enhanced safety and durability in applications.
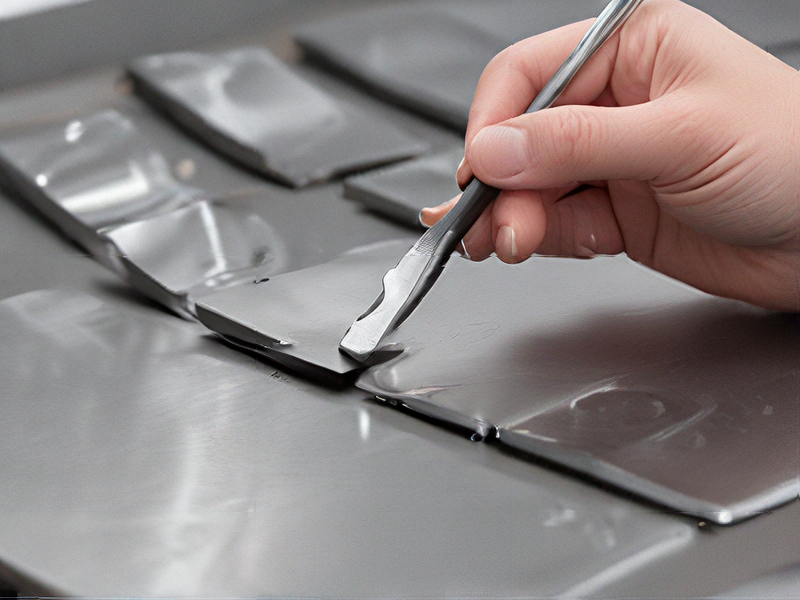
Tips for Procurement and Considerations when Purchasing from material stainless steel
When procuring stainless steel, consider the following tips and factors to ensure you make an informed purchase:
1. Material Specification: Understand the type of stainless steel needed for your application, such as 304 for general use, 316 for marine environments, or specialized grades for high-temperature or corrosive applications.
2. Certifications and Standards: Verify that the supplier complies with relevant standards (e.g., ASTM, ISO) and provides certification for the material’s properties and composition.
3. Supplier Reputation: Choose reputable suppliers with positive reviews and a proven track record in quality and customer service. Request references if necessary.
4. Pricing and Quantity: Compare prices from multiple suppliers, but consider the balance between cost and quality. Be mindful of minimum order quantities and bulk pricing options.
5. Lead Times: Confirm lead times for delivery to avoid delays in your project. Ensure the supplier can meet your timeline.
6. Testing and Quality Control: Inquire about the testing methods used to ensure material quality, such as tensile strength, corrosion resistance, and surface finish.
7. Surface Finish: Consider the required surface finish based on end-use. Polished finishes may be necessary for aesthetic applications, while rough finishes might be suitable for industrial use.
8. Sustainability Practices: Evaluate the supplier’s environmental policies and recycling practices, as sustainability is increasingly important.
9. Post-Purchase Support: Check if the supplier offers assistance with handling, fabrication, and any warranty or support for their products.
By carefully evaluating these factors, you can optimize your procurement process and secure high-quality stainless steel materials for your needs.
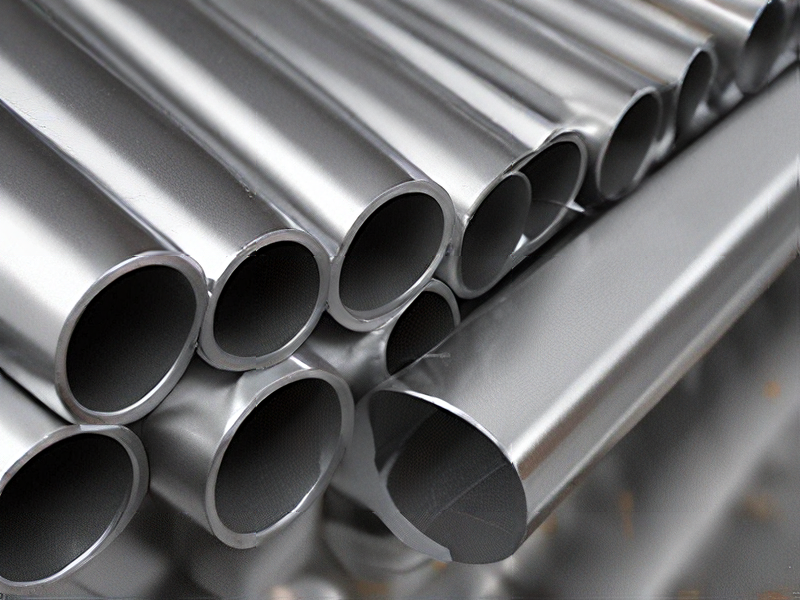
FAQs on Sourcing and Manufacturing from material stainless steel in China
FAQs on Sourcing and Manufacturing Stainless Steel in China
1. Why choose China for stainless steel sourcing?
China is a global leader in stainless steel production, offering competitive prices, a wide range of materials, and advanced manufacturing technologies.
2. What types of stainless steel materials can I source?
You can source various grades, such as 304, 316, and 430, catering to different applications like construction, automotive, and food processing.
3. How do I find reliable suppliers?
Utilize platforms like Alibaba, Made-in-China, or Global Sources. Consider attending trade fairs or using sourcing agents to vet potential suppliers.
4. What certifications should suppliers have?
Look for certifications like ISO 9001, ASTM, or equivalent. It ensures adherence to international quality and safety standards.
5. How do I ensure product quality?
Request samples before placing bulk orders and conduct quality inspections through third-party agencies. Specify quality control measures in your contract.
6. What are the typical lead times?
Lead times can vary but generally range from 4 to 12 weeks depending on order complexity and supplier capacity.
7. Are there minimum order quantities (MOQs)?
Yes, most suppliers have MOQs that can vary significantly based on product type and customization requirements.
8. How do I handle shipping and logistics?
Coordinate shipping through freight forwarders. Understand Incoterms (e.g., FOB, CIF) to clarify responsibilities for shipping costs and risk.
9. What are the payment terms typically used?
Common payment methods include T/T (wire transfer), PayPal, and potentially L/C (letter of credit). Always negotiate terms upfront.
10. What are common challenges?
Challenges include language barriers, cultural differences, and varying quality standards. Clear communication and thorough planning are crucial to overcoming these.
By understanding these key areas, you can streamline your sourcing and manufacturing process for stainless steel in China effectively.
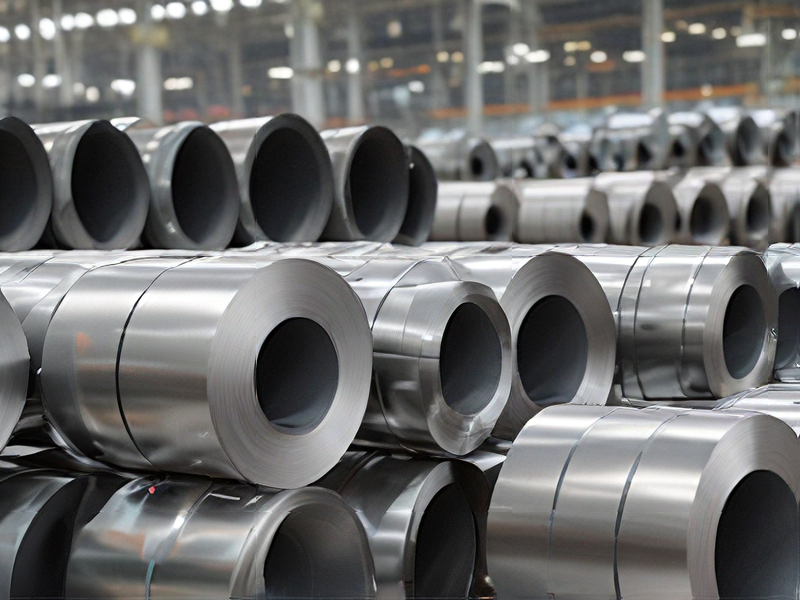