Technology and Applications of melting point steel
Melting point steel typically refers to high-temperature steel alloys engineered for applications that require resistance to deformation and structural integrity at elevated temperatures. These steels, such as AISI 310, AISI 316, and others, exhibit melting points significantly higher than conventional steels, often exceeding 1400°C (2550°F).
Technology: The production of melting point steel involves alloying elements like chromium, nickel, and molybdenum, which enhance oxidation resistance and strength at high temperatures. Advanced techniques such as vacuum arc remelting (VAR) and electro-slag remelting (ESR) are utilized to purify the steel and improve its microstructure, thus enhancing uniformity and mechanical properties. The deployment of sophisticated heat treatment processes further optimizes toughness and resistance to thermal fatigue.
Applications: High melting point steels are crucial in sectors such as aerospace, power generation, and chemical processing. They are commonly used in manufacturing turbine blades, heat exchangers, and furnace components that must endure extreme temperatures and corrosive environments. For example, in gas turbines, these steels provide reliability and efficiency, reducing the risk of failure during operation. In nuclear reactors, they serve in critical components, maintaining structural integrity under intense heat and radiation.
Additionally, the automotive industry increasingly adopts these materials for high-performance applications, enabling vehicles to withstand higher operating temperatures, thus enhancing fuel efficiency and emissions reduction.
In summary, the technology behind melting point steels is driven by alloying and advanced processing techniques, making them indispensable in high-temperature applications across various industries.
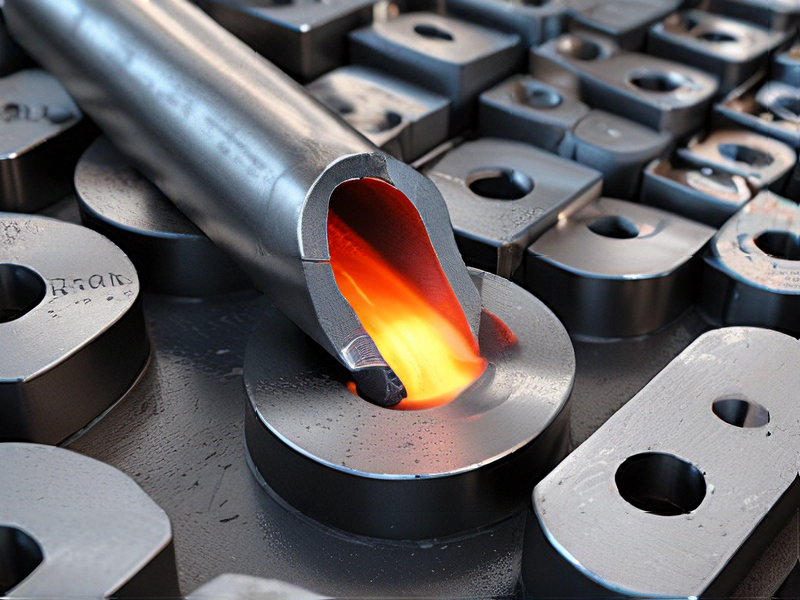
Quality Testing Methods for melting point steel and how to control quality
Quality testing of melting point steel is essential for ensuring the material meets industry standards and performs reliably in applications. Here are key methods and quality control measures:
Testing Methods
1. Thermographic Analysis: Employ differential scanning calorimetry (DSC) to determine melting point. This method analyzes thermal transitions in materials, providing accurate melting temperature data.
2. Melting Point Apparatus: Use a melting point apparatus or capillary method where small steel samples are heated gradually. The temperature at which the sample transitions from solid to liquid is recorded.
3. X-ray Diffraction (XRD): Analyze the crystalline structure of steel before and after heating. Changes in the structure can indicate alterations in melting behavior and properties.
4. Spectroscopy: Utilize optical emission spectroscopy to assess chemical composition. This ensures the alloying elements are within specified limits that can influence melting point and quality.
5. Hardness Testing: Conduct Rockwell or Brinell hardness tests post-melting point measurement to ensure the material retains desired mechanical properties.
Quality Control Measures
1. Standard Operating Procedures (SOPs): Establish standardized protocols for each testing method to ensure consistency and reliability.
2. Regular Calibration: Routine calibration of testing equipment is essential to maintain accuracy in measurements.
3. Material Traceability: Implement systems to trace the source of raw materials used in steel production, allowing for better quality assurance.
4. Training Programs: Regular training for personnel on the latest testing methodologies and quality control practices.
5. Documentation and Review: Maintain comprehensive records of test results and perform periodic reviews to ensure compliance with industry standards (e.g., ASTM, ISO).
By utilizing these methods and controls, manufacturers can ensure the quality and reliability of melting point steel, which is crucial for its performance in various applications.
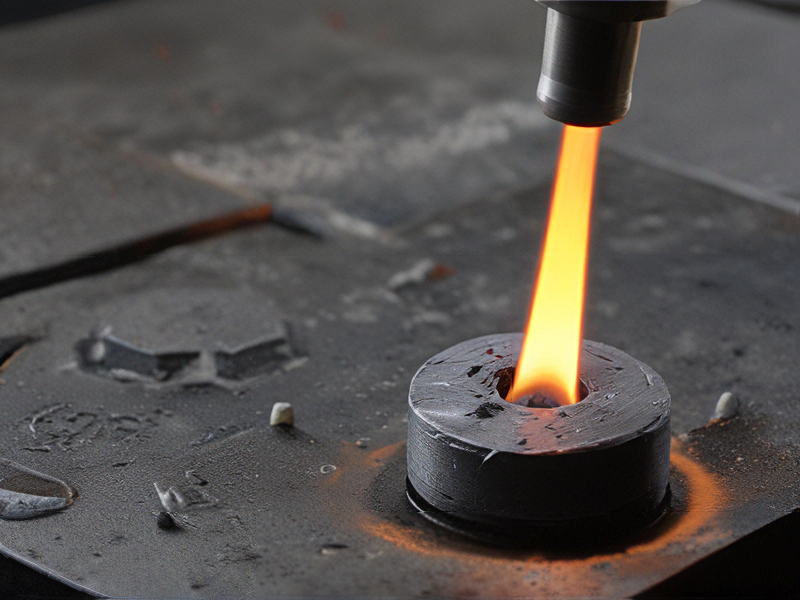
Tips for Procurement and Considerations when Purchasing from melting point steel
When procuring melting point steel, several key considerations can help ensure optimal purchasing decisions:
1. Understand Specifications: Familiarize yourself with the specific grades and compositions of melting point steel. Different applications may require varying grades based on mechanical properties and melting points.
2. Supplier Reputation: Choose suppliers with a strong reputation for quality and reliability. Research their certifications, customer reviews, and delivery histories to assess their credibility.
3. Quality Assurance: Verify that the supplier follows stringent quality control measures. Request certifications like ISO or ASTM compliance, which indicate adherence to industry standards.
4. Pricing and Budget: Compare pricing among multiple suppliers but don’t compromise quality for cost. Understand the factors that influence pricing, such as raw material costs, manufacturing processes, and market demand.
5. Lead Time and Availability: Consider the lead time for procurement. Ensure that the supplier can meet your delivery schedule to avoid project delays.
6. Technical Support: Opt for suppliers that offer technical support or consultation. This can be crucial for addressing specific project needs and ensuring compatibility with existing materials.
7. Testing and Certifications: Request mechanical property test results and certifications that validate the material’s performance, especially if used in critical applications.
8. Sustainability Practices: In today’s market, consider suppliers that engage in sustainable practices. This aligns with corporate social responsibility goals and may enhance your brand image.
9. Long-term Relationships: Building a long-term relationship with a trusted supplier can lead to better pricing, priority service, and access to new innovations.
By keeping these tips and considerations in mind, you can streamline your procurement process and ensure you select the right melting point steel for your needs.
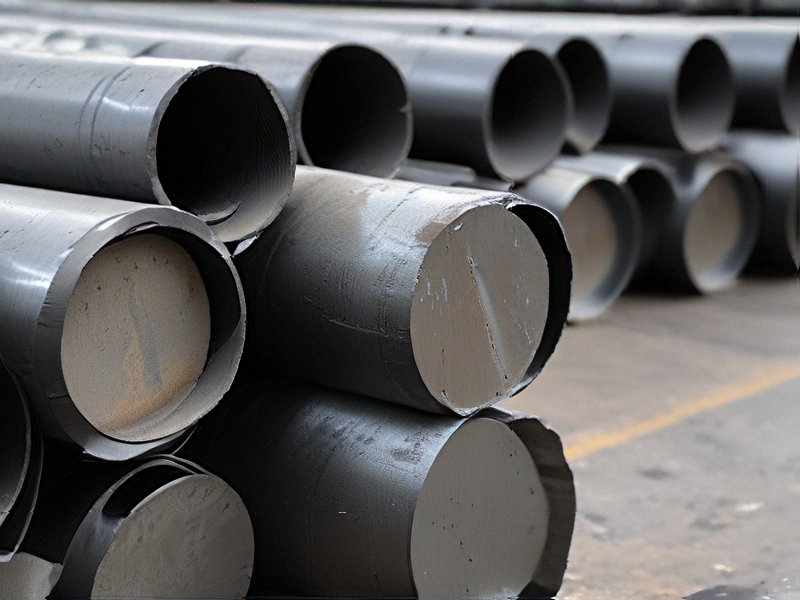
FAQs on Sourcing and Manufacturing from melting point steel in China
FAQs on Sourcing and Manufacturing Melting Point Steel in China
1. What is melting point steel?
Melting point steel typically refers to specialty steels with high-temperature resistance, commonly used in harsh environments. Understanding its melting point is crucial for applications in aerospace, automotive, and industrial manufacturing.
2. Why source from China?
China offers competitive pricing, advanced manufacturing capabilities, and a wide range of suppliers. Its established infrastructure and experienced workforce make it a preferred destination for sourcing high-quality steel products.
3. How to find reputable suppliers?
Research potential suppliers through online platforms like Alibaba, Global Sources, or industry-specific directories. Verify their certifications, customer reviews, and manufacturing capabilities. Consider visiting their facilities for a firsthand evaluation.
4. What certifications should suppliers have?
Key certifications include ISO 9001 for quality management, ASTM standards for material specifications, and any relevant industry-specific certifications. Ensure suppliers comply with international quality standards.
5. What are the common challenges?
Challenges may include communication barriers, quality assurance, intellectual property protection, and logistical issues. Establish clear contracts and maintain regular communication to mitigate these risks.
6. How do I ensure product quality?
Implement stringent quality control measures, including pre-shipment inspections and material testing. Request samples before large orders to evaluate material properties and manufacturing quality.
7. What are the lead times for sourcing?
Lead times can vary based on order size and complexity. Typically, expect 4-12 weeks for production, plus additional time for shipping. Clarify timelines with suppliers upfront.
8. How do tariffs and regulations impact sourcing?
Stay informed about current tariffs and trade regulations that may affect steel imports. Consulting with a trade specialist can help navigate these challenges and minimize costs.
For further inquiries, it’s advisable to engage with professionals experienced in sourcing and manufacturing in China.
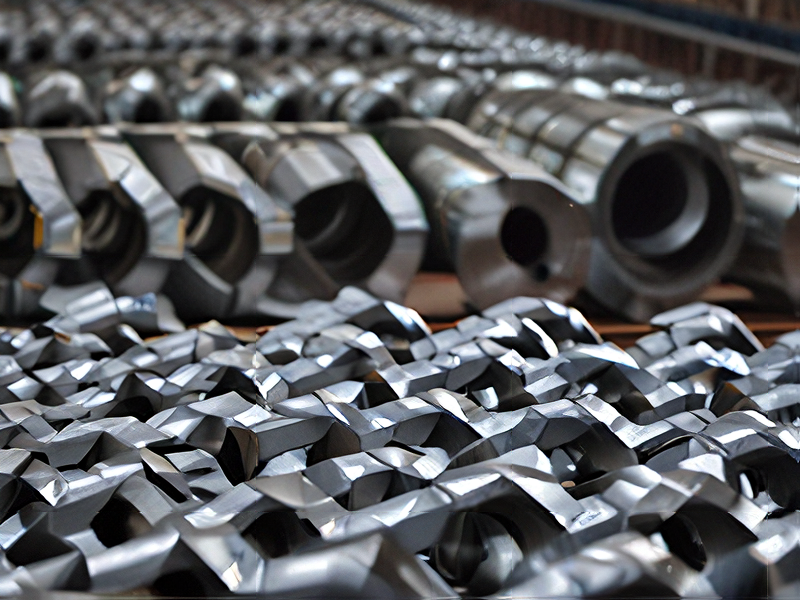