Technology and Applications of metal brackets
Metal brackets are essential components in various industries, particularly in construction, manufacturing, and electronics, due to their strength, durability, and versatility. They are typically made from steel, aluminum, or stainless steel, offering varying levels of resistance to corrosion and mechanical stress.
Technology
Manufacturing Processes:
1. Stamping: Metal sheets are cut and shaped using dies and presses, allowing for high precision and repeatability.
2. Casting: Molten metal is poured into molds to create brackets with complex geometries.
3. Extrusion: Metal is forced through a die to produce continuous shapes that are then cut to length.
4. Machining: CNC machines and lathes are used to create brackets with precise dimensions and intricate designs.
Finishing Techniques:
1. Galvanization: Coating with zinc to prevent rust.
2. Anodizing: Enhancing corrosion resistance and aesthetic appeal for aluminum brackets.
3. Powder Coating: Applying a durable, colorful finish.
Applications
Construction:
– Structural Support: Metal brackets reinforce beams, columns, and trusses.
– Wall Mounts: Used for securing shelves, cabinets, and other fixtures to walls.
Manufacturing:
– Assembly Components: Integral in machinery and equipment assembly for holding parts together.
– Automotive Industry: Used in vehicle frames, engine components, and exhaust systems.
Electronics:
– Mounting Hardware: Secure circuit boards, components, and devices within enclosures.
– Heat Sinks: Certain brackets double as heat sinks, dissipating heat from electronic components.
Furniture:
– Joint Reinforcement: Strengthen joints in tables, chairs, and other furniture items.
– Aesthetic Fixtures: Decorative brackets for shelving and furniture design.
Metal brackets are indispensable in creating robust, reliable, and long-lasting structures and products across various sectors. Their adaptability to different manufacturing processes and finishing techniques makes them a versatile choice for both functional and decorative applications.
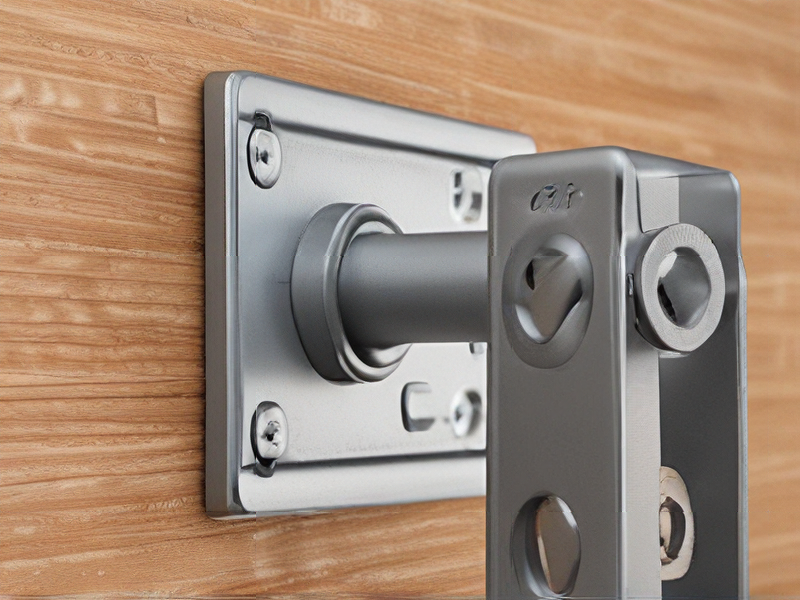
Quality Testing Methods for metal brackets and how to control quality
Quality testing for metal brackets involves various methods to ensure they meet required standards and perform as expected. Key testing methods include:
1. Material Testing:
– Chemical Composition Analysis: Verifies that the metal’s chemical makeup meets specifications.
– Mechanical Testing: Includes tensile strength, yield strength, and hardness tests to assess the bracket’s ability to withstand forces and impacts.
2. Dimensional Inspection:
– Calipers and Micrometers: Measure the dimensions of the brackets to ensure they conform to design specifications.
– Coordinate Measuring Machines (CMM): Provide precise measurements of complex geometries.
3. Surface Finish Inspection:
– Visual Inspection: Detects surface defects like scratches, cracks, or corrosion.
– Surface Roughness Tester: Measures the smoothness of the surface, ensuring it meets the required finish.
4. Non-Destructive Testing (NDT):
– Ultrasonic Testing: Detects internal flaws or inconsistencies without damaging the bracket.
– Magnetic Particle Inspection: Identifies surface and slightly subsurface defects in ferromagnetic materials.
5. Load Testing:
– Static Load Testing: Evaluates the bracket’s performance under a constant load.
– Dynamic Load Testing: Assesses the bracket’s behavior under varying loads and conditions.
Quality Control Measures:
1. Standard Operating Procedures (SOPs): Detailed procedures for manufacturing and testing ensure consistency and compliance with standards.
2. Regular Calibration of Equipment: Ensures measurement tools and machines provide accurate and reliable results.
3. Statistical Process Control (SPC): Uses statistical methods to monitor and control the manufacturing process, reducing variability and defects.
4. Supplier Quality Management: Ensures raw materials meet quality standards before they enter the production process.
5. Training and Certification: Regular training for staff on quality standards and testing procedures ensures a skilled workforce.
6. Documentation and Traceability: Keeping detailed records of materials, processes, and tests ensures any issues can be traced and addressed efficiently.
By integrating these testing methods and quality control measures, manufacturers can ensure the reliability and performance of metal brackets.
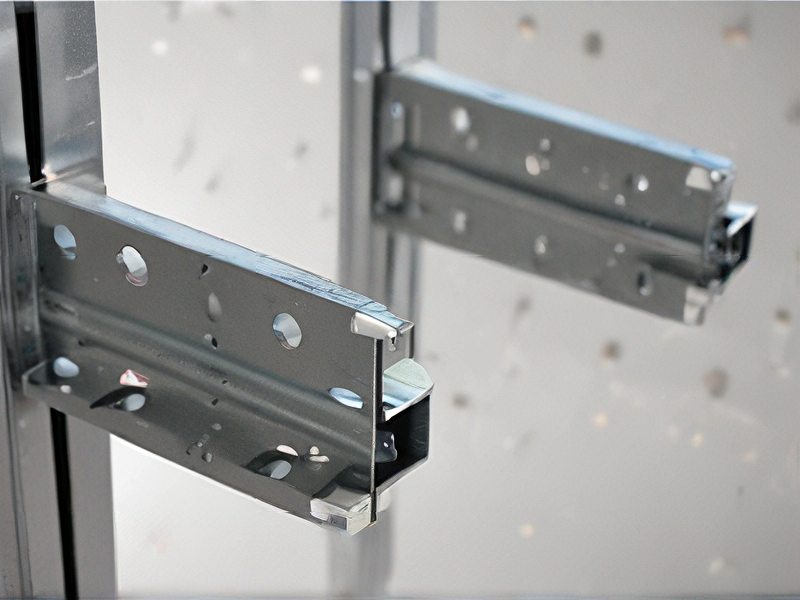
Tips for Procurement and Considerations when Purchasing from metal brackets
When procuring metal brackets, consider the following tips to ensure quality and cost-efficiency:
1. Material Quality: Select brackets made from high-quality metals like stainless steel or aluminum, depending on your specific needs. Stainless steel is durable and resistant to corrosion, making it ideal for outdoor or humid environments, while aluminum is lightweight and suitable for less demanding applications.
2. Supplier Reputation: Choose suppliers with a good track record for reliability and quality. Check reviews, request references, and consider suppliers with industry certifications.
3. Compliance and Standards: Ensure that the metal brackets comply with industry standards and regulations. This guarantees safety, durability, and performance.
4. Customization Options: If your project has unique requirements, look for suppliers that offer customization. Custom brackets can better meet specific design and functional needs.
5. Cost Considerations: While cost is crucial, it should not compromise quality. Compare prices from multiple suppliers and consider the total cost of ownership, including installation and maintenance.
6. Lead Times: Assess the supplier’s lead times to ensure they can meet your project deadlines. Delays can be costly and disruptive.
7. Sample Testing: Request samples before placing a large order. Testing samples can help you verify the quality and fit of the brackets.
8. Bulk Purchasing: For large projects, consider bulk purchasing to negotiate better prices and ensure uniformity in your brackets.
9. Warranty and Support: Choose suppliers that offer warranties and post-purchase support. This can provide peace of mind and reduce risks associated with defects.
10. Sustainability: Consider the environmental impact of your purchase. Opt for suppliers that use sustainable practices and materials.
By focusing on these considerations, you can ensure a successful procurement process for metal brackets, balancing quality, cost, and project requirements.
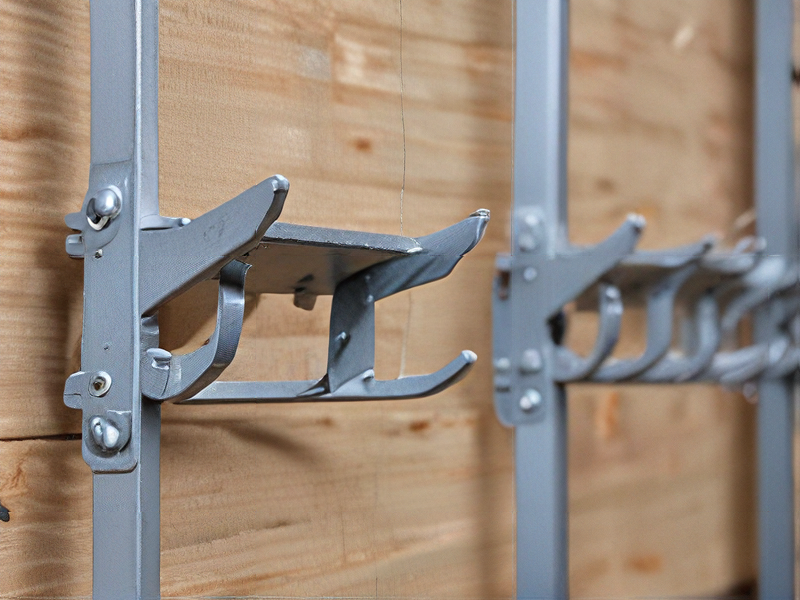
FAQs on Sourcing and Manufacturing from metal brackets in China
FAQs on Sourcing and Manufacturing Metal Brackets in China
1. Why source metal brackets from China?
China offers cost-effective manufacturing, advanced technology, and a vast selection of suppliers. This combination can lead to reduced production costs and access to high-quality products.
2. How do I find reliable suppliers?
Use platforms like Alibaba, Global Sources, and Made-in-China. Attend trade shows such as the Canton Fair and seek recommendations from industry contacts. Verify supplier credentials through certifications like ISO and request samples before making large orders.
3. What should I consider when selecting a supplier?
Check their manufacturing capabilities, quality control processes, lead times, and communication skills. Ensure they can meet your specifications and volume requirements. Visiting the factory can provide a better understanding of their operations.
4. How can I ensure product quality?
Implement rigorous quality control measures, such as pre-production samples, in-line inspections, and final product inspections. Use third-party inspection services to verify compliance with your standards.
5. What are the common challenges in sourcing from China?
Language barriers, cultural differences, and varying quality standards are common challenges. Effective communication, clear contracts, and building a good relationship with your supplier can mitigate these issues.
6. How do I handle logistics and shipping?
Work with experienced freight forwarders to manage shipping and customs clearance. Consider factors like shipping costs, delivery times, and Incoterms (FOB, CIF, etc.) to optimize your logistics strategy.
7. What are the payment terms typically offered?
Common payment terms include 30% deposit before production and 70% balance before shipment. Other options include letters of credit (LC) or escrow services to protect both parties.
8. How can I protect my intellectual property (IP)?
Use non-disclosure agreements (NDAs) and register your patents or trademarks in China. Regularly monitor the market for any infringements and take legal action if necessary.
9. What are the legal considerations?
Ensure your contracts are clear and legally binding. Understand Chinese laws and regulations related to manufacturing, labor, and trade. Consulting with legal experts who specialize in Chinese manufacturing can be beneficial.
By addressing these key points, you can effectively navigate the complexities of sourcing and manufacturing metal brackets in China.
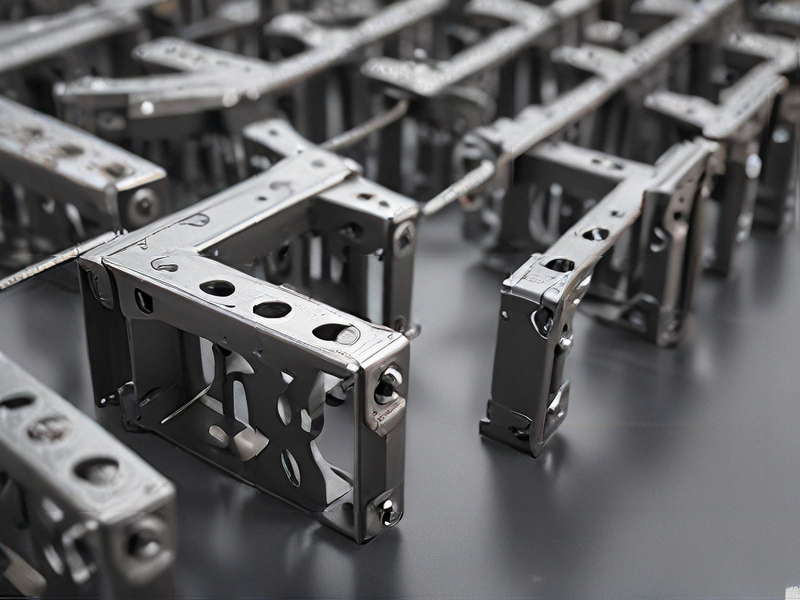