Technology and Applications of metal cutting by laser
Laser cutting is a precise and versatile technology widely used in various industries, including automotive, aerospace, electronics, and manufacturing. This method involves directing a high-powered laser beam to melt, burn, vaporize, or blow away material, leaving a clean and accurate cut.
Technology
1. Types of Lasers:
– CO2 Lasers: Suitable for cutting, boring, and engraving on non-metallic materials and some metals.
– Fiber Lasers: Known for high efficiency and the ability to cut reflective metals such as aluminum, brass, and copper.
– Nd:YAG Lasers: Ideal for high-power applications, including welding and deep engraving.
2. Cutting Process:
– Laser Source: Generates the laser beam.
– Beam Delivery: Optical fibers or mirrors guide the laser to the cutting head.
– Cutting Head: Focuses the laser beam onto the material with a lens.
– Assist Gas: Blows molten material out of the cut, improves cutting quality, and cools the material.
3. Control Systems:
– CNC (Computer Numerical Control): Offers precise control over the laser cutting process, allowing for complex and intricate designs.
Applications
1. Industrial Manufacturing:
– Automotive: Cutting intricate parts like airbags and instrument panels.
– Aerospace: Precision cutting of components like turbine blades and structural parts.
2. Electronics:
– PCB Manufacturing: Cutting and shaping printed circuit boards.
– Microelectronics: Precision cutting of tiny components.
3. Medical Devices:
– Surgical Instruments: Manufacturing precise and intricate instruments.
– Implants: Cutting and shaping medical implants.
4. Jewelry and Art:
– Custom Designs: Creating intricate and personalized jewelry pieces.
– Art Installations: Precise and detailed cutting for artistic expressions.
Laser cutting offers numerous advantages, including high precision, speed, versatility, and the ability to cut a wide range of materials. As technology advances, laser cutting continues to evolve, finding new applications across various industries.

Quality Testing Methods for metal cutting by laser and how to control quality
Quality Testing Methods for Laser Metal Cutting
1. Visual Inspection: Check for smooth, burr-free edges, consistent kerf width, and absence of dross. Imperfections like burns or rough edges indicate issues in laser settings.
2. Dimensional Measurement: Use calipers, micrometers, or coordinate measuring machines (CMM) to ensure cut dimensions meet specified tolerances.
3. Surface Roughness Measurement: Employ profilometers to measure the surface roughness of cut edges. Lower roughness values indicate better quality cuts.
4. Metallurgical Analysis: Conduct microscopic examination and hardness testing to assess heat-affected zones (HAZ) and material integrity.
5. Microhardness Testing: Evaluate changes in hardness around the cut area to detect thermal effects and ensure material properties remain consistent.
6. Tensile Testing: Check the mechanical properties of the cut pieces to ensure they meet the required strength and ductility specifications.
Controlling Quality in Laser Metal Cutting
1. Laser Calibration: Regularly calibrate the laser to maintain optimal focus, power, and speed settings.
2. Material Preparation: Ensure materials are clean and free of contaminants that could affect the cutting process.
3. Monitoring Systems: Implement real-time monitoring systems, such as cameras or sensors, to detect deviations during the cutting process and adjust parameters dynamically.
4. Parameter Optimization: Optimize laser settings (power, speed, gas pressure) for different materials and thicknesses through experimental trials and data analysis.
5. Regular Maintenance: Conduct routine maintenance of the laser equipment to prevent wear and tear, ensuring consistent performance.
6. Training and Skill Development: Ensure operators are well-trained and aware of the best practices and troubleshooting techniques.
7. Quality Audits: Perform regular quality audits and process reviews to identify areas for improvement and implement corrective actions promptly.
By combining these methods and controls, manufacturers can ensure high-quality laser cutting of metals, reducing defects and improving overall production efficiency.
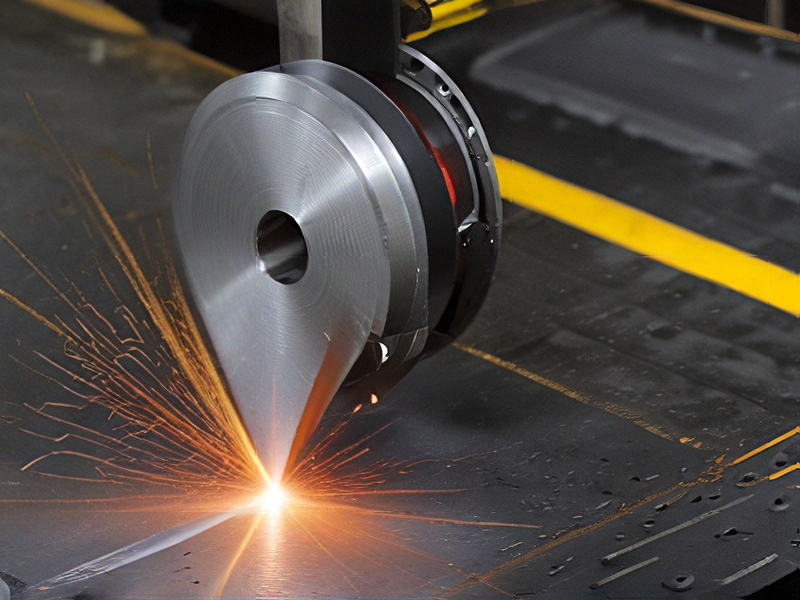
Tips for Procurement and Considerations when Purchasing from metal cutting by laser
When procuring laser-cut metal components, consider the following tips and considerations to ensure quality, cost-efficiency, and timely delivery:
1. Material Selection: Specify the type and grade of metal required. Common choices include stainless steel, aluminum, and carbon steel. Each material has unique properties affecting the cutting process, finish, and durability.
2. Precision and Tolerance: Define the required precision and tolerances. Laser cutting offers high accuracy, but it’s essential to communicate specific requirements to avoid discrepancies.
3. Cutting Speed and Quality: Faster cutting speeds can reduce costs but may affect edge quality. Balance speed with quality requirements based on the application of the components.
4. Design Complexity: Laser cutting allows for intricate designs, but complex shapes may increase costs and production time. Simplify designs where possible to optimize efficiency.
5. Thickness of Material: Thicker materials require more powerful lasers and slower cutting speeds, which can increase costs. Ensure the supplier has the appropriate equipment for the material thickness needed.
6. Supplier Expertise: Choose suppliers with a proven track record in laser cutting. Verify their certifications, capabilities, and experience in handling similar projects.
7. Technology and Equipment: Ensure the supplier uses advanced and well-maintained laser cutting machines. Outdated or poorly maintained equipment can affect quality and turnaround time.
8. Post-Cutting Processes: Consider additional processes such as deburring, finishing, or heat treatment. Clarify whether these services are offered and included in the quote.
9. Volume and Batch Size: Large orders may benefit from economies of scale, but small batches or prototypes might incur higher costs per unit. Discuss batch sizes and potential cost implications with the supplier.
10. Lead Time and Delivery: Confirm lead times and delivery schedules. Reliable suppliers should provide realistic timelines and stick to agreed deadlines to avoid project delays.
By addressing these factors, you can make informed decisions, ensuring the procurement of high-quality laser-cut metal components tailored to your specific needs.

FAQs on Sourcing and Manufacturing from metal cutting by laser in China
FAQs on Sourcing and Manufacturing from Metal Cutting by Laser in China
1. Why choose China for laser metal cutting?
China offers advanced technology, cost-effective labor, and a robust supply chain, making it a preferred choice for laser metal cutting services.
2. What types of metals can be cut by laser in China?
Commonly cut metals include steel, aluminum, brass, copper, and titanium. Specialized facilities can handle a variety of other metals as well.
3. How does the quality of laser cutting in China compare to other countries?
Chinese manufacturers use state-of-the-art laser cutting machines and follow stringent quality control measures, ensuring high precision and quality comparable to global standards.
4. What are the typical lead times for laser cutting projects in China?
Lead times vary based on the complexity and volume of the project. Typical lead times range from a few days to several weeks.
5. How can I ensure the reliability of a Chinese laser cutting service provider?
Verify certifications (e.g., ISO), request samples, review past projects, and seek customer references. Conducting an on-site audit can also be beneficial.
6. What are the cost considerations when sourcing laser cutting services from China?
Costs include material, labor, machine operation, shipping, and tariffs. China generally offers competitive pricing, but it’s crucial to get detailed quotes to avoid hidden costs.
7. Are there any risks associated with sourcing laser cutting services from China?
Risks include communication barriers, quality inconsistencies, and logistical challenges. Mitigate these by working with reputable suppliers and maintaining clear communication.
8. What logistical aspects should be considered?
Consider shipping costs, delivery times, customs clearance, and import regulations. Working with experienced logistics providers can streamline the process.
9. How do I handle intellectual property (IP) protection?
Sign non-disclosure agreements (NDAs) and work with suppliers familiar with international IP laws. Register your IP in China if necessary.
10. Can I visit the manufacturing site in China?
Yes, visiting the site can help build trust and ensure the supplier meets your standards. Many manufacturers welcome site visits from potential clients.
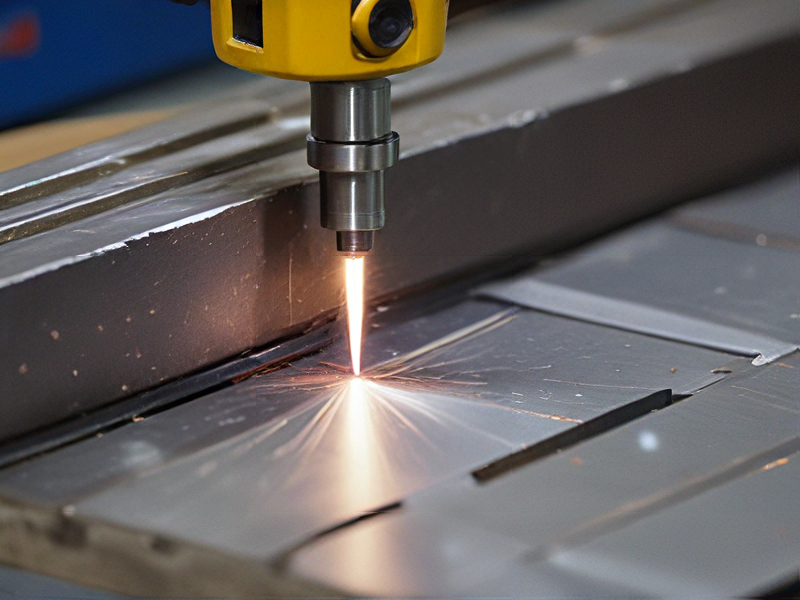