Technology and Applications of metal filer tool
The metal filer tool, an essential instrument in machining and finishing processes, is designed to shape and smooth metal surfaces. It features a hardened steel blade with teeth cut into its surface, allowing for effective material removal. Metal filers come in various shapes and sizes, including flat, round, half-round, and triangular, each suited for specific tasks and contours.
Applications:
1. Machining and Fabrication: In metalworking, filers are used for precision shaping and finishing of components, ensuring desired dimensions and surface quality. They remove burrs and sharp edges left by other machining processes.
2. Prototype Development: Filers play a critical role in prototype fabrication, enabling designers to refine parts quickly by hand, especially in low-volume production.
3. Repair Work: Technicians use metal filers to smooth out worn or damaged metal parts, ensuring they fit correctly and function optimally.
4. Jewelry Making: In jewelry production, filers help artists create intricate designs and smooth finishes on metal pieces, enhancing aesthetic appeal.
5. Automotive and Aerospace: In these industries, filers are essential for refining component fit and function, often applied in assembly processes for precision parts.
Advantages:
– Versatility: Metal filers can handle various metal types, making them a go-to tool across multiple industries.
– Control: The manual operation allows for fine control over the material removal process, ideal for intricate work.
– Cost-Effective: They are relatively inexpensive and easy to use, making them accessible for hobbyists and professionals alike.
In summary, the metal filer tool is a vital instrument in various sectors, combining functionality with precision to enhance metalworking processes.
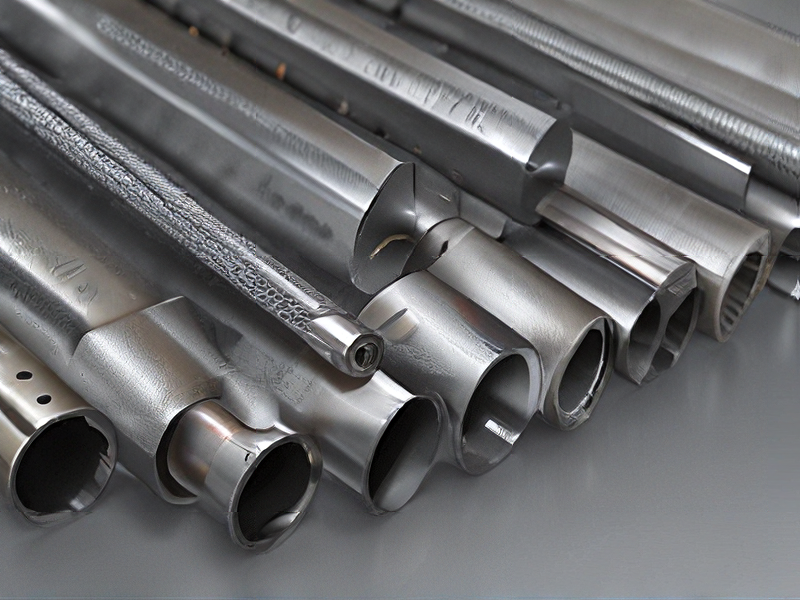
Quality Testing Methods for metal filer tool and how to control quality
Quality testing for metal filler tools involves several key methods to ensure durability, performance, and safety. Here are some effective testing methods and quality control measures:
Testing Methods:
1. Visual Inspection: Check for surface defects such as cracks, rust, or improper finishes. This initial assessment helps identify obvious manufacturing flaws.
2. Dimensional Verification: Use calipers and gauges to measure the tool against specified dimensions. Accurate measurements are crucial for correct fitting and function.
3. Material Analysis: Conduct chemical composition analysis through spectrometry to ensure the metal’s properties meet required standards. This can include testing for tensile strength and hardness.
4. Functional Testing: Test the tool under simulated operational conditions to evaluate performance. This includes checking its flexibility, ease of use, and effectiveness in filling applications.
5. Fatigue Testing: Apply cyclic loads to assess the tool’s durability over repeated use. This highlights any potential failures that could arise during its lifecycle.
Quality Control Measures:
1. Standard Operating Procedures (SOPs): Develop and enforce SOPs for manufacturing and testing processes. This ensures consistency and adherence to quality standards.
2. Statistical Process Control (SPC): Implement SPC techniques to monitor production processes. This helps identify any variations that may lead to defects.
3. Training and Certification: Ensure that staff are trained in quality control methodologies. Certification programs can enhance knowledge and skill levels in quality assurance practices.
4. Supplier Quality Management: Collaborate closely with suppliers to ensure the materials used meet quality requirements. Regular audits and assessments can help maintain standards.
5. Feedback Mechanism: Establish channels for receiving feedback from users to identify areas for improvement. Continuous improvement should be a core focus.
By integrating these methods and measures, manufacturers can effectively control the quality of metal filler tools, minimizing defects and enhancing product reliability.
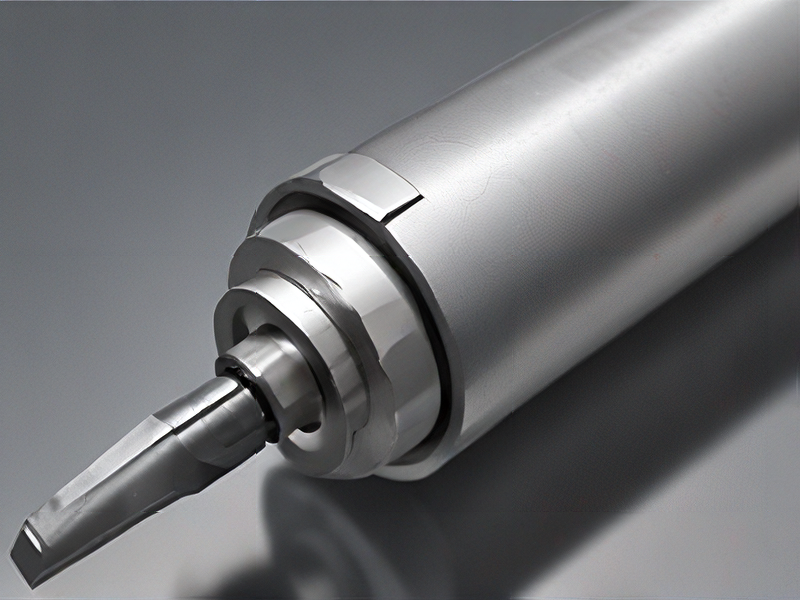
Tips for Procurement and Considerations when Purchasing from metal filer tool
When procuring metal filer tools, consider the following tips and factors to ensure you make the right choice:
1. Analyze Requirements: Determine the specific applications and materials the tool will be used for. Different projects may require different types and grades of metal filers.
2. Quality Assurance: Always opt for reputable suppliers known for their quality. Check for certifications or industry standards that the product meets.
3. Materials and Construction: Look for metal filers made from durable materials such as high-carbon steel or alloy. Consider the construction technique, as well-made tools will last longer and perform better.
4. Type of Filer: Familiarize yourself with the various types of metal filers (e.g., flat, half-round, round) to select the one best suited for your tasks.
5. Ergonomics: Choose tools that are comfortable to use. An ergonomic handle can prevent fatigue during prolonged usage.
6. Cost vs. Value: While it’s important to stay within budget, the cheapest option isn’t always the best. Consider long-term use, performance, and maintenance costs.
7. Supplier Reputation: Research and read reviews about potential suppliers. Good customer service and a robust return policy are also essential.
8. Bulk Purchasing: If you require multiple tools, consider buying in bulk, which might offer cost savings and ensure consistency in quality.
9. Warranty and Support: A solid warranty can provide peace of mind. Check if the supplier offers support or replacement options.
10. Sustainability: If environmental impact is a concern, assess the sustainability practices of the manufacturer.
Making an informed decision through careful assessment of these considerations will help ensure you are satisfied with your metal filer tools.
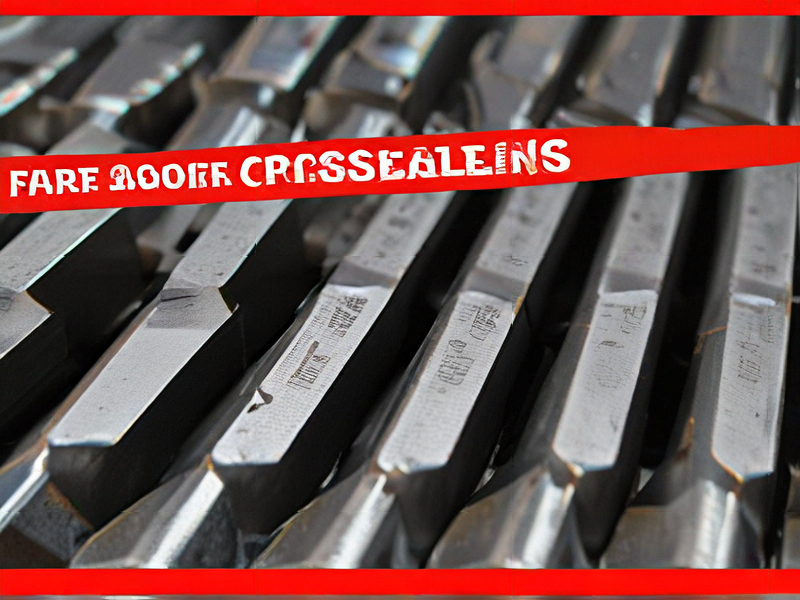
FAQs on Sourcing and Manufacturing from metal filer tool in China
FAQs on Sourcing and Manufacturing Metal Filter Tools in China
1. Why source metal filter tools from China?
China offers competitive pricing, a wide range of manufacturers, and advanced production capabilities. Its established supply chains and expertise in metal fabrication make it an attractive option for sourcing.
2. How do I find reliable suppliers?
Utilize platforms like Alibaba or Global Sources to identify manufacturers. Check reviews, ask for references, and verify their business credentials. Attending trade shows can also facilitate direct connections.
3. What are the key factors to consider when selecting a manufacturer?
Evaluate quality certifications (ISO, CE), production capacity, lead times, and communication effectiveness. Request samples before committing to large orders to assess quality.
4. How can I ensure product quality?
Implement a quality control process by setting clear specifications, conducting factory audits, and hiring third-party inspection services. Regular communication with the manufacturer can also help maintain standards.
5. What are typical lead times for production?
Lead times can vary widely, typically ranging from 4 to 12 weeks, depending on order size and complexity. Discuss timelines upfront to avoid delays.
6. What payment terms are common?
Common payment methods include T/T (bank transfer), L/C (letter of credit), or PayPal for smaller orders. It’s wise to negotiate terms upfront to protect both parties.
7. How do I handle shipping and logistics?
Consider working with a freight forwarder to manage shipping logistics. Factor in duties, taxes, and potential tariffs when planning your budget.
8. What should I know about intellectual property?
Register relevant trademarks and patents before engaging with manufacturers. Use non-disclosure agreements (NDAs) to protect proprietary designs and processes.
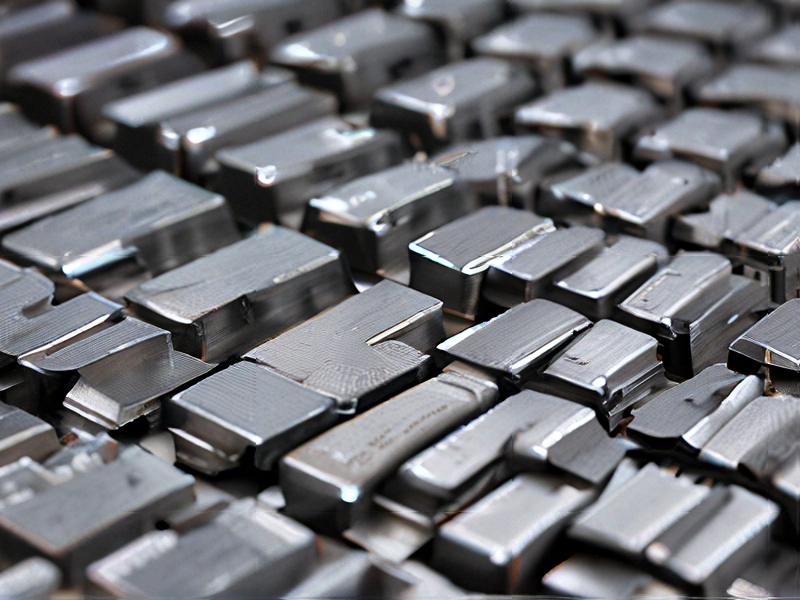