Technology and Applications of metal for 3d printer
Metal 3D printing, also known as additive manufacturing, has rapidly evolved with various technologies and applications transforming industries like aerospace, automotive, and healthcare. The primary methods include Selective Laser Melting (SLM), Direct Metal Laser Sintering (DMLS), and Electron Beam Melting (EBM).
In SLM and DMLS, a high-powered laser fuses metal powder layer by layer to create complex geometries with high precision. These technologies are ideal for producing intricate components that traditional methods struggle with, such as lightweight structures with internal cooling channels in aerospace engines.
EBM employs an electron beam in a vacuum to melt metal powder, making it highly suitable for titanium and its alloys, particularly in the aerospace industry for components that demand high strength-to-weight ratios.
Application-wise, metal 3D printing is used to manufacture tooling, prototypes, and end-use parts. In the medical field, custom implants and prosthetics can be tailored specifically to patient anatomy. Automotive companies leverage metal printing for lightweight components that enhance fuel efficiency and performance.
Moreover, advancements in binder jetting technology enable the production of metal parts with minimal residual stress and improved surface finish. With ongoing improvements in speed, material diversity, and print quality, metal 3D printing is set to revolutionize manufacturing processes, reducing waste and lead times while fostering innovation.
Overall, the integration of metal 3D printing presents transformative opportunities across sectors, facilitating design freedom and enhancing product performance.
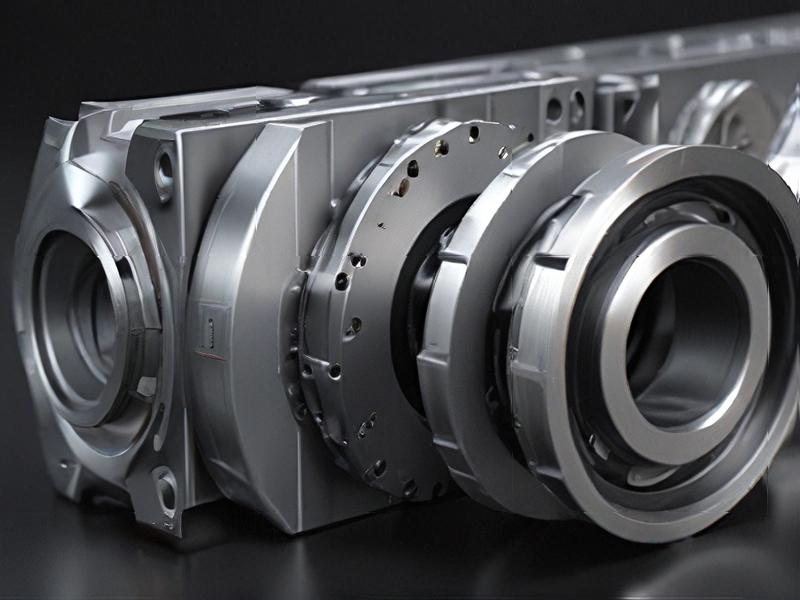
Quality Testing Methods for metal for 3d printer and how to control quality
Quality testing for metal 3D printed parts is essential to ensure mechanical performance, structural integrity, and durability. Here are key methods and control strategies:
1. Visual Inspection: Routine visual checks can identify surface defects, layer misalignments, and dimensional inaccuracies.
2. Dimensional Measurement: Use calipers and CMMs (Coordinate Measuring Machines) for precise verification of dimensions against CAD specifications.
3. Non-Destructive Testing (NDT): Techniques like ultrasonic testing (UT) and X-ray computed tomography (CT) can detect internal flaws without damaging the part.
4. Mechanical Testing: Conduct tensile, compression, and hardness tests. These assess material properties and ensure they meet required specifications.
5. Microstructural Analysis: Employ metallography to analyze grain structure and phase distribution, which can influence strength and fatigue resistance.
6. Post-processing Inspection: Evaluate parts after processes like heat treatment and surface finishing to ensure desired mechanical properties and surface quality.
Quality Control Strategies:
1. Material Certification: Ensure all metal powders or feedstock are sourced from certified suppliers with traceability.
2. Process Monitoring: Implement real-time monitoring of the printing process using sensors to track variables like temperature, speed, and laser/power settings.
3. Standard Operating Procedures (SOPs): Develop and follow SOPs for each phase of the 3D printing process, from setup to post-processing.
4. Statistical Quality Control (SQC): Use statistical methods to analyze data from testing phases, identifying trends, and controlling variability.
5. Feedback Loops: Create mechanisms for continuous feedback and adjustment based on testing results to improve future prints.
By employing these methods and controls, manufacturers can ensure the production of high-quality metal parts through 3D printing.
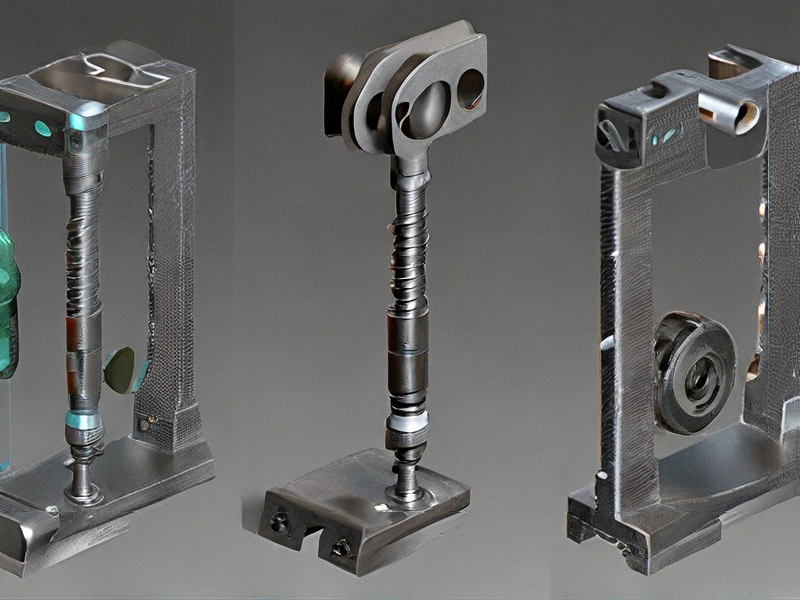
Tips for Procurement and Considerations when Purchasing from metal for 3d printer
When procuring metal for 3D printing, consider the following tips and factors:
1. Material Selection: Choose the right metal based on the application. Common options include titanium, aluminum, stainless steel, and cobalt-chrome. Each has distinct properties like strength, weight, and corrosion resistance.
2. Supplier Reliability: Research potential suppliers. Look for reputable companies with experience in metal 3D printing. Customer reviews and certifications (like ISO standards) can indicate quality and reliability.
3. Material Specifications: Ensure the metal powder meets the specifications for your 3D printer. Pay attention to particle size distribution, morphology, and flowability, as these will affect print quality and performance.
4. Batch Consistency: Check for consistency between batches, as variations can impact the mechanical properties and overall quality of printed parts.
5. Cost vs. Quality: Balance cost with the quality of metal. While cheaper options may be tempting, they can lead to poor print quality and additional costs in post-processing.
6. Post-Processing Requirements: Understand the post-processing needs of the metal you choose. Some metals may require heat treatment or surface finishing, which could increase overall project time and costs.
7. Sustainability and Recycling: Consider suppliers who focus on sustainable practices. Metal powders can often be recycled, reducing waste and environmental impact.
8. Documentation and Compliance: Ensure that the supplier provides technical data sheets, certifications, and compliance with industry standards, especially for critical applications like aerospace or medical.
By carefully evaluating these factors, you can optimize your procurement process and ensure successful 3D printing outcomes with metal materials.
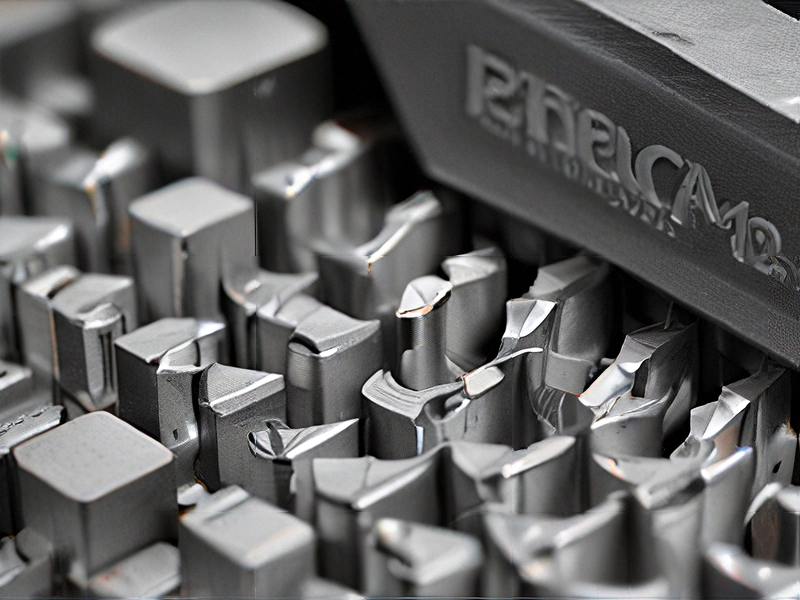
FAQs on Sourcing and Manufacturing from metal for 3d printer in China
FAQs on Sourcing and Manufacturing Metal for 3D Printers in China
1. What types of metal can be sourced for 3D printing in China?
Common metals include stainless steel, aluminum, titanium, and cobalt-chrome. Each material offers unique properties suitable for various applications.
2. How do I choose a reliable supplier?
Research potential suppliers by checking their certifications (like ISO 9001), customer reviews, and previous projects. Request samples to evaluate quality.
3. What are the typical lead times for sourcing metal?
Lead times vary but generally range from 2 to 8 weeks, depending on the material, complexity, and supplier capacity.
4. Are there minimum order quantities (MOQs)?
Yes, most suppliers have MOQs, typically ranging from 50 to 500 kg, depending on the metal type and specific requirements.
5. How can I ensure quality during manufacturing?
Establish clear quality control standards, conduct regular inspections, and use third-party quality assurance services to verify compliance.
6. What are the shipping options available?
Shipping methods include air freight for quicker delivery and sea freight for cost-effectiveness. Choose based on your timeline and budget.
7. Are there import duties or taxes to consider?
Yes, check with your country’s customs regulations regarding import duties and taxes to avoid unexpected costs.
8. How do I handle intellectual property (IP) concerns?
Draft NDAs and contracts carefully to protect your designs. Consider working with suppliers who have a good reputation for respecting IP rights.
9. What additional services do suppliers offer?
Many suppliers provide post-processing services, including machining, heat treatment, and surface finishing, to enhance the final product’s quality.
10. Can I visit the manufacturing facility?
Yes, if feasible, visiting the factory provides insight into their operations and quality control processes. Otherwise, request virtual tours or video calls.
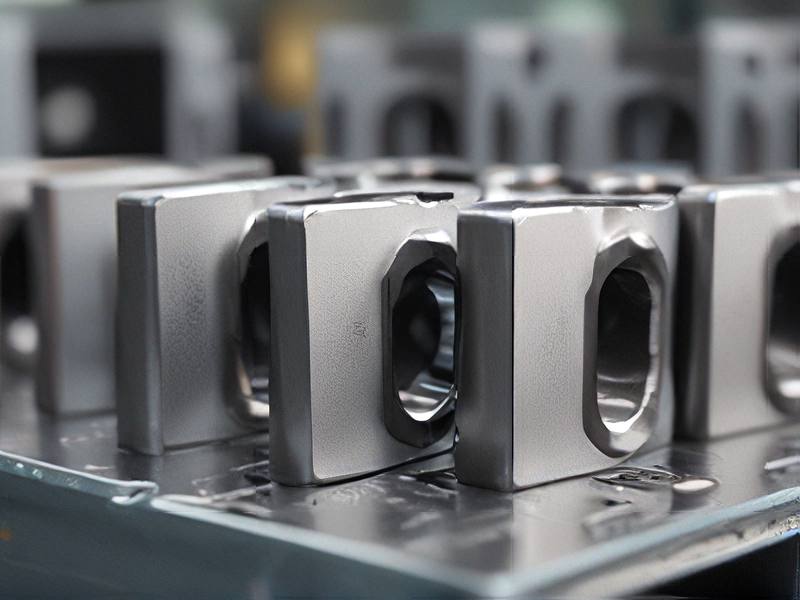