Technology and Applications of metal in stainless steel
Stainless steel is a versatile alloy primarily composed of iron, chromium, and nickel, designed to resist corrosion and oxidation. The critical technology behind stainless steel involves the precise control of its composition and the use of various alloying elements that enhance its properties. The chromium content, generally at least 10.5%, forms a passive layer of chromium oxide on the surface, which protects the underlying metal from rusting and staining.
Various grades of stainless steel exist, each tailored for specific applications. Ferritic stainless steels, for instance, are magnetic and offer good corrosion resistance but low ductility, making them suitable for automotive applications and kitchenware. Austenitic stainless steels, the most common type, are non-magnetic and exhibit excellent toughness and weldability. They are widely used in food processing, medical devices, and architectural applications due to their aesthetic appeal and resistance to extreme temperatures.
The application of stainless steel spans numerous industries. In the food and beverage sector, it’s utilized for equipment like tanks, pipes, and utensils, ensuring hygiene and longevity. In construction, stainless steel provides strength and durability for structural components and facades. In the medical field, its biocompatibility makes it ideal for instruments and implants.
Advancements in technology, such as 3D printing and improved welding techniques, continue to expand the applications of stainless steel, fostering innovations in design and functionality. The recycling of stainless steel is also noteworthy, as it is fully recyclable without losing its properties, making it an environmentally friendly choice. Overall, stainless steel’s unique combination of strength, corrosion resistance, and aesthetic value underscores its importance across various industries.
Quality Testing Methods for metal in stainless steel and how to control quality
Quality testing methods for stainless steel are essential to ensure its integrity and performance in various applications. Here are some key methods and control practices:
1. Visual Inspection: Initial checks for surface defects such as cracks, pits, or discoloration. This method is quick and helps identify obvious flaws.
2. Mechanical Testing:
– Tensile Testing assesses yield strength, ultimate tensile strength, and elongation.
– Hardness Testing (e.g., Rockwell, Brinell) evaluates material hardness, which correlates with strength.
3. Metallographic Analysis: Involves microscopic examination of the microstructure to identify grain size, phase distribution, and inclusion content, ensuring the stainless steel’s composition is appropriate for its intended use.
4. Chemical Composition Testing: Techniques such as X-ray fluorescence (XRF) or optical emission spectrometry (OES) are used to verify the elemental composition, ensuring compliance with specifications (e.g., ASTM, ISO).
5. Non-Destructive Testing (NDT):
– Ultrasonic Testing (UT) detects internal flaws, ensuring structural integrity without damaging the material.
– Magnetic Particle Inspection (MPI) identifies surface and near-surface defects in ferromagnetic stainless steel.
6. Corrosion Testing: Methods like salt spray testing determine the material’s resistance to corrosion in aggressive environments.
Quality Control Measures:
– Standard Operating Procedures (SOPs): Implementing SOPs for testing and inspections helps ensure consistency.
– Regular Calibration: Ensuring that testing equipment is properly calibrated to maintain accuracy.
– Training and Certification: Providing ongoing training for personnel conducting quality tests to uphold testing standards.
– Traceability: Maintaining records of material batches and test results aids in tracking quality performance over time.
By utilizing these testing methods and control measures, manufacturers can ensure the quality and reliability of stainless steel products.
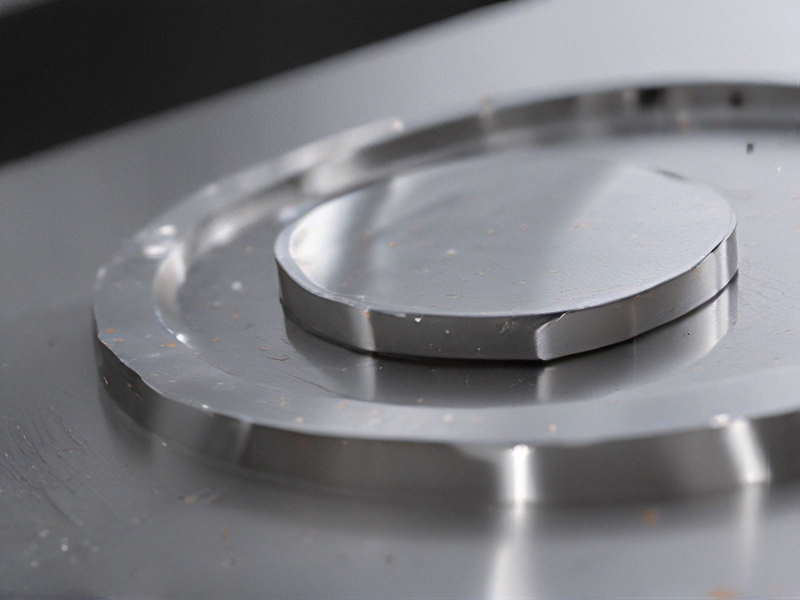
Tips for Procurement and Considerations when Purchasing from metal in stainless steel
When procuring stainless steel, several key tips and considerations can ensure a successful purchase:
1. Identify Grades: Stainless steel comes in various grades (e.g., 304, 316) which exhibit different properties such as corrosion resistance and tensile strength. Determine the appropriate grade based on environmental conditions, chemical exposure, and mechanical requirements.
2. Supplier Quality: Choose suppliers with a solid reputation. Look for those certified by recognized standards (e.g., ISO, ASTM) to ensure product quality. Request material certifications to verify the grade and properties of the stainless steel.
3. Quantity and Size Specifications: Clearly define the quantities and dimensions required. This minimizes waste and ensures that the material procured meets project specifications.
4. Pricing: Compare prices from multiple suppliers but balance cost with quality. The cheapest option may compromise quality and durability, leading to higher long-term costs.
5. Delivery Timeframe: Confirm lead times and ensure they align with project timelines. Late deliveries can disrupt schedules, so establish clear agreements on delivery dates.
6. Finished Specifications: Consider whether you need additional services such as cutting, welding, or surface finishing. Clarifying these needs upfront can save time and money.
7. Customer Support: A good supplier should offer support in case of questions or issues during the procurement process. Strong communication can facilitate smoother transactions.
8. Environmental Considerations: Look for suppliers that practice sustainable sourcing and environmentally friendly manufacturing processes.
By following these tips, you can optimize your procurement process, ensuring you get high-quality stainless steel that meets your project’s requirements effectively.
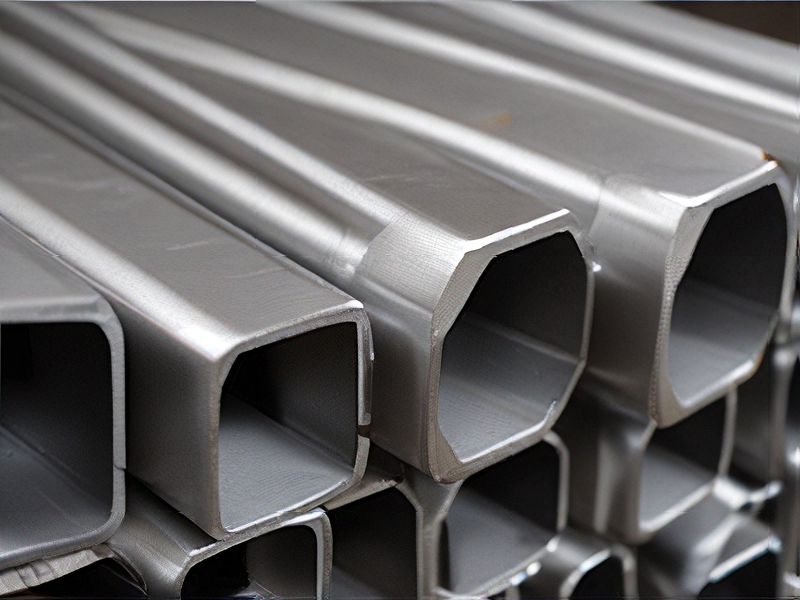
FAQs on Sourcing and Manufacturing from metal in stainless steel in China
FAQs on Sourcing and Manufacturing Stainless Steel Products in China
1. Why choose China for stainless steel manufacturing?
China offers cost-effective pricing, advanced manufacturing technologies, and a vast network of suppliers. It is one of the largest producers of stainless steel and has extensive experience in various industries.
2. What types of stainless steel products can be sourced?
You can source a wide range of stainless steel products, including kitchenware, industrial components, medical instruments, automotive parts, and custom fabrication.
3. How do I find reliable suppliers?
Utilize platforms such as Alibaba, Made-in-China, or Global Sources to connect with suppliers. Always verify their credentials through reviews, certifications, and factory visits if possible.
4. What is the typical lead time for manufacturing?
Lead times vary based on order complexity and quantity. Generally, it can range from 4 to 12 weeks. Discuss timelines with the supplier before placing an order.
5. Are there quality control measures in place?
Yes, implement quality control practices such as pre-production samples, in-line inspections, and final product checks. Consider hiring a third-party inspection service for added assurance.
6. What are common payment terms?
Payment terms typically include a deposit (usually 30-50%) upfront, with the balance paid before shipment. Using secure payment methods like PayPal or letters of credit is advisable.
7. How do I handle shipping and customs?
Work with your supplier to arrange shipping. Familiarize yourself with customs regulations and duties in your country to avoid unexpected costs.
8. What certifications should I expect?
Ensure your supplier provides relevant certifications such as ISO 9001, ASTM standards for materials, and other industry-specific certifications, depending on your product use.
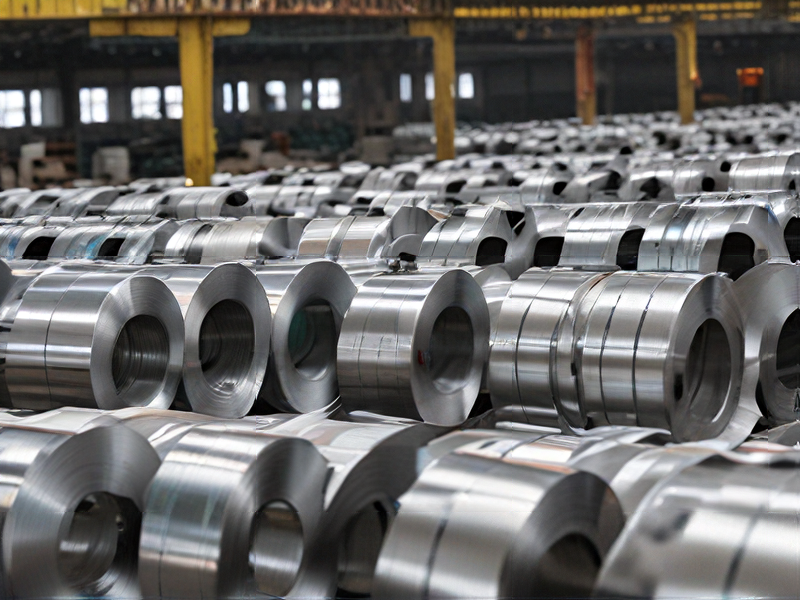