Technology and Applications of metal inj
Metal injection molding (MIM) is a sophisticated technology that integrates traditional powder metallurgy with injection molding processes to produce complex metal parts with high precision and efficiency. By combining fine metal powders with a binder material, MIM allows for the creation of intricate geometries that cannot be achieved through conventional machining methods.
The MIM process involves several key stages: mixing metal powders with a thermoplastic binder, injection molding the mixture into a mold, and then removing the binder through debinding, followed by sintering, where the metal powders fuse together at high temperatures. This process results in dense, high-strength components that retain the desired properties of the metal.
Applications of MIM span various industries, including automotive, aerospace, medical, and consumer electronics. In the automotive sector, MIM is used to create precision gears, connectors, and valve components that enhance performance and reduce weight. In aerospace, it enables the production of lightweight yet durable parts, optimizing fuel efficiency. Medical devices, such as surgical instruments and implants, benefit from MIM’s ability to produce biocompatible components with exceptional accuracy.
Furthermore, consumer electronics leverage MIM for producing small, complex engine parts, enhancing both functionality and aesthetics. The technology is particularly advantageous for producing high volumes of parts at lower costs, making it an attractive option for manufacturers.
In summary, metal injection molding is a cutting-edge technology that offers significant advantages in producing complex metal parts across various industries, combining efficiency, precision, and cost-effectiveness.
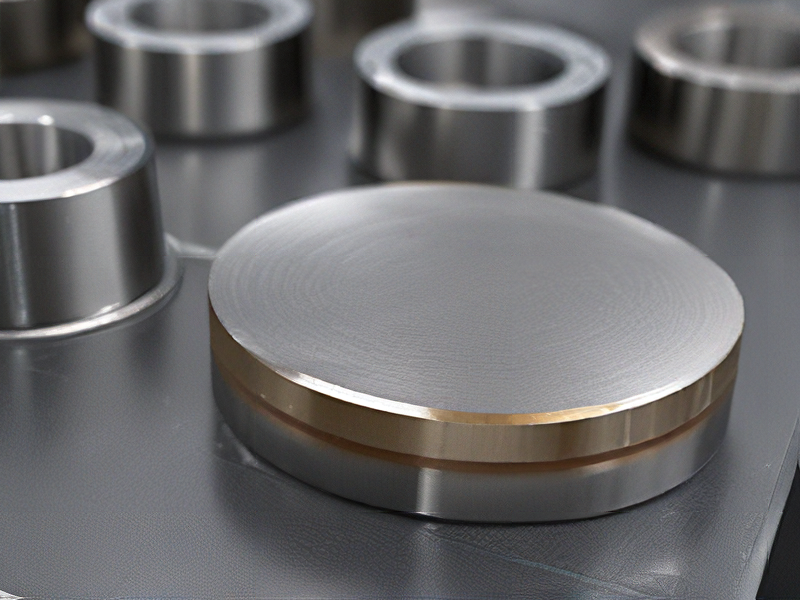
Quality Testing Methods for metal inj and how to control quality
Quality testing methods for metal injection molding (MIM) are crucial for ensuring the integrity and performance of the final products. Here are some key methods:
1. Dimensional Inspection: This involves measuring the physical dimensions of parts using calipers, micrometers, and coordinate measuring machines (CMM). Ensuring that dimensions adhere to specified tolerances is fundamental.
2. Visual Inspection: Surface quality is assessed through visual examination. This checks for defects such as porosity, cracks, or surface roughness.
3. Mechanical Testing: Tests such as tensile, hardness, and impact tests ascertain the mechanical properties of the material. This ensures that the injected metal can withstand operational stresses.
4. Microstructural Analysis: Metallographic techniques involve examining the microstructure through optical or electron microscopy. This helps in understanding grain structure, phase distribution, and identifying impurities.
5. Non-Destructive Testing (NDT): Methods such as X-ray, ultrasonic testing, and dye penetrant tests can identify internal defects without damaging the sample.
To control quality in MIM, several strategies should be implemented:
– Process Control: Regular monitoring of parameters such as temperature, pressure, and time during the injection process ensures consistency. Statistical Process Control (SPC) can help identify deviations early.
– Material Control: Using high-purity powders and ensuring proper handling and storage can prevent contamination.
– Standard Operating Procedures (SOPs): Documenting and adhering to SOPs for every step of production secures a repeatable process, helping to minimize variability.
– Training and Involvement: Educating staff on quality standards and involving them in quality assurance activities cultivates a culture of quality throughout the organization.
Incorporating these testing methods and control measures can significantly enhance the reliability and performance of metal injection molded parts.
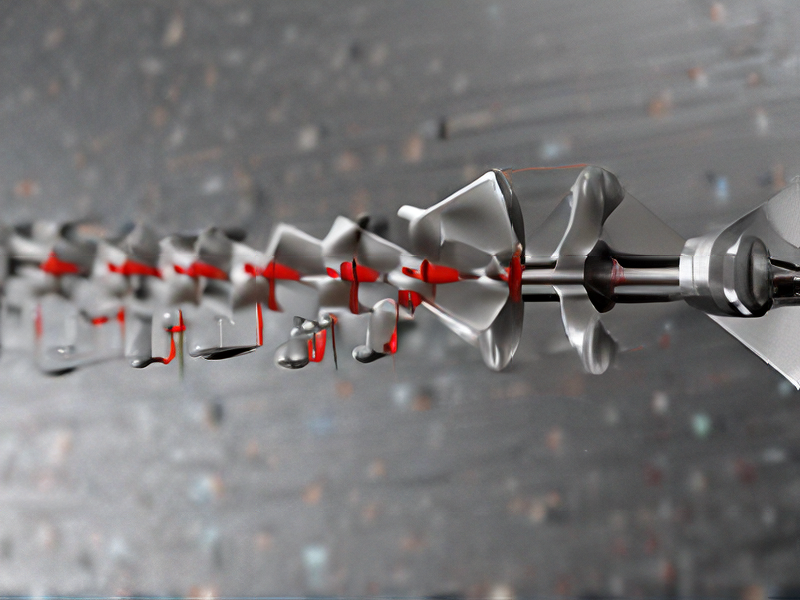
Tips for Procurement and Considerations when Purchasing from metal inj
When purchasing from metal injection molding (MIM) suppliers, consider the following tips and considerations to ensure a successful procurement process:
1. Supplier Expertise: Look for suppliers with proven expertise in MIM. Assess their experience in producing similar components and their technical capabilities.
2. Material Selection: Verify the range of metal powders available. The choice of material significantly impacts the performance and cost of your final product. Ensure the supplier can meet specific industry standards.
3. Quality Control: Request information about the supplier’s quality assurance processes. Certifications such as ISO 9001 or IATF 16949 indicate robust quality management systems.
4. Production Capacity: Evaluate the supplier’s production capabilities to ensure they can meet your volume requirements, whether for prototyping or large-scale production.
5. Cost Structure: Obtain detailed quotes, considering not only unit price but also tooling costs, lead times, and potential discounts for larger orders. Understanding the full cost landscape will aid in budgeting.
6. Lead Times: Confirm the anticipated lead times for both prototypes and full production runs. Efficient suppliers should provide transparent timelines.
7. Design Support: Seek suppliers who offer design assistance. They may provide insights on optimizing designs for MIM, potentially reducing costs and improving manufacturability.
8. Communication: Establish clear channels of communication. Regular updates on progress, issues, or changes can be critical to the success of your project.
9. Logistics and Delivery: Discuss logistics to ensure timely delivery. Understand any potential shipping challenges that could affect timelines.
10. References and Case Studies: Request references or case studies of past projects similar to yours to gauge the supplier’s reliability and quality.
By carefully considering these factors, you can enhance your procurement process in metal injection molding.
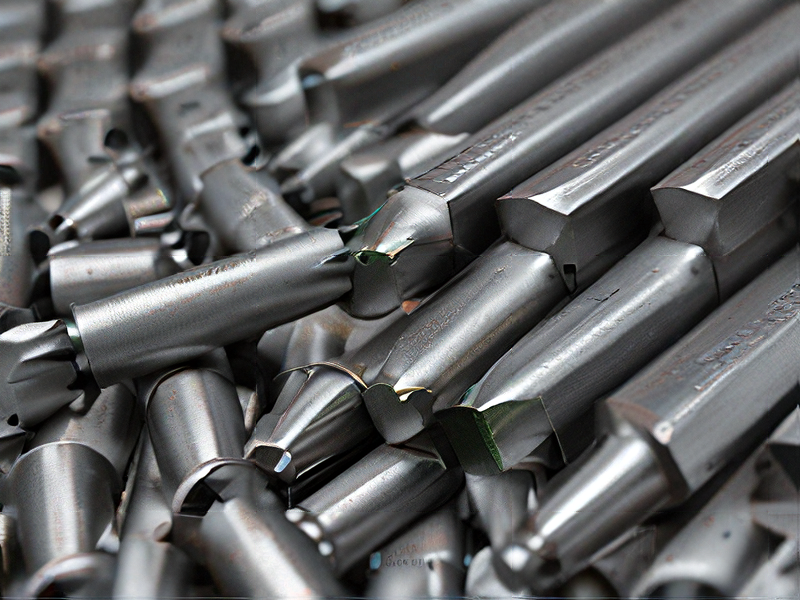
FAQs on Sourcing and Manufacturing from metal inj in China
FAQs on Sourcing and Manufacturing Metal Injection Molding (MIM) in China
1. What is Metal Injection Molding (MIM)?
MIM is a manufacturing process that combines the versatility of plastic injection molding with the benefits of powder metallurgy. It is used to produce complex, high-precision metal parts efficiently.
2. Why source MIM parts from China?
China offers competitive pricing, a vast range of materials, advanced manufacturing technology, and experienced suppliers. The scale of production capabilities allows for economies of scale, making it cost-effective for large volumes.
3. How do I find reliable MIM suppliers in China?
Start by researching online platforms such as Alibaba or Made-in-China, and attend trade fairs like the Canton Fair. Conduct due diligence by checking supplier certifications, reviews, and previous projects.
4. What are the typical lead times for MIM parts?
Lead times can vary based on complexity and batch size, typically ranging from 4 to 12 weeks for production after design finalization. It’s crucial to communicate timelines upfront with suppliers.
5. How is quality assurance managed?
Quality assurance includes pre-production samples, in-process quality checks, and final inspections. Ensure your supplier follows international quality standards, such as ISO 9001.
6. What materials can be used in MIM?
Common materials include stainless steel, titanium, nickel-based alloys, and cobalt. The choice depends on the application and required mechanical properties.
7. Are there any minimum order quantities (MOQs)?
Most suppliers have MOQs, which can range from a few hundred to several thousand pieces, depending on the complexity and material used.
8. What are the shipping options from China?
Shipping can be by air or sea, with air being faster and more expensive, while sea is cost-effective but slower. Discuss preferences with your supplier based on urgency and budget.
By understanding these aspects, you can effectively navigate the MIM sourcing process in China.
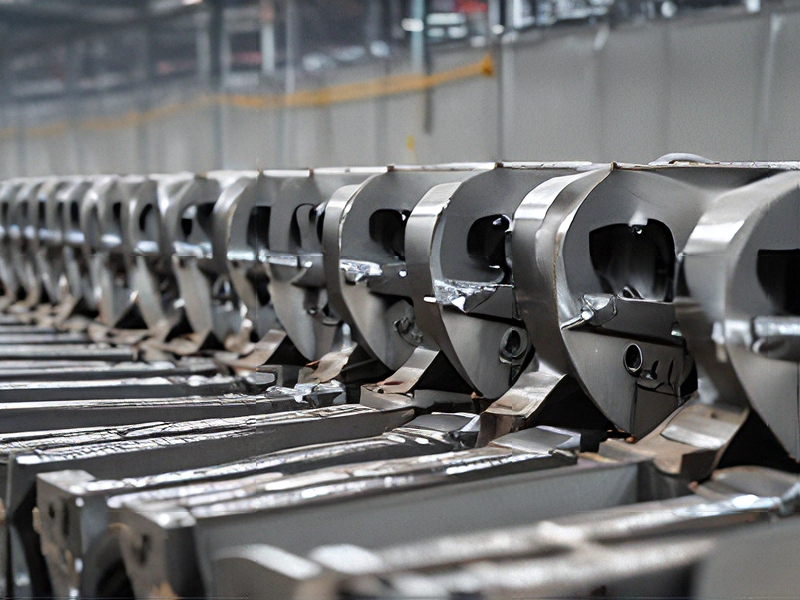