Technology and Applications of metal laser engraver machine
Metal laser engraving machines utilize laser beams to etch designs, text, or patterns onto various metal surfaces. These machines employ high-powered lasers, typically fiber lasers, which are well-suited for marking and engraving metals due to their precision and efficiency. Here are some key aspects and applications:
1. Precision and Versatility: Metal laser engravers offer high precision, allowing for intricate designs and fine details on metals such as stainless steel, aluminum, brass, and titanium. They can mark serial numbers, logos, barcodes, and decorative patterns with consistent quality.
2. Durability and Marking Quality: Laser engraving provides permanent markings that are resistant to wear, corrosion, and fading. This durability makes it ideal for industries requiring long-lasting identification marks, such as aerospace, automotive, and medical devices.
3. Speed and Efficiency: Compared to traditional methods like mechanical engraving, laser engraving is faster and more efficient. It reduces production time and allows for quick customization and on-demand marking.
4. Non-contact Process: Laser engraving is a non-contact process, meaning there is no physical tooling that wears out over time. This reduces maintenance costs and ensures consistent quality over the machine’s lifespan.
5. Wide Range of Applications: Beyond industrial uses, metal laser engravers are also employed in artistic and personalized engraving applications. They can create custom jewelry, personalized gifts, and architectural signage with intricate designs that traditional methods cannot easily replicate.
6. Environmental Considerations: Laser engraving produces minimal waste and consumes less energy compared to traditional methods, making it a more environmentally friendly option.
Overall, metal laser engraving machines combine advanced technology with versatility, offering precise and durable marking solutions across various industries and applications.
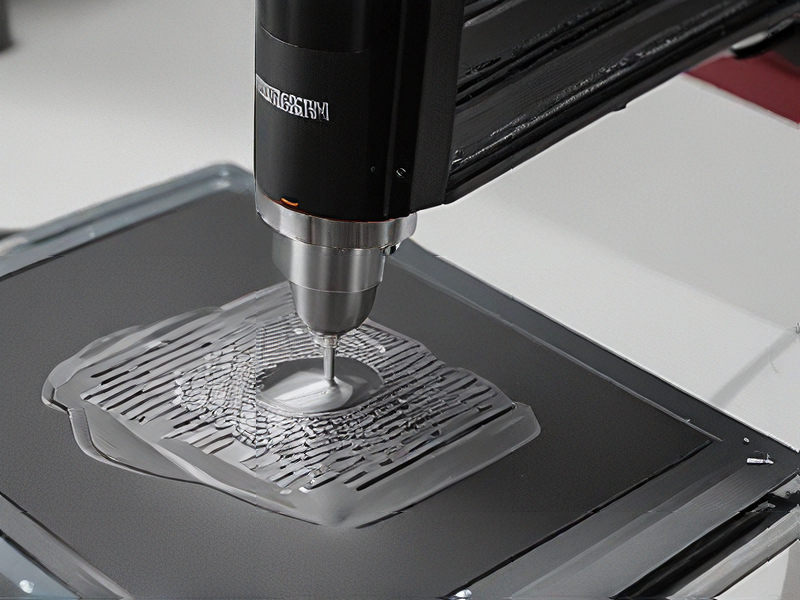
Quality Testing Methods for metal laser engraver machine and how to control quality
Ensuring quality in a metal laser engraver machine involves several key methods:
1. Initial Inspection: Conduct thorough checks during manufacturing to verify all components meet specifications and are defect-free.
2. Performance Testing: Perform functional tests to ensure the machine operates correctly under various conditions, such as different materials and settings.
3. Accuracy Verification: Use precision measurement tools to verify the accuracy of engraving depth, dimensions, and alignment of the laser beam.
4. Durability Testing: Subject the machine to continuous operation tests to evaluate its longevity and robustness under normal usage conditions.
5. Material Compatibility Testing: Test the machine’s ability to engrave different types of metals and materials commonly used in industrial applications.
To control quality effectively:
1. Documented Processes: Establish clear procedures for assembly, testing, and inspection to ensure consistency.
2. Quality Checks: Implement regular checkpoints throughout manufacturing to catch any deviations early.
3. Training: Provide training for operators and inspectors on quality standards and procedures.
4. Feedback Loop: Implement a feedback system to incorporate lessons learned from quality issues into continuous improvement processes.
5. Supplier Quality Assurance: Ensure that components sourced from suppliers meet defined quality standards through audits and inspections.
By integrating these methods and controls, manufacturers can maintain high standards of quality in metal laser engraver machines, ensuring reliability and customer satisfaction.
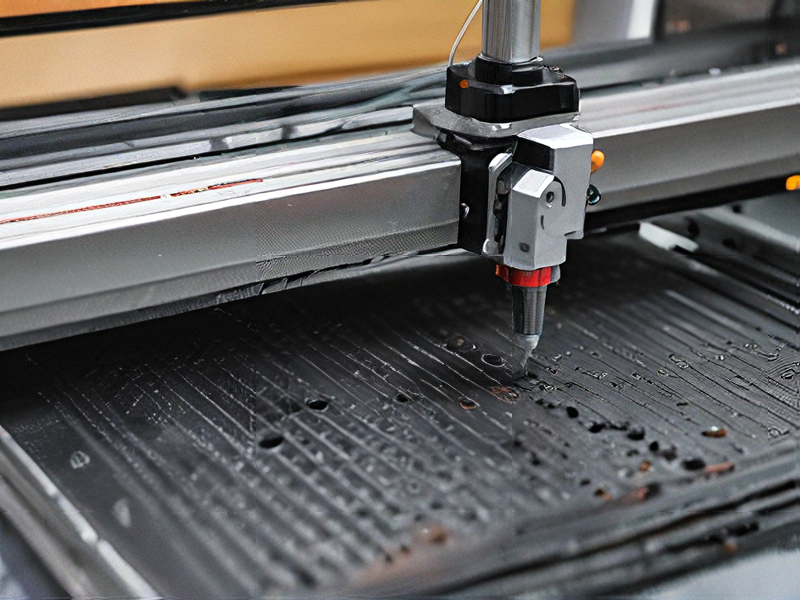
Tips for Procurement and Considerations when Purchasing from metal laser engraver machine
When purchasing a metal laser engraver machine, several key considerations can ensure you make an informed decision:
1. Machine Specifications: Evaluate the machine’s power output, laser type (fiber or CO2), and wavelength to ensure compatibility with the materials you intend to engrave. Consider factors like marking speed, resolution, and depth of engraving based on your specific needs.
2. Ease of Use: Look for user-friendly interfaces and software that support your workflow. Ensure the machine integrates well with your existing setup and can be operated efficiently by your team.
3. Precision and Quality: Check the machine’s precision capabilities through sample tests or reviews. Quality of engraving, consistency, and ability to handle intricate designs are crucial for meeting your output expectations.
4. Maintenance and Support: Inquire about maintenance requirements, availability of spare parts, and technical support. Reliable after-sales service ensures minimal downtime and longer machine lifespan.
5. Safety Features: Laser machines pose safety risks; ensure the equipment meets or exceeds safety standards. Features like enclosed workspaces, interlocks, and safety protocols are essential.
6. Cost and ROI: Compare upfront costs, operational costs (including maintenance and consumables), and potential return on investment. Balance affordability with long-term benefits and productivity gains.
7. Supplier Reputation: Choose a reputable supplier with a track record of delivering quality products and excellent customer support. Check reviews, testimonials, and warranty terms before finalizing your purchase.
By considering these factors, you can select a metal laser engraver machine that aligns with your operational needs, budget constraints, and long-term business goals effectively.
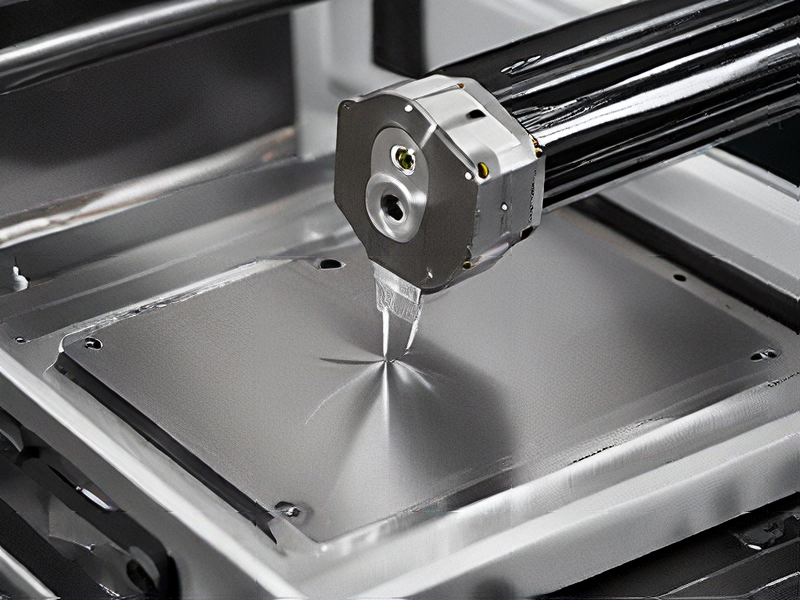
FAQs on Sourcing and Manufacturing from metal laser engraver machine in China
Certainly! Here are some frequently asked questions (FAQs) about sourcing and manufacturing from metal laser engraver machines in China:
1. Why choose China for metal laser engraver machines?
China offers competitive pricing, advanced technology, and a wide range of manufacturers specializing in laser engraving equipment.
2. What should I consider when selecting a supplier?
Factors to consider include the supplier’s reputation, product quality, pricing, lead times, support services, and adherence to international manufacturing standards.
3. How can I ensure product quality?
Conduct thorough supplier assessments, request product samples, and consider visiting the supplier’s facilities to inspect manufacturing processes and quality control measures.
4. What are the typical lead times for manufacturing?
Lead times vary but can range from a few weeks to several months depending on the complexity of the machine and current production schedules.
5. What certifications should I look for?
Look for certifications such as ISO 9001 for quality management systems and CE certification for compliance with European safety standards.
6. How can I manage logistics and shipping?
Work closely with the supplier to coordinate shipping arrangements, manage customs procedures, and ensure timely delivery of your equipment.
7. What after-sales support can I expect?
Ensure the supplier provides technical support, warranty coverage, and access to spare parts to maintain and repair your laser engraver machine.
8. Are there potential challenges in sourcing from China?
Challenges may include language barriers, cultural differences, intellectual property protection, and navigating import/export regulations.
By addressing these FAQs, you can better navigate the process of sourcing and manufacturing metal laser engraver machines from China, ensuring a smoother procurement experience.
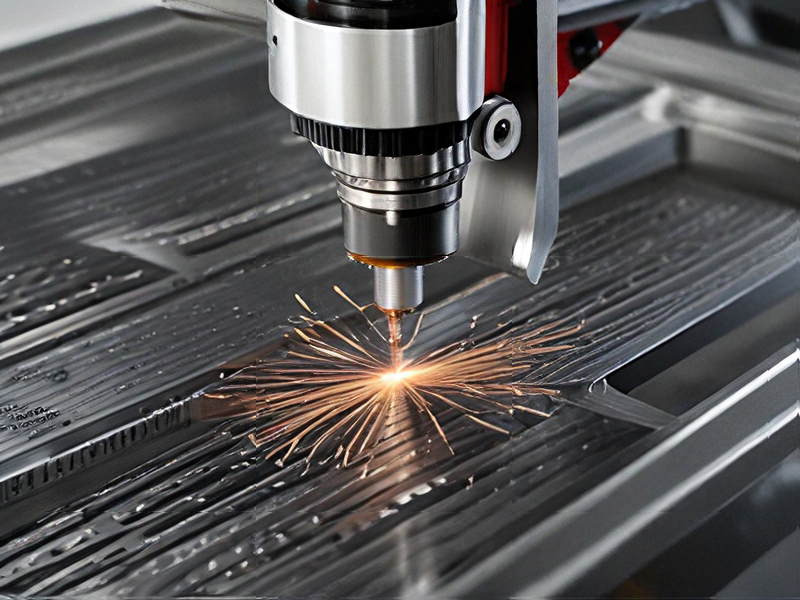