Technology and Applications of metal perforating
Metal perforating involves the process of creating holes or patterns in metal sheets or screens. This technique serves various functional and aesthetic purposes across different industries. In manufacturing, perforated metal sheets are crucial for filtration, ventilation, acoustic control, and architectural design.
Applications:
1. Filtration and Separation: Perforated metal sheets are used in filters for air, water, and other substances. The precise hole patterns allow specific particle sizes to pass through, making them ideal for industrial filtration systems.
2. Acoustic Control: In architecture and automotive industries, perforated metal panels help in controlling sound transmission. They are used in ceilings, walls, and machinery enclosures to absorb or diffuse sound waves.
3. Decorative and Architectural Design: Perforated metal offers designers flexibility in creating aesthetically pleasing facades, sunshades, balustrades, and interior partitions. The patterns can range from simple geometric shapes to intricate designs, enhancing visual appeal.
4. Safety and Security: In industrial settings and public spaces, perforated metal sheets are used for safety guards, barriers, and anti-slip flooring. The perforations ensure adequate visibility and airflow while maintaining security.
Technologies:
1. Punching: Traditional method where punches and dies are used to create holes of various shapes and sizes.
2. Laser Cutting: Provides high precision and flexibility in creating intricate patterns and designs on metal sheets.
3. Chemical Etching: Utilizes chemical solutions to selectively remove metal and create precise perforations with minimal burrs.
4. Water Jet Cutting: Uses high-pressure water jets mixed with abrasive materials to cut through metal sheets, offering versatility in hole sizes and shapes.
Metal perforating technologies continue to evolve, driven by demands for efficiency, precision, and customization in various industries, from aerospace and automotive to architecture and manufacturing.
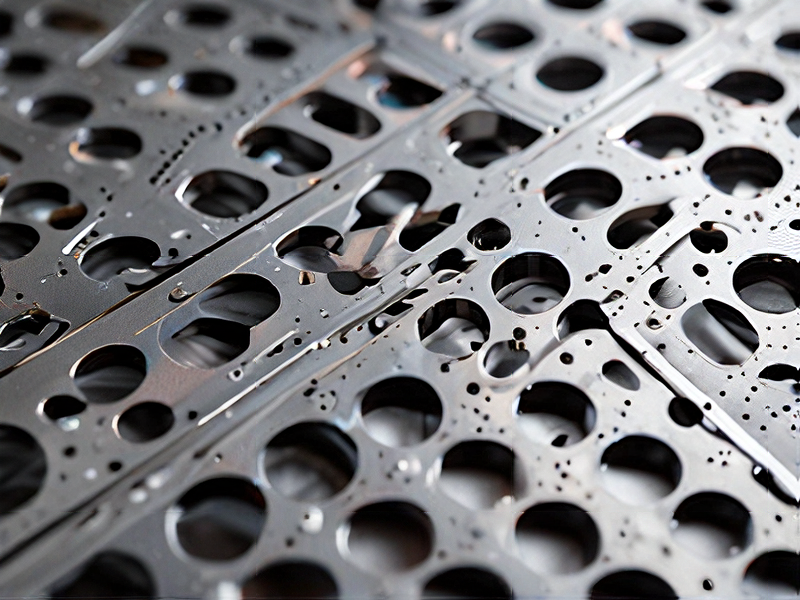
Quality Testing Methods for metal perforating and how to control quality
Quality testing methods for metal perforating involve several key approaches to ensure the accuracy and consistency of the perforated products:
1. Dimensional Inspection: Utilizing precise measurement tools such as calipers or coordinate measuring machines (CMMs) to verify hole diameters, pitch, and overall dimensions against engineering drawings.
2. Visual Inspection: A visual check ensures there are no burrs, cracks, or other surface defects that could affect the functionality or aesthetics of the perforated metal.
3. Tensile Testing: This method assesses the strength of the metal after perforation, ensuring it meets specified mechanical properties.
4. Perforation Integrity: Testing the integrity of the holes by methods such as pressure testing or passing a pin gauge through the holes to verify their size and shape.
5. Surface Finish Evaluation: Ensuring the surface finish meets required standards, typically through visual inspection or using surface roughness measurement tools.
To control quality effectively:
1. Process Control: Implementing strict process controls during perforation, including machine settings, tool maintenance, and operator training.
2. Quality Assurance: Regular audits and inspections throughout the manufacturing process to identify and rectify potential issues promptly.
3. Data Analysis: Collecting and analyzing data from quality tests to identify trends or deviations, allowing for continuous improvement.
4. Supplier Management: Ensuring that raw materials used in perforating meet quality standards through effective supplier management and material testing.
By employing these methods and controls, manufacturers can consistently produce high-quality perforated metal products that meet customer expectations and industry standards.
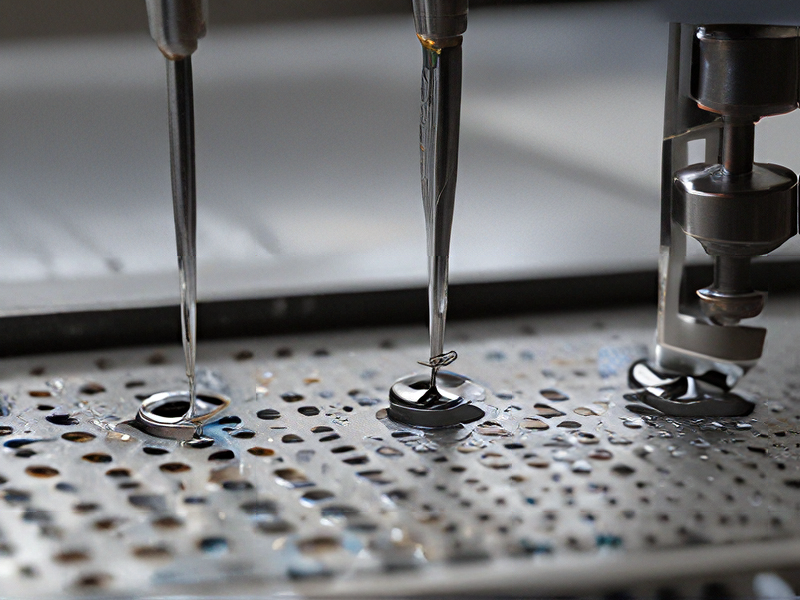
Tips for Procurement and Considerations when Purchasing from metal perforating
When procuring metal perforating services, several key considerations can ensure successful outcomes:
1. Specifications and Requirements: Clearly define your perforation needs, including material type, thickness, hole size, pattern, and tolerances. This clarity helps in selecting a supplier capable of meeting your specifications.
2. Supplier Capability: Assess the supplier’s experience and capabilities in metal perforating. Look for their track record in handling similar projects, their equipment capabilities, and their quality control measures.
3. Material Quality: Ensure the supplier uses high-quality materials suitable for your application. Verify the material certifications and standards compliance to avoid future issues.
4. Cost and Pricing Structure: Obtain detailed pricing proposals that outline costs for materials, perforation services, tooling (if applicable), and any additional services. Consider the overall value rather than just the lowest cost.
5. Lead Times and Delivery: Discuss expected lead times and delivery schedules to align with your project timelines. Clarify any expedited options and associated costs if quicker delivery is needed.
6. Quality Assurance: Inquire about the supplier’s quality assurance processes, including inspections during and after perforation. Certifications such as ISO standards can indicate their commitment to quality.
7. Customer Support and Communication: Evaluate the supplier’s responsiveness and ability to communicate effectively throughout the procurement process. Clear communication helps prevent misunderstandings and delays.
8. Flexibility and Customization: Determine if the supplier can accommodate custom perforation patterns or unique requirements specific to your project. Flexibility is crucial for meeting diverse customer needs.
9. Reputation and References: Seek references or reviews from other customers to gauge the supplier’s reputation for reliability, customer service, and product quality.
10. Contract Terms and Conditions: Review contract terms thoroughly, including payment terms, warranties, intellectual property rights, and dispute resolution procedures. Ensure all terms are fair and align with your expectations.
By considering these factors, you can navigate the procurement process effectively and select a metal perforating supplier that meets your project requirements and business goals.
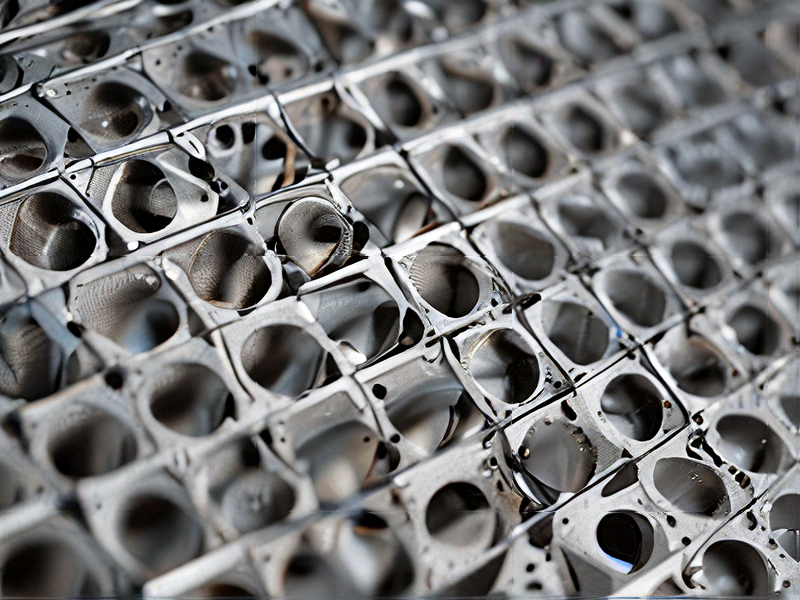
FAQs on Sourcing and Manufacturing from metal perforating in China
FAQs on Sourcing and Manufacturing from Metal Perforating in China
1. What is metal perforating?
Metal perforating is the process of creating holes in metal sheets or plates, often used for decorative or functional purposes like ventilation or filtration.
2. Why source metal perforating from China?
China is a leading manufacturer of metal products, offering competitive pricing, advanced technology, and a wide range of materials. This allows for cost-effective solutions and a variety of customization options.
3. What materials are commonly used for perforated metal?
Common materials include stainless steel, aluminum, carbon steel, and galvanized steel. The choice depends on the intended application, desired strength, and corrosion resistance.
4. How do I find reliable manufacturers?
Research potential suppliers by checking their credentials, reading reviews, and requesting references. Trade shows, online platforms like Alibaba, and industry associations are also valuable resources.
5. What are the typical lead times?
Lead times can vary based on order size and complexity. Generally, small to medium orders can take 2-4 weeks, while larger projects may take longer.
6. How do I ensure quality control?
Establish clear specifications and conduct regular quality inspections. You may also hire a third-party inspection service to verify compliance with standards.
7. What are the customs and shipping considerations?
Understand import regulations, tariffs, and shipping options. Working with a freight forwarder can streamline the logistics process.
8. Can I customize designs?
Yes, most manufacturers offer customization options. Provide detailed drawings and specifications to ensure your requirements are met.
9. What are payment terms?
Payment terms can vary by supplier but typically involve a deposit upfront with the balance due before shipping. Always clarify and agree on terms before proceeding.
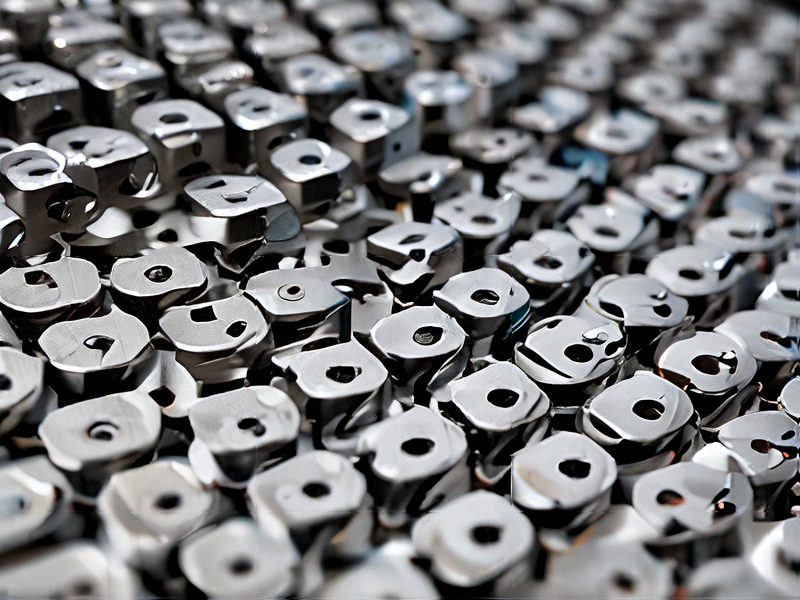