Technology and Applications of metal sheet fabricators
Metal sheet fabrication involves the process of cutting, bending, and assembling flat metal sheets into various shapes and products. This versatile technique is fundamental in manufacturing industries, enabling the production of a wide range of items, from intricate components to large structural elements.
Technology in Metal Sheet Fabrication:
1. Cutting: Advanced technologies like laser cutting, plasma cutting, and water jet cutting provide precision and efficiency. Laser cutting, for instance, uses a high-powered laser to make accurate cuts, suitable for complex designs and thin materials. Plasma cutting is ideal for thicker materials and is faster, while water jet cutting uses high-pressure water mixed with abrasives to cut through metals without affecting their inherent properties.
2. Bending: CNC (Computer Numerical Control) press brakes are commonly used to bend metal sheets with high precision. These machines can be programmed to perform complex bends, ensuring consistency and accuracy across large production runs.
3. Assembling: Welding, riveting, and adhesive bonding are standard methods for assembling metal parts. Robotic welding systems enhance efficiency and precision, especially in repetitive and high-volume tasks.
Applications of Metal Sheet Fabrication:
1. Automotive Industry: Metal sheet fabricators produce parts like body panels, chassis components, and brackets. Advanced fabrication techniques contribute to the manufacture of lightweight and durable automotive parts, improving vehicle performance and fuel efficiency.
2. Aerospace: Precision and reliability are crucial in aerospace applications. Fabricated metal sheets are used for aircraft skins, structural components, and engine parts, where weight reduction without compromising strength is essential.
3. Construction: In construction, metal sheet fabricators create roofing materials, HVAC ducts, and structural frameworks. The durability and versatility of metal sheets make them ideal for various building applications.
4. Electronics: Enclosures for electronic devices, including computer cases and server racks, are often made from fabricated metal sheets, providing protection and structural integrity.
5. Consumer Goods: Household appliances, furniture, and kitchen equipment frequently utilize metal sheet fabrication for both functional and aesthetic purposes.
In summary, metal sheet fabrication combines cutting-edge technology with a broad range of applications, driving innovation and efficiency across multiple industries.
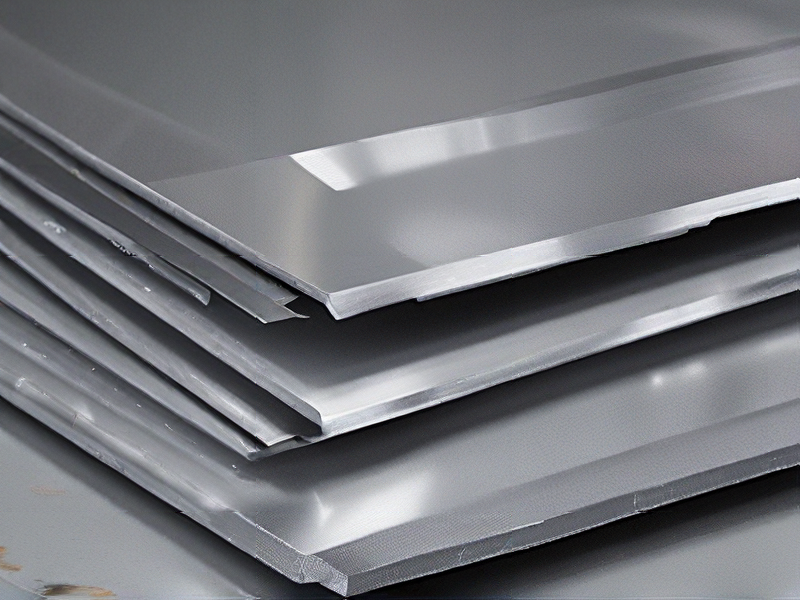
Quality Testing Methods for metal sheet fabricators and how to control quality
Quality testing for metal sheet fabricators involves various methods to ensure that the final products meet the required standards and specifications. Key methods include:
1. Visual Inspection:
– Purpose: Identifies surface defects like scratches, dents, and corrosion.
– Implementation: Regular inspections by trained personnel during and after production.
2. Dimensional Inspection:
– Purpose: Ensures dimensions and tolerances are within specifications.
– Implementation: Use of calipers, micrometers, and coordinate measuring machines (CMMs).
3. Non-Destructive Testing (NDT):
– Purpose: Detects internal flaws without damaging the material.
– Types: Includes ultrasonic testing (UT), magnetic particle testing (MT), dye penetrant testing (PT), and X-ray inspection.
– Implementation: Conducted during and after fabrication to check for internal and surface defects.
4. Material Testing:
– Purpose: Verifies material properties such as hardness, tensile strength, and composition.
– Implementation: Includes hardness testing (e.g., Rockwell, Vickers), tensile testing, and spectroscopic analysis.
5. Weld Inspection:
– Purpose: Ensures the integrity of welds.
– Types: Visual weld inspection, ultrasonic weld testing, and radiographic weld inspection.
– Implementation: Regular checks during and after welding processes.
Quality Control Measures
1. Standard Operating Procedures (SOPs):
– Purpose: Ensure consistency and adherence to quality standards.
– Implementation: Documented procedures for each stage of fabrication.
2. Training and Certification:
– Purpose: Skilled workforce ensures high-quality output.
– Implementation: Regular training programs and certification for workers.
3. Quality Management Systems (QMS):
– Purpose: Systematic approach to quality control.
– Implementation: Adopting standards like ISO 9001, involving regular audits and continuous improvement processes.
4. Statistical Process Control (SPC):
– Purpose: Monitors and controls production processes.
– Implementation: Use of control charts and statistical methods to identify and rectify variations.
5. Supplier Quality Management:
– Purpose: Ensures quality of raw materials.
– Implementation: Supplier audits, certifications, and regular material testing.
Implementing these methods and measures helps metal sheet fabricators maintain high quality, reduce defects, and ensure customer satisfaction.
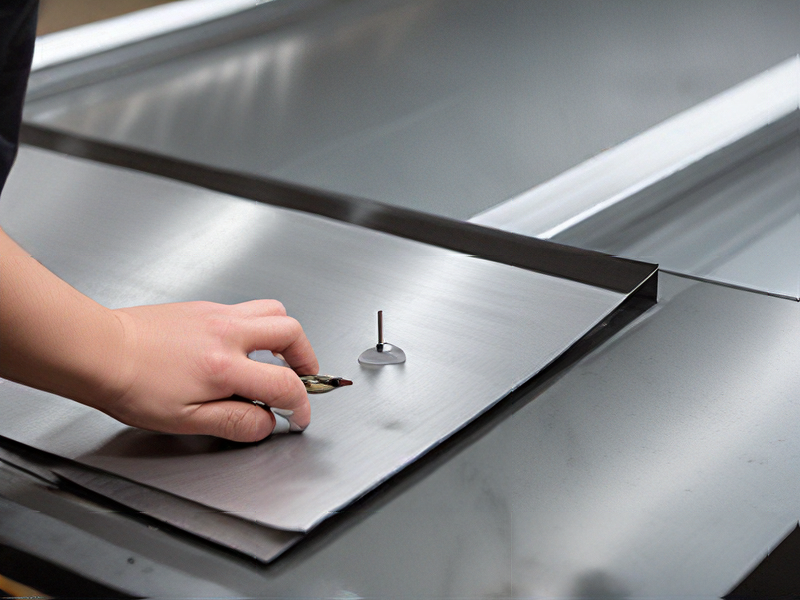
Tips for Procurement and Considerations when Purchasing from metal sheet fabricators
When purchasing from metal sheet fabricators, consider the following tips and considerations to ensure a smooth procurement process and high-quality results:
1. Define Requirements Clearly:
– Specify material type, thickness, dimensions, tolerances, and finishing requirements.
– Provide detailed drawings or CAD files to avoid misinterpretation.
2. Research and Select Reputable Fabricators:
– Look for fabricators with a strong track record and positive customer reviews.
– Verify their experience with similar projects and materials.
3. Quality Assurance:
– Ensure the fabricator follows industry standards and certifications (ISO, ASTM).
– Request samples or inspect previous work to assess quality.
4. Lead Times and Capacity:
– Confirm the fabricator’s lead times and ensure they align with your project timeline.
– Discuss their production capacity to handle your order volume.
5. Cost and Budgeting:
– Obtain multiple quotes to compare prices.
– Consider the total cost, including material, fabrication, shipping, and potential hidden costs.
6. Communication and Support:
– Establish clear communication channels.
– Ensure the fabricator provides timely updates and support throughout the project.
7. Contract and Terms:
– Review and negotiate contract terms, including payment schedules, delivery terms, and warranties.
– Clarify terms for handling defects or delays.
8. Sustainability and Compliance:
– Check if the fabricator adheres to environmental regulations and sustainability practices.
– Ensure compliance with safety and labor standards.
9. Technology and Capabilities:
– Evaluate the fabricator’s machinery and technology to ensure they can meet your specifications.
– Consider fabricators with advanced capabilities like CNC machining, laser cutting, or automated welding.
10. Logistics and Delivery:
– Plan for shipping and handling, considering packaging requirements to prevent damage.
– Verify delivery schedules and track shipments to ensure timely receipt.
Following these tips will help you make informed decisions, ensuring quality, efficiency, and reliability in your metal sheet fabrication projects.
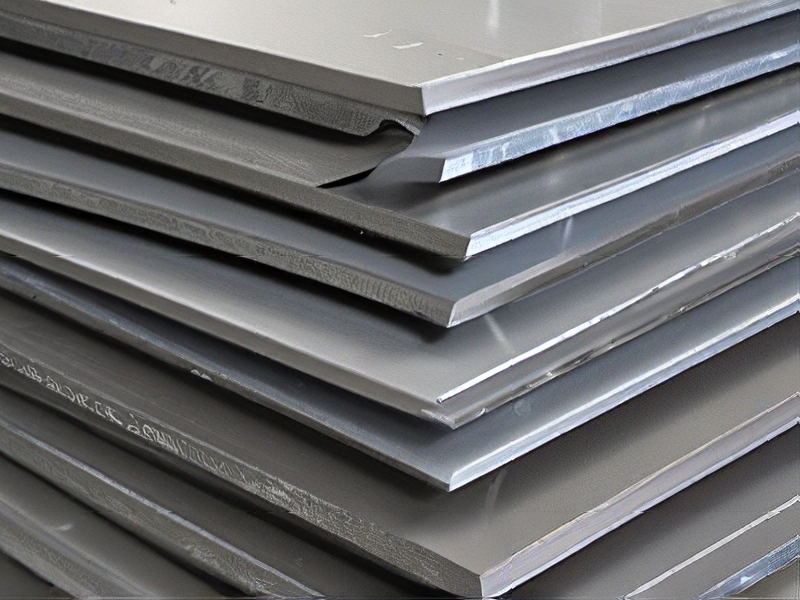
FAQs on Sourcing and Manufacturing from metal sheet fabricators in China
FAQs on Sourcing and Manufacturing from Metal Sheet Fabricators in China
1. Why source metal sheet fabrication from China?
– Cost-Effective: China offers competitive pricing due to lower labor costs and economies of scale.
– Expertise: Chinese manufacturers have extensive experience and advanced technology in metal fabrication.
– Capacity: High production capacity and the ability to handle large orders efficiently.
2. What types of metal fabrication services are available?
– Laser Cutting: Precision cutting of metal sheets using laser technology.
– Bending and Forming: Shaping metal sheets into desired forms.
– Welding: Joining metal parts through various welding techniques.
– Punching: Creating holes and other shapes in metal sheets.
– Finishing: Surface treatments like powder coating, painting, and anodizing.
3. How to choose a reliable metal sheet fabricator in China?
– Research: Look for manufacturers with a strong track record and good reviews.
– Certifications: Verify certifications such as ISO for quality management.
– Factory Visits: If possible, visit factories to inspect their facilities and capabilities.
– Samples: Request samples to assess the quality of their work.
4. What are the common challenges in sourcing from China?
– Communication Barriers: Language and cultural differences can impact communication.
– Quality Control: Ensuring consistent quality requires rigorous oversight.
– Logistics: Managing shipping, customs, and potential delays can be complex.
5. How can I ensure quality control?
– Clear Specifications: Provide detailed drawings and specifications.
– Third-Party Inspections: Hire third-party inspectors to verify quality before shipment.
– Regular Audits: Conduct regular audits and inspections of manufacturing processes.
6. What are the payment terms typically used?
– TT (Telegraphic Transfer): Commonly used, often with a deposit upfront and balance upon shipment.
– L/C (Letter of Credit): Provides more security but can be more complex and costly.
– Alibaba Trade Assurance: For transactions through Alibaba, offering protection for buyers.
7. How long does the manufacturing process take?
– Lead Times: Typically range from a few weeks to a couple of months, depending on the complexity and volume of the order.
8. Are there any import duties or taxes?
– Customs Duties: Vary by country; check with local customs authorities.
– VAT/GST: May apply depending on your country’s regulations.
By addressing these FAQs, businesses can better navigate the process of sourcing and manufacturing from metal sheet fabricators in China, ensuring a successful and efficient partnership.
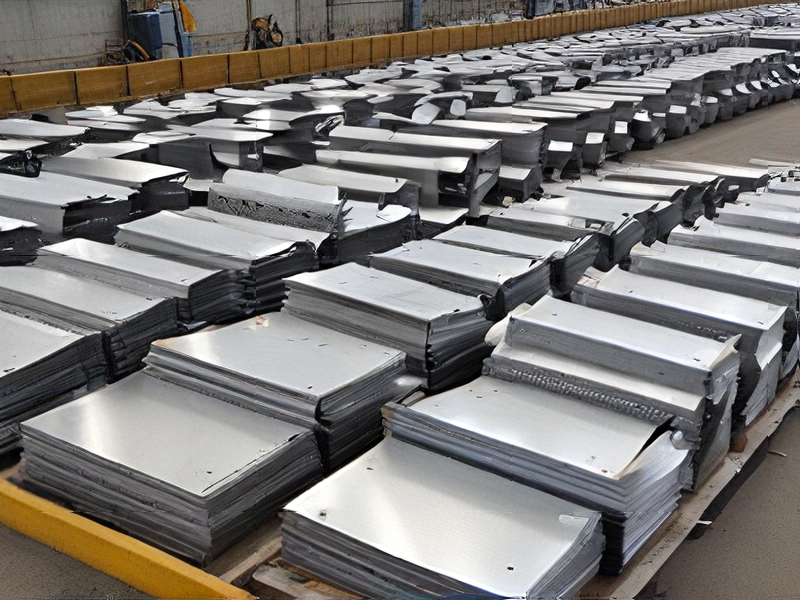