Technology and Applications of metals in bronze
Bronze, an alloy primarily composed of copper and tin, has been pivotal in human civilization since its development around 3300 BCE. Its unique properties, including durability, corrosion resistance, and malleability, have made it a valuable material for various applications.
Technology: The production of bronze involves smelting copper and tin ores. Innovations such as the use of casting techniques allowed artisans to create intricate shapes and designs, enhancing both utility and aesthetics. The lost-wax casting method, for instance, enabled the production of detailed sculptures and tools. Over time, advancements in metallurgy improved the alloy’s properties, leading to variations like phosphor bronze and aluminum bronze, each tailored for specific applications.
Applications: Bronze has been extensively utilized in various domains:
1. Tools and Weapons: Early civilizations employed bronze to make superior tools and weapons, significantly impacting warfare and agriculture. Swords, axes, and plows ushered in more efficient practices.
2. Art and Sculpture: Due to its malleability and ability to capture fine details, bronze became a favored medium for artists. Statues and decorative elements from ancient times to the Renaissance highlight its aesthetic appeal.
3. Architecture: Bronze has been used for various architectural elements, including doors and fixtures, offering durability and an appealing finish.
4. Marine Applications: Its resistance to corrosion makes bronze ideal for ship fittings, propellers, and underwater applications.
5. Electrical Conductivity: Certain bronze alloys exhibit good electrical conductivity, making them suitable for electrical connectors and components.
In summary, the technology and applications of bronze have evolved tremendously, reflecting its significance across multiple facets of society. Its exceptional properties ensure that bronze continues to be relevant in modern technology and art.
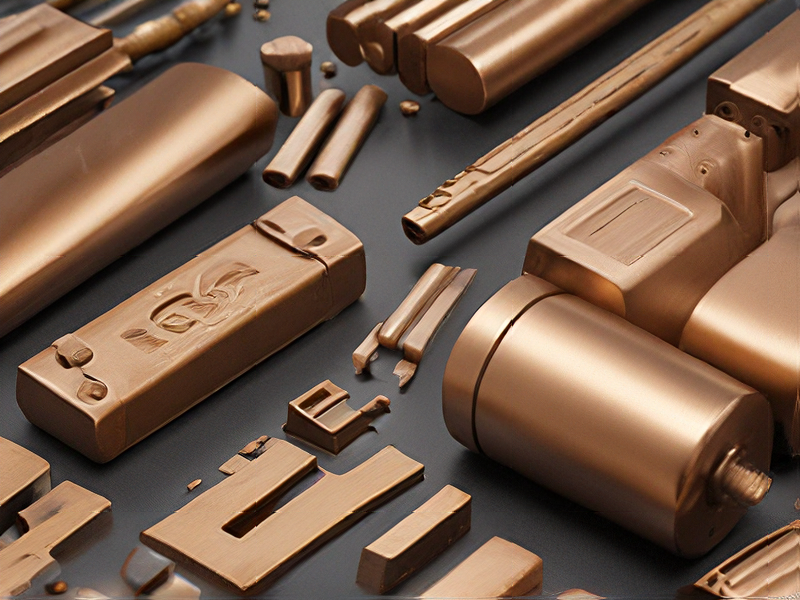
Quality Testing Methods for metals in bronze and how to control quality
Quality testing for bronze, an alloy primarily of copper and tin, is essential to ensure its performance in various applications. Key methods for quality testing metals in bronze include:
1. Chemical Analysis: To determine the composition of bronze, spectroscopic techniques such as X-ray fluorescence (XRF) and inductively coupled plasma mass spectrometry (ICP-MS) are employed. Accurate composition is crucial as variations can affect mechanical properties and corrosion resistance.
2. Mechanical Testing: Tests such as tensile strength, hardness, and impact tests are conducted to assess the material’s performance under stress. Common methods include Rockwell or Brinell hardness tests to determine hardness and tensile testing to evaluate strength and ductility.
3. Microstructural Analysis: Optical microscopy and scanning electron microscopy (SEM) are used to examine the grain structure and phase distribution in bronze. This can reveal information about the alloy’s properties and any potential defects.
4. Non-destructive Testing (NDT): Techniques like ultrasonic testing and eddy current testing are employed to detect internal flaws without damaging the material. These methods help in assessing quality while maintaining the integrity of the sample.
Quality Control Processes:
To ensure consistent quality in bronze production, implement rigorous quality control measures:
– Standard Operating Procedures (SOPs): Establish detailed SOPs for testing and inspections.
– Regular Training: Provide ongoing training for personnel in testing methods and quality standards.
– Sampling Techniques: Use statistical sampling to assess the quality of production batches.
– Documentation: Maintain comprehensive records of tests and inspections to track quality over time.
By integrating these testing methods and control measures, manufacturers can ensure the reliability and performance of bronze products.
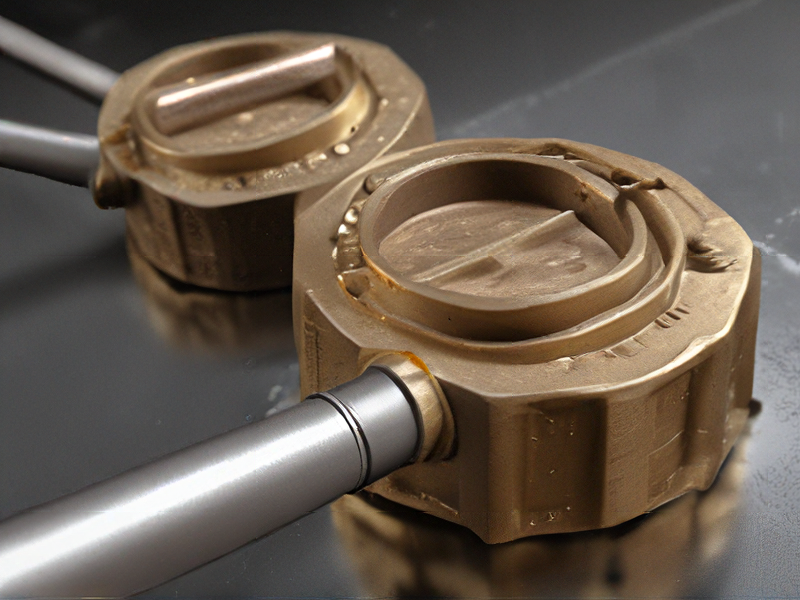
Tips for Procurement and Considerations when Purchasing from metals in bronze
When procuring bronze metals, consider the following tips and factors to ensure you make informed decisions:
1. Understand Bronze Alloys: Familiarize yourself with different bronze types, such as aluminum bronze, silicon bronze, and copper-tin bronze. Each alloy has unique properties suited for specific applications.
2. Supplier Reputation: Choose reputable suppliers with a track record of quality and reliability. Look for certifications and endorsements from industry standards, as these can indicate a supplier’s credibility.
3. Material Specifications: Specify the necessary standards, such as ASTM or ISO, for the bronze required. Clear communication regarding grade, composition, and mechanical properties ensures you receive the right materials.
4. Quality Assurance: Inquire about the supplier’s quality control processes, including testing methods for tensile strength, corrosion resistance, and appearance. Request certificates of compliance if necessary.
5. Price vs. Quality: While cost is important, prioritize quality over price. Higher-quality bronze can save costs in the long run by reducing maintenance needs and enhancing performance.
6. Quantity and Lead Times: Determine your quantity requirements early and discuss lead times with the supplier. Make sure the supplier can meet your timeline without compromising quality.
7. Applications and Performance: Assess the specific use case of the bronze. Consider factors like wear resistance, fatigue strength, and machinability based on how the metal will be used.
8. Sustainability: Evaluate the sustainability practices of suppliers, including material sourcing and recycling. This aligns your procurement with environmental considerations.
By considering these factors, you can make informed decisions that meet your specific needs in bronze procurement.
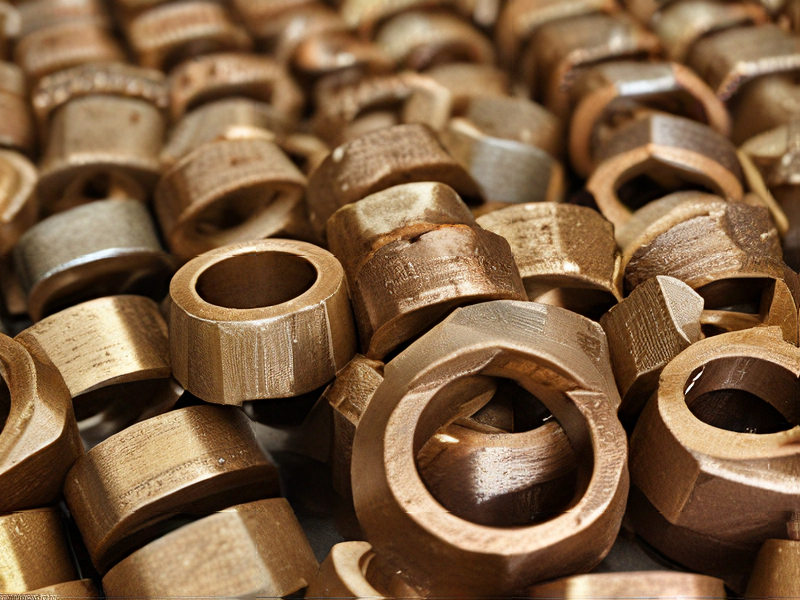
FAQs on Sourcing and Manufacturing from metals in bronze in China
FAQs on Sourcing and Manufacturing Bronze in China
1. What is bronze?
Bronze is an alloy primarily composed of copper, usually with tin as the main additive, though other metals may also be included. It is valued for its durability and resistance to corrosion.
2. Why source bronze products from China?
China is one of the largest producers of bronze and offers competitive pricing, a wide range of manufacturers, and advanced production technologies. This makes it an attractive option for sourcing bronze products.
3. How do I find reliable suppliers?
Research online marketplaces like Alibaba or Global Sources. Additionally, consider attending trade fairs such as the Canton Fair or using sourcing agents who can vet suppliers. Always verify credentials and request samples.
4. What are the common manufacturing processes for bronze?
Bronze can be manufactured using several methods, including casting, forging, and CNC machining. The process chosen often depends on the specific product requirements and complexity.
5. Are there quality control standards?
Yes, most suppliers adhere to international quality standards such as ISO 9001. It’s recommended to establish a quality inspection process before mass production, including pre-production samples and factory audits.
6. What is the typical lead time for bronze manufacturing?
Lead times can vary, but generally, they range from 30 to 90 days, depending on order complexity and production capacity. Always confirm timelines with suppliers before placing orders.
7. What import/export regulations should I be aware of?
Familiarize yourself with regulations governing metal imports in your country, including tariffs, taxation, and required documentation. Compliance ensures smoother customs clearance.
8. What are the payment terms usually offered?
Common payment terms include a 30% deposit upfront and the balance upon completion. However, terms can vary, so it’s essential to discuss and agree upon them with the supplier beforehand.
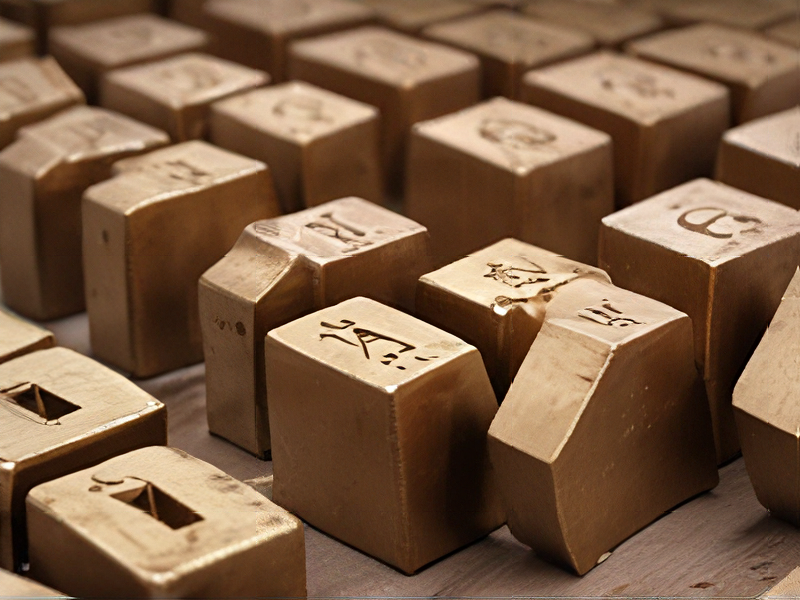