Technology and Applications of milling milling machine
Milling machines are essential tools in manufacturing, capable of shaping various materials through a rotating cutting tool. This technology operates on the principles of removing material from a workpiece, often metal or plastic, to achieve desired shapes and sizes.
Types of Milling Machines:
1. Vertical Milling Machines: The spindle axis is vertical, allowing for more versatile machining and the ability to execute complex shapes.
2. Horizontal Milling Machines: These feature a horizontal spindle, ideal for heavy-duty tasks and producing large quantities of symmetrical pieces.
Key Technologies:
– CNC Milling: Computer Numerical Control (CNC) milling machines automate the machining process using programmed instructions. This enhances precision and repeatability, crucial for complex parts in aerospace and automotive industries.
– 3D Milling: This technology enables the creation of three-dimensional objects by milling multiple surfaces, widely used in prototyping and mold-making.
Applications:
1. Aerospace: Milling is used for components like airframes and engine parts that require high precision.
2. Automotive: Parts such as brackets, engine mounts, and other complex geometries benefit from milling.
3. Medical Devices: Custom implants and surgical instruments are often created with CNC milling for accuracy.
4. Tool and Die Making: Milling machines are used to produce molds and tooling for manufacturing processes.
In summary, milling machines combine advanced technology with versatile applications, making them indispensable in various industries. Their ability to produce precise and intricate designs positions them as a cornerstone of modern manufacturing.
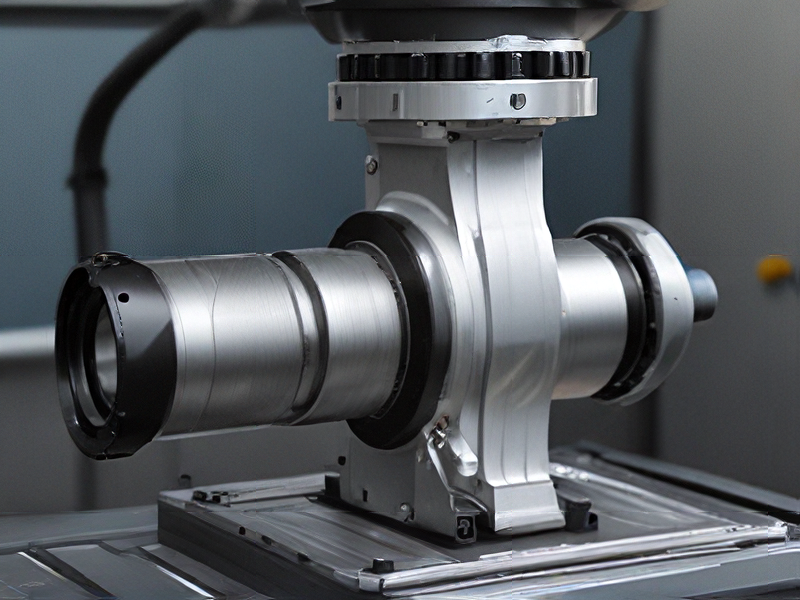
Quality Testing Methods for milling milling machine and how to control quality
Quality testing methods for milling machines are essential to ensure precision, reliability, and optimal performance. Here are key methods and practices to control quality:
1. Calibration Checks: Regular calibration of milling machines against reference standards ensures accuracy in measurements. This includes checking spindle speed, feed rates, and tool positioning to maintain consistency.
2. Dimensional Inspection: Use precision measuring tools such as calipers, micrometers, and gauges to inspect the dimensions of the machined components. This helps verify that parts meet specified tolerances.
3. Surface Finish Evaluation: Assess the surface roughness using a profilometer or visual inspection techniques. A good surface finish is crucial for subsequent machining processes and product performance.
4. Tool Condition Monitoring: Regularly inspect cutting tools for wear and damage. Implement tool wear sensors or scheduled tool replacements to ensure effective cutting performance and reduce scrap rates.
5. Process Control: Utilize a Statistical Process Control (SPC) system to monitor critical parameters during milling operations. Control charts can help identify variations and ensure processes remain within acceptable limits.
6. Material Quality Verification: Ensure that the raw materials used are of specified quality. Chemical composition analysis and mechanical testing can help in verifying material properties before machining.
7. Feedback Loop: Establish a feedback system from downstream processes to continuously evaluate the quality of machined parts, facilitating adjustments and improvements in milling operations.
By integrating these quality testing methods, manufacturers can maintain high standards in milling processes, minimize defects, and enhance overall product quality. Regular training and adherence to industry standards further contribute to an effective quality control system.
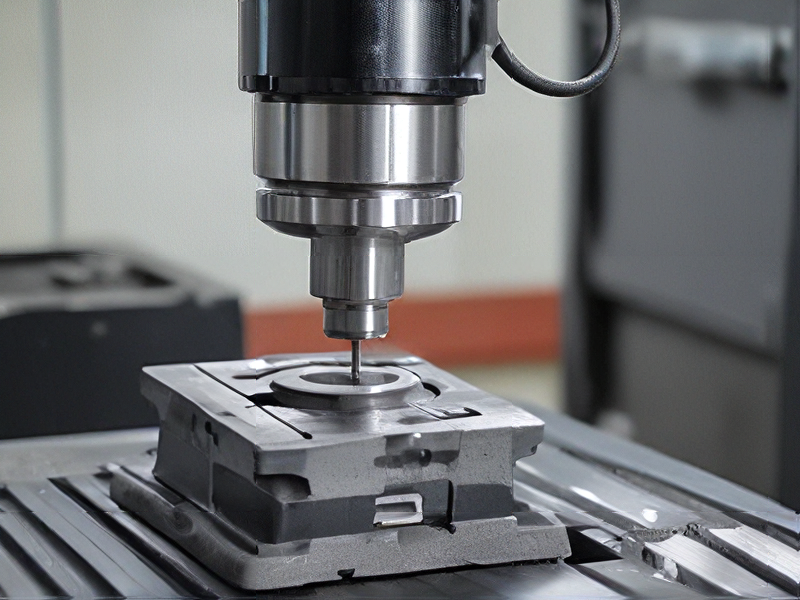
Tips for Procurement and Considerations when Purchasing from milling milling machine
When purchasing a milling machine, careful consideration is essential to ensure that you select the right equipment for your needs. Here are some key tips and considerations:
1. Evaluate Your Needs: Determine the type of milling operations you intend to perform (e.g., vertical vs. horizontal milling), the materials you will work with, and the size and complexity of the parts.
2. Budget: Establish a clear budget that includes not just the machine cost but also additional expenses such as tooling, accessories, maintenance, and training.
3. Machine Specifications: Pay attention to the machine’s specifications such as spindle speed, power, table size, and feed rates. Ensure they align with your production requirements.
4. Brand Reputation: Consider established brands with a good track record for quality and reliability. Research customer reviews, warranty options, and after-sales support.
5. New vs. Used: Decide whether to purchase a new or used machine. New machines offer the latest technology and warranties, while used machines can provide significant savings but might require more maintenance.
6. Supplier Relationships: Build a strong relationship with the supplier. Assess their support services, spare parts availability, and warranty policies as these are crucial for long-term operation.
7. Technical Support and Training: Ensure that the supplier provides adequate training and technical support for your team to operate and maintain the machine effectively.
8. Future-Proofing: Consider the potential for upgrades and integration with future technologies like CNC capabilities, as this can enhance productivity and flexibility.
In conclusion, a thorough evaluation of your requirements and careful selection of the milling machine and supplier will lead to improved productivity and cost-effectiveness in your operations.
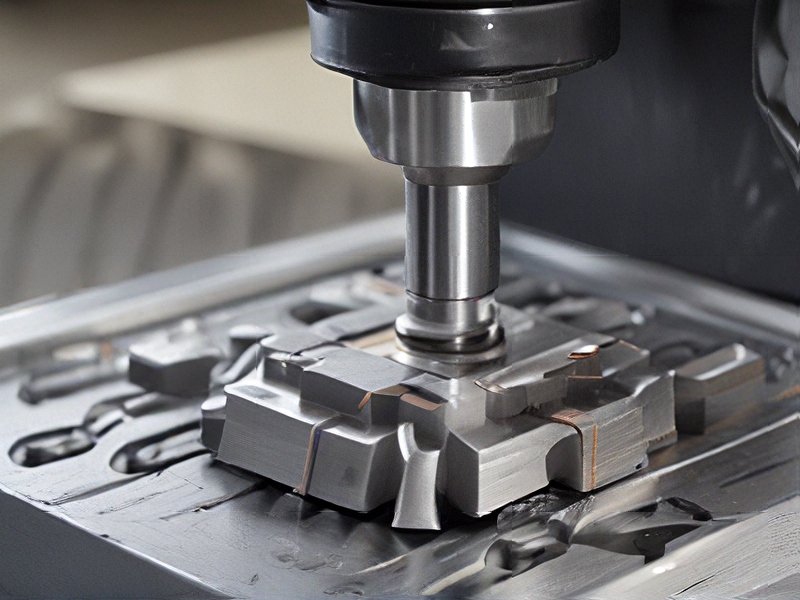
FAQs on Sourcing and Manufacturing from milling milling machine in China
FAQs on Sourcing and Manufacturing Milling Machines in China
1. Why source milling machines from China?
China is a global leader in manufacturing, offering competitive pricing, a wide range of products, and advanced technology. Many Chinese manufacturers also have experience in exporting, making the sourcing process smoother.
2. How do I find reliable suppliers?
Start by researching online platforms such as Alibaba, Made-in-China, or Global Sources. Verify suppliers through reviews, ratings, and requesting samples. Visiting trade shows in China can also provide firsthand experience with manufacturers.
3. What should I consider when selecting a manufacturer?
Assess the manufacturer’s production capacity, quality control measures, certifications (like ISO), and experience in milling machine production. Understanding their engineering capabilities is crucial for custom specifications.
4. How do I ensure product quality?
Implement quality control checks during production. Consider third-party inspection services before shipment to ensure the machines meet your specifications and standards.
5. What are the shipping logistics?
Discuss shipping options with your supplier, considering factors like cost, time, and safety. Common options include air freight for speed or sea freight for cost-effectiveness. Ensure proper documentation for customs clearance.
6. What are the payment terms?
Standard practices include a deposit (usually 30%) before production and the balance upon completion. Use secure payment methods like escrow services for added protection.
7. Are there language barriers?
While many manufacturers have English-speaking staff, expect some language differences. Use clear communication and, if needed, hire a translator to avoid misunderstandings.
8. Can I customize my milling machines?
Yes, many manufacturers offer customization options. Be specific about your requirements, and ensure they can meet technical specifications.
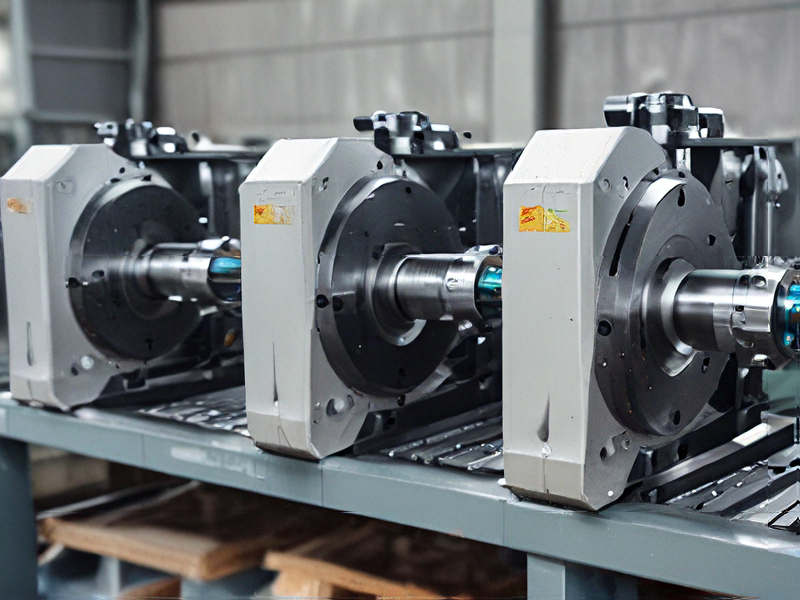