Technology and Applications of paint in metal
Paint plays a crucial role in enhancing and protecting metal surfaces across various applications. The primary technologies employed in metal paint include powder coating, electrocoat (e-coat), and liquid paint systems.
Powder Coating is a dry finishing process where finely ground paint particles are electrostatically charged and sprayed onto a metal surface. The coated items are then cured in an oven, resulting in a durable finish that is more resilient to scratches and environmental degradation than traditional liquid paints. This method is eco-friendly, as it produces minimal VOCs (volatile organic compounds).
Electrocoating (E-coat) is another advanced technology where an electrical current causes paint particles suspended in a water-based solution to deposit uniformly onto metal surfaces. This method ensures an even coat, even in hard-to-reach areas, making it ideal for automotive components and intricate metal parts. E-coating offers excellent corrosion resistance and durability.
Liquid Paint Systems include various formulations, such as solvent-based and water-based paints. They can be applied using brushes, rollers, or spray guns. These systems are versatile and can be tailored for specific requirements, including rust prevention and aesthetic finishes. However, they may emit higher levels of VOCs compared to powder coatings.
The applications of painted metal are extensive, encompassing automotive, construction, appliance manufacturing, and industrial equipment. Paint not only improves the aesthetic appeal of metal products but also enhances their longevity by providing a barrier against corrosion, UV rays, and other environmental factors. Overall, the technology and applications of paint in metal are integral to ensuring product quality and performance in a variety of industries.
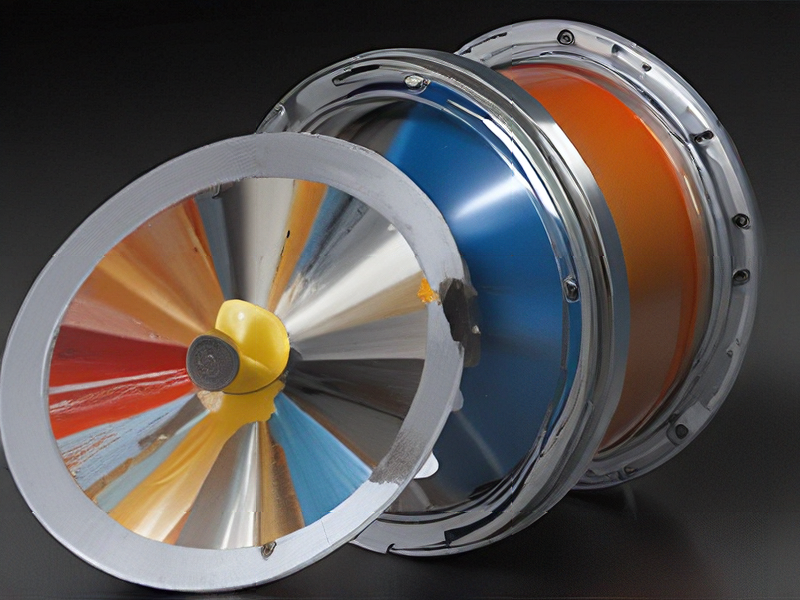
Quality Testing Methods for paint in metal and how to control quality
Quality testing of paint on metal surfaces is crucial to ensure durability, adherence, and aesthetics. Effective methods include:
1. Adhesion Testing: This is typically conducted using the tape test (ASTM D3359), where adhesive tape is applied to the painted surface and then removed. A rating is given based on how much paint is removed, ensuring strong adhesion.
2. Crosshatch Testing: Similar to the tape test but involves making a crosshatch pattern with a cutter and applying tape over it. The tape is pulled away to assess the amount of paint that comes off, giving insight into adhesion under stress.
3. Impact Resistance: Testing involves dropping a weight onto the painted surface to assess its ability to withstand shocks without chipping or cracking (ASTM D2794).
4. Gloss Measurement: Using a gloss meter (ASTM D523), the sheen of the paint is measured to ensure it meets specifications. This is vital for aesthetic quality.
5. Corrosion Resistance: Salt spray tests (ASTM B117) are performed to evaluate the paint’s ability to protect metal from rust under aggressive conditions.
6. Color Consistency: Spectrophotometers are used to ensure the paint color matches specifications consistently across different batches.
To control quality, implement a Quality Management System (QMS) that includes:
– Standard Operating Procedures (SOPs): Establish clear protocols for each testing method.
– Training: Regular training for personnel handling testing and application.
– Batch Testing: Sample each batch for tests before large-scale application.
– Regular Calibration: Ensure all testing equipment is calibrated and maintained.
– Documentation: Maintain records of all tests conducted for traceability and accountability.
Implementing these strategies fosters consistent paint quality and enhances the performance and longevity of metal coatings.
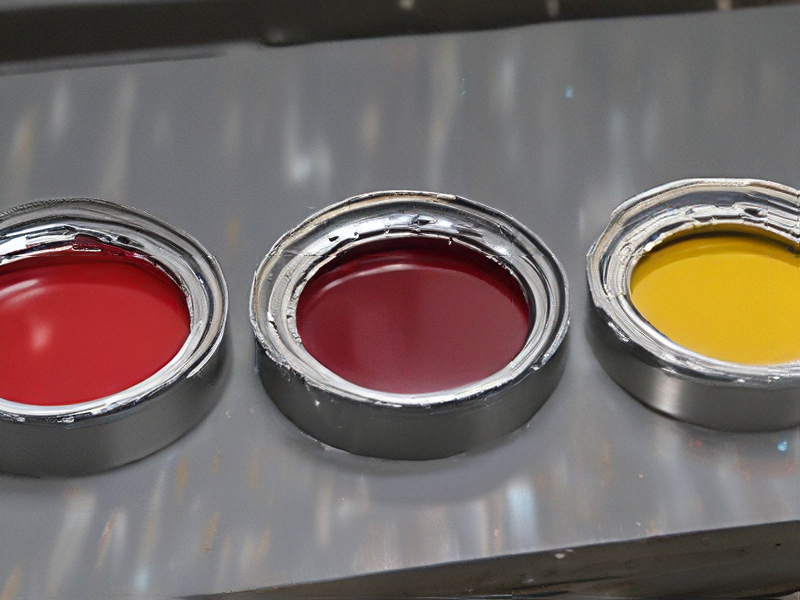
Tips for Procurement and Considerations when Purchasing from paint in metal
When procuring paint for metal surfaces, several key factors and considerations can ensure optimal results.
Tips for Procurement:
1. Identify Requirements: Determine the specific application, whether for industrial, automotive, or decorative purposes. Understand the environment—indoors or outdoors—and exposure to elements like moisture, UV light, or chemicals.
2. Select the Right Type of Paint: Choose between oil-based, water-based, or specialized coatings like epoxy or urethane. Oil-based paints provide durability, while water-based options offer ease of cleanup and lower VOC emissions.
3. Check Compatibility: Ensure the paint is compatible with the type of metal being coated (e.g., steel, aluminum). Some paints require specific primers for optimal adhesion.
4. Evaluate Performance Features: Look for properties such as rust resistance, abrasion resistance, and flexibility. Consider paints with anti-corrosive attributes for longevity in harsh conditions.
5. Review Certification and Safety: Check for compliance with relevant safety and environmental regulations, such as VOC limits and hazardous materials.
Considerations:
1. Surface Preparation: Properly prepare the metal surface by cleaning, sanding, and applying primer if necessary. This step is crucial for adhesion and a smooth finish.
2. Application Method: Decide whether to use brushes, rollers, or spray systems based on the area size and finish desired. Ensure equipment is compatible with the chosen paint.
3. Color and Finish: Consider colorfastness and the type of finish (glossy, matte, etc.) based on aesthetic and functional requirements.
4. Batch Consistency: Purchase enough paint from the same batch to ensure consistency in color and texture across the project.
By thoughtfully considering these aspects, you can make informed decisions that lead to successful paint procurement for metal surfaces.
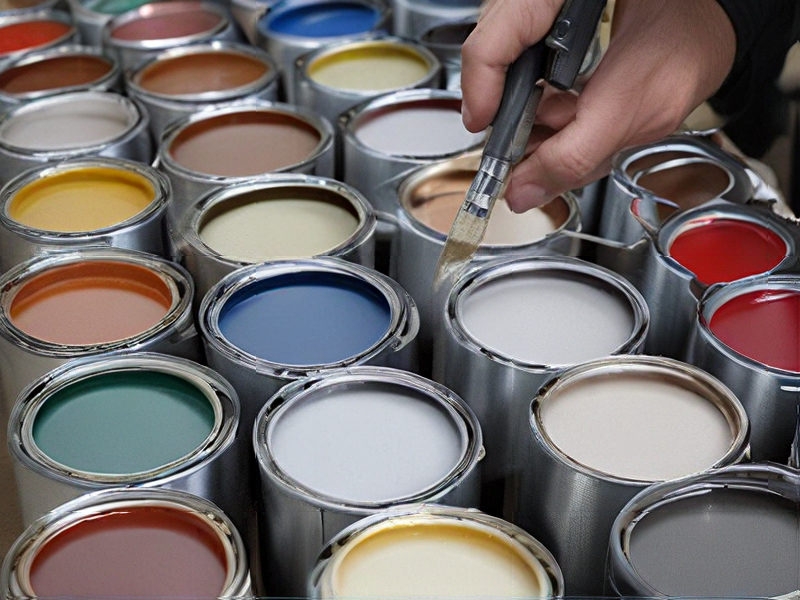
FAQs on Sourcing and Manufacturing from paint in metal in China
FAQs on Sourcing and Manufacturing Metal Paint in China
#### 1. What types of metal paints can I source from China?
China offers a wide range of metal paints including acrylics, epoxy, polyurethane, and rust-proof coatings. Custom formulations are also available based on specific requirements.
#### 2. What are the minimum order quantities (MOQs)?
MOQs can vary by supplier and product type but typically range from 500 to 1,000 liters for custom formulations. Always confirm with the supplier.
#### 3. How do I ensure quality during manufacturing?
Implement a quality control plan, including pre-production samples, in-process inspections, and final product testing. Engage third-party inspection services if needed.
#### 4. What certifications should I look for in suppliers?
Seek suppliers with ISO 9001 certification and appropriate environmental certifications (like RoHS or REACH) to ensure adherence to international quality and safety standards.
#### 5. What is the typical lead time for production?
Lead times generally range from 4 to 12 weeks, depending on the order size, product complexity, and supplier capacity.
#### 6. How do I handle shipping and logistics?
Most suppliers can assist with logistics, but it’s advisable to work with a reliable freight forwarder. Consider shipping costs, customs duties, and lead times.
#### 7. What are the payment terms?
Common payment terms include a 30% deposit upfront and 70% payment before shipment. Some suppliers may accept letters of credit.
#### 8. Are there any environmental regulations to consider?
Yes, be aware of China’s environmental regulations regarding paint manufacturing. Verify that your suppliers comply with local and international standards.
#### 9. How should I choose a supplier?
Research potential suppliers through platforms like Alibaba, verify their credentials, request samples, and read reviews. It’s wise to visit the factory if possible.
By carefully considering these factors, you can successfully source and manufacture metal paint in China.
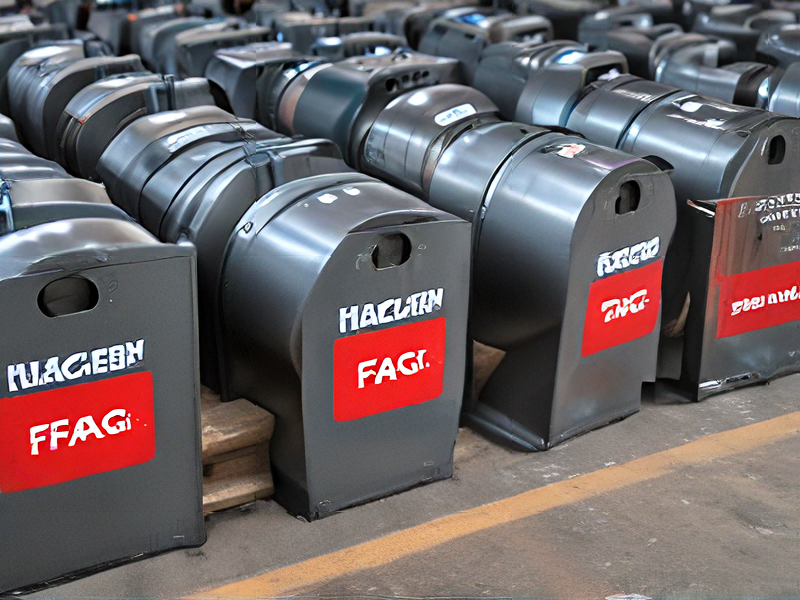