Technology and Applications of pemrograman cnc
Computer Numerical Control (CNC) programming is pivotal in modern manufacturing, enabling precise control of machine tools through coded instructions. CNC utilizes programming languages like G-code to dictate tool movement, speed, and machining operations. Applications span diverse industries such as aerospace, automotive, and electronics manufacturing, where high precision and repeatability are critical.
Key technologies in CNC programming include CAD (Computer-Aided Design) software for part design and CAM (Computer-Aided Manufacturing) software for generating toolpaths from CAD models. CAD/CAM integration streamlines the process from design to production, enhancing efficiency and accuracy. Simulation software validates programs before actual machining, minimizing errors and material waste.
Advanced CNC machines incorporate multi-axis control, allowing complex geometries to be machined in a single setup. This capability is crucial in producing intricate components like turbine blades or medical implants. Additionally, CNC machining centers can perform tasks beyond traditional milling, such as turning, grinding, and laser cutting, further expanding their versatility.
Industry 4.0 trends integrate CNC machines with IoT (Internet of Things) sensors for real-time monitoring and data collection. This connectivity enables predictive maintenance and adaptive machining strategies, optimizing uptime and productivity. Moreover, AI-driven algorithms enhance CNC capabilities by optimizing toolpaths for speed and efficiency based on real-time conditions.
In conclusion, CNC programming underpins modern manufacturing’s precision and flexibility across various sectors. Continual advancements in software, hardware, and integration with emerging technologies ensure CNC remains at the forefront of industrial automation, driving innovation and efficiency in production processes.
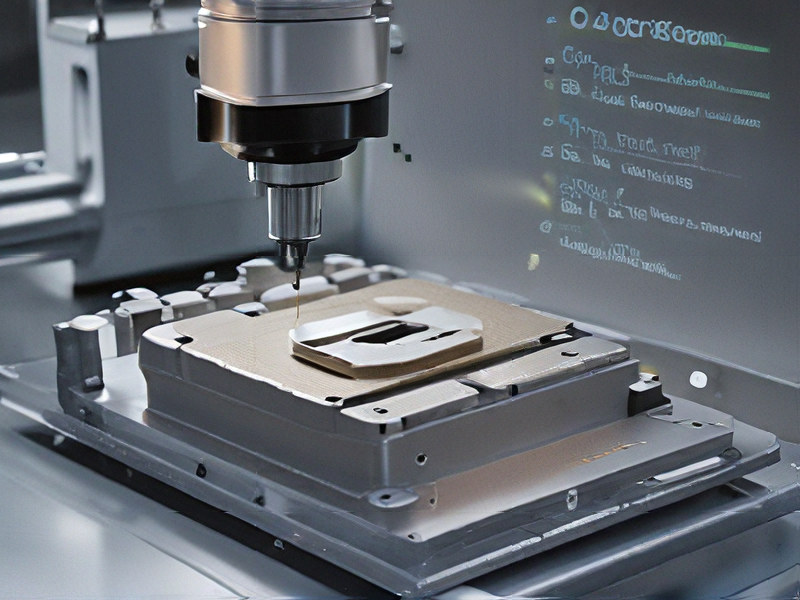
Quality Testing Methods for pemrograman cnc and how to control quality
Quality testing methods for CNC programming typically involve a combination of simulation and verification processes to ensure accuracy and reliability:
1. Simulation: Use CNC simulation software to simulate tool paths and machining operations based on the programmed code. This helps in identifying potential errors in tool movements, collisions, or incorrect dimensions before actual machining.
2. Code Verification: Perform a thorough review of the CNC code (G-code or similar) manually or using software tools designed for code analysis. Check for syntax errors, correct tool paths, tool changes, spindle speeds, and feed rates to ensure they align with the intended machining requirements.
3. Dimensional Inspection: After machining, use precision measuring tools such as calipers, micrometers, or coordinate measuring machines (CMMs) to verify the dimensions and tolerances of machined parts against engineering drawings.
4. Tooling Inspection: Regularly inspect and maintain CNC machine tools, cutting tools, and fixtures to ensure they are in good condition and capable of producing parts within specified tolerances.
5. Process Control: Implement process control measures such as statistical process control (SPC) to monitor key machining parameters over time. This helps in detecting variations and ensuring consistency in part quality.
6. Training and Documentation: Ensure CNC programmers and operators are adequately trained in programming techniques, machine operation, and quality standards. Maintain comprehensive documentation of programming instructions, tooling specifications, and quality control procedures.
By integrating these methods into CNC programming and machining processes, manufacturers can effectively control and maintain quality standards, minimizing errors, and ensuring the production of accurate and high-quality machined components.
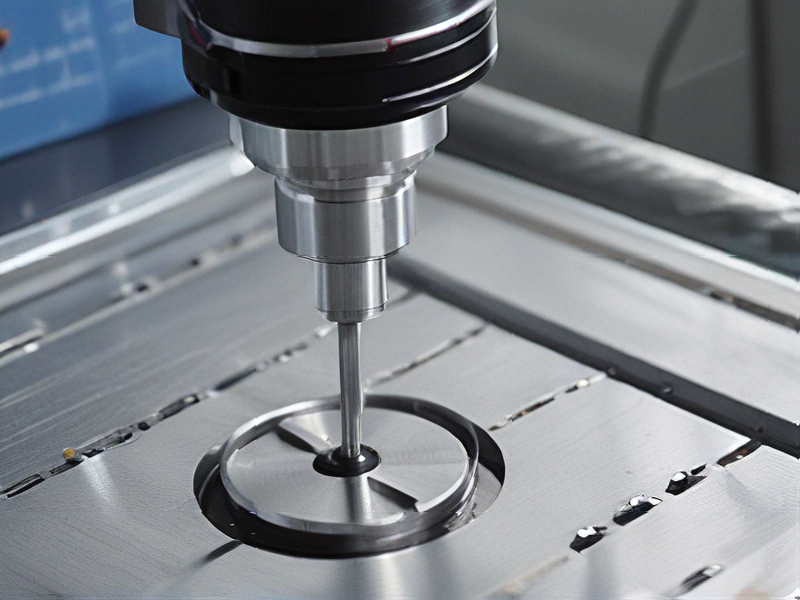
Tips for Procurement and Considerations when Purchasing from pemrograman cnc
When procuring CNC (Computer Numerical Control) programming services, several key considerations can ensure a successful purchase:
1. Technical Expertise: Ensure the service provider has proficient knowledge and experience in CNC programming relevant to your specific needs. Ask for examples of past projects similar to yours.
2. Software Compatibility: Verify that the CNC programming software used aligns with your existing manufacturing equipment and processes. Compatibility issues can lead to delays and inefficiencies.
3. Quality Assurance: Inquire about the provider’s quality control measures. This includes how they ensure accuracy, precision, and adherence to specifications in their programming.
4. Cost and Budget: Obtain detailed quotes and compare them across multiple providers. Consider not only the initial programming costs but also potential savings through efficiency improvements or reduced material waste.
5. Turnaround Time: Understand the provider’s typical turnaround times for programming tasks. This is crucial to meeting production deadlines and managing workflow effectively.
6. Support and Maintenance: Evaluate what support the provider offers post-programming. This includes troubleshooting, updates, and ongoing technical assistance.
7. Communication and Collaboration: Effective communication is essential. Ensure the provider is responsive to queries and can collaborate seamlessly with your engineering or production team.
8. References and Reviews: Check for testimonials or references from other clients. This can provide insights into the provider’s reliability, customer service, and overall satisfaction.
9. Contractual Agreements: Clearly define deliverables, timelines, payment terms, and intellectual property rights in a formal contract to protect both parties.
10. Continuous Improvement: Look for providers who emphasize continuous improvement and innovation in CNC programming techniques. This ensures you benefit from advancements in technology and methodology.
By considering these factors, you can make a well-informed decision when purchasing CNC programming services, ensuring they meet your technical requirements, budget constraints, and operational timelines effectively.
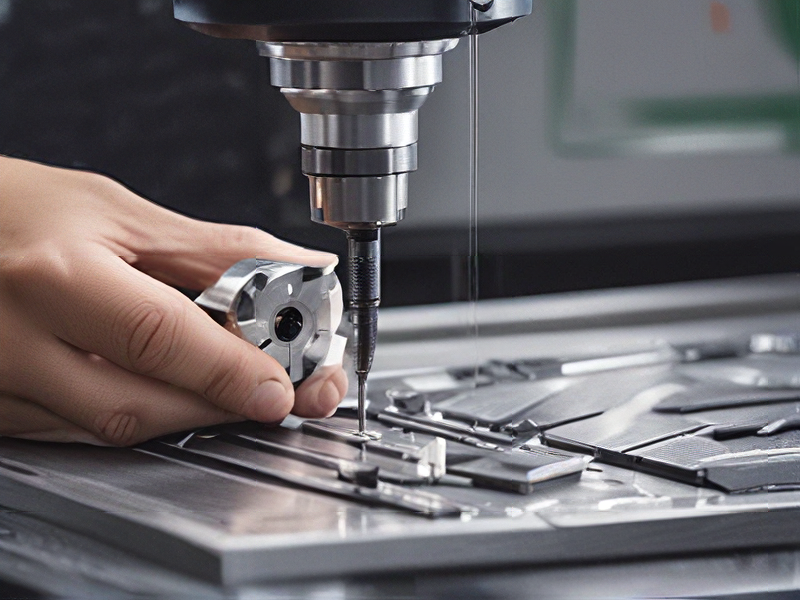
FAQs on Sourcing and Manufacturing from pemrograman cnc in China
When sourcing and manufacturing from CNC programming in China, consider these FAQs:
1. What are the key advantages of sourcing CNC services from China?
China offers cost-effective solutions due to lower labor and operational costs. It also boasts a vast manufacturing infrastructure capable of handling large-scale production.
2. How do I ensure quality when outsourcing CNC manufacturing to China?
Conduct thorough supplier assessments, including factory visits if possible. Implement quality control measures at different production stages and consider certifications like ISO standards.
3. What are the common challenges in sourcing CNC services from China?
Language barriers, cultural differences, and intellectual property protection are significant challenges. Effective communication and clear contracts are crucial to overcoming these hurdles.
4. How can I protect my designs and intellectual property?
Work with reputable suppliers and consider legal protections such as non-disclosure agreements (NDAs) and trademarks. Registering your designs and patents can offer additional security.
5. What is the typical lead time for CNC manufacturing in China?
Lead times vary depending on complexity and order volume. Generally, expect lead times between 2-6 weeks, but this can be shorter or longer based on specific project requirements.
6. What are the payment terms usually accepted by CNC manufacturers in China?
Common payment terms include T/T (Telegraphic Transfer), L/C (Letter of Credit), and sometimes PayPal for smaller transactions. Negotiate terms that balance risk and ensure timely delivery.
7. How do I navigate import/export regulations and logistics?
Partner with freight forwarders experienced in shipping from China. Stay informed about tariffs, customs procedures, and import regulations specific to your country.
Navigating these considerations ensures a smoother process when sourcing CNC services from China, optimizing cost-effectiveness and quality assurance.
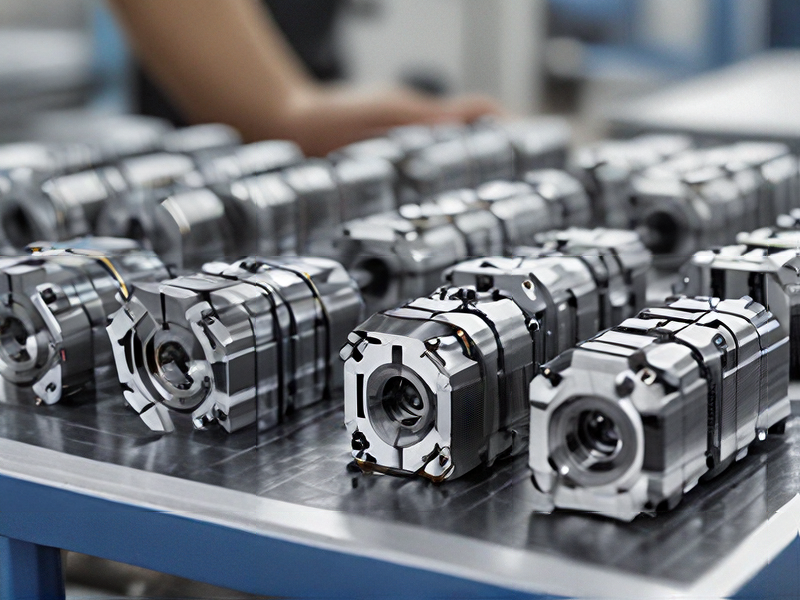