Technology and Applications of precision machines
Precision machines encompass a diverse array of technologies designed to achieve extremely accurate and repeatable outcomes in manufacturing and beyond. These machines are crucial in industries such as aerospace, automotive, electronics, and medical devices, where precision is paramount.
Technologies: Precision machines utilize advanced mechanisms like CNC (Computer Numerical Control) systems, which automate machining processes with high accuracy. CNC machines can perform complex tasks such as milling, turning, and grinding with minimal human intervention, ensuring consistency and precision. Other technologies include EDM (Electrical Discharge Machining), laser cutting, and 3D printing, each offering unique capabilities in achieving precise geometries and tolerances.
Applications: In aerospace, precision machines manufacture critical components like turbine blades and aircraft structures, meeting stringent safety and performance standards. In electronics, they fabricate microchips and circuit boards with nanoscale accuracy, enabling faster and more efficient devices. Medical applications range from manufacturing surgical instruments to producing implants customized to patient anatomy, ensuring compatibility and functionality.
Precision machines also play a vital role in research and development, enabling the prototyping of new designs and materials with exact specifications. Their versatility extends to industries like watchmaking, where intricate parts demand micrometer-level precision.
In conclusion, precision machines are indispensable across industries that prioritize accuracy and quality. Their technological advancements continue to drive innovation, supporting the development of new materials, products, and applications that shape modern technology and manufacturing practices.
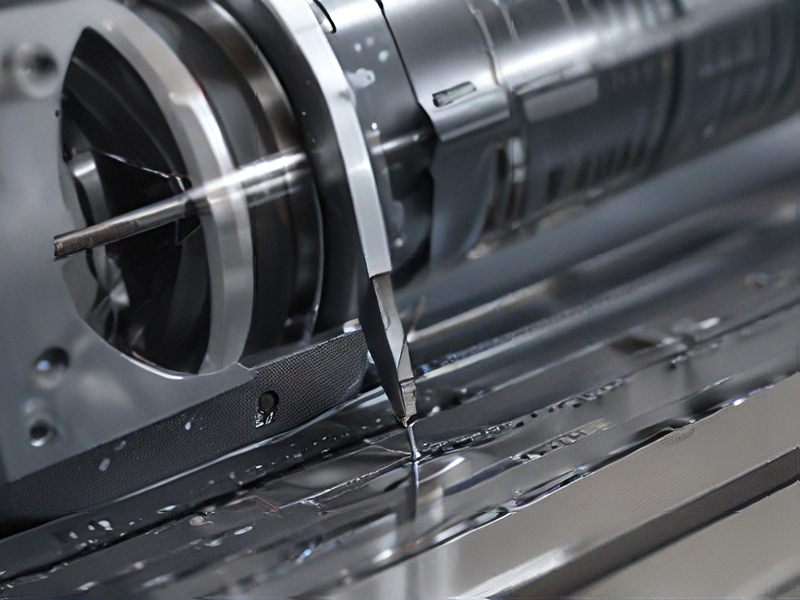
Quality Testing Methods for precision machines and how to control quality
Quality testing methods for precision machines typically involve a combination of techniques to ensure accuracy and reliability:
1. Dimensional Metrology: This includes measurements using tools like micrometers, calipers, and coordinate measuring machines (CMMs) to verify part dimensions against specifications.
2. Surface Roughness Analysis: Utilizing profilometers or optical interferometers to assess the surface quality and texture of machined components.
3. Alignment and Positioning Tests: Ensuring proper alignment of machine components using laser alignment tools or precision levels to maintain accuracy.
4. Functional Testing: Running parts through simulated operational tests to verify functionality under expected conditions.
5. Material Analysis: Employing spectroscopy or material testing techniques to ensure the integrity and composition of materials used in precision components.
To control quality effectively:
1. Establish Clear Specifications: Define precise tolerances and quality standards for each component or product.
2. Regular Calibration: Maintain and calibrate measuring instruments regularly to ensure accuracy in measurements.
3. Process Monitoring: Implement process controls and monitoring systems to detect deviations early.
4. Training and Skill Development: Ensure operators and technicians are well-trained in operating machines and conducting quality tests.
5. Quality Assurance Protocols: Develop robust protocols for quality checks at various stages of production to catch defects early.
By integrating these methods and controls, manufacturers can uphold high standards of precision and reliability in their machines, ensuring consistent quality output.
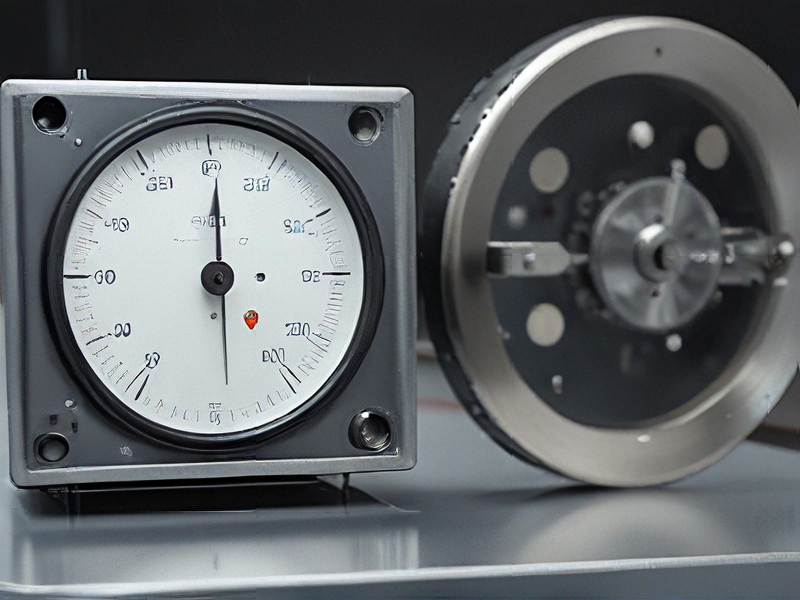
Tips for Procurement and Considerations when Purchasing from precision machines
When purchasing precision machines, several considerations can ensure you make an informed procurement decision:
1. Accuracy and Precision: Verify the machine’s specifications regarding accuracy levels and precision capabilities. This ensures it meets your production needs.
2. Reliability and Durability: Evaluate the machine’s reputation for reliability and longevity. Check reviews, warranties, and service agreements to understand its lifespan and maintenance requirements.
3. Ease of Use and Integration: Choose a machine that integrates smoothly into your existing processes. User-friendly interfaces and compatibility with your current systems reduce training time and operational disruptions.
4. Supplier Reputation: Research the supplier’s reputation for customer support, spare parts availability, and service responsiveness. A reliable supplier ensures ongoing support and maintenance.
5. Cost and ROI: Consider both initial purchase costs and long-term return on investment (ROI). Factor in operational costs, maintenance expenses, and potential productivity gains to assess overall cost-effectiveness.
6. Technology and Innovation: Assess the machine’s technological features and innovations. Up-to-date technology may offer improved efficiency, automation capabilities, and future scalability.
7. Safety and Compliance: Ensure the machine meets industry safety standards and regulatory requirements. Prioritize machines with built-in safety features and clear compliance certifications.
8. Training and Support: Evaluate the training and support options provided by the supplier. Comprehensive training programs and ongoing technical support enhance operational efficiency and troubleshooting capabilities.
By focusing on these considerations, you can make a well-informed decision when purchasing precision machines, ensuring they meet your production requirements while providing long-term value and reliability.
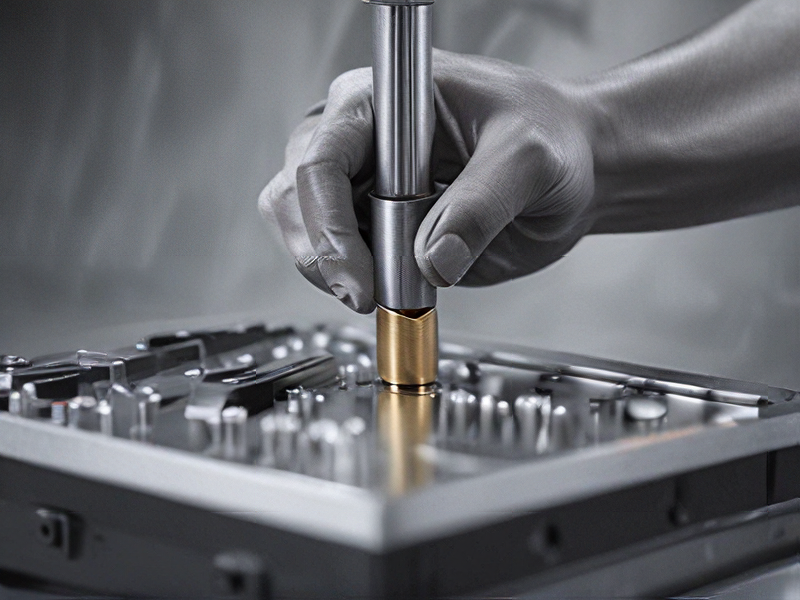
FAQs on Sourcing and Manufacturing from precision machines in China
Certainly! Here are some FAQs on sourcing and manufacturing precision machines in China:
1. Why should I consider sourcing precision machines from China?
China offers competitive pricing due to lower manufacturing costs and a robust industrial infrastructure for precision engineering.
2. How can I ensure quality when sourcing from China?
Select suppliers with ISO certifications and a proven track record. Conduct factory audits and request samples to assess quality standards.
3. What are the typical lead times for manufacturing precision machines in China?
Lead times vary but generally range from 4-12 weeks depending on complexity and customization requirements.
4. How do I manage communication and language barriers?
Use clear and detailed technical specifications. Employ bilingual project managers or translators if necessary to facilitate effective communication.
5. What are the potential challenges in sourcing from China?
Challenges may include intellectual property protection, logistical complexities, and cultural differences affecting business practices.
6. What are the advantages of partnering with a sourcing agent or consultant?
Sourcing agents provide local expertise, negotiate pricing, oversee quality control, and handle logistics, reducing risks and enhancing efficiency.
7. How can I protect my intellectual property when manufacturing in China?
Use non-disclosure agreements (NDAs), trademarks, and patents where applicable. Choose suppliers with a reputation for IP protection.
8. What are the payment terms typically used in China?
Common payment terms include T/T (Telegraphic Transfer) and L/C (Letter of Credit), with initial deposits and final payments upon inspection and acceptance.
9. How important is it to visit the manufacturing facilities in China?
Visiting facilities allows firsthand evaluation of capabilities, quality control measures, and overall production conditions before committing to partnership.
10. What steps can I take to ensure ethical sourcing practices?
Verify supplier compliance with international labor standards and environmental regulations. Consider certifications like SA8000 or ISO 14001.
Navigating sourcing and manufacturing in China requires careful planning, clear communication, and strategic partnerships to ensure successful outcomes.
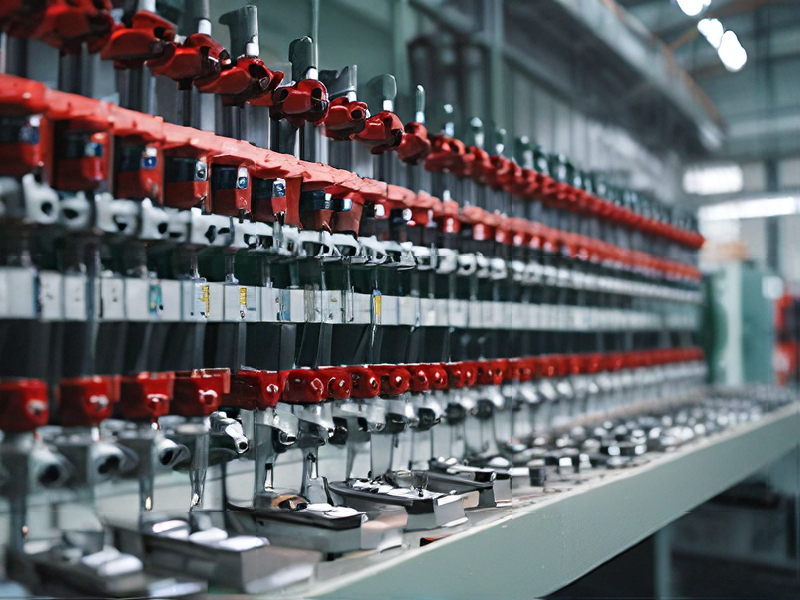