Technology and Applications of print 3d metal
3D metal printing, or additive manufacturing, has revolutionized various industries by enabling the production of complex metal parts with reduced waste and enhanced customization. This technology utilizes techniques such as Powder Bed Fusion (e.g., Selective Laser Melting or SLM) and Directed Energy Deposition (DED), where metal powders or wires are selectively melted layer by layer to create intricate designs that traditional methods cannot achieve.
Key applications include aerospace, automotive, and medical sectors. In aerospace, companies like GE and Boeing leverage 3D metal printing for lightweight components, enhancing fuel efficiency and performance. In the automotive industry, manufacturers utilize it for rapid prototyping and producing low-volume, customized parts, significantly speeding up development cycles. In medicine, custom implants and prosthetics tailored to individual patients improve fit and functionality.
The advantages of 3D metal printing include reduced material waste, shorter lead times, and the ability to create geometrically complex structures. It also allows for on-demand production, minimizing inventory and logistics costs. Moreover, advancements in materials, including titanium alloys and stainless steels, expand the scope of applications.
Challenges remain, including high initial costs, slow production rates for mass manufacturing, and the need for post-processing to achieve desired surface finish and mechanical properties. However, ongoing research and technological advancements are expected to address these issues, further integrating 3D metal printing into mainstream manufacturing processes.
Ultimately, 3D metal printing stands poised to transform production paradigms across various sectors, fostering innovation and efficiency in the creation of metal components.
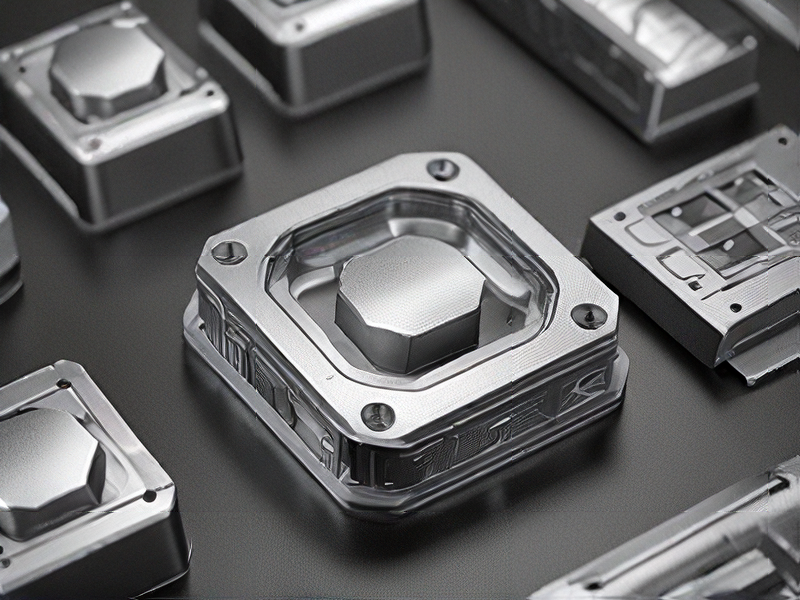
Quality Testing Methods for print 3d metal and how to control quality
Quality testing for metal 3D printed parts is crucial to ensure performance, reliability, and safety. Here are key methods and strategies to control quality:
1. Visual Inspection: Conduct a preliminary visual assessment to detect surface defects, such as cracks, warping, or inconsistent layers. This initial inspection can help identify any glaring issues before more detailed testing.
2. Dimensional Measurement: Utilize precision tools like calipers and coordinate measuring machines (CMM) to verify that the printed dimensions conform to the CAD specifications. Tolerances should be defined and adhered to for functional parts.
3. Non-Destructive Testing (NDT): Techniques such as ultrasonic testing, X-ray, or infrared thermography can be employed to identify internal defects and voids without damaging the part. NDT is essential for critical components in aerospace and biomedical applications.
4. Mechanical Testing: Conduct tensile, hardness, and fatigue tests to evaluate the material properties and structural integrity of the printed metal. These tests help to understand how the part will behave under operational conditions.
5. Microstructure Analysis: Use microscopy to observe the microstructure of the metal. Analyzing grain size and morphology can reveal the effects of the printing process on material performance.
6. Process Control: Implementing strict control over the 3D printing parameters (temperature, speed, powder quality) is essential. Utilize software for real-time monitoring and adjust parameters as needed to maintain consistency.
7. Post-Processing Inspection: Evaluate any post-processed parts to ensure that additional treatments (e.g., heat treatment, machining) meet quality standards.
By integrating these methods into a comprehensive quality assurance plan, manufacturers can enhance the reliability of metal 3D printed components.
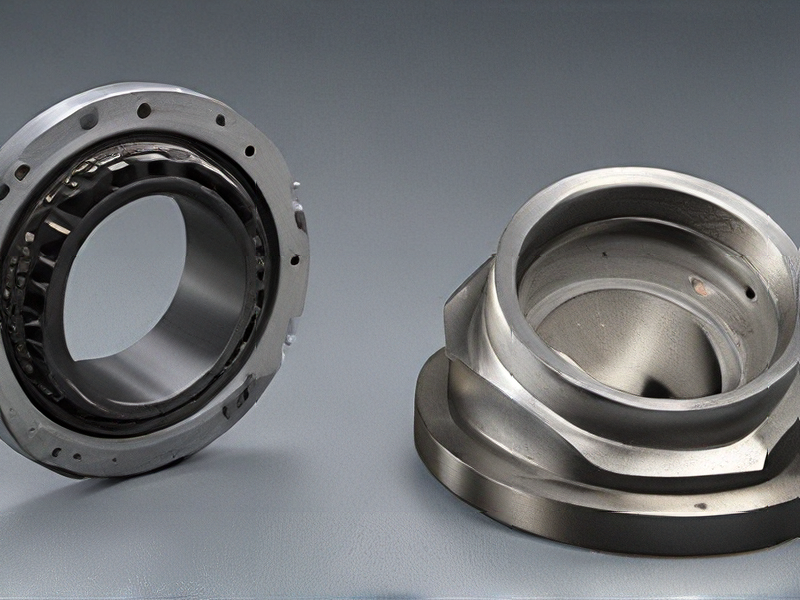
Tips for Procurement and Considerations when Purchasing from print 3d metal
When procuring 3D metal printing services or equipment, consider the following essential tips and considerations:
1. Understand Your Needs:
– Define the specific materials, tolerances, and finishing requirements necessary for your project.
– Assess the volume and type of parts you need, whether prototypes or production runs.
2. Material Selection:
– Investigate various metal options like titanium, aluminum, or stainless steel based on strength, weight, and corrosion resistance.
– Verify the supplier’s material certification and quality standards.
3. Supplier Evaluation:
– Research potential suppliers thoroughly; check their experience, capabilities, and customer reviews.
– Request case studies to understand their expertise with similar projects.
4. Cost Considerations:
– Evaluate the total cost of ownership, factoring in not just the price of parts but also shipping, post-processing, and potential rework.
– Compare quotes but be cautious of overly low bids that may compromise quality.
5. Technology and Equipment:
– Ensure the supplier utilizes up-to-date technologies such as Selective Laser Melting (SLM) or Electron Beam Melting (EBM).
– Ask about their maintenance protocols for machinery to ensure quality consistency.
6. Lead Times and Deliverables:
– Confirm lead times that align with your project timelines.
– Clarify deliverables, including documentation and conformity certifications.
7. Post-Processing Capabilities:
– Discuss available finishing options such as heat treatment, machining, or surface finishing to enhance performance.
8. Intellectual Property (IP) Protection:
– Address IP concerns in contracts, ensuring that your designs and proprietary information are safeguarded.
By comprehensively addressing these considerations, you can streamline the procurement process and ensure successful outcomes in 3D metal printing projects.
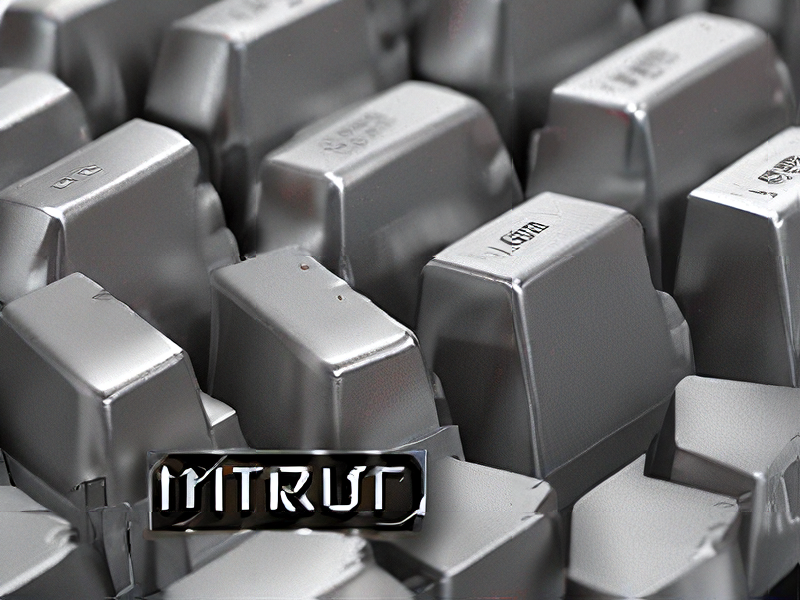
FAQs on Sourcing and Manufacturing from print 3d metal in China
FAQs on Sourcing and Manufacturing 3D Printed Metal in China
1. What types of metal can be 3D printed in China?
China offers a variety of metals for 3D printing, including aluminum, titanium, stainless steel, and cobalt chrome. Each material has unique properties suited for different applications.
2. How do I find reliable suppliers?
Research potential suppliers through platforms like Alibaba, Globalsources, or local trade shows. Verify their credentials, reviews, and previous work. Request samples to assess quality.
3. What is the typical lead time for 3D printed metal parts?
Lead times vary based on complexity and batch size but typically range from 2 to 8 weeks. Always confirm specific timelines with your chosen supplier.
4. What certifications should I look for?
Ensure the supplier adheres to relevant quality standards such as ISO 9001, AS9100 (for aerospace), or medical-related certifications as applicable.
5. How do I manage communication barriers?
Choose suppliers with English-speaking representatives and utilize clear, structured communication. Consider using translation services if needed.
6. What are the cost factors for 3D printing in China?
Costs depend on material, complexity, volume, and post-processing requirements. Request detailed quotes to understand pricing structures.
7. How can I ensure quality control?
Implement quality assurance processes, including regular inspections and testing, and ask for documentation like inspection reports and certificates from manufacturers.
8. What are the common shipping options?
Shipping methods include air freight for urgency and sea freight for cost-effectiveness. Discuss trade terms (e.g., FOB, CIF) with your supplier for clarity on logistics.
9. Are there any legal considerations?
Ensure that you have clear agreements on intellectual property rights and compliance with local regulations in China regarding manufacturing.
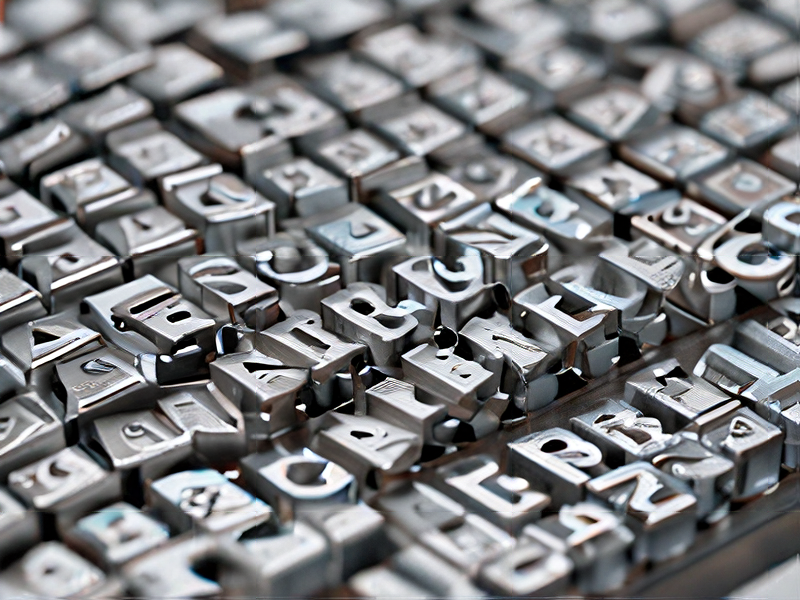