Technology and Applications of printing 3d metal
3D metal printing, or additive manufacturing, involves creating metal objects layer by layer from a digital model using techniques like Selective Laser Melting (SLM), Electron Beam Melting (EBM), and Bound Metal Deposition (BMD). These technologies enable the production of complex geometries that are often impossible to achieve with traditional machining methods.
Technology:
1. Selective Laser Melting (SLM): Uses a laser to selectively melt powdered metal, layer by layer, to create high-density parts. It’s capable of producing intricate designs with good mechanical properties.
2. Electron Beam Melting (EBM): Utilizes an electron beam in a vacuum to melt metal powder. It is often used for high-temperature alloys and is efficient for larger parts.
3. Binder Jetting: Involves laying down a binder on metal powder, which is then sintered in a furnace. This method allows for high-speed production but may require post-processing for strength.
4. Bound Metal Deposition: This technology extrudes a metal-polymer composite filament, which is later sintered to achieve full metallic properties.
Applications:
3D metal printing finds extensive applications across various industries:
– Aerospace: Lightweight components, fuel nozzles, and complex parts that reduce weight and improve performance.
– Healthcare: Customized implants, prosthetics, and surgical instruments tailored to individual patient needs.
– Automotive: Rapid prototyping and production of complex parts, tooling, and fixtures that enhance manufacturing efficiency.
– Defense: Production of specialized components with intricate designs to meet strict performance standards.
In summary, 3D metal printing is revolutionizing manufacturing by offering innovative solutions for complex designs, material efficiency, and rapid production across industries.
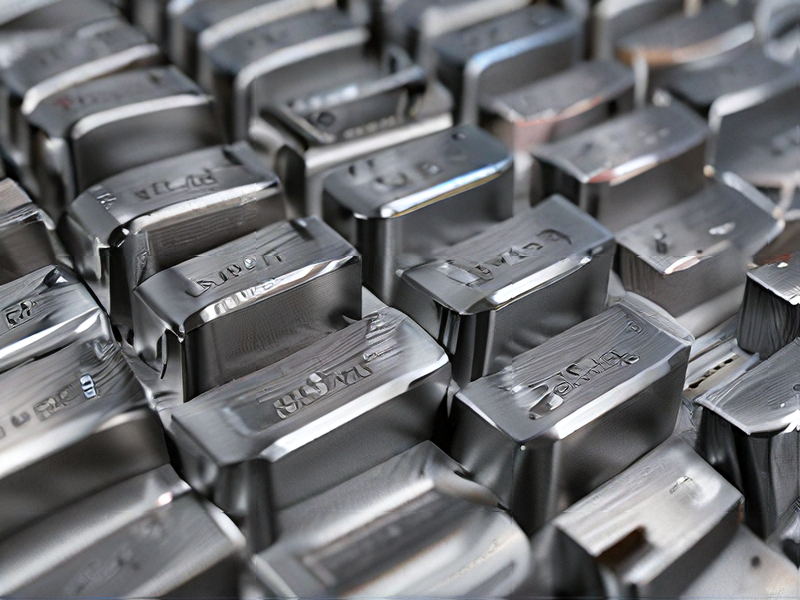
Quality Testing Methods for printing 3d metal and how to control quality
Quality testing for 3D metal printing is essential to ensure the mechanical integrity and functionality of printed components. Here are key methods and controls:
1. Visual Inspection: Start with a visual check for surface defects such as layer misalignments, voids, or excess material. This preliminary assessment can help identify obvious flaws.
2. Dimensional Analysis: Use calipers or coordinate measuring machines (CMM) to verify that printed dimensions meet specifications. Tolerances should align with design requirements, ensuring parts fit accurately.
3. Non-Destructive Testing (NDT): Techniques such as ultrasonic testing, X-ray computed tomography, and magnetic particle inspection can reveal internal defects without damaging the part. These methods are crucial for detecting anomalies like porosity or inclusions.
4. Mechanical Testing: Conduct tensile, compressive, and fatigue tests to assess the material’s mechanical properties. These tests provide essential data on yield strength, ductility, and toughness.
5. Microstructural Analysis: Use optical microscopy or scanning electron microscopy (SEM) to examine the microstructure. Assess grain size, phase distribution, and defects at a microscopic level, which significantly influence mechanical properties.
6. Heat Treatment Control: Implement appropriate heat treatment processes to relieve stresses and enhance material properties. Monitor the temperature and time closely to ensure consistency.
7. Process Monitoring: Utilize real-time monitoring tools during printing, such as infrared thermography and melt pool monitoring, to detect anomalies as they occur. This allows for immediate adjustments to maintain quality.
By integrating these testing methods and controls throughout the manufacturing process, manufacturers can ensure the quality and reliability of 3D-printed metal parts, leading to better performance in their intended applications.
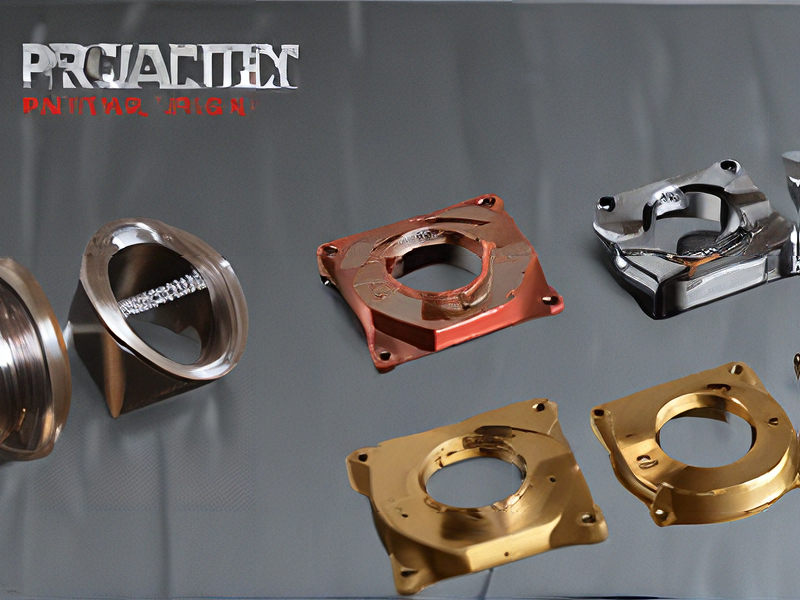
Tips for Procurement and Considerations when Purchasing from printing 3d metal
When procuring 3D metal printing services, several key considerations can ensure a successful purchase:
1. Supplier Expertise: Choose a supplier with a proven track record in metal 3D printing. Check their experience, certifications, and the range of industries they serve to ensure they can meet your specific needs.
2. Technology and Materials: Understand the types of 3D printing technologies offered (e.g., DMLS, SLM) and the range of metals available (e.g., titanium, aluminum, stainless steel). Ensure they can provide the specific material required for your application.
3. Quality Assurance: Inquire about quality control measures. Request information on their testing methods (e.g., non-destructive testing), certifications (like ISO 9001), and if they provide detailed reports on the quality of the produced parts.
4. Prototype vs. Production Runs: Clarify your needs, whether for prototyping or full-scale production. Some companies specialize in low-volume prototyping, while others may be better for high-volume production, which could affect pricing and turnaround time.
5. Lead Times: Discuss production timelines upfront. Understand the typical lead times for both prototype and production runs, and factor in potential delays, especially in high-demand seasons.
6. Cost Analysis: Get detailed quotes that include material costs, printing, post-processing, and shipping. Compare multiple suppliers to ensure competitiveness while not compromising on quality.
7. Customer Support: Evaluate the level of customer service offered. A supplier that provides responsive support can help address issues throughout the production process.
8. Intellectual Property: Ensure that your intellectual property is protected, especially if you’re providing designs. Consider confidentiality agreements as necessary.
By taking these factors into account, you can make informed decisions that align with your project goals.
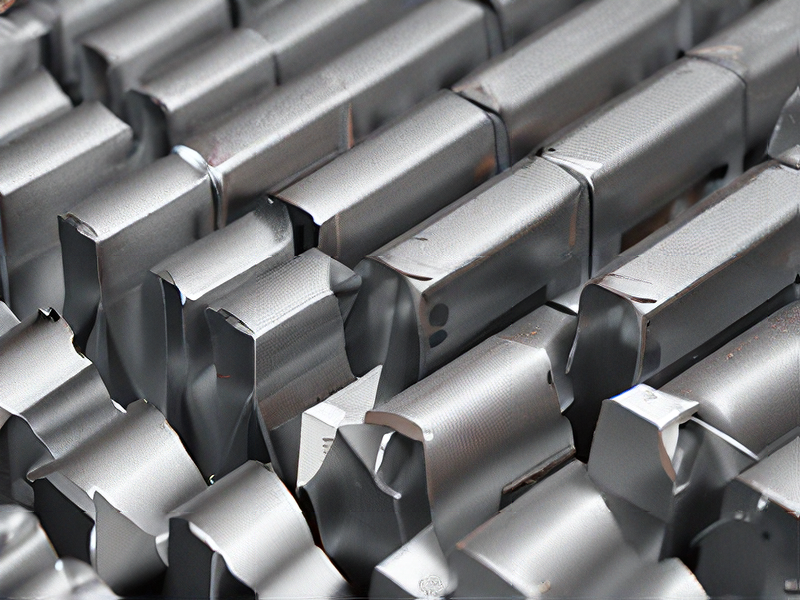
FAQs on Sourcing and Manufacturing from printing 3d metal in China
FAQs on Sourcing and Manufacturing 3D Metal Printing in China
1. What is 3D metal printing?
3D metal printing, or additive manufacturing, involves creating metal parts layer by layer using a digital design. This method allows for complex geometries that traditional manufacturing can’t achieve.
2. Why source 3D metal printing from China?
China offers a robust manufacturing infrastructure, skilled labor, and competitive pricing, making it an attractive option for businesses looking to source 3D metal printing services.
3. What materials can be used in 3D metal printing?
Common materials include stainless steel, aluminum, titanium, and cobalt-chrome alloys. The choice of material depends on the application and required properties.
4. How do I select a reliable manufacturer?
Research potential manufacturers by checking their certifications, past projects, and customer reviews. It’s also beneficial to request prototypes to assess quality.
5. What are the lead times for production?
Lead times can vary based on complexity and volume, typically ranging from a few weeks to several months. Discuss timelines upfront with the manufacturer.
6. What are the quality assurance measures?
Reputable manufacturers should have quality control processes in place, including inspections, certifications, and compliance with industry standards.
7. How do I handle shipping and logistics?
Work with manufacturers that offer logistics support. Familiarize yourself with international shipping regulations and consider duties, tariffs, and local customs.
8. What are the payment terms?
Payment terms may vary; however, most manufacturers require a deposit upfront, with the balance payable upon completion or before shipping.
9. Are there intellectual property considerations?
Yes. Ensure you have non-disclosure agreements in place to protect your designs and consider trademarking key technologies.
10. How can I ensure my project is protected legally?
Consult legal experts familiar with international manufacturing laws to draft contracts that safeguard your interests.
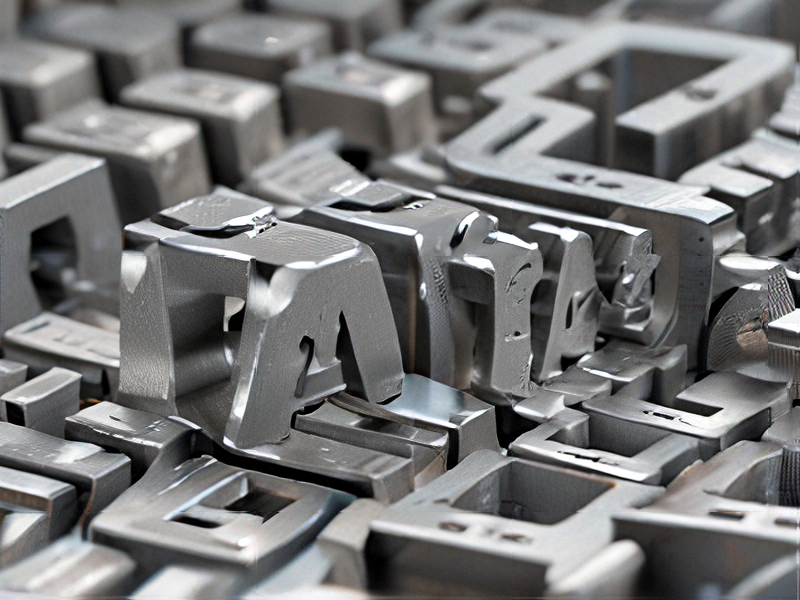