Technology and Applications of programming a cnc machine
Programming a CNC (Computer Numerical Control) machine involves translating design specifications into commands that guide the machine’s tools to create precise parts. This process utilizes specialized software where programmers input geometrical dimensions, tooling information, and cutting parameters.
Key applications include:
1. CAD/CAM Software: Computer-Aided Design (CAD) software is used for creating 2D or 3D digital models of parts, while Computer-Aided Manufacturing (CAM) software translates these models into toolpaths and generates G-code, the programming language understood by CNC machines.
2. Toolpath Generation: CAM software calculates the optimal toolpaths based on factors like tool geometry, material properties, and desired surface finish. This ensures efficient cutting while minimizing tool wear and material waste.
3. Simulation: Before actual machining, virtual simulation ensures that the toolpaths are collision-free and that the machining process will produce the desired part accurately.
4. Multi-axis Machining: CNC machines can operate in multiple axes (typically 3, 4, or 5 axes), allowing complex geometries to be machined without repositioning the workpiece. This capability is crucial in industries like aerospace and automotive for manufacturing intricate components.
5. Automation and Integration: CNC machines often integrate with other manufacturing systems such as robotic loaders, quality control devices, and ERP (Enterprise Resource Planning) systems to streamline production processes and maintain consistency in output quality.
6. Precision and Repeatability: CNC machining offers high accuracy and repeatability, making it suitable for producing identical parts in large quantities or intricate one-off prototypes with tight tolerances.
Overall, CNC programming and machining play a vital role across various industries, from aerospace and automotive to medical device manufacturing, enabling efficient production of complex parts with high precision and reliability.
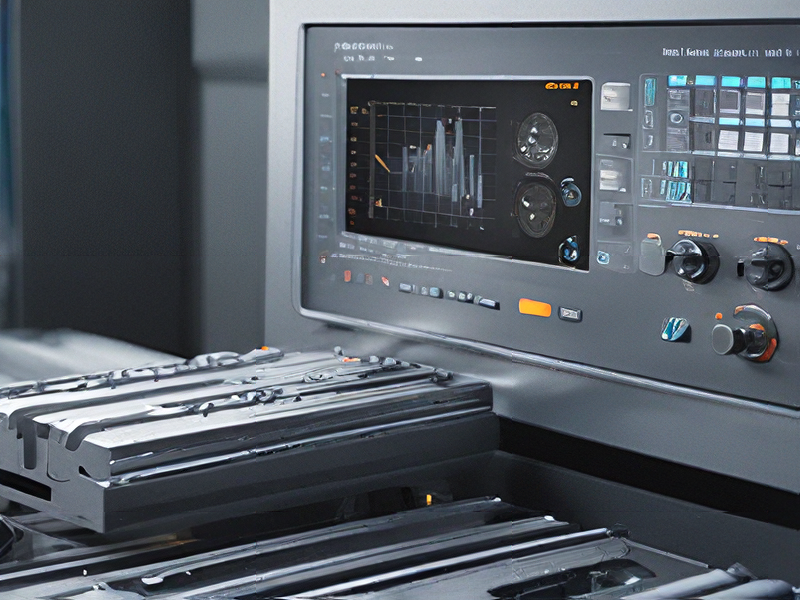
Quality Testing Methods for programming a cnc machine and how to control quality
Quality testing methods for programming a CNC (Computer Numerical Control) machine involve several key approaches to ensure precision and reliability:
1. Simulation Testing: Utilize software simulations to verify the CNC program’s behavior and outputs before actual machining. This helps in detecting errors in tool paths, speeds, feeds, and collisions.
2. First Article Inspection (FAI): Conduct a thorough inspection of the first piece manufactured using the CNC program. Measure critical dimensions and compare them against the design specifications to identify any discrepancies.
3. In-process Monitoring: Implement sensors and monitoring systems during machining to detect deviations in tool wear, dimensional accuracy, and surface finish in real-time. This allows for immediate adjustments and corrections.
4. Statistical Process Control (SPC): Use SPC techniques to monitor process variation over time. Control charts for key process parameters such as dimensional accuracy and surface roughness help in maintaining consistency and identifying trends that may indicate process drift.
5. Tool Calibration and Maintenance: Regularly calibrate CNC machine tools and verify their performance using precision instruments. Establish a preventive maintenance schedule to ensure tools are in optimal condition for accurate machining.
To control quality effectively:
– Documented Procedures: Develop and follow standardized procedures for CNC programming, setup, and operation.
– Training and Skill Development: Train operators and programmers in quality control methods and the use of inspection tools.
– Feedback Mechanism: Establish a feedback loop where operators report issues encountered during machining, enabling continuous improvement.
By integrating these methods into CNC machining processes, manufacturers can enhance quality control, minimize scrap, and improve overall productivity.
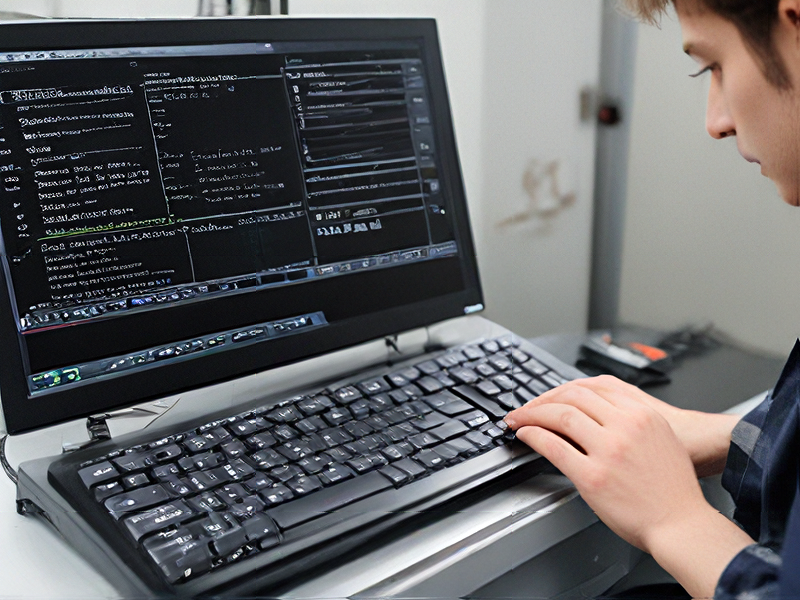
Tips for Procurement and Considerations when Purchasing from programming a cnc machine
When procuring a CNC machine, several key considerations can ensure you make an informed decision:
1. Machine Capability: Evaluate the CNC machine’s specifications such as axis travel, spindle speed, and tool capacity to ensure it meets your manufacturing needs and can handle your typical project sizes.
2. Accuracy and Precision: Check the machine’s accuracy specifications (like positioning and repeatability) to ensure it can achieve the precision required for your parts.
3. Software Compatibility: Ensure the CNC machine is compatible with your existing CAD/CAM software. Compatibility issues can lead to inefficiencies and extra costs.
4. Support and Training: Consider the availability of technical support from the manufacturer or supplier. Training programs for operators can also reduce downtime and improve productivity.
5. Maintenance Requirements: Understand the maintenance schedule and requirements of the CNC machine. Regular maintenance ensures longevity and reliability.
6. Cost Considerations: Compare initial purchase costs, ongoing operational costs (like energy consumption and tooling), and potential cost savings through increased productivity or reduced scrap.
7. Supplier Reputation: Research the reputation and reliability of the supplier or manufacturer. Customer reviews and testimonials can provide insights into their after-sales support and product quality.
8. Future Expansion: Consider future needs and whether the CNC machine can be upgraded or expanded with additional features or capabilities.
9. Safety Features: Ensure the machine complies with safety regulations and includes necessary safety features to protect operators.
10. Integration with Existing Workflow: Evaluate how easily the CNC machine can integrate into your existing production workflow and infrastructure.
By carefully considering these factors, you can select a CNC machine that not only meets your current machining requirements but also supports your long-term manufacturing goals efficiently and effectively.
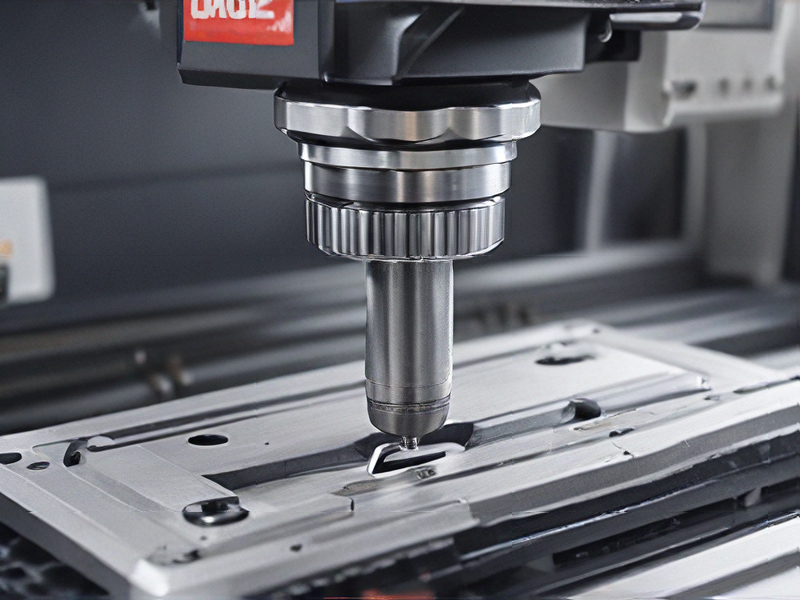
FAQs on Sourcing and Manufacturing from programming a cnc machine in China
When sourcing CNC machining services from China, several key considerations and frequently asked questions (FAQs) often arise:
1. Quality Assurance: How do Chinese manufacturers ensure quality control?
– Reputable manufacturers employ strict quality control processes, including inspections at various stages of production. They often adhere to international quality standards like ISO.
2. Communication: How do I communicate design specifications effectively?
– Clear communication is crucial. Utilize detailed drawings and specifications, ideally in both English and Chinese, to minimize misunderstandings.
3. Lead Times: What are typical lead times for CNC machining in China?
– Lead times vary based on complexity and quantity but are generally competitive. It’s advisable to clarify lead times before placing orders.
4. Cost Factors: What factors influence pricing?
– Pricing depends on material costs, machining complexity, tolerances required, batch size, and surface finishes. Request detailed quotes to understand cost breakdowns.
5. Intellectual Property: How can I protect my designs and intellectual property?
– Sign non-disclosure agreements (NDAs) and ensure manufacturers respect your intellectual property rights. Consider legal advice if necessary.
6. Logistics: How are shipping and customs handled?
– Manufacturers often assist with shipping arrangements. Understand shipping costs, transit times, and customs duties to avoid surprises.
7. Payment Terms: What are typical payment terms?
– Payment terms vary but often include initial deposits and final payments upon satisfactory completion and inspection of goods.
8. Prototyping: Can I request prototypes before full production?
– Many manufacturers offer prototyping services to validate designs before scaling production. Clarify prototyping costs and timelines upfront.
9. After-Sales Support: What support is provided after delivery?
– Reputable manufacturers offer warranties and support for defects or issues post-delivery. Ensure these terms are clearly defined in your agreement.
Navigating these FAQs will help ensure a smoother sourcing and manufacturing process when programming CNC machines in China.
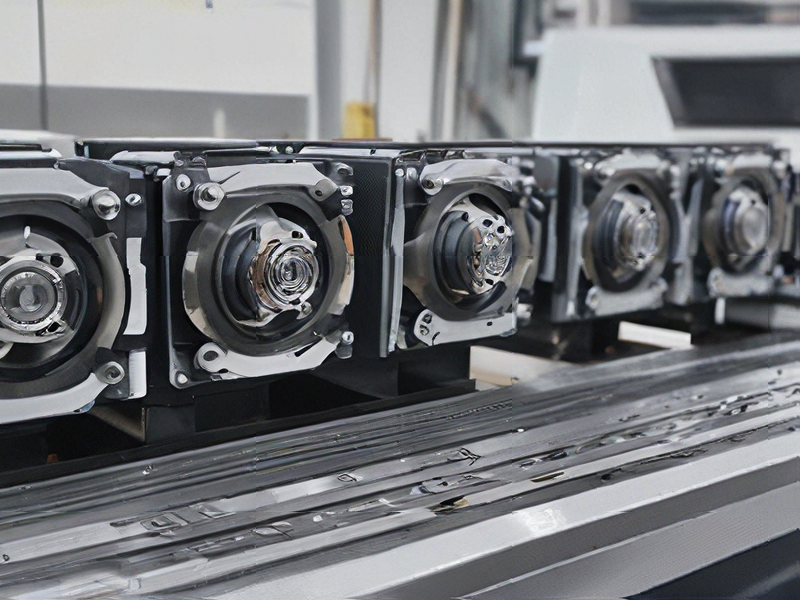