Technology and Applications of prototype tooling
Prototype tooling, also known as rapid tooling, is a crucial process in product development that enables the creation of prototypes quickly and cost-effectively. This process bridges the gap between initial design and full-scale production, allowing for testing, validation, and refinement of designs before committing to expensive production tooling.
Technology:
1. Additive Manufacturing (3D Printing): This method builds prototypes layer by layer, offering high flexibility in design and material usage. It is particularly useful for creating complex geometries and custom parts.
2. CNC Machining: This subtractive process uses computer-controlled tools to shape parts from solid blocks of material. It provides high precision and is suitable for creating functional prototypes with production-like properties.
3. Injection Molding: For more extensive prototyping, injection molding using soft or aluminum molds can produce multiple parts quickly. This method is ideal for testing material properties and production processes.
4. Vacuum Casting: This technique uses silicone molds to replicate parts from a master model. It is efficient for producing small batches of prototypes with excellent detail and finish.
Applications:
1. Product Development: Prototype tooling allows designers and engineers to test form, fit, and function, ensuring the product meets all requirements before full-scale production.
2. Functional Testing: Prototypes can be subjected to real-world conditions to evaluate performance, durability, and identify any potential design flaws.
3. Marketing and Demonstration: High-fidelity prototypes can be used for marketing purposes, giving potential customers and stakeholders a tangible product experience before launch.
4. User Feedback: Early-stage prototypes facilitate user testing and feedback, enabling iterative design improvements based on real user interactions.
5. Customization: Prototype tooling is essential in industries like healthcare, where customized parts, such as prosthetics and implants, need to be tailored to individual patients.
In summary, prototype tooling is a pivotal aspect of modern manufacturing, leveraging advanced technologies to accelerate product development, enhance quality, and reduce time-to-market.
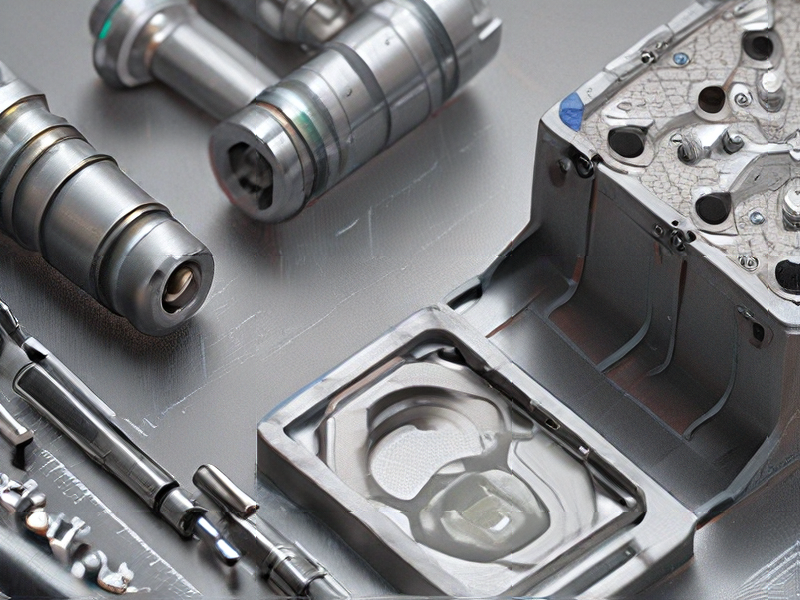
Quality Testing Methods for prototype tooling and how to control quality
Quality testing for prototype tooling focuses on identifying and mitigating risks early in the development cycle.
Here’s a breakdown:
Methods:
* Functional Testing: Ensure the tool performs as intended. This involves checking inputs, outputs, and error handling.
* Usability Testing: Evaluate how easy the tool is to use. Observe real users interacting with the prototype to identify pain points and areas for improvement.
* Performance Testing: Measure the tool’s speed, responsiveness, and resource consumption under varying loads.
* Compatibility Testing: Verify the tool works across different platforms, operating systems, and browsers.
Quality Control:
* Defined Requirements: Clearly document what the tool should do and how it should behave.
* Iterative Testing: Integrate testing throughout the development process, testing frequently and incorporating feedback.
* Automated Testing: Use scripts to automate repetitive tests, freeing up time for more complex testing scenarios.
* Feedback Mechanisms: Establish clear channels for users to report issues and provide suggestions.
Remember, quality is an ongoing process. By implementing these methods and practices, you can significantly improve the quality of your prototype tooling and minimize the risk of costly rework later on.
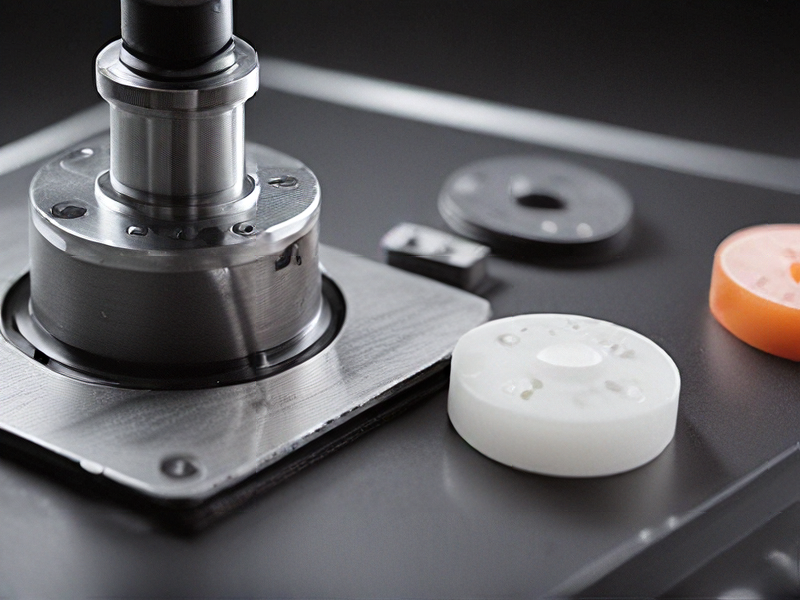
Tips for Procurement and Considerations when Purchasing from prototype tooling
When procuring and purchasing from prototype tooling, several key tips and considerations can help ensure a successful process:
1. Define Requirements Clearly: Clearly specify the design, materials, tolerances, and quantities. Precise requirements help suppliers understand your needs and reduce the risk of errors.
2. Supplier Selection: Choose a reputable supplier with experience in prototype tooling. Assess their track record, certifications, and client testimonials. Ensure they have the capability to meet your technical requirements and deadlines.
3. Cost and Budgeting: Consider the total cost, including tooling, production, and any post-processing. Compare quotes from multiple suppliers to ensure competitive pricing. Remember to account for potential hidden costs like shipping and handling.
4. Lead Time: Understand the lead time for tooling and production. Factor in potential delays and plan your project timeline accordingly. Communicate your deadlines clearly to the supplier.
5. Quality Assurance: Implement a quality assurance process. Request samples or small production runs to verify the tooling and final product quality before full-scale production. Ensure the supplier has robust quality control measures in place.
6. Communication: Maintain open and clear communication with the supplier throughout the process. Regular updates and feedback loops help address issues promptly and ensure the project stays on track.
7. Flexibility and Scalability: Consider the flexibility of the tooling for potential design changes. Ensure the tooling can accommodate future scalability if production volumes increase.
8. Contract and Agreements: Draft a comprehensive contract that outlines all terms, including payment schedules, delivery timelines, quality standards, and intellectual property rights. Ensure both parties have a clear understanding of their responsibilities.
9. Risk Management: Identify potential risks, such as delays, defects, or supplier insolvency. Develop contingency plans to mitigate these risks, including backup suppliers or alternative production methods.
10. Post-Purchase Support: Ensure the supplier provides adequate post-purchase support, including maintenance, repair, and potential modifications to the tooling.
By following these tips, you can optimize the procurement process, minimize risks, and achieve successful outcomes in prototype tooling projects.
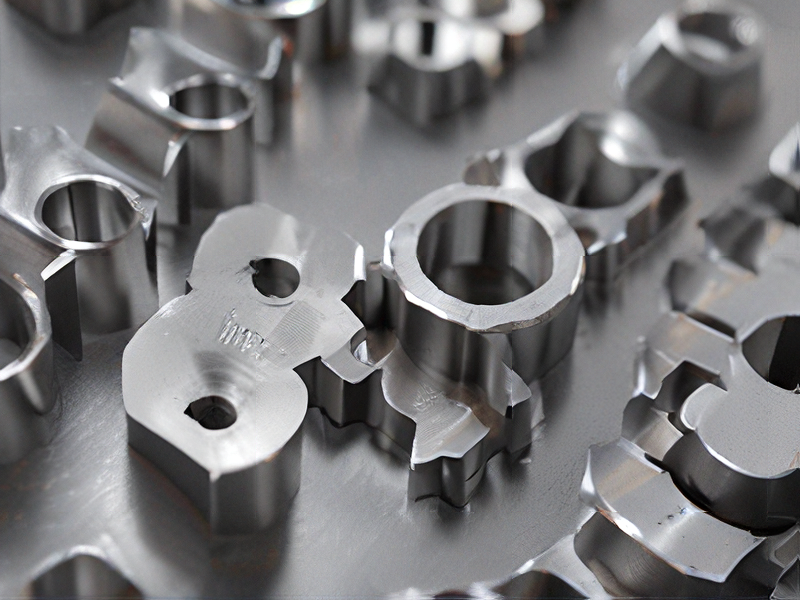
FAQs on Sourcing and Manufacturing from prototype tooling in China
FAQs on Sourcing and Manufacturing from Prototype Tooling in China
1. Why source prototype tooling from China?
China offers competitive pricing, advanced manufacturing capabilities, and quick turnaround times, making it a popular choice for prototype tooling.
2. What types of prototype tooling are available in China?
China provides various tooling types, including injection molding, die casting, CNC machining, and 3D printing.
3. How do I ensure the quality of tooling from Chinese manufacturers?
To ensure quality, select manufacturers with ISO certification, check for good reviews and references, and request samples before committing to large orders.
4. What is the typical lead time for prototype tooling in China?
Lead times vary but typically range from 2 to 6 weeks, depending on the complexity and type of tooling required.
5. How can I protect my intellectual property (IP) when manufacturing in China?
Sign Non-Disclosure Agreements (NDAs) and Non-Compete Agreements (NCAs) with your manufacturers, and consider working with manufacturers that have a reputation for respecting IP.
6. What is the cost range for prototype tooling in China?
Costs can vary widely based on the type and complexity of the tooling, but China generally offers lower prices compared to Western countries.
7. How do I communicate effectively with Chinese manufacturers?
Use clear, concise language and provide detailed specifications. Utilize tools like video calls and project management software to facilitate communication.
8. What are the shipping options and costs?
Shipping options include air freight, sea freight, and courier services. Costs depend on the shipping method, weight, and dimensions of the tooling.
9. Can I visit the manufacturing facility in China?
Yes, visiting the facility is recommended to assess capabilities and build a relationship with the manufacturer. Many factories welcome visits from potential clients.
10. What should I consider when selecting a Chinese manufacturer?
Consider the manufacturer’s experience, capabilities, quality control processes, communication skills, and ability to meet deadlines.
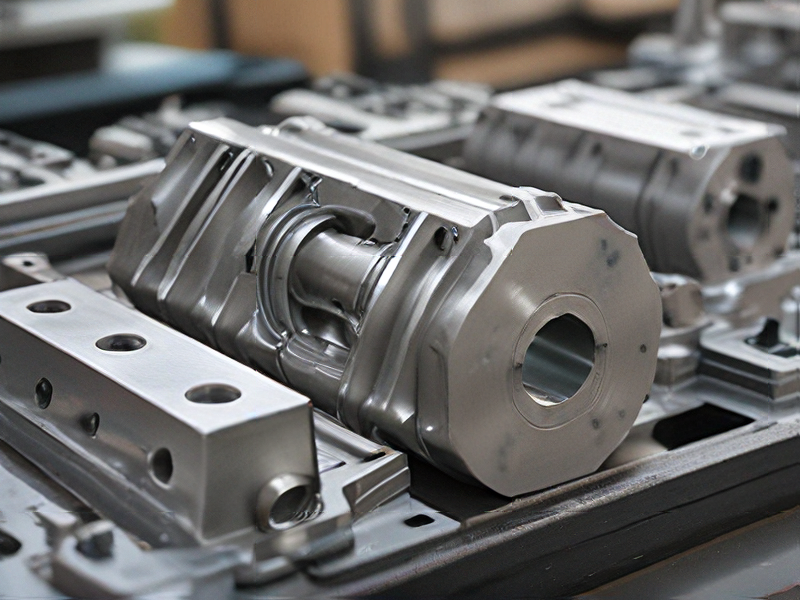